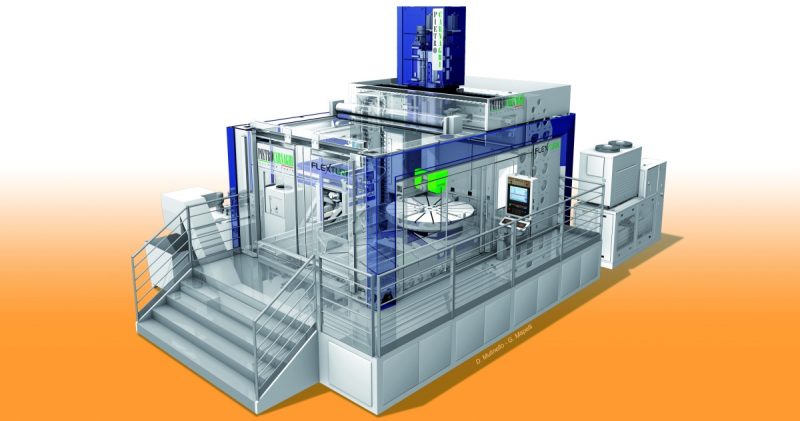
Unire tornitura verticale e fresatura ad alta potenza in un solo modello: con Flexturn la Pietro Carnaghi ha sfruttato il proprio know how per offrire una soluzione che non scende a compromessi
di Andrea Pagani
La lavorazione in verticale è uno dei punti di forza della Pietro Carnaghi: decenni di esperienza nella progettazione e nella costruzione di queste macchine – molte destinate a settori applicativi estremamente esigenti – hanno permesso all’azienda di Villa Cortese, in provincia di Milano, di accumulare un significativo know-how in materia. E proprio da questo know how nasce Flexturn, un centro di tornitura verticale che unisce esperienza, capacità operativa e prestazioni ai vertici della propria categoria per completare una gamma di soluzioni multitasking che in casa Pietro Carnaghi include già altri modelli che fanno leva sull’alta possibilità di personalizzazione. Si tratta del consolidamento, contestuale a tanti anni di esperienza in tornitura in settori critici quali l’aeronautico, di questa specifica taglia di macchina Pietro Carnaghi, arricchita con una “iniezione tecnologica” importante, e includendo le operazioni di fresatura più complesse richieste su pezzi così critici (per il valore unitario e per la difficoltà intrinseca di lavorazione).
Una macchina ben dimensionata
Vantando caratteristiche innovative, Flexturn è un tornio verticale con una funzione di fresatura arricchita e sviluppata con la migliore tecnologia attualmente disponibile. Il design rispecchia le caratteristiche tipiche dei torni verticali Pietro Carnaghi, ossia rigidità e precisione unite a funzionalità di fresatura ai massimi livelli, e capacità di entrare in profondità nel pezzo in verticale, sia durante le operazioni di fresatura che di tornitura grazie a un robusto Ram. Disponibile in due configurazioni, a traversa fissa e a traversa mobile (modello W), Flexturn è nata per offrire la migliore qualità possibile di tornitura su macchine di questa taglia (2.500 mm di diametro lavorabile).
La tornitura è infatti una lavorazione in grado di mettere a dura prova le macchine utensili in termini di materiali, forze e reazioni sulla struttura: a partire dai tagli interrotti più impegnativi dal punto di vista delle forze impattanti fino all’hard turning con precisione e rugosità prossime a quelle della rettifica, Flexturn è pensata per assicurare risultati ottimali in ogni condizione operativa. Questo anche grazie alla struttura opportunamente dimensionata attraverso un software di ottimizzazione agli elementi finiti (FEM) e all’esperienza dell’azienda che, sulla base degli oltre mille macchinari installati nel corso degli anni e operativi in tutto il mondo, hanno pensato a ogni situazione operativa.
