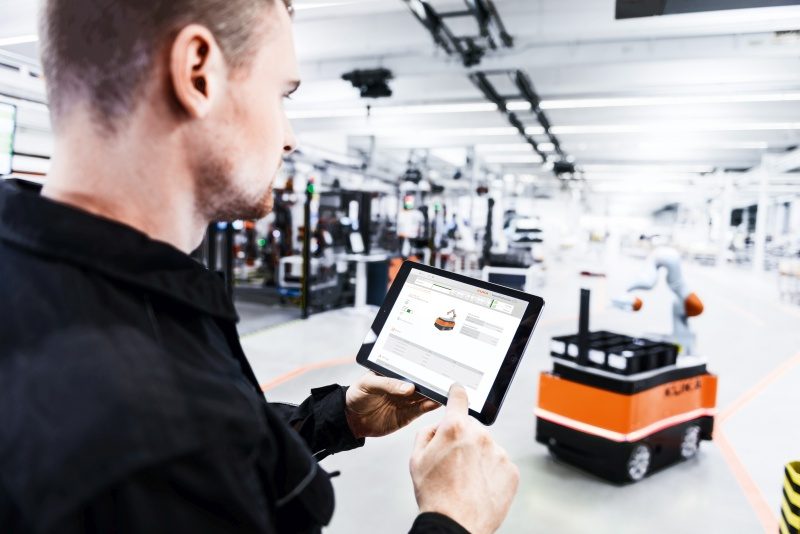
I veicoli a guida autonoma (AGV – Autonomous Guided Vehicle) aprono prospettive totalmente inedite per i processi produttivi del futuro
Piattaforme che si spostano autonomamente all’interno dei reparti produttivi e trasportano i pezzi in lavorazione da una macchina all’altra: uno scenario che in alcuni settori industriali è già realtà. Laddove i pezzi sono troppo pesanti per essere movimentati con la sola forza fisica dell’operatore, i veicoli a guida autonoma (AGV – Autonomous Guided Vehicle) provvedono ad alleggerire il carico, oltre a eliminare la necessità di integrare ogni nuova fase di lavorazione nelle linee di produzione esistenti. In un periodo caratterizzato da prodotti sempre più personalizzati, riuscire a sfruttare queste nuove opportunità per ottenere una maggiore flessibilità rappresenta un vantaggio competitivo decisivo. Sistemi robotizzati mobili in grado non solo di trasportare i pezzi, ma anche di lavorarli e di collaborare direttamente con l’uomo, costituiranno parte integrante della fabbrica del futuro, versatile e flessibile.
Finora, gli AGV hanno sempre rappresentato soluzioni principalmente destinate a soddisfare esigenze specifiche. Siano essi utilizzati da Airbus per trasportare componenti di velivoli oppure da Siemens per movimentare componenti di treni, le piattaforme come KUKA omniMove spostano carichi pesanti all’interno delle fabbriche da una stazione di lavorazione alla successiva. La crescente personalizzazione ai tempi dell’Industria 4.0 è destinata a determinare ulteriori e duraturi cambiamenti nei processi di produzione. La volatilità dei mercati nella maggior parte dei settori rende ancora più importante realizzare lotti di dimensioni limitate in maniera redditizia. In altre parole, i fabbricanti sono chiamati a produrre un numero ancora maggiore di varianti e modelli di un prodotto in quantità variabili.
Soluzioni per la fabbrica del futuro
Una maggiore personalizzazione, più varianti dello stesso prodotto, e l’abbandono della rigida produzione di massa a favore di prodotti personalizzati che possono essere configurati dai clienti nell’ambiente digitale del proprio PC e ordinati via internet da un distributore o direttamente dal fabbricante: tutte queste evoluzioni richiedono un cambio di mentalità radicale. In questo nuovo mondo, infatti, la produzione di beni dovrà diventare notevolmente più flessibile. Per raggiungere questo obiettivo, in futuro occorreranno nuovi concetti di produzione che consentano processi estremamente versatili su scala industriale, oltre che connessi in rete lungo l’intera filiera. Anche la logistica nell’ambito della produzione industriale è destinata a subire un mutamento sostanziale. I robot si sposteranno autonomamente all’interno dello stabilimento, su piattaforme mobili, eseguendo un’ampia gamma di funzioni differenti e interagendo con gli operatori umani.
I primi passi verso la produzione del futuro sono già stati compiuti: KUKA, ad esempio, ha sviluppato il concetto di produzione a matrice, un sistema in grado di trasformarsi automaticamente, in corso d’opera, al variare della tipologia di prodotto, senza tempi di attesa né fermi di produzione, ad esempio sfruttando le piattaforme mobili.
