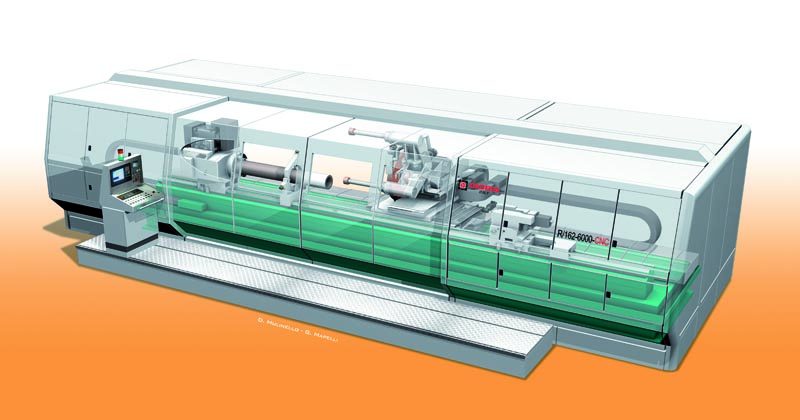
Per propria natura, i costruttori di macchine utensili sono a loro volta utilizzatori di impianti industriali, con una differenza sostanziale rispetto ad altri: sanno esattamente cosa chiedere, quali caratteristiche ricercare e come ottenere il massimo dalla tecnologia a loro disposizione. La macchina del mese di questo fascicolo è destinata proprio a uno di questi utilizzatori: si tratta di Pama, azienda con oltre 80 anni di esperienza nello sviluppo e nella produzione di alesatrici e centri di fresatura costruiti interamente al proprio interno. L’esigenza era quella di affiancare ad una rettificatrice a tavola mobile un modello più performante e capace di garantire precisioni molto spinte nella finitura dei cannotti e dei bareni di alesatura. La scelta è caduta su una rettificatrice cilindrica universale a mola mobile modello R/162 – 6000 x 450 CNC di Gioria, che racchiude in sé una serie di funzionalità in grado di rispondere alle esigenze attuali e future di Pama. Pensata anche per le esigenze di domani La R/162 – 6000 x 450 CNC è un modello a tre assi lineari controllati, un asse rotativo e due assi mandrino. È studiata per la rettifica di precisione di diametri cilindrici e conici esterni ed interni e di spallamenti. Le tendenze di mercato hanno portato alla costruzione di pezzi di dimensioni sempre maggiori, che necessitano di macchine più grandi e più precise. La rettificatrice Gioria è stata quindi pensata per raggiungere un’elevata precisione nonostante le considerevoli dimensioni: entro i 3 micron di concentricità tra i diametri esterni e interni, sia per le lavorazioni cilindriche sia per quelle coniche. La finitura di un mandrino portapezzi, infatti, richiede una rispondenza perfetta tra i due coni: nell’ambito dello stesso ciclo di lavoro il cliente ha inoltre la possibilità di utilizzare appositi tamponi per poter ispezionare il cono e verificare in tempo reale le tolleranze sul pezzo. Poiché in futuro si prevede che i pezzi da lavorare avranno caratteristiche di durezza e tenacità sempre maggiori, dovute anche all’impiego di nuovi materiali e dai trattamenti che subiscono, la macchina è stata progettata per utilizzare sia mole tradizionali, sia mole in superabrasivo come il diamante o il CBN. In quest’ottica la macchina è dotata di sistemi di ravvivatura e sagomatura della mola specifici. La macchina offre un’altezza punte di 450 mm, un diametro massimo rettificabile di 900 mm e una lunghezza massima rettificabile di 6000 mm senza impiego dell’unità per rettifica interni. Nel caso in cui venga utilizzata l’unità per rettifica interni per una profondità di lavoro di 600 mm, la lunghezza massima del pezzo ammessa in macchina è di 4700 mm.