Il peso di Flexturn, 75 tonnellate, lascia intuire la qualità strutturale utilizzata rispetto alle altre macchine del segmento: non si tratta di un puro esercizio di stile, ma di contrastare tutte le forze indotte dalla lavorazione. Questi vantaggi sono ancora più evidenti con il passare del tempo: questa tipologia di macchina è infatti destinata a lavorare per molti anni, decenni, ed è sul medio periodo che una struttura ben dimensionata si differenzia da altre soluzioni più leggere. Lavorare un componente di precisione anche in presenza di forti stress termici e strutturali, il tutto con margine per gestire errori o imprevisti (come sovrametalli superiori al previsto), è un valore aggiunto di assoluto rilievo per le moderne officine.
Ergonomia ai massimi livelli
Tutte queste possibilità comportano naturalmente un arricchimento della macchina a livello tecnologico, ma non per questo è necessario rinunciare alla compattezza e alla praticità di impiego: i tecnici hanno lavorato molto sul concetto di ergonomia, poiché il cliente non è solo l’acquirente della macchina ma è anche (e soprattutto) l’operatore, che deve potere contare su una soluzione in grado di eseguire le varie lavorazioni con le tolleranze, i tempi, i costi e anche l’ergonomia necessaria affinché le operazioni possano essere svolte in modo agevole e comodo. Per questo Flexturn dispone di un accesso ottimale al pezzo e un’ampia visibilità della zona di lavoro. La natura verticale della macchina permette di entrare facilmente nel campo di lavoro per lo staffaggio del pezzo o per le verifiche durante il processo di lavorazione, oltre a migliorarne la precisione e la finitura grazie alla minimizzazione delle interpolazioni tra gli assi. L’ergonomia è massima anche dal punto di vista della manutenzione. Tutto può essere gestito in modo semplice attraverso un unico energy box che contiene tutte le utenze ed è posizionato in un punto di facile accesso.
Un dettaglio molto apprezzato da chi ha già Flexturn nella propria officina è la pressoché assenza di fondazioni: grazie a una struttura ben bilanciata, infatti, è sufficiente un pavimento industriale di qualità sul quale fissare la macchina per ottenere le prestazioni promesse. Altro aspetto interessante, gli avanzamenti in rapido degli assi lineari X/Y/Z raggiungono i 40 m/min e assicurano la massima accelerazione con zero attrito.
Accessori e opzioni
Flexturn si avvale di una serie di accessori utili per eseguire tutte le lavorazioni richieste come teste universali, verticali e orizzontali di potenza, elettromandrini eccetera. Gli accessori per tornitura sono accoppiati tramite anello Hirth, che assorbe gli sforzi e rende più stabili anche le operazioni più impegnative come quelle a taglio interrotto.
Offre inoltre un sistema di lubrificazione aria/olio e fino a 6.000 giri/min in fresatura attraverso l’uso di direct drive (quindi con motori che minimizzano le catene cinematiche grazie a una trasmissione ridotta al minimo e conseguente riduzione delle vibrazioni indotte).
L’albero di trasmissione per la fresatura è in carbonio: questo materiale assicura la massima rigidità e leggerezza, oltre a ridurre le variazioni dimensionali indotte dalla temperatura. Dal punto di vista delle lavorazioni multitasking, l’asse C garantisce un movimento della testa fresante all’interno di un RAM studiato per avere sia la rigidità richiesta dalle operazioni di tornitura, sia la compattezza necessaria per permettere alla testa di fresatura di entrare all’interno di diametri contenuti tipici di molti pezzi. La testa è intercambiabile tra dispositivi per la fresatura e per la tornitura, affinché la macchina sia equipaggiata con la tecnologia più idonea per la lavorazione da compiere.
In ambito fresatura la Pietro Carnaghi ha investito molte risorse: le operazioni multitasking, infatti, rappresentano il naturale complemento della tornitura. Per questo l’azienda ha creato un reparto che si occupa dell’assemblaggio e della costruzione di teste di fresatura e del relativo collaudo, affinché le caratteristiche siano esattamente quelle che il cliente richiede. Qui sofisticati banchi prova verificano le teste universali dal punto di vista del movimento degli assi, della lubrificazione, dell’adduzione di refrigerante e ovviamente del mandrino di fresatura.