I robot imparano a “camminare”
I sistemi robotizzati mobili svolgono un ruolo centrale in questi scenari futuri, e a buon diritto: essi rappresentano infatti uno sviluppo importante nell’evoluzione degli AGV. In combinazione con un robot riposizionabile, le piattaforme a navigazione autonoma saranno in grado, in futuro, di eseguire non solo le normali attività di movimentazione, ma anche svariate operazioni di carico, scarico e lavorazione, e di collaborare direttamente con gli operatori umani. In altri termini, in futuro i robot “impareranno a camminare” e a spostarsi in maniera flessibile tra i vari reparti di produzione, invece di rimanere fissati dietro alle barriere di protezione. Non sarà più necessario, quindi, trasportare il pezzo fino al robot, ma sarà il robot stesso a muoversi direttamente verso il pezzo e a lavorarlo immediatamente.
Potenziale applicativo illimitato
Questa nuova mobilità apre le porte alla potenziale applicazione dei robot in svariati settori industriali in cui i costi di investimento, ad esempio per l’impiego su una sola macchina, risultavano in passato troppo elevati. Infatti, se il robot è mobile e può spostarsi tra diverse macchine del medesimo tipo, eseguendo in maniera affidabile lo stesso compito su ciascuna di esse, il periodo di ammortamento dell’investimento si riduce sensibilmente. Questa nuova mobilità fa inoltre dei robot una possibile soluzione laddove gli operatori si trovino a dover lavorare in condizioni particolarmente avverse: in questi casi, i robot possono intervenire alleviando il carico di lavoro che grava sui “colleghi” umani. Nella costruzione di velivoli, ad esempio, gli AGV movimentano componenti che pesano diverse tonnellate con precisione millimetrica, mentre i robot assistono gli operatori specializzati in compiti particolarmente difficili o monotoni. Le possibilità sono numerose, dalla foratura, rivettatura, fissaggio, sollevamento e posizionamento all’applicazione di rivestimenti, adesivi e sigillanti. Un sistema robotizzato mobile, ad esempio, può applicare del sigillante anti-corrosione sulle saldature esterne di una fusoliera. Questi componenti sono semplicemente troppo grandi per dei robot fissi, mentre i robot mobili sono flessibili, e si spostano attorno ai componenti a diverse velocità, oltre a poter essere utilizzati per altri compiti, come ad esempio la movimentazione dei materiali.
40 prototipi in funzione
Nel corso degli ultimi anni, KUKA ha sviluppato diversi prototipi di sistemi robotizzati mobili, circa 40 dei quali sono attualmente in fase di collaudo presso varie aziende operative in diversi settori. Molte di esse hanno riconosciuto i vantaggi offerti da questa nuova mobilità, e KUKA ha ricevuto nuove richieste. La produzione in serie di sistemi robotizzati mobili è iniziata alla fine del 2017. La serie KMR (KUKA Mobile Robotics) comprende tutti e quattro i componenti fondamentali che un sistema robotizzato mobile deve avere per offrire il massimo vantaggio: una piattaforma mobile, un pacchetto software per la navigazione intelligente, un robot flessibile e un dispositivo di controllo potente e facile da usare.
Cresce la gamma di piattaforme mobili AGV disponibili
Innanzitutto, un sistema robotizzato mobile necessita di una piattaforma mobile. A seconda della portata richiesta, essa può essere di diversi tipi: una piattaforma mobile KUKA (KMP) omniMove con portata superiore a 3 tonnellate; una KMP 1500 con portata fino a 1,5 tonnellate; una KMP 200 da 0,2 tonnellate.
Tutte e tre le soluzioni integrano la tecnologia di azionamento KUKA omniMove, appositamente sviluppata, basata sulla ruota Mecanum, che garantisce la completa manovrabilità dei veicoli in qualsiasi direzione. Le ruote, dotate di rulli a botte separati, sono in grado di muoversi in maniera indipendente l’una dall’altra. Ciò consente alle KMP di muoversi lateralmente e di ruotare negli spazi più angusti, partendo da ferme. In questo modo, le piattaforme sono capaci di spostarsi rapidamente entro aree ristrette in ogni direzione.
La piattaforma mobile KUKA omniMove per impieghi pesanti può essere controllata manualmente, nonostante le dimensioni ingombranti e le portate elevate, oppure muoversi autonomamente. In opzione, la piattaforma può inoltre essere equipaggiata con un alimentatore indipendente. La piattaforma KMP 1500 è in grado di posizionarsi con una precisione di ±3 millimetri persino negli spazi più angusti, offrendo una soluzione di automazione per applicazioni logistiche compatta ed estremamente accurata. Come tutte le piattaforme, anche il modello più piccolo (KMP 200) è dotato di un campo protetto impostabile per velocità da 0,1 a 0,83 metri al secondo, in base all’applicazione specifica; questo campo arresta la piattaforma mobile in presenza di persone nelle immediate vicinanze, rendendolo idoneo alla collaborazione tra uomo e robot per la lavorazione di pezzi relativamente piccoli e leggeri con un peso massimo di 200 chilogrammi.