Robusta e affidabile
Rispetto ad altre macchine destinate a lavorazioni più impegnative, come nel caso dei rulli di laminatoio, gli alberi nel settore energetico o la trasmissione di potenza, questo modello non ha un compito particolarmente gravoso in termini di asportazione di materiale. Il peso massimo ammesso tra le punte e sulle lunette è di 4 tonnellate. Ciò nonostante, proprio nell’ottica di assicurare una precisione dimensionale elevata e costante nel tempo, Gioria è ricorsa ad una struttura in ghisa capace di limitare le possibili influenze date dalla variazione della temperatura di esercizio. Gioria è infatti tra i pochissimi costruttori di macchine utensili a disporre di una fonderia interna, nella quale sono realizzati i componenti di tutte le proprie macchine. La R/162 – 6000 x 450 CNC è costituita da un basamento monolitico in ghisa, sul quale sono ricavate le guide longitudinali del carro portamola e le guide della tavola. In fusione di ghisa sono anche le slitte, la testa portapezzo, la contropunta e la testa portamola; si tratta di un materiale particolarmente adatto a garantire la più alta stabilità e l’ottimale assorbimento delle vibrazioni contribuendo così a migliorare la qualità della superficie del pezzo. Le guide degli assi Z e X sono di tipo a strisciamento, sono ricavate direttamente nella fusione e sono rettificate. Sulle controguide viene applicato un riporto plastico antifrizione accuratamente raschiettato. Tutte le guide di scorrimento sono lubrificate in maniera forzata ed automatica. Il carro testa portamola è dotato di due ampie guide rettificate, una piana ed una prismatica, con controguide ricoperte di materiale plastico antifrizione e raschiettate. Questa soluzione si rivela indispensabile per mantenere il corretto allineamento degli assi lineari in qualsiasi posizione di lavoro dato che la macchina deve lavorare con precisioni certe e ripetibili indistintamente pezzi da sei metri così come componenti da meno di un metro. Inoltre, il gruppo porta mola dispone di un asse che ruota di ±10° che, abbinato ad una slitta longitudinale supplementare, consente di rettificare coni in passata per una lunghezza di 400 mm. Con questa soluzione il cono può essere rettificato senza la necessità di profilare la mola né di interpolare gli assi Z e X con il risultato di tempi ciclo più rapidi, una precisione maggiore e una finitura superficiale migliore.
Dettagli di valore
Indipendentemente dalla tipologia di macchina, il nemico numero uno della precisione rimane il gradiente di temperatura, ovvero la variazione della temperatura in una data unità di tempo. Per questo i progettisti Gioria hanno pensato ad una serie di accorgimenti per mantenere sotto controllo la temperatura d’esercizio della macchina anche con un utilizzo discontinuo dato che far lavorare la macchina per alcune ore, spegnerla e riaccenderla alcune ore dopo significa operare in condizioni difficilmente prevedibili. A questo proposito, per stabilizzare la temperatura all’interno della macchina è previsto un sistema di condizionamento che raffredda o riscalda il lubrorefrigerante sulla base del gradiente di temperatura. Sulla R/162 – 6000 x 450 CNC il lubrorefrigerante non solo viene spruzzato nella zona di contatto tra mola e pezzo ma viene fatto circolare all’interno del basamento in appositi canali ricavati nella fusione contribuendo così a mantenerne costante la temperatura. Alla Pama poi, la macchina è stata installata in un ambiente a temperatura costante, limitando di fatto ogni deriva termica. Anche la carenatura integrale della macchina, oltre a rispondere alle prescrizioni normative in tema ecologico e di sicurezza, concorre al raggiungimento di una stabilità termica di esercizio. L’azienda acquirente ha chiesto inoltre la fornitura di uno strumento di ispezione geometrica che la stessa Gioria utilizza in officina e durante le installazioni: si tratta di un supporto montato sulle guide longitudinali del basamento sul quale viene posizionato lo specchio dell’autocollimatore laser con cui viene ispezionata la geometria della macchina. Infine è degno di nota il fatto che la componentistica impiegata nella costruzione delle rettificatrici Gioria reperita da commercio mantiene la codifica del produttore originario. In tal modo l’utilizzatore può decidere di approvvigionarsi autonomamente dei componenti da sostituire senza dover necessariamente interpellare il costruttore della macchina. Considerando che molte macchine vengono vendute all’estero, sovente in paesi distanti, poter intervenire autonomamente nella sostituzione dei componenti implica per il cliente un considerevole risparmio di tempo.
