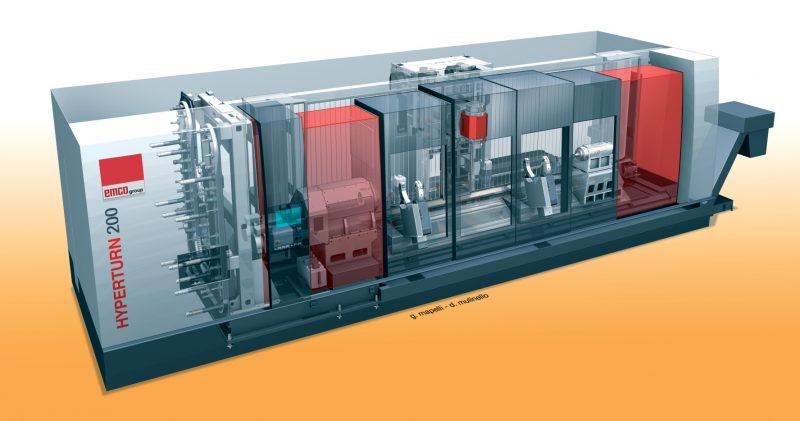
Hyperturn 200 nasce dalla somma delle conoscenze di due aziende del gruppo Emco: Emco Italia e Mecof. Il risultato è un centro di tornitura e fresatura di grandi dimensioni che non scende a compromessi sul fronte del campo di lavoro, delle prestazioni e della qualità della lavorazione.
Negli ultimi anni tutte le aziende del Gruppo Emco hanno puntato allo sviluppo di prodotti che si ponessero ai vertici delle rispettive categorie per tecnologia e prestazioni. Seguendo queste linee guida, Emco Italia ha recentemente sviluppato Hyperturn 200, che si pone – per complessità tecnologica e dimensione macchina – in cima alla gamma di fornitura Emco nell’ambito della tornitura.
Sviluppo costante
La linea Hyperturn comprende oggi cinque modelli, dal 45 al 110, che negli anni si sono dimostrati prodotti di punta, apprezzati dai mercati di tutto il mondo. Proseguire su questa strada, aggiungendo una macchina ancora più grande dimensionalmente e tecnologicamente più avanzata, è stata la naturale evoluzione per la gamma.
L’obiettivo erano sin da subito le nicchie di mercato, slegandosi dai numeri più consistenti raggiungibili da macchine più compatte. Spostandosi sul “campo di battaglia” della tecnologia, svincolandosi per buona parte da quello meramente economico, Hyperturn 200 può avvantaggiarsi della qualità e dell’affidabilità garantita da uno sviluppo volto a massimizzare le prestazioni anche attraverso l’impiego di componentistica e partner di fornitura di prim’ordine.
Hyperturn 200 si pone dunque al top della gamma di tornitura Emco e nasce dalla compartecipazione a livello progettuale tra Emco Italia, il centro di eccellenza del gruppo Emco per la parte dei centri di tornitura, e Mecof, per la parte di fresatura di grandi dimensioni.
Le caratteristiche della macchina prevedono infatti da un lato la ripresa della filosofia multitasking Hyperturn, capace di tornire e fresare con mandrino, contromandrino o contropunta, asse B di tornitura/fresatura, lunette ecc. Dall’altro vengono ripresi alcuni tratti di Mecof, in quanto il bancale e il basamento sono piani e il montante è di tipo mobile con Ram. Questa soluzione tecnica non era stata ancora utilizzata nella linea di tornitura Emco: le altre macchine della linea Hyperturn sono di tipo a bancale inclinato.
Le dimensioni contano
Come accennato, la prima caratteristica che salta all’occhio osservando questa macchina sono le dimensioni e, di conseguenza, le potenze in gioco. Pur essendo Emco Italia focalizzata su torni e centri di tornitura medio-grandi, in questo caso il salto in avanti è stato notevole. Per fare un confronto con il modello della serie Hyperturn più grande finora in produzione, l’Hyperturn 110, si è passati da un diametro tornibile di 620 mm per una lunghezza di 2.300 mm a ben 1.000 mm di tornibile su un massimo di 6.000 mm (a seconda delle necessità del cliente è possibile partire da 3.000 mm salendo a step di 1.000 mm).
La logica è quella di affrontare pezzi grandi e complessi, senza dover scendere a compromessi. Molte macchine si presentano come torni in grado di effettuare operazioni di fresatura; o, eventualmente, centri di lavoro con una tavola girevole dalle buone performance. In Hyperturn sono stati accoppiati un vero modulo di tornitura a un vero modulo di fresatura: il risultato è una soluzione con un mandrino di tornitura capace di 84 kW di potenza (6.400 Nm di coppia) e uno di fresatura da 80 kW (700 Nm di coppia).
La struttura della Hyperturn 200 è completamente in acciaio elettrosaldato, esclusi alcuni particolari – come la testa, il supporto del mandrino e quello della contropunta – in ghisa per sfruttare il naturale effetto di smorzamento delle vibrazioni che questa lega garantisce.
La movimentazione lungo l’asse Z è di tipo a pignone e cremagliera: rispetto all’impiego di viti a ricircolo di sfere, abbinata all’impiego di righe ottiche di serie su tutti gli assi, garantisce la massima precisione e una più semplice gestione della modularità per tutte le lunghezze. Inoltre, poiché in opzione è possibile installare delle lunette, sulla cremagliera ciascuna di esse può muoversi indipendentemente dalle altre e dalla contropunta, essendo veri e propri assi controllati dal controllo numerico, per posizionarsi nel punto più opportuno in base alla lavorazione da effettuare e dalla geometria del pezzo.
