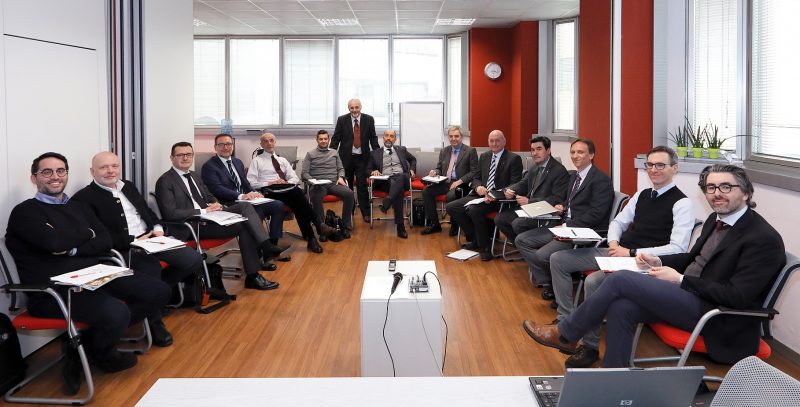
Affidabilità, prestazioni, semplicità d’uso e contenimento dei costi sono le principali caratteristiche che i clienti chiedono ai costruttori di impianti e sorgenti laser, in fibra e diodo.
Affidabilità, prestazioni, semplicità d’uso e contenimento dei costi sono le principali caratteristiche che oggi i clienti chiedono ai costruttori di impianti e sorgenti laser, in fibra e diodo, al fine di raggiungere quel livello di qualità del prodotto indispensabile per rimanere competitivi sul mercato.
di Flavio della Muzia ed Ezio Zibetti
Alla soglia della quarta rivoluzione industriale, ogni settore del manifatturiero sta compiendo i passi necessari per affrontare questo nuovo viaggio che coinvolge clienti, costruttori e integratori. E anche il comparto della produzione di macchine e sistemi laser si sta dimostrando molto attivo sotto l’aspetto dell’innovazione tecnologica con il passaggio dagli impianti a CO2 per il taglio delle lamiere, peraltro ancora molto attivi in taluni ambiti, alle sorgenti laser in fibra e diodo che, specialmente in questi ultimi tempi, hanno fatto registrare tassi di crescita davvero importanti anche grazie a costi d’esercizio ridotti, grande affidabilità e semplicità d’uso, in risposta alle richieste provenienti da un mercato sempre più competitivo. Abbiamo dunque incontrato alcuni tra i maggiori costruttori di macchine e sorgenti laser per avere un quadro generale circa la situazione economica e tecnologica di un settore che vede sempre più la richiesta di prodotti altamente performanti, accompagnati da un servizio di assistenza tecnica e ricambistica molto qualificato.
Stiamo vivendo, in generale, un momento positivo del mercato. Dalla vostra posizione privilegiata, come valutate l’andamento del settore macchine e sistemi laser, in particolare?
Giovanni Di Stefano, Comau
«Negli ultimi sette anni abbiamo registrato un tasso di crescita media, nella richiesta di sistemi laser, pari al 9% annuo. Per questo motivo nel 2017, assieme al nostro partner Prima Electro, abbiamo sviluppato una sorgente Comau proprio per seguire questa tendenza. Non prevediamo che il settore possa subire una flessione nel prossimo futuro in quanto anche i vecchi clienti, utilizzatori del laser, si stanno consolidando. In generale, poi, anche in quei comparti laddove un tempo questa tecnologia non era presente in maniera massiccia oggi esiste un vivo interesse: per esempio nel settore dello stampaggio, quella che prima era una realtà un po’ localizzata oggi si sta invece sviluppando a livello globale, con sempre più clienti che utilizzano il laser per sviluppare al meglio le giuste durezze in alcune zone della vettura».
Maurizio Gattiglio, Convergent Photonics
«Dal nostro punto di vista, il fatturato del Gruppo dello scorso anno è stato estremamente positivo, direi da record, toccando quasi i 400 milioni di euro, quindi sulla scorta dell’ottimo risultato del 2016 le aspettative per il 2017 non possono che essere positive, con una crescita globale del mercato delle sorgenti che si attesta attorno al 5-6% annuo. In realtà, se vogliamo vedere l’altro lato della medaglia, ci possono essere delle possibili preoccupazioni per il mercato italiano, con fenomeni di aiuti economici e vantaggi fiscali che, sicuramente, influenzano il mercato stesso. In questo momento, poi, è in atto una grande crescita del settore nei Paesi asiatici, con un’enorme pressione sui costi e, inoltre, la tecnologia laser allo stato solido, dunque fibra, diodi, alta e bassa brillanza è molto sensibile ai volumi, quindi servirà chiedersi cosa succederà, in questo senso, nel prossimo futuro».
Cristiano Porrati, Prima Power
«Il mercato italiano, per noi, è cresciuto complessivamente di oltre il 18% sul comparto degli impianti di lavorazione lamiera, più di quanto non sia cresciuto mediamente il Gruppo: se guardiamo i laser piani 2D, le macchine tridimensionali e le combinate, sono saliti anche di qualche punto in più, dunque il 2016 è stato un anno davvero importante, con l’inizio del 2017 che sta mantenendo il trend. In questo momento tutti quelli che puntano a investimenti per l’Industria 4.0 cercano di approfondire gli aspetti legati all’applicabilità e alla convenienza, per comprendere a fondo come concludere al meglio questo tipo di operazione finanziaria».
Stefano Bordoni, TTM Laser
«Abbiamo visto che nello scorso anno c’è stato un incremento dell’ordinato, in Europa, del 17% e anche in Italia abbiamo riscontrato un aumento delle vendite e delle richieste sia da nuovi clienti che da aziende consolidate: queste ultime hanno accelerato le loro decisioni in vista di questo iperammortamento, puntando molto sulla tecnologia in fibra, più semplice da adottare e da mantenere oltre che più economica. Ultimamente abbiamo avuto molte richieste per quanto riguarda il taglio piano di grosso formato, anche se c’è stato un notevole aumento del tubo senza tralasciare le combinate, quindi saldatura e taglio sulla stessa macchina».
Stefano Draghi, Coherent-Rofin
«Durante l’annata del 2016 abbiamo ottenuto buoni risultati, migliori dell’anno precedente, non soltanto nel campo delle alte potenze per il laser a fibra ma anche per quello delle microapplicazioni. Riteniamo che quest’anno in corso possa essere anche migliore nell’ambito di nostra competenza, ovvero in Italia e nei Paesi che s’affacciano sul Mediterraneo, Turchia compresa. L’acquisizione del gruppo Rofin da parte di Coherent ha coinciso con il trasferimento di tutta l’attività sul laser a fibra da Santa Clara (California) ad Amburgo (Germania), ritenendo la Rofin Sinar Laser un’eccellenza da potenziare e sviluppare ulteriormente».
