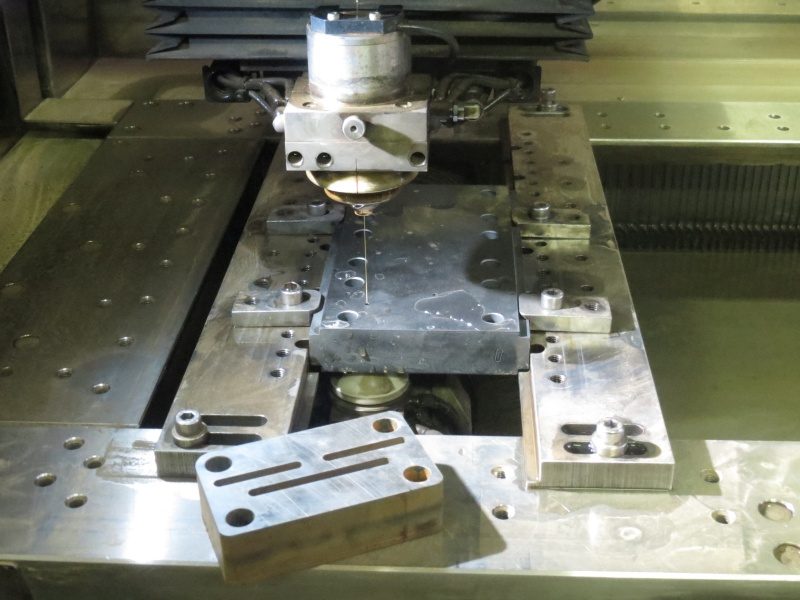
Mb ha scelto l’elettroerosione a filo di Fanuc con cui riesce ad eseguire lavorazioni anche in modalità non presidiata per la massima efficienza e flessibilità
Per approfondire come un contoterzista riesce ad abbinare qualità ed efficienza nelle lavorazioni tramite elettroerosione a filo, incontriamo Alessandro Vergnani, Responsabile Attrezzeria della MB, nella sede dell’azienda a Crevalcore (BO), in modo da conoscere meglio una realtà capace di adeguarsi alle esigenze di un mercato sempre mutevole. Lo facciamo in un momento congiunturale abbastanza favorevole, anche perché la realtà bolognese ha sofferto la crisi del 2008 in modo meno pesante rispetto ad altre industrie nel comparto della meccanica grazie alla diversificazione e alla clientela trasversale sul territorio italiano. A dare un’ulteriore spinta ai risultati dello scorso anno anche le facilitazioni fiscali, i cui benefici si stanno ancora sentendo: quest’anno infatti l’azienda (una sessantina di persone, più una ventina di collaboratori) vede una crescita ancora superiore al 2017.
Da stampista a terzista
Fondata nel 1970 come azienda individuale allo scopo di progettare, realizzare stampi e produrre manufatti in metallo per conto terzi, la MB ha assunto negli anni 90 la forma giuridica di società di capitali distribuiti in forma paritaria tra i tre soci Bottazzi, Ferriani e Veronesi. L’esperienza maturata all’inizio nella costruzione di stampi, utilizzati principalmente per la costruzione di mobili e arredi d’ufficio e componentistica per l’arredamento industriale, ha portato l’officina meccanica a volere completare il proprio servizio al cliente iniziando a stampare parti in lamiera, fino ad arrivare negli anni 2000 al servizio completo (divenuto gran parte del business) di realizzazione stampo e utilizzo dello stesso per la produzione dei lotti richiesti dal cliente. Ecco quindi la trasformazione in contoterzista, lavorando la lamiera in coil da 2 a 5 mm in acciaio inox e zincato per costruzione, quindi con resistenze importanti. Per consentire il passaggio alla situazione attuale è stata determinante l’attività di ricerca e sviluppo, che ha via via dotato l’azienda di strumenti in grado di portarla oltre la semplice produttività delle presse e che potesse facilitare il cliente nel posizionare le proprie campionature. MB si è quindi dotata a più riprese d’impianti laser, piegatrici e impianti di saldatura robotizzati, rivolgendosi a fornitori selezionati per trattamenti termici e superficiali. «Il nostro core business è sostanzialmente rappresentato da applicazioni legate per il 90-95% a tre settori: elettrodomestici, automotive, scaffalature e magazzini automatici», ci confida Vergnani, che racconta anche il modo in cui l’azienda entra in contatto con i clienti.
Può capitare che qualcuno arrivi da noi già con un’idea precisa che vuole sviluppare, oppure che porti un particolare campione di cui vuole creare diverse copie, o anche industrializzare un processo che prima era manuale o meno efficiente rispetto alle prospettive che s’immagina, o ancora con un determinato disegno da produrre. Per lo più si fidelizza la partnership creando un percorso insieme, che va dall’idea progettuale alla sua realizzazione e industrializzazione. Di solito comunque i clienti ci approcciano avendo ben chiaro il risultato che vogliono raggiungere, e confrontando valutazioni comuni decidiamo insieme qual è la strada migliore per affrontare il progetto». Il tutto richiede molta flessibilità nella programmazione degli acquisti, oltre all’amministrazione dei servizi d’approvvigionamento che unisca buon senso e sano realismo. «Si può anche intraprendere la strada della prototipazione rapida non da stampa 3D ma con campioni prodotti con l’impianto laser con cui trovare lo sviluppo ideale, per poi costruire l’eventuale stampo o l’attrezzatura per la realizzazione del pezzo finale».
