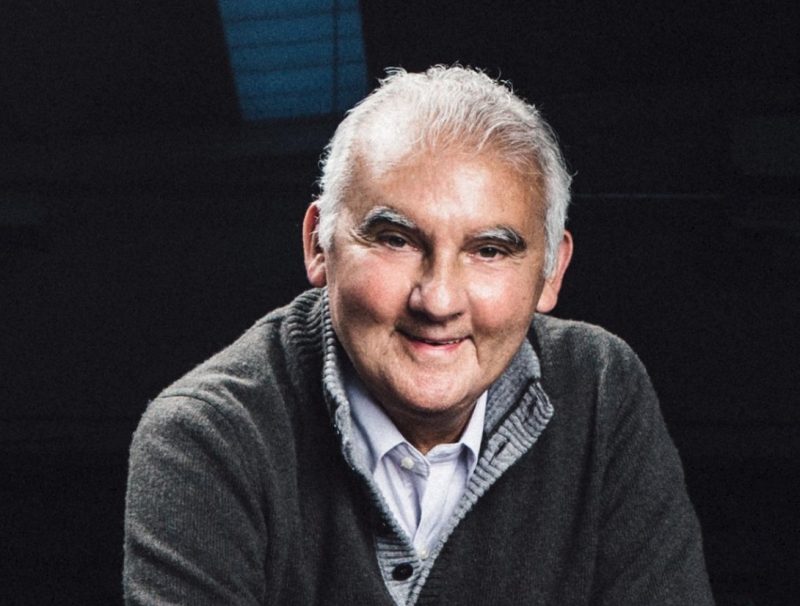
Artigianalità e tecnologia sapientemente mixate rappresentano il punto di forza di Termignoni, azienda italiana specializzata nella produzione di impianti di scarico per moto stradali e da competizione.
Artigianalità e tecnologia sapientemente mixate rappresentano il punto di forza di Termignoni, azienda italiana specializzata nella produzione di impianti di scarico per moto stradali e da competizione.
di Davide Davò
I centauri sono creature mitologiche rappresentate come esseri umani dal bacino in su, mentre il resto del corpo appartiene a un cavallo. Al giorno d’oggi esiste anche un’altra “specie” di centauri, esseri interamente umani che diventano tutt’uno con il loro destriero metallico. In una parola, motociclisti. Normalissimi uomini colti dalla passione per questo mezzo meccanico che, come vuole una famosa massima, è capace di muovere l’anima, non solo i corpi. Una passione la cui espressione più alta è rappresentata dalle competizioni motociclistiche, dove primeggiare è una questione di equilibrio in tutti i sensi. Equilibrio per non cadere, equilibrio nelle prestazioni del mezzo, equilibrio tra pilota e moto. Una perfetta sinergia tra parte umana e componente meccanica vissuta in prima persona anche da Luigi Termignoni, pilota degli anni 60 che ha saputo trasferire tale sinergia all’interno della propria azienda produttrice di impianti di scarico per moto stradali e da competizione.
Specialisti dello scarico
«Termignoni nasce nel 1969 per volontà di Luigi Termignoni, fondatore e attuale Presidente dell’azienda, che dopo avere trascorso alcuni anni tra i cordoli delle piste decide di dedicare tutte le sue energie a una nuova passione: l’elaborazione dei motori – esordisce Elio Mariani, Responsabile Marketing e Comunicazione di Termignoni – Apre così una piccola officina all’interno della quale esegue lavorazioni meccaniche sui principali componenti dei motori da competizione per migliorarne le prestazioni. Da subito si rende conto che la moto negli anni diventerà sempre più tecnologica, intuendo la necessità di affiancare alle conoscenze e competenze del personale una serie di opportuni strumenti che migliorino la qualità del prodotto finito. Motivo per cui nel 1971 acquista un banco prova per testare le prestazioni delle moto, operazione in precedenza affidata alla sensibilità del collaudatore».
Attraverso questo strumento, Termignoni fornisce ai propri clienti dati reali che attestano in modo analitico l’incremento delle prestazioni ottenuto grazie all’elaborazione del motore. Tradotto, i risultati si dimostrano più affidabili e di facile interpretazione anche per il cliente.
«A metà degli anni 70 Luigi Termignoni nota una crescente richiesta da parte del mercato di soluzioni capaci di trasformare una moto da strada in una da competizione – prosegue Mariani – Un’esigenza che, unita alla mancanza in quel periodo di un vero e proprio produttore dedicato alla realizzazione di impianti di scarico aftermarket, lo spinge a specializzarsi in questo campo. Sviluppa così i primi scarichi, prodotti in modo completamente artigianale ma altamente performanti grazie al processo di miglioramento continuo del prodotto basato sulle informazioni ricevute dai test effettuati sul banco prova».
