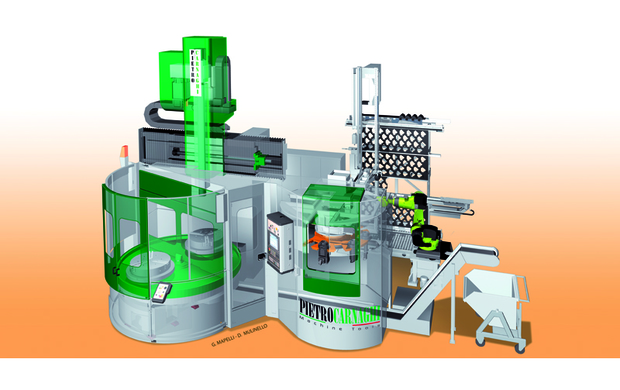
Con la rinnovata serie ATF, Pietro Carnaghi risponde alle richieste di settori applicativi esigenti come l’aeronautico e l’Oil&Gas. La possibilità di personalizzare le macchine è uno dei fattori chiave per raggiungere il successo in questi complessi mercati.
Il settore aeronautico è da sempre all’avanguardia nelle richieste di innovazione sia in termini di nuovi materiali da utilizzare che di metodologie di taglio, ma richiede anche un elevato standard di qualità e di garanzia del risultato. Pietro Carnaghi ha sviluppato nuove caratteristiche sulle proprie macchine per consentire lo sviluppo delle strategie di taglio per materiali tenaci ad alta resistenza al calore quali titanio, leghe a base nichel (Inconel 718, Waspalloy, Renè ecc.), acciai con alto contenuto di molibdeno e cobalto (Stellite). L’ultima applicazione innovativa nel suo genere riguarda la fornitura di svariati centri di tornitura e fresatura per la produzione dei nuovi motori aerei caratterizzati da ridotti consumi, ridotta rumorosità e soprattutto basse emissioni, per la lavorazione sia dei dischi turbina che dei corpi. In questi centri viene utilizzata la tecnologia innovativa dell’alta pressione unita alla tavola con motore a tecnologia direct drive e caratteristiche di coppia, potenza e numero di giri in una combinazione votata alle prestazioni e all’affidabilità.
Una famiglia rinnovata
Poter contare su quasi 100 anni di esperienza è decisamente un punto a favore della Pietro Carnaghi: fondata nel 1922, l’azienda è oggi un importante punto di riferimento nel panorama internazionale dei produttori di macchine utensili, grazie al continuo e costante sviluppo.
La famiglia Carnaghi, fondatrice dell’azienda, è oggi rappresentata dalla terza e dalla quarta generazione, attiva nella gestione aziendale, affiancata da figure manageriali di livello.
ATF è la rinnovata famiglia di centri di tornitura verticali per pezzi di dimensioni medio-piccole, ma che richiedono un approccio volto alla qualità totale unita a un costo di gestione contenuto.
Non solo: poiché non è più possibile prescindere da soluzioni multiprocesso, la serie ATF è in grado di eseguire anche le più complesse operazioni di fresatura, foratura, rettifica e altro ancora, in funzione delle specifiche esigenze dell’utilizzatore.
Questo è un altro punto chiave: non si vende solo una macchina o un impianto. Spesso i clienti approcciano i costruttori come Pietro Carnaghi con il progetto di un componente e chiedono una soluzione chiavi in mano, incluso ogni altro fattore utile a portare a termine la commessa in maniera tecnicamente corretta ed economicamente remunerativa, che sia in grado di offrire le prestazioni volute e che le mantenga per tutta la vita utile dell’impianto stesso. Vengono incluse quindi le attrezzature, gli utensili, il ciclo di lavoro, il programma di lavorazione pezzo, ecc.
Ecco quindi che esperienza, tecnologia e capacità umana di analizzare e risolvere problematiche sempre più complesse giungono a un divisore comune: una macchina capace di realizzare il componente in modo tecnologicamente adeguato ed economicamente sostenibile.