Federico Campana, CY Laser
«Dopo dodici anni in cui abbiamo continuato a proporre il laser fibra vediamo che finalmente se ne parla seriamente, anzi scatenando l’entusiasmo del mercato dopo periodi di stagnazione del comparto, grazie al fatto che vengono ridotti i costi d’esercizio. Siamo produttori d’impianti speciali, studiati su specifiche esigenze del singolo cliente quindi, per noi, la crisi non è mai esistita, con un tasso di crescita aziendale che mediamente si attesta attorno al 30% annuo. L’interesse acceso dagli incentivi statali è stato sicuramente un fattore importante di sviluppo del comparto ma, secondo me, a medio e lungo termine sarà dannoso per il mercato interno».
Ivo Pasqualini, LVD Italia
«Devo dire anzitutto che il mondo della lamiera sta restituendo segnali positivi e questa situazione la vediamo e la riscontriamo un po’ tutti, soprattutto nel campo del laser, che diciamo rappresenta un po’ la “primadonna”. Il mercato italiano per noi è considerato tra i più importanti, con un trend di crescita positivo che si registra nell’ordine delle due cifre, e credo che il laser sia proprio il punto di riferimento per noi in questo 2017… paradossalmente con un problema di eccessivo incremento, se pensiamo al recupero e ricollocamento dei vecchi impianti a CO2».
Giovanni Zacco, BLM Group
«Utilizziamo il laser principalmente per la lavorazione del tubo che rimane il nostro obiettivo principale, anche se abbiamo delle macchine combinate. Registriamo ancora un altro anno di crescita a due cifre, in linea con gli ultimi anni, anche grazie alle misure economiche e agli incentivi predisposti dallo Stato. In questo senso avremo modo di vedere in anticipo cosa succederà osservando la Francia, dove misure del genere erano già state adottate e stanno terminando: va anche detto, però, che la crescita nel nostro Paese non è da attribuirsi solo agli incentivi fiscali. Anche l’Europa e gli Stati Uniti rimangono aree economiche importanti per noi, con un buon tasso d’ordini che provengono un po’ da tutte le regioni».
Alberto Vismara, Trumpf
«Sicuramente stiamo assistendo a una crescita a livello mondiale e, anche per il nostro Paese, i risultati sono davvero interessanti con tassi a due cifre; il mercato più importante rimane quello dei laser 2D con tassi di sviluppo decisamente alti, soprattutto nelle macchine con sorgenti allo stato solido. Si sta iniziando a parlare, sempre più, di saldatura laser e questo è un bene, perché l’Italia si sta avvicinando a Paesi come la Germania dove oggi è decisamente più diffusa: stiamo cominciando a proporre anche in Italia l’Additive Manufacturing, che sta ricevendo molto interesse da parte della clientela».
Ivan Verpilio, Yamazaki Mazak Italia
«Confermo i dati di mercato del 2016, con una tendenza positiva che dura ormai da qualche anno e con buone prospettive per il futuro: vorrei aggiungere che oggi sono presenti nuovi player, nel mondo delle macchine a taglio laser, che prima non esistevano. Gli investimenti dei clienti vanno in tre diverse direzioni: nuovi clienti con nuovi prodotti, clienti esistenti che acquistano una nuova macchina per incrementare la produzione investendo in nuovi impianti, e clienti che trasferiscono internamente la lavorazione del taglio laser che precedentemente svolgevano tramite partner esterni».
Stefano Cattaneo, IPG Photonics
«Il 2016 per noi è stato un ottimo anno, con una crescita in Italia del 22% circa, arrivando a consegnare quasi 500 sorgenti laser ad alta potenza. Siamo quindi decisamente soddisfatti considerando che una decina d’anni fa di laser l’anno ne consegnavamo dieci al massimo. Sicuramente gli incentivi statali aiutano e, in questo senso, vediamo un 2017 molto positivo. Guardando i diversi mercati in cui operiamo, quello del taglio laser è di gran lunga il più importante. Una nota interessante: negli ultimi anni hanno avuto una crescita maggiore i piccoli produttori di macchine rispetto ai grandi Gruppi industriali».
Pierluigi Vaghini, Amada Italia
«Arriviamo da un 2016 molto interessante e ci aspettiamo un 2017 sulle stesse orme anche grazie all’iperammortamento, benché a oggi ci siano ancora dei punti oscuri. A livello tecnologico, sicuramente il laser è la punta di diamante della tecnologia odierna: riteniamo sia necessario fornire il maggiore aiuto possibile alle aziende che si trovano ad affrontare una scelta legata all’acquisto di un nuovo impianto. Amada propone una soluzione globale legata alla gestione completa del processo. Pensiamo che questa possa essere una visione moderna e performante».
Pierandrea Bello, Salvagnini
«Secondo me c’è da fare una netta divisione tra il mercato italiano e quello globale: se osserviamo i dati generali forniti da Ucimu in merito alle importazioni/esportazioni questi non sembrano così rosei, con un 2016 in leggero calo nell’export (anche se il mondo del laser, storicamente, è sempre cresciuto) e in decisa flessione nell’import, pari a circa il 10%. Dal nostro punto di vista, considerando che ci occupiamo di laser per il taglio bidimensionale, possiamo dire che l’Europa è abbastanza stabile, con l’Italia che fa discorso a sé grazie agli incentivi statali che, certamente, hanno influenzato l’andamento del business. Vediamo anche il continente asiatico in generale flessione, nel senso che osservando una Cina che dichiara di crescere del 2% annuo dopo tassi che avevano raggiunto anche la doppia cifra, c’è da vedere cosa accadrà».
Il laser ha rappresentato una delle tecnologie di lavorazione caratteristiche di un’evoluzione, nel mondo delle lavorazioni meccaniche degli ultimi due decenni, che non s’è fermata. Quali sono le principali tendenze tecnologiche in atto nel mondo del laser?
Pierandrea Bello, Salvagnini
«Ci sono due aspetti da considerare, il primo dei quali è relativo alla tecnologia laser in sé, che comunque si sta muovendo bene in special modo sul taglio in fibra, dove si osserva un generale aumento della potenza, quindi dei campi applicativi. Tuttavia, al fianco di questa evoluzione, ciò che vediamo è l’attenzione sempre crescente da parte dei clienti circa il modo di utilizzare al meglio le macchine laser e come integrarle all’interno dei propri flussi produttivi. Uno dei motivi per i quali ci si sposta verso l’aumento di potenza è che si vuole incrementare la produttività, tuttavia ci sono dei benefici che possono essere molto superiori, ovvero i benefici derivanti dall’integrazione dei sistemi laser specie con i sistemi gestionali e di programmazione a monte e con la piegatura a valle, in un’ottica anche rivolta all’Industria 4.0».