Evoluzione continua
A fine anni 70 Termignoni avvia la produzione di silenziatori con camicia e componenti in alluminio, e i risultati ottenuti nelle competizioni di durata da moto equipaggiate con questi elementi danno sempre maggiore visibilità all’officina piemontese. A cavallo tra gli anni 80 e 90 arrivano i primi titoli iridati nelle più importanti competizioni a livello mondiale, i primi impianti di scarico in titanio e una forte spinta alla crescita aziendale legata all’evoluzione del mercato, che richiede numeri sempre maggiori abbinati alla massima qualità dei prodotti.
«Oggi la filosofia che Luigi Termignoni porta avanti è la stessa di quando ha avviato l’attività, ovvero abbinare le competenze degli operatori all’innovazione tecnologica – commenta Mariani – Da piccola officina ci siamo trasformati in una società composta da circa 70 dipendenti con 6.000 m2 di capannone a disposizione per la produzione degli scarichi e clienti in tutto il mondo. Siamo strutturati per affrontare senza difficoltà le richieste di un mercato complesso come quello delle moto in tutte le nostre aree di interesse, ovvero equipaggiamenti di primo impianto per una delle principali case costruttrici italiane, prodotti aftermarket e soluzioni per il mondo delle competizioni. L’innovazione continua del prodotto e del processo produttivo, la ricerca di tecnologie di lavorazione e di materiali sempre più efficienti e performanti ci hanno permesso di raccogliere continui successi nei più prestigiosi campionati mondiali e di diventare uno dei top player nel settore degli scarichi di serie. Siamo molto orgogliosi di questi risultati, ottenuti valorizzando il Made in Italy. Tutte le lavorazioni avvengono all’interno dello stabilimento di Predosa (AL), la maggioranza dei nostri fornitori è italiana, e abbiamo deciso di dare risalto a questo aspetto affiancando al nostro logo il claim The Italian Sound».
L’intero know how relativo alla produzione degli impianti di scarico rimane dunque confinato tra le mura del capannone alessandrino, dove tecnici e operatori seguono l’evoluzione di ogni progetto. Ma esattamente, come nasce uno scarico? «Ogni impianto dev’essere montato su una moto, di conseguenza il primo passo nella fase di progettazione è capire com’è fatta la moto e dove posso andare a posizionare i vari elementi dello scarico – spiega Mariani – Possiamo partire dal modello reale del mezzo, che viene portato in officina e sul quale l’operatore inizia a lavorare per dare forma all’impianto, oppure sfruttiamo un gemello digitale della moto per andare a definire geometria e matematiche dello scarico. In entrambi i casi si tratta di un lavoro delicato, perché lo spazio a disposizione per fare passare i tubi dell’impianto tra i vari elementi della moto (soprattutto nel caso di modelli di serie) è estremamente ristretto. Nelle moto da competizione il compito è un po’ più agevole perché non sono presenti elementi come il portatarga, che possono condizionare la geometria o la posizione dello scarico. Da sottolineare che l’attività del Reparto Corse è fondamentale per noi, perché oltre a dare maggiore visibilità al marchio contribuisce a incrementare il nostro know how, che viene trasferito e adattato alla produzione di serie».
Produttività flessibile
Una volta che il prototipo raggiunge i target prefissati in fase di progetto, si passa alla produzione in serie dello scarico. Un’attività svolta interamente nello stabilimento di Predosa, strutturato con un lay-out votato alla massima flessibilità esattamente come gli impianti che vi sono installati. «Il mercato della moto è un mercato stagionale, e quindi i volumi produttivi subiscono forti variazioni durante l’anno – interviene Cristian Zappia, Ufficio Tecnico di Termignoni – Inoltre i componenti che realizziamo possono avere forme relativamente semplici oppure estremamente complesse, che in alcuni casi richiedono continui passaggi da un reparto di lavorazione all’altro e devono essere lavorati dalla stessa tecnologia più volte all’interno del ciclo produttivo. Nel caso dei silenziatori per esempio gli sviluppi di lamiera vengono saldati tra loro, poi passano al reparto assemblaggio per il fissaggio di alcuni elementi, e infine tornano al reparto saldatura dove viene aggiunta una copertura che racchiude il tutto». Per riuscire a gestire tale variabilità di volumi e di prodotti, Termignoni ha dovuto modificare il proprio approccio alla produzione e diventare molto elastica, organizzando il reparto produttivo con un layout che fosse il più aperto possibile e acquistando impianti capaci di passare in modo semplice e rapido da un pezzo a quello successivo indipendentemente dalla sua complessità.