Completa sotto ogni aspetto
Vista la lunghezza rettificabile, è fondamentale disporre del supporto di lunette. La fornitura prevede due lunette aperte a due punti di appoggio adatte per diametri pezzo da 110 a 320 mm e due lunette chiuse a tre punti di appoggio che coprono il campo diametrale da 250 a 410 mm. Entrambe le tipologie di lunetta sono dotate di regolazione micrometrica manuale dei pattini e di passaggio del lubrorefrigerante attraverso di essi. Quest’ultima caratteristica assicura una corretta lubrificazione del punto di contatto tra pattini lunetta e pezzo riducendo eventuali segni estetici. In quest’ottica Pama ha richiesto anche un dispositivo aggiuntivo di superfinitura e lappatura mediante nastri flessibili per rimuovere eventuali tracce di lavorazione dal pezzo. Pur non essendo geometricamente rilevanti, questi inestetismi vengono eliminati attivando direttamente nel part program l’impiego dell’unità di superfinitura che opera automaticamente in macchina senza bisogno di alcun attrezzaggio supplementare. Un’altra prerogativa di questa famiglia di rettificatrici è la possibilità di registrare con dei lardoni conici la perpendicolarità tra l’asse verticale della mola e l’asse dei centri in modo agevole e preciso per avere la certezza ripetibile nel tempo del taglio incrociato nella rettifica di spallamenti. Il dispositivo elettronico per il taglio in aria permette di rilevare il contatto fra mola e pezzo. Il segnale acustico acquisito viene successivamente elaborato dall’unità elettronica che confronta il valore riscontrato con i limiti di soglia programmati, in questo modo è possibile ottimizzare l’avanzamento della mola durante il ciclo di rettifica, riducendo i tempi improduttivi.
Una macchina intelligente
La riduzione dei tempi di attrezzaggio è un’altra delle richieste salienti del committente: per ottenere questi risultati Gioria ha integrato una serie di accorgimenti per ridurre i tempi morti. L’unità per rettifica interni, ad esempio, è costituita da un unico elettromandrino su cui è possibile montare varie prolunghe per interni da 110 fino a 600 mm di lunghezza. Il motore dell’elettromandrino è stato progettato per garantire uno spettro di velocità e coppia adatte per la capacità di rettifica interni possibile in macchina. L’attacco di queste prolunghe è di tipo HSK 63, che consente all’utilizzatore di dotarsi di una vasta serie di accessori e prolunghe facilmente reperibili sul mercato. Per la programmazione, Gioria ha sviluppato la propria interfaccia uomo-macchina sulla piattaforma Siemens Operate disponibile con il controllo numerico Siemens 840D sl. Sinumerik Operate è dotata di numerose funzioni in grado di migliorare le prestazioni e di combinare la programmazione dei cicli di lavoro in un’unica interfaccia operativa, garantendo così la compilazione dei part program e la preparazione del lavoro di attrezzaggio in modo veramente rapido, razionale e intuitivo. Gli operatori troveranno quindi specifiche pagine dedicate alle varie funzionalità, come ad esempio la compensazione delle curve, il richiamo dei cicli di diamantatura o in generale l’impostazione di dettaglio dei parametri tecnologici di lavoro. In questo modo la compilazione dei cicli di lavoro direttamente in macchina diventa semplice e veloce, eliminando il ricorso all’ufficio tecnico o alla programmazione remota. Il software è stato sviluppato nel modo più completo e versatile per venire incontro alle esigenze di riduzione dei tempi di lavorazione sia per i componenti esistenti sia prevedendo ogni possibile sviluppo tecnologico futuro. Tra le funzioni maggiormente apprezzate c’è la possibilità di azzerare il pezzo ed il diamante in modo automatico con un tastatore passivo che, toccando il pezzo o il supporto del diamante, consente di acquisirne la posizione nel controllo numerico senza alcuna operazione manuale. Bareno e mandrino sono il cuore di una fresalesatrice e la criticità della loro lavorazione rende impensabile nonché rischiosa l’automazione completa del ciclo, per questo risulta più appropriato predisporre dei cicli per le singole operazioni all’interno del ciclo di rettifica completo da attivare singolarmente o lanciati in sequenza. È possibile inoltre, sempre all’interno del medesimo ciclo, richiamare degli arresti per consentire all’operatore eventuali verifiche, misurazioni e compensazioni delle quote dimensionali prima di procedere con le fasi finali di lavoro. Per raggiungere la precisione prescritta senza rischiare di scendere sotto la quota stabilita, l’operatore può decidere di interrompere la lavorazione in qualsiasi momento prima del diametro finito nominale e verificare che la quota sia quella corretta. In caso affermativo il ciclo riprende altrimenti la quota può essere aggiornata compensando il diametro del controllo con quello effettivamente misurato. La ripartizione del ciclo in singoli settori risulta utile anche in presenza di pezzi simili per geometria ma diversi per dimensioni, infatti un programma esistente può essere duplicato, modificato nei parametri differenti e salvato senza dover scrivere un part program del tutto nuovo.
Condividi l'articolo
Scegli su quale Social Network vuoi condividere