Pierluigi Vaghini, Amada Italia
«L’obiettivo che vogliamo perseguire è quello di dare una soluzione in fibra a 360 gradi, andando a coprire la fascia di spessori e di materiali che i clienti ci chiedono. È fondamentale, oggi, fare un’analisi per capire se sia necessario introdurre impianti d’alta potenza all’interno di una realtà aziendale consolidata. Spesso il cliente vuole sostituire un CO2 e ha due necessità: la risoluzione di un problema produttivo e, in parallelo, aumentare le performance della sua azienda. Se non c’è un’analisi preventiva si corre il rischio di creare uno sbilanciamento produttivo all’interno dell’azienda. Se aumentano le performance di taglio in modo esponenziale, si generano colli di bottiglia a valle in fase di piegatura e a monte in fase di nesting».
Stefano Cattaneo, IPG Photonics
«Il nostro punto di vista è quello dei produttori di sorgenti e non di macchine, così che quello che vediamo noi è un laser in evoluzione verso una funzione di commodity all’interno della macchina. La parte nobile dell’impianto, infatti, un tempo era il laser (divenuto uguale per tutti) mentre oggi è la macchina stessa, che può davvero fare la differenza: ciò su cui stiamo lavorando è lo sviluppo di un motore, da dare agli integratori, che sia sempre più affidabile, performante, economico e facile da utilizzare. Vedo la richiesta di alta potenza sempre più insistente, ma un po’ diversa da quella che c’era un tempo sul CO2. Con il fibra, tagliare con 10, 12 o anche 15 kW non è così impegnativo, sempre che le teste e le ottiche siano in grado di gestire questi livelli di potenza».
Ivan Verpilio, Yamazaki Mazak Italia
«La tendenza del mercato è quella oggi di andare sempre più verso una tecnologia in fibra anche se, in alcuni settori industriali, la qualità del taglio non eguaglia ancora quella del CO2. Probabilmente, il giusto compromesso è quello di trovare una macchina che assicuri un risparmio energetico e che sia produttiva, in modo tale da garantire un bilanciamento tra la potenza e la qualità del taglio. Diventa, in questo caso, fondamentale il servizio offerto al cliente, al quale si devono illustrare tutti gli aspetti legati a questo tipo di tecnologia. Inoltre, notiamo la necessità da parte dei nostri clienti di affiancare la macchina a un’automazione per una lavorazione h24 senza presidio».
Alberto Vismara, Trumpf
«Da una parte, il laser CO2 è cresciuto con la potenza in diversi anni, mentre il laser allo stato solido questa crescita l’ha compiuta in pochissimo tempo, attestandosi ormai su valori anche di 10/12 kW per il taglio. Le macchine, dunque, devono cambiare per seguire questa tendenza attraverso l’aumento delle prestazioni, della qualità e dei consumi, al fine di rendere più produttivo il processo. Evoluzioni, nei prossimi anni, ce ne saranno parecchie e probabilmente arriverà anche il diodo diretto e, qui, vedremo quali potenze sarà in grado di fornire: l’Additive Manufacturing, poi, è già di per sé un’evoluzione arrivata anche in relazione alla tecnologia laser. Laser che oggi, allo stato solido, viene considerato un po’ come una macchina a elevate prestazioni, ma nello stesso tempo è anche una tecnologia delicata così che, dove la qualità dei materiali non è sempre eccelsa, il CO2 può fornire risposte migliori in termini di qualità di taglio. Infine, costruire macchine sempre più modulari, attente alla sicurezza di processo nel tempo, è una delle sfide del futuro».
Giovanni Zacco, BLM Group
«Oggi essere integratori significa qualcosa in più di soggetti che comprano il laser e lo installano sulle macchine: è richiesta una profonda conoscenza della tecnologia laser anche a noi, che siamo dunque coinvolti in tutte le novità che caratterizzano questa fase, estremamente effervescente. In aggiunta a quanto affermato dai colleghi, posso dire che il tema dell’alta potenza è per noi strettamente legato alla sensorizzazione delle sorgenti, con la capacità di controllare adeguatamente le operazioni di taglio e fornire informazioni in un’ottica rivolta al concetto d’Industria 4.0».
Ivo Pasqualini, LVD Italia
«Come costruttori siamo impegnati nel completamento della gamma dei nostri formati, seguendo quella che è una trasformazione dal laser CO2 a quello in fibra, nostro primo obiettivo per i prossimi mesi. Dall’altra parte, queste potenze che aumentano rapidamente, in maniera esponenziale, devono poi essere trasferite sul campo come parametri ottimali di taglio, dunque i nostri tecnici sono concentrati su questo punto. Infine, stiamo operando per creare un comune denominatore tra queste tecnologie sempre più complesse, ma integrate tra loro, dando vita a un qualcosa che possa essere semplice per le aziende da utilizzare, accompagnato da un’adeguata formazione agli operatori in modo da sfruttare al meglio le potenzialità delle nuove macchine».
Federico Campana, CY Laser
«A questo tavolo siamo quasi tutti integratori che montano, tra l’altro, lo stesso tipo di sorgenti: questo può portare a pensare che comprare una sorgente e metterla su un sistema 2D sia semplice e di facile realizzazione, ma non è proprio così. Bisogna stare molto attenti a non generalizzare e fare formazione adeguata ai clienti, al fine di creare quella cultura necessaria ad affrontare nuovi processi di lavoro, ottimizzarli, assicurando anche l’opportunità di automatizzare il tutto in maniera efficiente. Vero è che la ricerca della qualità costruttiva è importantissima e anche un punto fondamentale per dare poi un prodotto commercialmente valido. È altresì vero che i nostri primi clienti sono coloro che ci pongono richieste customizzate a volte molto complesse, dandoci modo di scoprire nuovi spunti e nuove soluzioni».
Stefano Draghi, Coherent-Rofin
«Gli sforzi di Rofin in futuro saranno diretti principalmente verso lo stato solido. Per quanto concerne il nostro laser in fibra, la strategia di sviluppo è rivolta verso le alte potenze utilizzando il minore numero di moduli possibile. Al momento il modulo unitario è da 2.5 kW, ma non è detto che ci si fermi qui. Minimizzare il numero di moduli significa, tra gli altri benefici, conferire al laser una maggiore affidabilità. Abbiamo poi in essere un’evoluzione futura del diodo di alta potenza, presenza ormai importante nella saldatura, brasatura, trattamento termico. Per quanto riguarda il CO2, il nostro è un prodotto maturo con un’affidabilità molto elevata comprovata da oltre due decenni di utilizzo dalla sua introduzione sul mercato».