«Il ciclo parte ovviamente dal magazzino del materiale in ingresso, nel quale vengono stoccati tubi in acciaio o titanio con spessori di 1÷1,2 mm e lamiere piane in acciaio, titanio o alluminio con spessori da 1,2 fino a 0,6 mm – precisa Zappia – Da qui il materiale passa al reparto taglio, dove sono presenti diverse cesoie per il taglio della lamiera piana, mentre i tubi vengono presi in consegna da una tagliatubi automatica impegnata nelle produzioni di serie o da macchine manuali utilizzate per produzioni più piccole e caratterizzate da tagli inclinati o lavorazioni speciali». Termignoni dispone inoltre di una macchina per il taglio 3D con braccio antropomorfo per movimentazione e posizionamento del pezzo, che grazie alla sua grande flessibilità permette la lavorazione 3D del tubo e la lavorazione 2D e 3D della lamiera.
«Il taglio laser viene programmato tramite CNC o con sistema di autoapprendimento – prosegue Zappia – Nelle lavorazioni più semplici del tubo e nel taglio degli sviluppi della lamiera sfruttiamo la programmazione tramite software, ma quando dobbiamo rifilare geometrie estremamente complesse di particolari stampati e saldati troviamo maggiore beneficio lavorando con il sistema di autoapprendimento. Stiamo parlando di un impianto preciso e flessibile che Luigi Termignoni ha introdotto circa vent’anni fa, dimostrando grande lungimiranza e una forte volontà di innovare dotandosi di tecnologie capaci di migliorare la qualità del prodotto finito così come l’efficienza dell’intero ciclo produttivo».
Il tubo prende forma
Una volta tagliati alla giusta lunghezza, i tubi passano al reparto piegatura per essere lavorati da una delle tre macchine oleodinamiche oppure dalla curvatubi elettrica CN acquistata circa due anni fa. L’introduzione di quest’ultima soluzione ha risposto sia a un’esigenza di maggiore produttività legata all’incremento delle richieste da parte del mercato, sia alla necessità di garantire elevata precisione su pieghe complesse e una maggiore ripetibilità della precisione nella lavorazione dell’intero lotto.
«Nelle macchine oleodinamiche le variazioni della temperatura dell’olio vanno a incidere sul risultato finale della piega – aggiunge Zappia – Grazie alle loro capacità e alla grande esperienza i nostri operatori sono in grado di compensare queste variazioni, ma dove l’uomo non può arrivare subentra la tecnologia che in questo caso è rappresentata dalla curvatubi elettrica. Questa macchina ci permette di eseguire raggi differenti in un unico ciclo di lavoro, e di arrivare a curve di 180° senza incontrare particolari complessità anche nel caso di lavorazioni con rapporto diametro tubo/raggio di curvatura vicino all’1:1. Inoltre la maggiore stabilità termica assicura una precisione nel singolo pezzo decisamente elevata, accompagnata dalla garanzia che lotti realizzati in elevati volumi sono costituiti da particolari che presentano le medesime caratteristiche. Un aspetto importante soprattutto per elementi che vengono ripresi dalla macchina per il taglio laser 3D, dove il braccio antropomorfo va a prelevare pezzi geometricamente identici». Se le deformazioni che il tubo deve subire riguardano anche la sua sezione trasversale entra in gioco la macchina per la deformazione dei tubi, il cui compito è di generare forme ellittiche oppure conicità particolarmente spinte partendo da un tubo cilindrico. Poco distante dalle curvatubi si trova il reparto di stampaggio, dove le presse si occupano dell’imbutitura della lamiera piana. Tale lamiera non è sottoposta a un processo di ricottura prima della deformazione in macchina, quindi è necessario che il fornitore invii un materiale con le esatte specifiche richieste da Termignoni. Inoltre per le forme più complesse o per le imbutiture profonde è di fondamentale importanza lo studio del processo di imbutitura, in modo da individuare i parametri di lavoro e la geometria dello stampo che permettono di deformare il materiale senza strapparlo. Per questa fase del progetto l’azienda si appoggia a partner specializzati nell’utilizzo di software per la simulazione dello stampaggio, con l’obiettivo di individuare le criticità dello stampo e di modificare raccordi e spessori per ottenere un pezzo imbutito senza difetti.