Precisione garantita
Le caratteristiche principali di queste macchine sono sviluppate sulla base di una lunga esperienza in una vasta gamma di condizioni di lavorazioni critiche e nelle più diverse applicazioni. Innanzitutto le tavole sono dotate di cuscinetti speciali per garantire la minima deformazione in direzione X e Y in funzione del pezzo cliente: variabili quali il peso del pezzo, la sua altezza, il regime di rotazione che verrà raggiunto (e quindi di sviluppo di calore) sono tutte caratteristiche che modificano la risposta della cuscinetteria che, per non scendere a compromessi, deve essere scelta opportunamente e diversificata.
La struttura della macchina è stata sviluppata sulla base di analisi FEM e progettata in modo termosimmetrico. Ciò significa che, in presenza degli inevitabili gradienti termici ambientali, la struttura della macchina si comporterà in maniera lineare e prevedibile. Nell’aeronautico, dove i controlli e le verifiche degli impianti produttivi sono molto frequenti, le macchine ATF hanno dato prova di una affidabilità prossima al 99%.
Alta dinamica grazie ai direct drive
La tecnologia direct drive è operativa sulle macchine della Pietro Carnaghi dal 2007: da allora è progredita guadagnando in termini di affidabilità e prestazioni, fino a giungere oggi a soluzioni estremamente raffinate, in linea con il resto della meccanica e dell’elettronica degli impianti sui quali è equipaggiata.
L’ultima evoluzione è un motore, ideato e progettato dalla Pietro Carnaghi e realizzato da un partner strategico, capace di unire i benefici delle motorizzazioni tradizionali (alta potenza, coppia e giri) alle qualità dei direct drive (elevata dinamica, assenza di giochi e rinvii meccanici ecc.).
Per ottenere questo mix di performance è stato necessario riprogettare alcuni componenti chiave, oltre a rivedere il circuito di raffreddamento per assicurare la massima affidabilità anche in condizioni di utilizzo gravose. Ad oggi sono circa 50 i motori basati su questa tecnologia che operano senza problemi su altrettanti impianti, oltre a un modello installato nell’officina della Pietro Carnaghi operativo da 7 anni su tre turni.
Per sua natura, un motore direct drive è in grado di azzerare l’errore di inseguimento: questa caratteristica risulta fondamentale durante le contornature e con l’utilizzo dell’asse C.
La presenza di assi lineari idrostatici è un must che garantisce il massimo in termini di affidabilità e smorzamento vibrazioni. Oltre a ciò uno sviluppo intenso dell’idrostatica ha permesso inoltre di ottenere ulteriori vantaggi in fase di accelerazione e di velocità massima raggiungibile (40 m/min).
Alta dinamica non implica scarsa potenza: tra le applicazioni nelle quali le ATF si distinguono vi è l’Oil & Gas, con materiali particolarmente difficili da lavorare (Stellite gr 21, ad esempio) e richieste di elevati volumi trucioli asportati. Questo dimostra come la macchina assicuri grandi precisioni e dinamiche spinte, ma anche potenze generose con la giusta rigidezza.
Sono così sufficienti due piazzamenti su una sola macchina quando, in precedenza, erano necessari quattro piazzamenti su due macchine distinte.
Accessori di fascia alta
È chiaro come la fresatura non rappresenti più un optional sui centri di tornitura: nel caso delle ATF, anzi, diventa parte fondamentale della tecnologia disponibile. L’asportazione di truciolo avviene attraverso l’impiego di teste accessorie, che vengono cambiate automaticamente in macchina in funzione dell’operazione da eseguire.
Rispetto all’utilizzo di una testa integrata in grado di fresare e tornire, la soluzione di Pietro Carnaghi è pensata per evitare qualsiasi compromesso. Le teste a fresare installabili sulla serie ATF sono di svariate tipologie. Oggi il range di accessori è così ampio da poter includere operazioni prima non pensabili su un centro di tornitura: foratura profonda, fresatura di ingranaggi (hobbing, gashing), fresatura a 5 assi interpolanti ad alta velocità, ad esempio in grado di lavorare anche a 10.000 giri/min, con ausilio di cuscinetti ceramici in grado di ridurre il calore sviluppato e migliorare le condizioni operative del mandrino. Il must è quindi affiancare le più complete teste di fresatura e operazioni accessorie a quelle di tornitura, robuste e stabili.