Stefano Bordoni, TTM Laser
«La nostra capacità di personalizzare gli impianti incontra grande interesse da parte del mercato. La nostra ingegnerizzazione spinge molto sulla personalizzazione della macchina e, questo, ci porta a utilizzare svariati produttori di sorgenti, sia CO2 che fibra. In questi ultimi periodi stiamo spingendo molto sulle teste 3D sia per il taglio piano che per quello del tubo, con la sorgente che non diventa solo un dispositivo aggiuntivo ma ricopre un ruolo fondamentale e dev’essere integrata in maniera attenta. Ciò ha portato all’utilizzo di sorgenti da 1 a 12 kW in fibra, anche se molti costruttori che ci richiedono la testa inclinata per pezzi a elevato spessore preferiscono rimanere sulla sorgente CO2 proprio per il migliore livello di finitura assicurato. Stiamo spingendo molto poi sulla saldatura laser, con una potenza di sorgente fibra che ci aiuta anche nell’utilizzo di diversi materiali di vario spessore».
Cristiano Porrati, Prima Power
«Il mercato post-crisi è cambiato moltissimo, non solo perché la fibra ha soppiantato il CO2 ma anche per molti altri aspetti: ricordo, all’inizio degli anni 2000, quando le sorgenti CO2 di potenze superiori soppiantavano quelle di potenze inferiori, perché il mercato era molto ricettivo in tal senso e non stava ad analizzare approfonditamente i costi e i vantaggi. Oggi c’è una maggiore attenzione verso i costi, quindi nonostante molti costruttori spingano i clienti verso potenze superiori (che sicuramente offrono vantaggi prestazionali), le aziende operano anche attente valutazioni economiche. Parallelamente, notiamo una sempre maggiore richiesta d’impianti completamente integrati a un’automazione molto complessa, in grado di partire da operazioni semplici quali il carico/scarico arrivando poi a gestire magazzini integrati, pallettizzatori e quant’altro possa aumentare la produttività».
Maurizio Gattiglio, Convergent Photonics
«Noi identifichiamo principalmente due tendenze tecnologiche, che sono fra l’altro un po’ in contrapposizione tra loro: la prima è quella del laser allo stato solido che diventa una commodity, ossia un componente ormai comune, ed è vero che i costruttori in grado di produrre questo tipo di soluzione sono molto pochi e verticalizzati, nonostante la tecnologia in fibra sia abbastanza matura. La seconda, invece, vede sempre più l’esigenza di personalizzazione e specializzazione delle macchine: abbiamo concluso recentemente un progetto, in collaborazione con Comau, molto innovativo, in cui abbiamo realizzato una sorgente a laser diodo e fibra assieme destinata al mondo dell’automobile per brasare, saldare e tagliare, dunque un prodotto molto personalizzato sulle esigenze della singola realtà industriale».
Giovanni Di Stefano, Comau
«Quello che percepiamo come grande trend è la ‘globalizzazione’ delle applicazioni, con il cliente che desidera essere seguito in tutto il mondo con gli stessi livelli qualitativi. Tutte le campagne d’innovazione, quindi, devono in qualche modo essere globali ma, al tempo stesso, customizzate in base al cliente e al mercato. Tra i punti nevralgici che abbiamo individuato, dunque, ci sono la flessibilità, la scalabilità degli investimenti e la modularità dei progetti: questo ha portato alla realizzazione della nostra sorgente laser ibrida, dove la parte più innovativa del progetto risiede proprio nel fatto che le sorgenti in fibra e in diodo hanno sostanzialmente gli stessi pezzi di ricambio».
Quali sono i campi applicativi più sensibili alla tecnologia laser e quali comparti vedete, in prospettiva, da sviluppare?
Ivo Pasqualini, LVD Italia
«Noi vediamo il laser applicato alle macchine per il taglio della lamiera e a quelle per il tubo, i due settori nei quali operiamo, con tutta l’automazione spinta necessaria ai miglioramenti di processo. Quello che il cliente vuole, oggi, è una soluzione affidabile e performante: in questa direzione ci muoviamo con tutta l’innovazione necessaria».
Giovanni Zacco, BLM Group
«Il taglio laser per il tubo, ormai, viene utilizzato nei settori più disparati, applicato e conosciuto ovunque, con una tecnologia ben nota che si porta dietro importanti opportunità per gli utilizzatori. Un settore da evidenziare è quello delle costruzioni, secondo me in grado di trarre enormi benefici se riuscirà a comprendere a fondo i vantaggi nell’uso di una tale tecnologia. Un campo poi sicuramente interessante è quello delle macchine combinate di taglio laser per lamiere e tubo, sulle quali stiamo riuscendo ad avere buoni risultati perché in grado di offrire grande flessibilità ai clienti attraverso un sistema completamente automatico in entrambe le lavorazioni, con tutte le caratteristiche per essere competitivo nei due ambiti».
Alberto Vismara, Trumpf
«Per noi i settori più sensibili a questa tecnologia sono la saldatura laser e l’Additive Manufacturing e i comparti da sviluppare sono quelli del laser network, con la possibilità di utilizzare la sorgente su diverse macchine per sfruttare appieno la potenza su più utenze. È anche vero che, pur essendo tutti noi presenti sullo stesso mercato, abbiamo una popolazione di clientela differente, composta da chi cerca potenze medie e chi potenze alte. La maggior parte dei nostri clienti, poi, è in genere contoterzista, dunque orientata su potenze medio-alte che normalmente garantiscono prestazioni e flessibilità nello stesso tempo».
Ivan Verpilio, Yamazaki Mazak Italia
«Mazak sta investendo molto nel nuovo comparto industriale dell’Additive Manufacturing: e ne è prova il fatto che, all’ultimo Jimtof in Giappone, 4 delle 18 macchine esposte erano dotate di tecnologia ibrida, un mix tra asportazione e apporto di materiale. È dunque nata tutta una serie di nuove macchine che sfruttano questa tecnologia, con una logica che è quella di produrre un particolare sfruttando il multitasking per riuscire a ottenere il pezzo finito in un unico processo, evitando lavorazioni di ripresa. Per questo la nostra azienda ha creato una Divisione specifica, attiva da circa un anno a livello mondiale, che opera in questa direzione esportando le esperienze acquisite in un Paese in altre nazioni».
