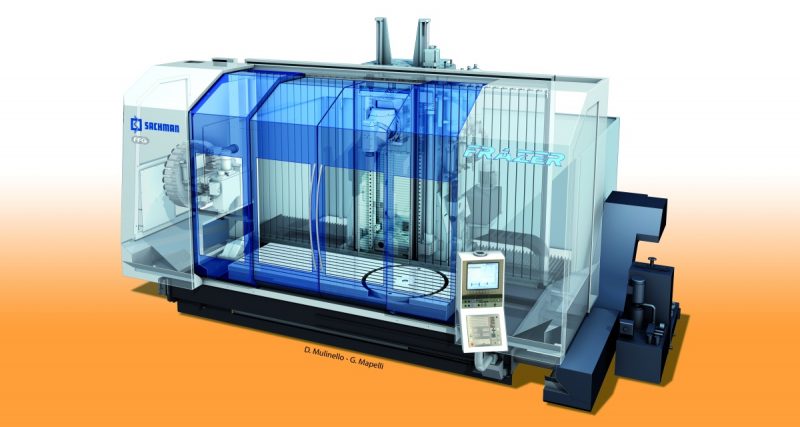
Configurazione orizzontale, struttura aperta o chiusa, massima flessibilità nella scelta della testa di fresatura e bassi costi di esercizio: Frazer di Sachman si caratterizza per una serie di qualità particolarmente apprezzate nel mondo dei terzisti evoluti
Immettere sul mercato un nuovo modello di macchina utensile – o una versione rinnovata – richiede attenti studi: di mercato (qual è la richiesta?), tecnologici (sotto quali aspetti altri modelli analoghi sono carenti?) e più in generale sulla percezione dei clienti nei confronti di una specifica soluzione.
È proprio questa la strada percorsa da Sachman, brand della piacentina Jobs (Gruppo FFG) che si occupa della produzione di macchine di fresatura in configurazione orizzontale, in occasione del lancio della nuova Frazer.
Pensata per esigenze specifiche
Innanzitutto occorre considerare che quello delle macchine in configurazione orizzontale per la lavorazione di pezzi di dimensioni medio-grandi è una nicchia che vede i maggiori numeri sul mercato italiano. Si tratta infatti di una soluzione molto più diffusa in Italia rispetto a quanto avvenga in altri Paesi e, in particolare, viene apprezzata dalle imprese che si occupano di lavorazioni conto terzi.
Tenendo conto di questa prima, importante informazione, i tecnici Sachman hanno perciò completato la propria offerta inserendo a catalogo un modello con caratteristiche specifiche.
Un’ulteriore indicazione deriva dall’utilizzatore-tipo: il contoterzista lavora a ore, non a pezzi, quindi ha tutto l’interesse nell’utilizzare macchine capaci di abbatterne costi.
Con Frazer l’obiettivo è stato raggiunto poiché si tratta di un prodotto con un costo orario contenuto e particolarmente adatto alle condizioni applicative tipiche dei terzisti.
Basso costo orario
Come è possibile abbassare il costo orario di una macchina? Anzitutto diminuendone il costo di acquisto: Frazer offre un ottimo rapporto prezzo/prestazioni grazie alla significativa riduzione del numero di componenti utilizzati e a un processo produttivo della macchina stessa ben ingegnerizzato.
Un altro aspetto importante è quello rappresentato dai costi ricorrenti e non ricorrenti, con particolare riferimento a quelli manutentivi. I progettisti Sachman hanno lavorato per ridurre al minimo la manutenzione necessaria, rendendola nel contempo semplice, poco invasiva e alla portata dell’operatore macchina.
Il terzo punto, non meno importante, è quello legato al service: i clienti giustamente pretendono un servizio sempre al top, per questo un’accurata ottimizzazione dei processi e degli interventi può migliorare l’impatto economico. Minimizzare i tempi di intervento favorisce inoltre l’attività in officina.
Lavorare con un basamento realizzato in un unico pezzo significa poter spedire la macchina in due sole parti, con evidenti vantaggi sul fronte dei tempi e dei costi di spedizione e, non meno importante, nei tempi di installazione presso il cliente. A tal proposito, la rigidezza complessiva è tale che un buon pavimento industriale e un corretto livellamento sono sufficienti a sorreggere e mantenere in posizione la macchina durante la lavorazione, escludendo la necessità di dover intervenire in officina con lunghe e costose opere murarie di fondazione.
