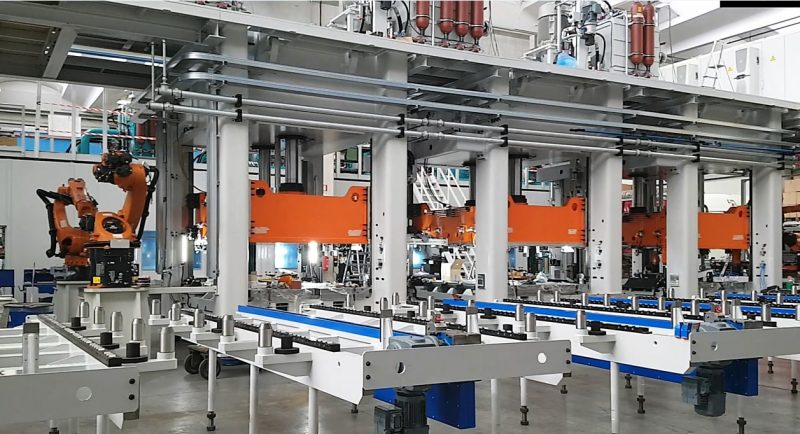
Miramondi e Bosch Rexroth progettano di ottimizzare il ciclo di lavoro di un impianto per lavorazione lamiera, contenendo i consumi elettrici.
Può la moderna oleodinamica assecondare la sempre più diffusa esigenza di sostenibilità ambientale, avvertita anche in ambiti apparentemente “ostili” all’argomento come le aziende metallurgiche, energivore per loro stessa natura? Sì, indubbiamente, e ne è dimostrazione l’esperienza di Miramondi, impresa manifatturiera del milanese specializzata nella costruzione e nella vendita di impianti, macchine ed attrezzature per la lavorazione e l’assemblaggio di componenti in lamiera per il mondo degli elettrodomestici.
«Progettiamo e realizziamo – premette Giacomo Gatti, Coordinator del dipartimento Hydraulic Engineering di Miramondi – impianti automatici customizzati per la lavorazione della lamiera a freddo. Il materiale grezzo in ingresso si trasforma in uscita in un prodotto che può essere il cestello della lavatrice, il cabinet di un’asciugatrice, la porta di un frigorifero. Le nostre linee di produzione sono divise in due grandi famiglie, vale a dire formatura ed assemblaggio». Ciò detto, va sottolineato che in questo tipo di stabilimenti uno degli impianti più energivori è costituito dalle presse idrauliche. «Uno dei progetti che abbiamo portato a termine per ridurre il loro consumo – rivela Gatti – riguarda uno stabilimento che produce porte per frigoriferi a stampaggio». L’impianto in questione è formato da 6 presse idrauliche che lavorano in parallelo con un ciclo di 12 s, in grado ciascuna di spostare carichi che possono arrivare a 18 t. La potenza installata di tutto l’impianto sfiora 1 MW. «Avendo ricevuto la richiesta – racconta il manager di Miramondi – di mettere in funzione sistemi di riduzione dell’impatto energetico, ci siamo rivolti a Bosch Rexroth per implementare l’impianto con gruppi energetici a giri variabili su presse idrauliche».
Il senso stesso dell’intervento effettuato lo spiega nei dettagli Stefano Peschiaroli, Sales Product Management Industrial Hydraulics dell’azienda del druppo Bosch e realtà di vertice globale in tecnologie integrate per l’automazione industriale e la movimentazione di macchine operatrici mobili: «Esiste una stretta correlazione tra idraulica connessa e risparmio energetico basata sull’evidenza che non tutte le fasi di un ciclo produttivo richiedono la massima potenza di cui un sistema è capace». Circostanza che riguarda anche le presse, macchinari che nelle diverse fasi di lavorazione vivono momenti in cui necessitano di maggiore energia, ed altri nei quali ne richiedono in misura minore. «Nei sistemi di efficientamento prodotti e distribuiti da Bosch Rexroth – puntualizza Peschiaroli – l’inverter gestisce le varie fasi in cui viene richiesta meno energia adattando il numero di giri del motore elettrico. Ed è questo il preciso momento in cui avviene la fase di risparmio energetico ed economico».