Stefano Cattaneo, IPG Photonics
«Sul taglio laser noi seguiamo gli input che ci arrivano dai clienti, gli integratori e i costruttori di macchine, che oggi ci chiedono potenze da 8, 10, 12 o addirittura 15 kW. Questo vanifica quasi completamente gli sforzi dei nuovi produttori di sorgenti in fibra, sia asiatici che non, in quanto oggi limitate a basse potenze (2 – 4 kW) con performance ancora tutte da verificare. Come IPG operiamo principalmente sullo sviluppo del mercato della saldatura laser; in particolare in IPG Italia abbiamo sviluppato un nuovo sistema di saldatura laser per tubi e profili che, rispetto agli attuali sistemi a CO2, riduce di un fattore 4 i costi orari di esercizio. Infine è importante menzionare anche le nuove sorgenti laser in fibra multifocali, nate per migliorare le applicazioni di brasatura in campo automotive ma subito applicate in numerosi altri settori con promettenti risultati».
Pierluigi Vaghini, Amada Italia
«I due settori che guardiamo con maggiore attenzione sono sicuramente il taglio della lamiera piana e la saldatura con sorgenti in fibra. Riteniamo sia indispensabile evidenziare la valutazione azienda per azienda dell’effettiva necessità di impiegare sorgenti ad alte potenze. L’analisi effettiva del rapporto costi/benefici sul lotto da produrre è la chiave di lettura più corretta per determinare il “taglio” tecnologico che l’impianto proposto deve avere. La comprensione della reale esigenza del cliente ci permette di proporre soluzioni che consentono l’innalzamento delle performance delle aziende che lo scelgono».
Pierandrea Bello, Salvagnini
«Nel nostro caso i contoterzisti rappresentano circa il 40% del numero totale di laser venduti per la restante parte rivolto alla grande industria, che vediamo richiedere oggi sempre più il laser per un discorso di flessibilità. Ci sono settori adesso in forte crescita che hanno utilizzato per anni la punzonatura ma che, ora, si stanno un po’ spostando su queste nuove tecnologie così che, dal punto di vista delle potenze, non chiedono valori così elevati come, per esempio, quelli voluti dai terzisti. Sul discorso del costo/pezzo l’aumento di potenza, quindi di produttività del laser, certamente aiuta, ma questo rapporto va guardato su tutta la fase produttiva, così che l’aumento dei kW non interviene necessariamente sull’intero processo. Oltretutto, al superamento di certi valori di potenza l’incremento del costo non è più solo relativo alla sorgente ma a tutto quello che ci sta dietro, dunque da valutare con attenzione».
Giovanni Di Stefano, Comau
«Gli ambiti di utilizzo del laser sono tutti legati al settore dell’automazione industriale. Si tratta di una tecnologia piuttosto costosa, che arriva a richiedere un investimento anche di 15 volte superiore a quello necessario per altri sistemi di giunzione. Ciò significa che è opportuno applicare questa tecnologia laddove c’è un reale ritorno economico. Il laser è quindi particolarmente adatto al settore ferroviario e aerospaziale, oppure di mass production come quello dell’automotive che, per noi, rimane sicuramente il comparto più importante. È interessante osservare come acciaio e alluminio siano i materiali che il cliente utilizza in predominanza insieme alla fibra di carbonio – ancora un po’ in fase sperimentale – e alla plastica, che sta acquisendo sempre più importanza: sarà questa, per noi, la sfida più importante da vincere nei prossimi anni».
Maurizio Gattiglio, Convergent Photonics
«Parlando di prospettive future, per i “sorgentisti” vedo una differenza importante rispetto alla tecnologia a CO2 perché, con il gas, si limitavano a fornire al costruttore di macchine un laser da gestire in seguito per quanto riguarda tutti gli aspetti legati alla sua propagazione. Oggi, con lo stato solido, c’è il rischio che fornendo la testa, la fibra e la sorgente tutto ritorni nelle mani del “sorgentista” perdendo, da parte di chi costruisce le macchine, flessibilità e possibilità di agire tecnologicamente. Secondo me, inoltre, ciò che servirà veramente sarà riuscire a portare intelligenza all’interno dei processi, una cosa insita nella creatività italiana e che potrà fare la differenza sul mercato».
Cristiano Porrati, Prima Power
«Una domanda difficile a cui rispondere, visto che la tecnologia laser è ormai applicata in molteplici settori industriali e, proprio per questo, la sua importanza è stata definita come validante per l’Industria 4.0. Entrando nello specifico del nostro Gruppo, utilizziamo il laser nel taglio piano applicato a macchine 3D, o in combinazione con le punzonatrici. Per quanto concerne l’argomento dei settori, invece, siamo certamente influenzati dal resto delle macchine che offriamo, dunque vediamo un impiego importante nel comparto degli ascensori, degli arredi metallici, degli elettrodomestici, degli armadi elettrici, dell’automotive, del riscaldamento e dell’illuminazione. Anche noi stiamo approcciando il discorso dell’Additive Manufacturing come aspetto innovativo, dove il laser trova la sua naturale collocazione».
Stefano Bordoni, TTM Laser
«Se fino a un paio d’anni fa gli unici che richiedevano i tagli piani di grandi dimensioni con testa bevel per fare i cianfrini erano i costruttori di macchine, oggigiorno invece anche le carpenterie medio-piccole, che già conoscono la tecnologia laser e la usano, ci richiedono tavole un po’ più grandi e con teste 3D, per potersi smarcare dalla concorrenza. Per quanto riguarda l’applicazione del taglio laser per il tubo, sicuramente lo strutturale è il comparto che cerchiamo di aggredire maggiormente anche se, sfortunatamente, la consapevolezza dei vantaggi nell’utilizzo della tecnologia laser è più conosciuta nel Nord Europa che in Italia. Operiamo infine anche nel settore della saldatura con importanti commesse nel settore ferroviario oltre all’Additive Manufacturing, con referenze importanti soprattutto in ambito dei settori della ricerca».
Stefano Draghi, Coherent-Rofin
«Rofin è concentrata sullo sviluppo dei laser fibra a moduli singoli d’elevata potenza con un particolare focus sulla saldatura, che è un campo in notevole crescita e con moltissime potenzialità. Per quello che riguarda applicazioni ancora sulla cresta dell’onda, la saldatura in linea dei tubi, i componenti powertrain, utensili di vario di tipo occupano certamente posti di rilievo. Coherent-Rofin ha inoltre sviluppato anche laser a fibra con impulsi ai nsec fino a 1 kW di potenza».