Trattandosi di parti standardizzate, sono sempre disponibili come ricambio da spedire nel giro di 24 ore a quei cliente che dovessero averne necessità. La tavola di tornitura è equipaggiata con un particolare direct drive costruito da Pietro Carnaghi e denominato 2DD, doppio direct drive. Unisce infatti vantaggi che solitamente sono presenti in due differenti motorizzazioni, ovvero potenza, giri e coppia su una curva ottimale che è la somma delle migliori caratteristiche delle soluzioni tradizionali con trasmissione meccanica e di quelle dei motori direct drive. In questo modo si uniscono due soluzioni – quella specifica per alti numeri di giri e quella ad alta coppia/potenza – estremamente performanti e superiori rispetto ai motori tradizionali, il tutto con un posizionamento angolare di alta precisione (fino a 0,001°). Il magazzino utensili prevede un minimo di 40 posti – suddivisi tra tornitura e fresatura – e può essere espanso sulla base delle necessità dell’utilizzatore (fino a 380 unità).
Il diametro lavorabile raggiunge i 2500 mm, mentre la tavola può essere scelta tra tre modelli rispettivamente con diametro da 1600, 1800 e 2000 mm.
Processo sempre sotto controllo
La sempre maggiore sensorizzazione sta migliorando la comprensione di ciò che avviene in una moderna macchina utensile al fine di utilizzarla sempre al meglio. Da questo punto di vista, Flexturn trae beneficio da CMS (Connected Machine Supervisor): un sistema di sonde per il controllo di temperatura, pressione, vibrazione eccetera. È una tecnologia smart che nasce ormai alcuni anni fa per eseguire la manutenzione predittiva e che, oggi, si sposa con i paradigmi dell’Industria 4.0.
CMS è dunque un insieme di hardware (le sonde) e di software per l’analisi delle informazioni che la macchina genera in tempo reale. In funzione dei settaggi impostati, CMS può segnalare eventuali anomalie all’operatore o intervenire per evitare problemi al pezzo o alla macchina. Un carico sbilanciato, il surriscaldamento di un componente o un assorbimento anomalo vengono prontamente gestiti per un intervento immediato, oltre a essere resi disponibili sottoforma di dati da elaborare successivamente per uno storico accurato delle condizioni operative.
Cell-X, da macchina a FMS intelligente
Flexturn è pensata per essere anche pallettizzata: in questo modo si minimizzano i tempi morti e si aumenta la ripetibilità nelle lavorazioni. Celle complesse possono essere quindi equipaggiate con software di controllo gestione produzione. Pietro Carnaghi ha prodotto un software specifico, chiamato Cell-X, che si occupa della gestione dell’FMS con una serie di interessanti funzioni proprie dell’Industria 4.0.
Il sistema di controllo centralizzato consente una integrazione totale della macchina all’interno dell’intero stabilimento: l’interfaccia di gestione consente di accedere a tutti i dati inseriti e generati dall’FMS, elaborandoli per ottenere informazioni aggiuntive utili per migliorare le performance operative e per ottimizzare gli intervalli di manutenzione.
Operativo sia on-site su server dedicati, sia in remoto attraverso il cloud, Cell-X è in grado di verificare lo stato meccanico della macchina (idrostatica, idraulica, tasche idrostatiche eccetera), degli azionamenti (coppia, assorbimenti, temperature eccetera) e di verificare lo stato vibrazionale (analisi in frequenza tramite accelerometri) per generare un modello di sintesi di stato della macchina.
Questo consente di valutare l’andamento delle varie macchine e di stabilire la pianificazione della produzione sulla base dei singoli stati di funzionamento, modificando le priorità produttive sulla base della manutenzione prevista.
Condividi l'articolo
Scegli su quale Social Network vuoi condividere