Parlando di rettifica, si sono sviluppati una serie di accessori con specifica testa di rettifica dotata di elettromandrino integrato, per generare il moto direttamente dove occorre, in asse con la mola stessa e con un numero di giri superiore. Ravvivamento della mola e sistema di cambio mole in automatico completano le automazioni in questo campo. Oltre agli accessori dedicati, Pietro Carnaghi propone una soluzione ad hoc con carro di rettifica dedicato (versione SH) in grado di eseguire operazioni complete.
Operazioni complesse, senza problemi
L’obiettivo di ogni azienda manifatturiera è ridurre i costi di produzione: il metodo più semplice – sulla carta – è quello di lavorare su una singola macchina per azzerare gran parte dei tempi morti dovuti allo spostamento dei pezzi e alla conseguente perdita in termini di produttività e precisione.
Per ottenere questo risultato le macchine devono però garantire una multifunzionalità estremamente spinta: la serie ATF è pensata proprio in quest’ottica, poiché integra una serie di funzionalità che ne estendono le possibilità operative.
Oltre alle consuete operazioni di tornitura e fresatura, la macchina è in grado di effettuare operazioni anche molto complesse. La dimensione dei pezzi e la dinamica degli assi, unita alla fluidità dell’asse X idrostatico, all’assenza di giochi e alle capacità di elaborazione dei moderni controlli numerici, ha permesso a Pietro Carnaghi di implementare contemporaneamente lavorazioni complesse. Tra queste sicuramente la tornitura eccentrica, che permette di tornire fuori asse mandrino e la cui buona riuscita è direttamente proporzionale alla qualità della macchina e sistemi assi.
Rapido ritorno dell’investimento
L’acquisto di impianti con queste caratteristiche va analizzato da due punti di vista: quello tecnico e quello legato al ritorno dell’investimento.
Nel primo caso, non tutti i costruttori di macchine possono offrire soluzioni in grado di effettuare operazioni complesse, precise, produttive e ripetibili.
In secondo luogo, per ottenere utile è necessario anche che la macchina produca senza interruzioni inattese e con un costo di gestione accettabile. Proprio su quest’ultimo punto insiste la Pietro Carnaghi: poter contare su un impianto affidabile, di facile ed economica manutenibilità e performante nel tempo significa migliorare la sua capacità di ammortamento negli anni e ottenere il ritorno dell’investimento senza costi inattesi.
Dettagli di valore
ATF è un centro multitasking che può lavorare sia in modalità stand alone, sia insieme ad altre macchine in FMS ad elevata automazione.
Una recente applicazione vede infatti al lavoro diverse celle composte da centri di tornitura e fresatura ATF per la realizzazione di diversi componenti per i gruppi di trasmissione e di potenza di motori.
La pallettizzazione consente di azzerare i tempi morti, a patto di eseguirla nel migliore dei modi: Pietro Carnaghi ha sviluppato un sistema che garantisce una ripetibilità entro i 5 micron. Ciò significa che i pallet hanno performance paragonabili a quelle di un basamento fisso.
Questo risultato è stato raggiunto poiché l’azienda esegue tutte le lavorazioni nella propria officina, dove macchine utensili di qualità, ambienti climatizzati, ottimi materiali e controlli rigorosi concorrono a massimizzare le prestazioni degli impianti.
Supervisione completa
Tanti muscoli hanno bisogno di altrettanto cervello: nell’ottica della fornitura di un sistema chiavi in mano, l’ufficio tecnico della Pietro Carnaghi può intervenire a diversi livelli per assicurare la soluzione di un problema tecnologico.
In presenza di impianti complessi, quali gli FMS, un software gestisce la produzione con un sistema di scheduling completo. Diversi gli aspetti sviluppati e gestiti dal sistema.
Dal pieno management dei dati di singola macchina alla gestione dei pallet: al crescere del loro numero sale la complessità (in particolare se è necessario gestire componenti differenti e con diversi livelli di priorità in base a più variabili).
Inoltre è disponibile una tool room centrale nella quale l’operatore può intervenire su singoli utensili che, attraverso un sistema a navette, vengono distribuiti sulle diverse macchine. In questo modo è possibile tenere traccia e gestire al meglio migliaia di utensili, senza sprechi legati a utensili inutilmente ridondanti né fermi macchina dovuti a inefficienze del magazzino.
Condividi l'articolo
Scegli su quale Social Network vuoi condividere