Il giusto software per muoversi in sicurezza
Le piattaforme mobili necessitano anche di un software di navigazione intelligente che consenta loro di muoversi in sicurezza. KUKA.NavigationSolution rappresenta la soluzione ideale da installare sui veicoli a navigazione autonoma. Questo software consente la navigazione autonoma eliminando ogni rischio di collisione e senza richiedere marcature artificiali. Tutti i sistemi robotizzati mobili KUKA sono equipaggiati con scanner laser di sicurezza, che vengono utilizzati per creare mappe dell’ambiente di lavoro. Il software KUKA.NavigationSolution acquisisce tutti i dati rilevati dallo scanner laser di sicurezza e dai sensori presenti sulle ruote, e li sfrutta per creare una mappa fedele dell’ambiente circostante, utilizzando il metodo di localizzazione e mappatura simultanea SLAM.
Queste mappe costituiscono la base per la navigazione autonoma. Il sistema, inoltre, reagisce ai cambiamenti ambientali, particolarmente frequenti in sistemi logistici flessibili. L’utilizzo di piste virtuali consente di spostare la piattaforma esclusivamente su percorsi predefiniti. Nei reparti produttivi, i robot mobili impiegano invece questo sofisticato software di navigazione per muoversi in maniera del tutto autonoma senza ricorrere a linee sul pavimento, spire induttive o magneti. L’uso di scanner laser di sicurezza, infine, consente alle piattaforme mobili di condividere percorsi e ambiente lavorativo con il personale umano: l’installazione sulla piattaforma di un robot con tecnologia HRC (Human-Robot Collaboration) consente infatti una collaborazione attiva tra il sistema e l’operatore.
Quando al robot LBR iiwa spuntano le gambe
In linea teorica, tutti i robot KUKA possono essere installati su piattaforme mobili. Il modello LBR iiwa è attualmente disponibile di serie in versione KMR, come variante per la collaborazione uomo-robot (HRC). In un sistema modulare, il modello KMR iiwa unisce i punti di forza del robot LBR iiwa, sensibile e leggero, con quelli della piattaforma mobile KMP 200. Il robot KMR iiwa non dipende da alcuna postazione ed è caratterizzato da un’elevata flessibilità. I sette speciali sensori di coppia connessi fra loro e installati su ciascun asse del robot leggero LBR iiwa fanno di KMR iiwa un sistema altamente sensibile all’ambiente circostante. Ciò gli consente di muoversi in totale sicurezza e senza alcuna barriera di protezione: il contatto esterno, infatti, ne provoca l’arresto immediato. Il sistema KMR iiwa raggiunge una precisione di posizionamento nell’ordine di ±3 millimetri anche negli spazi più angusti, e grazie al software KUKA.NavigationSolution, è in grado di aggirare in maniera affidabile tutti gli ostacoli trovando un nuovo percorso. La combinazione tra robot a 7 assi e piattaforma omnidirezionale garantisce una flessibilità senza precedenti.
Controllare il futuro con KUKA Sunrise
Alla base dei robot KMR iiwa vi sono la tecnologia di controllo Sunrise, concepita appositamente per la serie LBR iiwa, i componenti hardware Sunrise Cabinet e il software Sunrise.OS. Sunrise Cabinet riunisce tutte le funzioni di controllo della sicurezza, controllo del robot, controllo logico e controllo del processo dell’intero sistema. Le interfacce, la scalabilità, le prestazioni e la struttura aperta che lo caratterizzano aprono le porte a possibilità di automazione pressoché illimitate. In futuro, sarà inoltre possibile comandare diversi robot leggeri con un unico dispositivo di controllo.
Fornitore unico
La soluzione sviluppata da KUKA abbatte gli ingombri nel reparto di produzione e aiuta a prevenire infortuni sul lavoro, rendendo i sistemi robotizzati mobili estremamente interessanti per la fabbrica del futuro. Dal momento che un sistema simile deve essere concepito su misura in base ai requisiti di produzione specifici, e tutti i componenti fondamentali devono provenire da un unico fornitore, affinché possano essere armonizzati in maniera ottimale, KUKA si propone come pioniere di questa nuova flessibilità produttiva.
Condividi l'articolo
Scegli su quale Social Network vuoi condividere