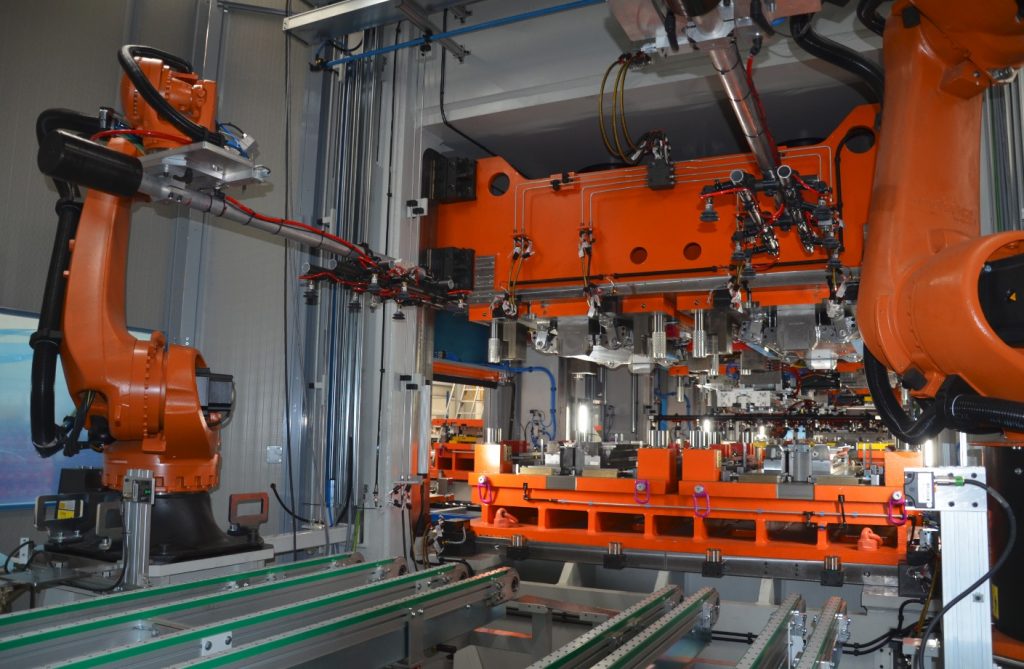
Vero è inoltre che non in tutti i momenti di vita di uno stabilimento l’utilizzo della potenza nominale risulta indispensabile. Le ragioni sono molteplici e Gatti ne illustra un paio. La prima: «Ci sono fasi del ciclo produttivo dove è previsto il trasferimento di un pezzo tra una pressa e l’altra, stadi di lavorazione in cui entrambe le macchine sono ferme e possono, anzi devono, consumare meno». L’altra: «Nelle linee multiprodotto è possibile ottimizzare l’output energetico fornito dalla centrale idraulica adattandolo al prodotto in quel momento lavorato, realizzando così forme di contenimento dei consumi elettrici».
«Nelle aziende metallurgiche dotate di presse di grandi dimensioni – specifica ancora Peschiaroli – l’ottimizzazione del programma della macchina, possibile se equipaggiata con motore a giri variabili, rappresenta un grande risparmio per il cliente, un vantaggio che non potrebbe essere conseguito attraverso l’intervento dell’idraulica tradizionale, ma è realizzabile grazie all’idraulica connessa». Non solo: «Stiamo parlando di impianti complessi – fanno notare in Miramondi – i cui componenti possono essere costantemente monitorati, così da acquisire in ogni singola fase moltissimi parametri, relativi ad esempio ai sensori di pressione o allo stato di salute delle valvole. È un’opportunità che l’idraulica connessa offre, e che si traduce in una serie di benefici che vanno dalla semplificazione della diagnostica in fase di commissioning all’opportunità di effettuare da remoto la manutenzione delle macchine».
Condividi l'articolo
Scegli su quale Social Network vuoi condividere