Progettazione accurata
Anni fa la valutazione sommaria della qualità di una macchina era legata al suo peso: più era pesante, più la struttura sarebbe stata in grado di assorbire vibrazioni, sforzi ecc.
Oggi qualsiasi ufficio tecnico sa che l’importante è inserire ciò che realmente contribuisce a una determinata prestazione, eliminando tutto ciò che non è utile. La progettazione di strutture basate sull’analisi agli elementi finiti è perciò all’ordine del giorno anche in Sachman, dove vengono irrobustiti i particolari più sollecitati e snelliti quelli che devono presentare caratteristiche dinamiche spinte. I componenti in movimento vengono dimensionati bilanciando accuratamente le masse al fine di assicurare la massima rigidezza possibile senza risultare vincolanti sul fronte delle prestazioni: da questo punto di vista i software di simulazione assicurano risultati eccellenti e permettono di intervenire in modo quasi chirurgico nella distribuzione delle masse e nel loro contributo alle caratteristiche della macchina.
Oltre all’analisi FEM, oggi è possibile simulare il comportamento di una macchina prima che questa venga fisicamente assemblata. L’accuratezza di questi software è superiore all’85%, il che permette di inserire un part program nella macchina virtuale e per ottenere una stima delle prestazioni tramite il simulatore. Si possono così valutare le effettive caratteristiche del progetto e decidere se proseguire con lo sviluppo o se occorre effettuare variazioni al progetto.
La struttura della Frazer è derivata dalla Thora, un altro modello di produzione Sachman del quale mantiene le caratteristiche di stabilità termica e dimensionale che l’hanno fatta apprezzare sul mercato. Pur richiamando il montante della Thora, Frazer presenta dimensioni inferiori e per questo sono state fatte scelte progettuali che hanno avuto un impatto positivo sui costi complessivi, mantenendo le elevate prestazioni richieste dal mercato.
Frazer dispone di una struttura a montante mobile in acciaio elettrosaldato e può essere configurata in versione open o box. La prima è priva di carenature e l’asse X è modulare in lunghezza, idonea quindi alla lavorazione di parti con uno sviluppo longitudinale importante oppure per effettuare operazioni su due distinte aree (lavorazione pendolare) e risulta particolarmente adatta ad ambiti applicativi quali l’energetico, l’aeronautico, la lavorazione dei compositi ecc.; la seconda prevede una carenatura completamente chiusa con misure da 3 a 5 mila mm sull’asse X e 1500 mm in Y, adatta per la meccanica generale e il settore degli stampi di medie dimensioni.
Il basamento è pensato per rispondere ad alcune esigenze espresse esplicitamente dagli utilizzatori: l’evacuazione del truciolo si è dimostrato un elemento critico per questa tipologia di macchine, motivo per il quale Sachman ha studiato un sistema di smaltimento particolarmente efficiente. Nella versione box, inoltre, il basamento è stato realizzato in codesign con il costruttore della cabina al fine di mantenere i fluidi di processo sempre all’interno della macchina, che risulta così perfettamente a tenuta. Il beneficio è importante anche per una questione ecologica, poiché in molti Paesi le leggi in tal senso sono molto severe e non ammettono possibili sversamenti (anche minimi) al di fuori della macchina stessa.
Come accennato, il montante mobile deriva da quello della Thora, mentre il Ram è sorretto da 4 guide a rulli precaricate che ne assicurano il massimo livello di rigidità. I movimenti degli assi sono di tipo misto: l’asse X viene mosso da un sistema a doppio pignone motorizzato su cremagliera, mentre gli assi Y e Z sfruttano viti a ricircolo di sfere.
La modularità dell’asse X trae evidente beneficio dalla modularità della soluzione a cremagliera: l’elettronica di comando e il relativo software, insieme al sistema di trasmissione a doppio pignone con recupero dei giochi, assicurano una precisione molto spinta anche su corse significative. Si tratta di una soluzione che Sachman utilizza da circa 10 anni e che assicura prestazioni elevate unite a una messa a punto semplice e veloce.
Teste e accessori
Al di là della configurazione scelta – open o box – è la tipologia di testa a definire l’utilizzo della Frazer. In quanto parte integrante di FFG Europe, Sachman può beneficiare delle soluzioni tecnologiche disponibili presso le altre realtà del gruppo: da questo punto di vista, la varietà di teste sviluppate da Jobs è a disposizione dei clienti Sachman, che possono così scegliere quella più idonea sulla base delle specifiche esigenze.