Saldatura manuale e automatizzata
Come già visto nel taglio e nella piegatura, anche nel reparto saldatura c’è una perfetta convivenza tra postazioni per il lavoro artigianale e impianti automatizzati. «I banchi di saldatura affidati a personale altamente qualificato ci permettono di eseguire le lavorazioni più complesse e customizzate, mentre il robot di saldatura è dedicato alle produzioni di pezzi in serie – continua Zappia – Il robot è fondamentale, per noi, perché ci permette di gestire senza difficoltà i picchi di produzione che caratterizzano il nostro settore durante la primavera. In questa stagione sfruttiamo al massimo l’impianto automatizzato, che lavora su due turni ed è dotato di doppia tavola rotante. In questo modo, mentre il robot porta a termine la saldatura l’operatore può montare le attrezzature da noi progettate a hoc e preparare il pezzo successivo».
Oltre al robot e alle postazioni manuali, Termignoni dispone anche di una serie di saldatrici longitudinali posizionate all’interno di piccole isole di lavoro e accoppiate a calandre a controllo numerico. Queste isole vengono utilizzate in buona parte per la produzione interna di tubi in titanio destinati all’utilizzo nelle competizioni. «In questi casi partiamo da una lamiera piana in titanio, da cui viene tagliato lo sviluppo – spiega Zappia – Il materiale passa quindi alla calandra a controllo numerico, che ci permette di creare diverse forme. Infine il pezzo viene spostato sulla saldatrice longitudinale opportunamente posizionata nei pressi della calandra, che chiude il particolare con una giunzione saldata. I tubi così prodotti vengono poi piegati dalle curvatubi, mentre le camicie vengono lavorate dalle presse per la formatura finale, in modo da conferire al pezzo la sagoma che caratterizza il nostro silenziatore».
La qualità è anche estetica
L’attenzione per l’intero processo così come per i più piccoli dettagli è sempre al massimo livello in Termignoni, e non potrebbe essere diversamente tenendo conto che gli impianti di scarico devono conquistare il cliente non solo dal punto di vista delle prestazioni ma anche estetico. «La finitura superficiale è estremamente importante per i nostri prodotti – prosegue Zappia – In quest’ottica circa un paio di anni fa abbiamo acquistato una granigliatrice grazie alla quale riusciamo a eliminare le imperfezioni e i difetti estetici che rimangono sul pezzo a valle delle operazioni di saldatura. Inoltre tale processo conferisce alla superficie del pezzo un aspetto simile alla satinatura, che molti clienti dimostrano di apprezzare».
Al termine del processo di granigliatura i componenti raggiungono il reparto di assemblaggio dove vengono completati con il fissaggio di alcuni elementi o direttamente preparati per la spedizione. Ogni impianto ha il suo imballo dedicato, in modo che possa raggiungere il cliente finale nelle migliori condizioni. «Come in tutti i settori in cui prestazioni, design e qualità del prodotto fanno la differenza, raggiungere il successo è questione di dettagli – conclude Mariani – Ogni aspetto dev’essere studiato, ottimizzato e continuamente migliorato per raggiungere l’eccellenza. Una sfida molto impegnativa ma altrettanto stimolante che affrontiamo da sempre col giusto mix di artigianalità e innovazione tecnologica, colonne portanti del dna dell’azienda ed espressione diretta della passione e delle competenze tecniche che Luigi Termignoni è riuscito a trasferire a tutti i dipendenti. Termignoni rappresenta un concreto esempio di come tecnologia e automazione non devono necessariamente sostituire l’uomo, ma al contrario possono affiancarlo all’interno di una produzione capace di dare spazio e di esaltare i punti di forza di macchine e persone».
Puntare sull’idroformatura
«Da alcuni anni ormai abbiamo modificato il modo in cui progettiamo alcuni componenti per adattarli al meglio al processo di idroformatura – spiega Cristian Zappia – Grazie a questa tecnologia possiamo ridisegnare particolari con cambi di sezione importanti anche con lunghezze di sviluppo ridotte. Parliamo quindi di geometrie difficilmente ottenibili con altri processi. Inoltre, cerchiamo di progettare il modello 3D in modo da incrementare la produttività e ottimizzare l’utilizzo dello stampo. Stiamo puntando molto sull’idroformatura, perché oltre a garantire una serie di vantaggi dal punto di vista delle caratteristiche meccaniche e geometriche del componente ci permette di evitare complesse operazioni di pulizia a valle della lavorazione. Essendo una tecnologia che non abbiamo in casa, ci affidiamo a un fornitore specializzato con il quale abbiamo uno stretto rapporto di partnership: noi ci occupiamo delle matematiche del componente, lui suggerisce correzioni alla geometria per non rovinare né il pezzo né lo stampo».
Condividi l'articolo
Scegli su quale Social Network vuoi condividere