Federico Campana, CY Laser
«Il nostro core business, a tutt’oggi, è il laser 2D, quindi la nostra visione è sempre stata quella di dare questa tecnologia a tutti i costruttori di macchine. Grazie ai costi d’esercizio molto bassi, che consentono il calcolo del ritorno d’investimento in modo molto accurato, diamo l’opportunità ai nostri clienti di valutarci su dati ben precisi e, in questo senso, è importantissimo fornire una macchina semplice da usare, oltre che un post vendita molto efficiente. In merito alla macchina, il know how è ormai consolidato e riusciamo a consegnare alle aziende impianti dai costi operativi molto bassi. Inoltre, l’esperienza che abbiamo acquisito in questi dieci anni ci ha permesso di costruire teste e ottiche: stiamo guardando anche al futuro con l’Additive Manufacturing, che sta assumendo una certa importanza anche se non è facile muoversi in questo campo».
La sorgente rappresenta uno degli elementi chiave della tecnologia laser. Ci potete raccontare, dal vostro punto di vista, quali sono rispettivamente gli input tecnologici dei produttori di sorgenti e le richieste dei costruttori di macchine laser?
Federico Campana, CY Laser
«A noi piace guardare le novità di mercato, cercando di capire le varie proposte dei costruttori per muoverci adeguatamente: secondo me, la parte fondamentale per noi è quella di cercare di sfruttare ciò che c’è a monte, come le lunghezze d’onda che ci vengono fornite, così da potere giocare con queste grazie a ottiche speciali, movimentazioni e dispositivi elettronici, al fine di migliorare la qualità del fascio».
Stefano Draghi, Coherent-Rofin
«Il nostro obiettivo è assicurare affidabilità e flessibilità alle soluzioni laser che proponiamo al mercato, così da aiutare l’utilizzatore a raggiungere il risultato che persegue. Altra cosa importante da sempre, per noi, è l’assistenza tecnica post vendita. In questo ambito dedichiamo risorse per la formazione del personale nonché per quanto riguarda la disponibilità in loco delle parti di ricambio a magazzino».
Stefano Bordoni, TTM Laser
«Visti i numeri di produzione odierne e la variabilità di richieste che riceviamo non riteniamo per ora conveniente sviluppare la nostra sorgente e utilizziamo prodotti diversi. Focalizziamo invece l’attenzione proprio sul servizio di assistenza e di ricambistica riferite al risonatore, oltre che sulla consulenza per la ricerca della soluzione giusta e affidabile in relazione alle esigenze del cliente».
Cristiano Porrati, Prima Power
«Il Gruppo Prima Industrie produce impianti e anche sorgenti utilizzate sulle nostre macchine: in questo momento, per alcune potenze ci avvaliamo ancora con soddisfazione di IPG alla quale chiediamo affidabilità, semplicità d’utilizzo e costi d’esercizio contenuti, che è poi quello che chiede a noi il mercato odierno».
Maurizio Gattiglio, Convergent Photonics
«Qui, nell’ambito dei “sorgentisti”, noi siamo piccoli, ma da dieci anni sviluppiamo questa tecnologia investendo svariate decine di milioni di euro, arrivando a fornire laser affidabili, semplici da usare e a costi competitivi. Pur non potendo ancora concorrere in termini di volumi con i grandi costruttori, ci rivolgiamo al cliente attraverso una politica molto chiara di trasparenza, in un’ottica di prodotto/servizio. Cerchiamo di aiutare le aziende a gestire il post-vendita, perché riteniamo che sia un grosso vantaggio specialmente nell’ambito del laser piano, dove la sorgente tipicamente rappresenta una parte molto consistente del costo finale, sfiorando anche il 50%».
Giovanni Di Stefano, Comau
«Chiediamo a noi stessi e ai nostri fornitori ciò che in sostanza i clienti chiedono a noi, ossia l’affidabilità della tecnologia laser che, soprattutto nel campo automobilistico, si utilizza per alte cadenze e, dunque, non deve fare perdere minuti preziosi alla catena di produzione. Abbiamo quindi target molto precisi in termini di MTBF e MTTR, che dovrebbero essere rispettivamente di 5 anni e di 30 minuti. Una delle principali necessità dei clienti, e delle grandi realtà industriali in generale, è la riduzione delle spese per il capitale, poiché i costi operativi del laser sono già più bassi di tutte le altre applicazioni tecnologiche: serve dunque essere più aggressivi, in quanto i clienti hanno bisogno di fare approvare i propri progetti».
Pierandrea Bello, Salvagnini
«L’affidabilità è oggi il valore più riconosciuto sul mercato e il mondo della tecnologia laser non fa eccezione, visto anche l’alto livello di competitività oggi in essere: infatti, vendere un impianto in Malesia o in Indonesia è piuttosto differente dal venderlo in Italia, per esempio, viste le enormi distanze che appunto richiedono una macchina che lavori sempre bene, in ogni condizione. Parimenti importanti sono il servizio di assistenza post vendita, al fine di garantire l’intervento di tecnici qualificati in caso di necessità, quello della ricambistica in tempi brevi, per evitare i fermi macchina, oltre che il livello tecnologico crescente, per stare al passo con le necessità del comparto industriale mondiale».
Pierluigi Vaghini, Amada Italia
«Amada progetta e produce sia gli impianti che le sorgenti a fibra “AJ” con potenze che vanno dai 2 ai 9 kW, garantendo flessibilità, affidabilità e alte prestazioni. L’obiettivo che ci siamo posti come costruttori di sorgenti è quello di eliminare i combiner o di utilizzarli nel modo più performante possibile. In questo modo siamo in grado di ottenere qualità del fascio laser molto elevate che ci consentono di non dovere per forza aumentare il wattaggio delle sorgenti per ottenere performance di alta qualità».
Stefano Cattaneo, IPG Photonics
«Come detto anche prima, noi pensiamo che la sorgente laser diventerà sempre più una commodity; rispetto al passato oggi ne esistono diverse sul mercato, anche se ancora limitate a medio-basse potenze. Quello che ci chiedono i produttori di sistemi sono soluzioni sempre più potenti, affidabili, compatte e di elevata efficienza. In particolare vorrei sottolineare che quest’ultima caratteristica rappresenta un parametro indicativo della bontà di una sorgente laser in fibra. Come già detto, i laser presenti oggi sul mercato sono tutti pressoché identici; la differenza fondamentale tra quanto è matura una tecnologia rispetto a un’altra la si evince dall’efficienza ottica ed elettrica. In generale, comunque, noi chiediamo ai nostri integratori di darci input sempre nuovi, perché la nostra mission è sviluppare tecnologia innovativa, pronta per il futuro».