La testa Universale è un modello esclusivo di Sachman ideale per la meccanica generale e rappresenta la scelta più frequente dei clienti: si tratta di una soluzione indexata con risoluzione di 0,02 centesimi di grado realizzata tramite doppia dentatura Hirth che consente di generare tutte le posizioni attraverso l’accoppiamento della doppia dentatura.
I modelli realizzati per lavorare in continuo sono invece derivati dall’esperienza Jobs: si tratta di soluzioni varie in termini di capacità, coppia, potenze (fino a 40 kW) e regimi di rotazione (fino a 24 mila giri/min). Complessivamente, sono 22 le teste installabili sulla Frazer, assicurando così la massima possibilità di scelta in funzione delle necessità dell’utilizzatore.
Un altro accessorio in grado di variare notevolmente le capacità operative della Frazer è la tipologia di tavola: oltre a quella fissa, infatti, Sachman ha previsto un modello girevole e uno per tornitura.
Abbinata a una testa con elettromandrino ad alte prestazioni con asse continuo, la versione girevole può trasformare la Frazer in un centro di fresatura a 5 assi continui. Quella per tornitura, invece, è in grado di raggiungere i 400 giri/min, adatti all’esecuzione di torniture di mediamente impegnative sui componenti.
La disponibilità di utensili varia anch’essa in base alle necessità operative: si parte dalla soluzione a 24 posizioni per salire a quelle a catena a bordo macchina (il magazzino a fine corsa X consente di ridurre le dimensioni della macchina). Una terza configurazione prevede un cambio utensile modulare sviluppato da Sachman e dotato di un robot centrale che si occupa della gestione degli utensili, dal recupero all’installazione sul cono mandrino.
Sachman ha infine previsto l’integrazione con tutti i principali costruttori di controlli numerici, in particolare Heidenhain, Siemens, Fanuc e Fidia.
Semplice da utilizzare e manutenere
Quello della minor invasività possibile presso il cliente è un punto sul quale Sachman insiste particolarmente: dal trasporto su camion all’installazione, ovviamente con tempistiche molto ridotte, tutto è pensato affinché l’utilizzatore finale abbia ciò che chiede, nel minor tempo possibile e con la massima efficienza.
Sul fronte manutentivo, poi, il materiale di consumo o quello soggetto a usura sono facilmente gestibili da un tecnico. Frazer è poi dotata di una serie di sensori in grado di monitorarne le condizioni operative e di rivelare eventuali criticità dovute al deterioramento di un componente, consentendo un intervento tempestivo o permettendo di procedere fino al successivo stop programmato per evitare interruzioni della produzione.
Ad esempio, la lubrificazione automatica delle guide e delle trasmissioni è affidata a sistemi di ultima generazione che, oltre a lanciare un allarme, indica anche la tipologia di problema, la posizione e, attraverso l’interfaccia del controllo numerico, come intervenire per risolverlo.
Anche le teste sono sensorizzate: a seconda del modello e delle relative caratteristiche, vengono monitorate le accelerazioni, le vibrazioni o le temperature.
Massima ergonomia
L’operatore è il primo a trarre un beneficio dall’utilizzo di una macchina a “misura d’uomo”. Non si tratta di modelli pensati per la produzione senza presidio di migliaia di pezzi: per gli stampi si parla di pezzi unici, mentre per l’aeronautico si producono in kit componenti singoli che si ripetono periodicamente. L’interazione con l’uomo è dunque molto importante, e ogni soluzione che ne faciliti il lavoro è strategica.
Assicurare una sorveglianza spinta si è rivelato un fattore chiave nella scelta di una macchina di questo tipo, per questo sulla versione open della Frazer è stata prevista la presenza dell’operatore a bordo macchina.
Si pensi, ad esempio, al caso della lavorazione di pezzi montati contro una squadra: stando di fronte non sarebbe possibile osservare il processo, mentre grazie a una postazione operatore a bordo è possibile effettuare operazioni di verifica in visione diretta o intervenire direttamente sul pezzo – a macchina ferma – per effettuare eventuali rilievi.
In un caso è stata quindi pensata una cabinatura efficiente dal punto di vista del contenimento, mentre dall’altro vengono offerte possibilità di sorveglianza molto spinte.
Condividi l'articolo
Scegli su quale Social Network vuoi condividere