Elettroerosione a filo, efficienza in non presidiato
Ponendosi come fornitore unico per i clienti dallo stampo al lotto produttivo, MB si è dotata di tutte le tecnologie produttive necessarie, tra le quali non poteva mancare ovviamente l’EDM. In quest’ottica, da oltre 25 anni la realtà bolognese ha scelto l’elettroerosione a filo di Fanuc, preferendola per molte lavorazioni all’elettroerosione a tuffo che non superava il limite del sottosquadro di cui c’è bisogno nella realizzazione di stampi. L’azienda ha quindi inserito nel proprio stabilimento anche l’elettroerosione a filo, essenziale per potere realizzare particolari complessi senza usare come prima fresatrici tradizionali. A oggi MB dispone di due impianti Fanuc, uno di fatto l’evoluzione dell’altro già presente da anni: «Come molte macchine apripista nei settori tecnologici, la V2 svolgeva bene il suo compito anche se volevamo migliorare il discorso dell’infilaggio automatico, che nell’elettroerosione non presidiata non la rendeva così efficiente come serve oggi. Da qui il passaggio all’attuale Robocut α-C600iB, con prestazioni e interfaccia molto più user friendly. Questa macchina ha un campo di lavoro di 600x400x300 mm e un’inclinazione massima di ±30° su 150 mm, dimensioni generose che quasi sempre vanno oltre quelle abituali dei particolari trattati termicamente, ed è stata equipaggiata con un contenitore di resine più capiente, utile per ottimizzare ulteriormente le tempistiche e prolungarne la funzionalità in non presidiato. La α-C600iB ha dato continuità alla soddisfazione nei confronti del marchio giapponese mantenendo una certa omogeneità del know how relativo agli impianti Fanuc, che oltretutto ha ridotto il periodo di start up dell’impianto». La precedente soluzione senza infilaggio automatico rendeva la produzione poco flessibile, in quanto veniva utilizzata in non presidiato solo per la realizzazione di pezzi con perimetri unici molto lunghi. L’adozione di una soluzione più performante con un efficiente sistema di infilaggio automatico ha permesso all’azienda di incrementare flessibilità e produttività avendo di fatto due macchine gemelle. «L’autonomia del lavoro non presidiato non è più direttamente proporzionale alla lunghezza del percorso che viene realizzato, e oggi le macchine non presidiate possono lavorare in sicurezza senza la presenza dell’operatore: il risultato è figlio anche di una programmazione attenta che riserva le lavorazioni più lunghe durante il week end, le quali permettono di raggiungere aliquote di lavoro non presidiato anche di alcuni giorni », rileva ancora Vergnani.
Elettroerosione a filo: massimizzare l’efficienza
«Tutto nasce dalla capacità dei tecnici di creare un nesting adeguato alle situazioni della macchina programmando per una parte importante la tavola 2D del CAD, in quanto prima di fare il CAM si ha sostanzialmente il programma già pronto: il CAM deve soltanto tradurre in linguaggio macchina la tavola realizzata, che comprende il blocco grezzo di partenza da cui ricavare i pezzi e all’interno del quale vengono inserite le forme, siano esse matrici, punzoni o altri particolari. Naturalmente è importante che tutte abbiano uno spessore analogo, ovvero non abbiano bisogno di lavorazioni successive per portarle alle misure della configurazione finale che richiedono. Questo perché nell’elettroerosione si lavorano quasi sempre pezzi già temprati, con durezze sui 60 Rockwell che quindi sarebbero difficili da rilavorare. L’efficienza nell’elettroerosione dunque la si ricava principalmente in ufficio, facendo una buona programmazione e una progettazione intelligente dello stampo, con spessori abbastanza omogenei e valutando numero e posizione dei particolari inseriti nello stesso grezzo: si ottengono tempi lunghi, che si sposano bene con il lavoro non presidiato. Quest’ultimo viene ottimamente eseguito dalle macchine Fanuc, la cui precisione e affidabilità ci hanno spinto a confermare la scelta del marchio. All’inizio abbiamo anche considerato se acquistare una macchina con campo di lavoro più piccolo anziché una delle stesse dimensioni di quella che già avevamo, poi ha giustamente prevalso la volontà di avere l’alternativa già pronta di una macchina in sostanza gemella». Oltre all’affidabilità e alla qualità della lavorazione, un altro aspetto che ha incontrato i favori di MB è il CN di ultima generazione, che ha completamente rivisto il rapporto con l’operatore sia nella parte di programmazione sia nella parte di CAM. In questo ambiente software si possono importare disegni in file .dxf e creare un percorso utensile direttamente dal bordo macchina. Si riducono così i tempi di programmazione dell’operatore alle prese con la nuova α-C600iB, che quindi si può dedicare alle attività a valore aggiunto. Non essendo state riscontrate grandi problematiche dopo l’acquisto, il servizio post vendita non ha mai dovuto richiedere interventi a fronte di un guasto. Si è quindi soltanto limitato all’acquisto di ricambi al massimo con una telefonata o l’invio di un’e-mail.
Condividi l'articolo
Scegli su quale Social Network vuoi condividere