Ivan Verpilio, Yamazaki Mazak Italia
«La presentazione da parte di Yamazaki Mazak dell’ultima tecnologia a diodo diretto sta a indicare proprio la volontà dell’azienda di sviluppare sempre nuove tecnologie al proprio interno. Da diverso tempo, infatti, progettiamo direttamente queste sorgenti proprio per puntare sull’affidabilità del prodotto. Ciò ha portato a notevoli miglioramenti dal punto di vista dell’efficienza energetica, maggiore del 15% rispetto alla sorgente in fibra. Un’altra grande differenza riguarda la velocità, che varia da un 15 a un 50% in più del diodo rispetto al fibra, a seconda dello spessore e dei materiali lavorati. Questo vantaggio si fa ancora più evidente per materiali altamente riflettenti come per esempio il rame e l’ottone».
Alberto Vismara, Trumpf
«L’obiettivo di noi costruttori di sorgenti è quello di fornire prodotti flessibili, affidabili, con un livello di assistenza tecnica adeguato e capillare nel mondo. Un altro aspetto su cui si deve ragionare è quello della compattezza delle sorgenti perché le macchine di oggi, rispetto alla tecnologia a CO2, vantano un minore ingombro e la tendenza sarà sempre più quella di ridurre lo spazio occupato, visti gli alti costi degli spazi negli stabilimenti. Per quanto concerne le macchine, invece, l’evoluzione delle stesse è molto rapida, dunque il costruttore deve ideare macchine che crescano ed evolvano nel tempo in modo che il cliente si trovi nel tempo una macchina sempre nuova e aggiornata allo stato dell’arte. Garantire ai propri clienti nel tempo la certezza che l’investimento iniziale rimanga performante e competitivo grazie a successive integrazioni, senza che sia necessario assolutamente l’acquisto di un nuovo impianto credo che sia una delle sfide più importanti nel prossimo futuro».
Giovanni Zacco, BLM Group
«Da integratori esigiamo affidabilità e assistenza puntando però sulla possibilità di differenziarci facendo valere le nostre competenze. Ai pochi e selezionati fornitori di teste e sorgenti chiediamo soluzioni sempre più in grado di dialogare con le nostre macchine, quindi di avere una sensoristica sempre più sofisticata, che ci consenta un controllo totale della sorgente laser al fine di elaborare i dati per ottimizzare il processo produttivo. Da questo punto di vista privilegiamo vere e proprie partnership con i costruttori, proprio per arrivare a scambiare conoscenze profonde sulla tecnologia allo stato solido, sfruttandone così al massimo le potenzialità».
Ivo Pasqualini, LVD Italia
«Gli input tecnologici che il mercato di oggi ci chiede sono l’affidabilità dell’intero sistema, quindi mettiamo a disposizione dei nostri clienti l’esperienza, la conoscenza del processo e della tecnologia. LVD sta oggi investendo molto nella formazione dei propri tecnici proprio per assecondare il profondo cambiamento nel mondo industriale, con livelli tecnologici degli impianti sempre crescenti, che hanno rivoluzionato il mondo del taglio».
L’argomento di attualità è oggi l’Industria 4.0. Che cosa stanno facendo le vostre aziende in quest’ambito e quali sono le opportunità per gli utilizzatori finali?
Cristiano Porrati, Prima Power
«Tutte le nostre macchine, non solo quelle laser, sono conformi alle direttive della legge sulle agevolazioni fiscali pensata per l’adeguamento a Industry 4.0, per quanto non sia chiarissima in tutti gli aspetti: a tal proposito, stiamo aiutando i nostri clienti a interpretare queste norme, non solo per quanto attiene l’impianto ma anche per quanto già esiste all’interno della loro azienda. Per ogni macchina abbiamo preparato fascicoli molto intuitivi, per fornire tutte le indicazioni del caso e siamo più che sicuri che tutti coloro che si occupano di finanziamenti faranno altrettanto per mostrare la convenienza. Quello che mi auguro è che le società italiane sappiano cogliere quest’occasione di vantaggio fiscale, per fare quel cambiamento che possa traghettarle nella nuova era industriale».
Maurizio Gattiglio, Convergent Photonics
«L’argomento mi vede particolarmente sensibile, perché ricopro anche la carica di Presidente di EFFRA, l’European Factories of the Future Research Association a Bruxelles ed è da diversi anni che lavoriamo su questo tema. Riconosco al Ministero il coraggio di avere fatto una cosa importante, perché l’Italia era davvero arretrata su questa tematica, con ripercussioni rilevanti sui posti di lavoro che verranno creati. Rimane tuttavia da potenziale il lato della ricerca e della creazione delle tecnologie e delle piattaforme, che forzatamente dovranno essere create in sinergia con gli altri Paesi europei e sono ancora irrisolte questioni come gli standard o la proprietà dei dati. È poi fondamentale, per la competitività delle soluzioni sviluppate, che queste siano aperte alla gestione dei big data, con connessioni sempre più estese nel pieno interesse del cliente: noi ci stiamo muovendo, in questo senso, con un team multinazionale che lavora per garantire questa futura apertura. La sorgente sviluppata con Comau è per esempio già fortemente inserita nell’Industria 4.0 con più di 50 sensori disponibili via Internet e in cloud, per manutenzione predittiva avanzata e monitoraggio continuo».
Giovanni Di Stefano, Comau
«Sicuramente la sensorizzazione e l’accesso alle informazioni da remoto sono i punti chiave dell’Industria 4.0 e dell’Internet of Things. A mio parere però abbiamo cominciato questa rivoluzione industriale senza capire bene cosa farne, nel senso che dovremmo prima cambiare il modo di pensare l’automazione. Si apre dunque il quesito che non riguarda tanto la generazione dei big data quanto quella dei big hypothesis, che poi vengono confermati dai primi: il contributo umano, dunque, non va a scemare ma deve aumentare».
Pierandrea Bello, Salvagnini
«Parliamo di un argomento abbastanza ampio, dove sicuramente c’è molta confusione, anche perché non si comprendono sempre fino in fondo i vantaggi dell’applicazione di questa nuova metodologia: serve, dunque, la capacità di spiegarli ai clienti, perché l’installazione di sensori va bene a patto che abbiano una logica all’interno di un processo produttivo. La cosa importante è che non ci si deve limitare solamente alle macchine, nel senso che il concetto d’intelligenza dev’essere anche portato fuori dagli impianti, a livello del processo stesso, con un continuo interscambio di informazioni tra le apparecchiature in fabbrica. Infine questa intelligenza, che voglio chiamare “di relazione”, va portata anche fuori dagli stabilimenti, diventando indispensabile per i controlli in remoto e per il service».