Potenza intelligente
Sempre nell’ottica della massima modularità, Emco ha scelto di integrare due differenti linee per il mandrino di fresatura: una ad alta coppia, disponibile di serie, e l’altra ad alta velocità per lavorare particolari in lega leggera, alluminio ecc.
L’impiego del montante mobile con Ram, la cui sezione è pari a 500×500 mm, è stato deciso dopo una attenta analisi delle possibilità tecniche offerte dalle varie soluzioni possibili: l’analisi FEM ha confermato che, rispetto a una macchina con asse B fisso e movimentazione lungo l’asse Y di tutta la colonna, il montante mobile con Ram avrebbe offerto le condizioni operative migliori, garantendo nel contempo la massima rigidezza al sistema e offrendo prestazioni dinamiche particolarmente spinte.
Sull’asse B è possibile collegare direttamente specifici bareni, inoltre Emco ha sviluppato una soluzione alternativa che permetta di collegare i bareni sul fianco dell’asse B per poter gestire utensili di maggior lunghezza e con ancora più stabilità.
A proposito di utensili, anche il magazzino è modulare: la versione base prevede 50 posti, ma a richiesta è possibile salire a 100 e 200, indifferentemente con attacco HSK 100 o Capto C8.
Visti gli 84 kW di potenza in gioco sulla testa, è stato deciso di utilizzare due distinti motori che funzionano anche da asse C: operando in contrapposizione garantiscono il recupero dei giochi, mentre insieme consentono di raggiungere le potenze e le coppie citate. Un singolo motore con queste caratteristiche avrebbe richiesto un ingombro considerevole, con conseguente sovradimensionamento degli organi di trasmissione (cinghia, puleggia ecc.) e alto tensionamento sull’albero motore, che sarebbe risultato perciò molto sollecitato. La gestione elettronica comanda i due motori in modo sincronizzato, esattamente come avviene per alcune tavole di torni verticali di grandi dimensioni.
Inoltre il mandrino è dotato di sistema di raffreddamento specifico, sviluppato per ottimizzarne la stabilità termica garantendo il massimo della precisione in lavorazione.
Compatta ma completa
Un punto critico per macchine di questo tipo è l’ingombro complessivo: con Hyperturn 200 i progettisti hanno lavorato sul fronte dell’ottimizzazione, rimanendo entro i 3.100 mm di profondità per la spedizione ed evitando così l’impiego di trasporti eccezionali o di doverla smontare. Anche l’armadio elettrico è integrato a bordo macchina: oltre ai vantaggi logistici, ne beneficano anche i tempi di installazione e il collaudo in officina presso il cliente.
All’affidabilità e alla stabilità è stata affiancata una notevole possibilità di personalizzazione: la macchina nasce già ben accessoriata, con filtro a carta, alta pressione per il lubrorefrigerante, porta automatica, righe ottiche e sistema Visiport, ma è possibile intervenire su parametri strutturali come la lunghezza tornibile, il tipo di mandrino di fresatura, contropunta o contromandrino, il numero di lunette, il sistema con cambio bareno, ecc.
Questa scelta nasce dalla consapevolezza che, oltre una determinata complessità della macchina, le opzioni sono vincolate al processo tecnologico. I terzisti tenderanno a cercare una soluzione più completa possibile per poter rispondere affermativamente a ogni genere di commessa, anche le più complesse, mentre gli utenti con una produzione stabile e consolidata preferiranno tarare la macchina ottimizzandone l’impiego, senza eccedere nelle opzioni e nei relativi costi.
Poiché è anche dai dettagli che è possibile capire la cura posta nella progettazione di una nuova macchina, i progettisti Emco hanno adottato soluzioni tecniche all’avanguardia in ogni ambito. Le coperture dell’asse Z, ad esempio, non sono i classici elementi telescopici: il sistema – innovativo ma già utilizzato in altri contesti – prevede l’impiego di una tapparella precaricata fissata verticalmente sul montante e composta da un cassone su ciascun lato. Una serie di profilati d’alluminio provvede quindi alla copertura e alla protezione degli organi sottostanti. I vantaggi sono molteplici: innanzitutto il montaggio e l’utilizzo risultano più pratici, perché si evitano gli attriti dovuti ai raschiatori e ai relativi aggiustaggi dei pannelli che sarebbero necessari con la copertura telescopica. Dal punto di vista manutentivo, poi, si tratta di soluzioni praticamente eterne: nel caso si rendesse necessaria la sostituzione di un elemento, si potrà sfilare il singolo elemento sostituendolo con uno nuovo, velocemente e senza spese eccessive.
Un’altra soluzione da sottolineare è l’impiego di un sistema di bilanciatura a gas del carro che, movimentato da una doppia vite lungo l’asse X, ne massimizza la stabilità e la precisione in fase di lavorazione.
Hardware & software
Il controllo numerico è il Siemens 840D solution line, già presente su tutte le altre macchine della linea Hyperturn: la sua flessibilità lo rende ideale quando le applicazioni sono le più disparate. Per le sue caratteristiche, Hyperturn 200 si rivolge infatti a settori come l’aeronautico, l’energetico, la produzione di alberame per grossi motori diesel e per il navale.
Completa l’offerta un’accoppiata di software altrettanto utili: insieme al Cam Esprit viene infatti fornito CPS Pilot, una riproduzione virtuale 1:1 della macchina utile non solo per testare i processi e verificarne la correttezza, stimare i tempi ed eliminare la possibilità di collisioni, ma anche per fare training. Non di rado, infatti, prima di affidare una macchina con queste caratteristiche a un pur esperto operatore si rivela utile far prendere confidenza con le principali funzionalità attraverso un simulatore virtuale.
Condividi l'articolo
Scegli su quale Social Network vuoi condividere