Pierluigi Vaghini, Amada Italia
«Sicuramente il vantaggio economico e fiscale per l’azienda che sposa questa nuova avventura è un fattore importante per lo sviluppo del concetto di Industria 4.0 e noi, da questo punto di vista, siamo pronti a supportare le aziende fornendo loro un servizio di consulenza e guida. Inoltre è importante anche l’aspetto legato al vero concetto di Industry 4.0, che noi vediamo come un’opportunità eccezionale per il mercato e per le aziende italiane. Quello che dobbiamo fare, dunque, è aiutare i nostri clienti a cogliere le opportunità legate a questa nuova era industriale attraverso la fornitura di soluzioni tecnologicamente avanzate, capaci di aumentare le performance delle aziende e la competitività sui mercati internazionali».
Stefano Cattaneo, IPG Photonics
«Dal nostro punto di vista, stiamo cercando di rendere la sorgente sempre più intelligente: per come nasce la fibra ha già un alto numero di sensori, ognuno dei quali è presente per tenere monitorato un processo e garantire che la lavorazione successiva avvenga in maniera perfetta. Serve programmare la macchina con tutta una serie d’informazioni indispensabili affinché possa controllare le varie fasi operative, in tempo reale, adattandosi alle diverse condizioni, compensando eventuali problemi, fino ad arrivare a segnalare in anticipo possibili guasti e prevenire costosi fermi di produzione».
Ivan Verpilio, Yamazaki Mazak Italia
«Sicuramente gli incentivi economici sono una grande opportunità per il nostro Paese anche se, come già detto dai colleghi, le normative non sono molto chiare: ci siamo accorti che la richiesta maggiore da parte degli utilizzatori è quella di avere la consulenza necessaria per arrivare alla certificazione dell’Industria 4.0. Mazak fornisce l’impianto e assicura la consulenza necessaria per fare sì che il cliente integri questo impianto nel ciclo produttivo. Abbiamo un nostro gestionale, installato nelle macchine, che può essere implementato e integrato all’interno del sistema di produzione del cliente. È indispensabile, infine, trovare protocolli di comunicazione standard tra la macchina e il sistema gestionale, argomento che attualmente non è specificato nella normativa».
Alberto Vismara, Trumpf
«Tutti noi stiamo costruendo impianti pronti a essere integrati in un sistema 4.0 e il tema riguarda proprio il salto di qualità che deve fare la nostra clientela grazie a questa agevolazione. Anche Trumpf ha il proprio sistema gestionale che si deve confrontare e integrare con quello già presente dai clienti: Trumpf ha creato una start-up in Germania, un paio d’anni fa, che si occupa proprio di fornire applicazioni e soluzioni per adattarsi a qualunque esigenza del cliente, fornendo un servizio a 360 gradi. È indispensabile, quindi, fare formazione e operarsi affinché la clientela non approfitti del mero vantaggio fiscale ma cerchi di innovare la gestione della propria azienda, digitalizzando i processi in modo che l’azienda stessa sia più competitiva tramite le soluzioni Trumpf in termini di software e macchine».
Giovanni Zacco, BLM Group
«Concordo con quanto detto dai colleghi, aggiungendo che fermarsi all’interpretazione della legge per com’è stata scritta rischia di fare perdere il nocciolo della questione. L’interconnessione va intesa come evoluzione complessiva del processo produttivo, spostando l’attenzione dalla singola lavorazione meccanica eseguita sul pezzo al processo stesso, ed è proprio questo il tema centrale che promuoviamo da tempo nei confronti del cliente, facendo dialogare fra loro i prodotti coinvolti in un processo produttivo. Non possiamo dimenticare che in Italia la maggioranza degli acquirenti ai quali vendiamo i nostri prodotti non è a livello di Industria 4.0 e alcuni di essi non hanno nemmeno un sistema informativo a cui collegarsi, dunque parlare di big data diventa molto difficile. Senza contare che andare a parlare di questi big data ad aziende di grandi dimensioni è impresa ancora più ardua, perché difficilmente accettano di portare le informazioni all’esterno degli stabilimenti produttivi, considerando la riluttanza già esistente in termini di teleassistenza».
Ivo Pasqualini, LVD Italia
«Industria 4.0 è un’ottima opportunità per il nostro cliente finale: si parla di digitalizzazione, d’interconnessione e di soluzioni globali ma poi si scopre che, entrando in un’azienda, si parlano 50 lingue diverse: come fa, dunque, un cliente a trarne un reale beneficio? Seguendo la strada pensata da LVD, che vuole essere presente in ciascun settore produttivo della lamiera, dal taglio alla piega, dal tubo alla punzonatura fino al software, avendo tutto il ciclo di lavoro in mano, con la possibilità di potere fare comunicare gli impianti tra loro».
Federico Campana, CY Laser
«Per Industry 4.0 s’intende la generazione di dati provenienti da materia prima, ciclo, prodotto finito, tempo d’esecuzione e costi di produzione, che dovrebbe servire all’imprenditore per comprendere la propria fase produttiva, analizzare i costi e i tempi, valutando la propria competitività sul mercato. I vantaggi della legge sull’Industria 4.0, quindi, dovrebbero essere un aiuto allo sviluppo di un nuovo modo di produrre e non solo per avere benefici fiscali: noi mettiamo a disposizione della clientela, dunque, tutti gli strumenti necessari per affrontare questa nuova rivoluzione industriale, spiegando nel dettaglio tutte le potenzialità che derivano dall’utilizzo degli ultimi strumenti tecnologici presenti sul mercato».
Stefano Draghi, Coherent-Rofin
«In qualità di costruttori di laser ci preoccupiamo di fornire sorgenti laser più intelligenti possibile, che possano scambiare con le macchine informazioni che testimonino lo stato del laser, il suo corretto funzionamento e, in modo predittivo laddove la sensoristica di cui è dotato lo consente, eventuali rischi incipienti o problematiche che, se anticipate, possono rendere la catena produttiva molto più efficiente».
Stefano Bordoni, TTM Laser
«Anche TTM sta lavorando in ottica 4.0, avendo fornito impianti in Germania e Francia negli ultimi anni: il problema più grande, come affermato da alcuni colleghi, è che la maggior parte delle carpenterie italiane è a conduzione familiare e non è affatto semplice fare comprendere le grandi potenzialità di questa quarta rivoluzione industriale. Oggi, a mio avviso, la cosa più difficile da gestire è la condivisione dei dati, perché rimane una grande riluttanza da parte soprattutto delle piccole e medie imprese ad aprire le porte tramite il costruttore dell’impianto alle esperienze anche dei loro concorrenti, riferite per esempio alla preventivazione o ad altri sistemi di processo».
Condividi l'articolo
Scegli su quale Social Network vuoi condividere