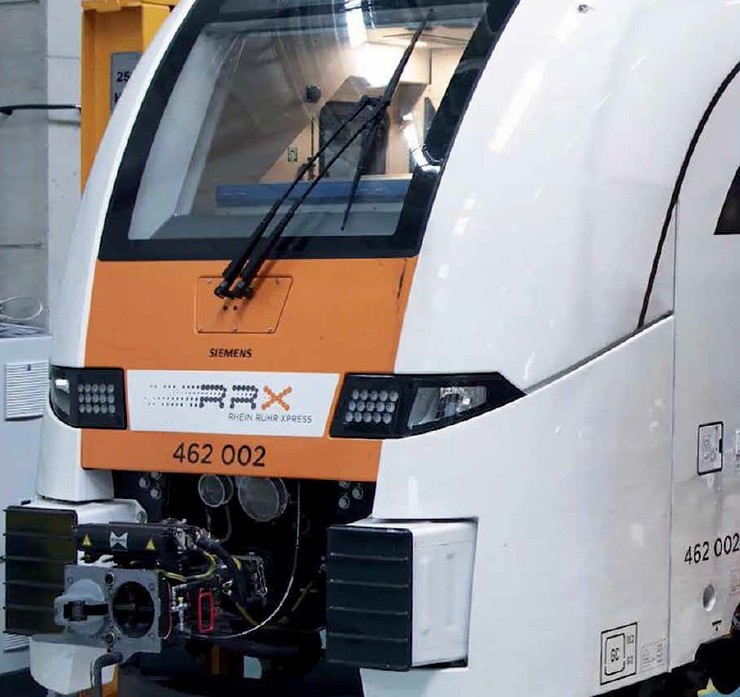
Le principali aziende di trasporto europee, da Bombardier Transportation a Deutsche Bahn ESG e Siemens Mobility, hanno investito nella fabbricazione additiva. Abbiamo incontrato gli esperti di queste aziende per conoscere meglio quali sono le sfide produttive poste dal settore e come l’adozione di questa tecnologia contribuisca ad affrontarle.
In tutto il mondo le aziende ferroviarie si trovano ad affrontare sfide crescenti per costruire treni e provvedere alla loro manutenzione in modo sempre più veloce e a costi inferiori. La spinta verso l’eccellenza ingegneristica e progettuale, unitamente a rigorose normative che regolamentano materiali e funzionalità nell’industria ferroviaria, aggiungono ulteriori livelli di complessità alla produzione di parti nuove o di ricambio per il settore. Per soddisfare tali esigenze tutte le aziende di trasporto leader in Europa, da Bombardier Transportation a Deutsche Bahn ESG e Siemens Mobility, hanno investito nella fabbricazione additiva. In questa intervista esperti di queste aziende forniscono la propria visione delle sfide produttive poste dal settore, spiegando come l’adozione di questa tecnologia contribuisca ad affrontarle.
Il ruolo delle aziende
Michael Kuczmik, Responsabile Fabbricazione Additiva/Servizio Clienti Mobilità di Siemens Mobility, sottolinea: «In tutta la Germania, gli operatori ferroviari si occupano della gestione quotidiana dei treni e hanno il compito di prendersi cura del trasporto pubblico. Le società di manutenzione garantiscono la disponibilità e talvolta l’attrattività dei treni, mentre definirei i fornitori di materiale rotabile come fornitori di veicoli ferroviari e di infrastrutture ai proprietari, che possono essere gli operatori stessi o una società di noleggio. Per quanto riguarda Siemens, siamo in grado di svolgere ognuno di questi ruoli in modo da supportare i nostri clienti con un portafoglio completo, a seconda delle caratteristiche e delle esigenze».
«Alla Bombardier operiamo in modo analogo», conferma André Bialoscek, Responsabile Vehicle Physical Integration presso lo stabilimento Bombardier Transportation di Hennigsdorf. «A volte siamo l’unico fornitore di materiale rotabile, oltre a essere responsabili della manutenzione e del funzionamento efficiente delle reti ferroviarie. Tutto dipende dal modello di business dei nostri clienti».
Nel Regno Unito la situazione è più segmentata, spiega invece Martin Stevens, Responsabile Ingegneria Meccanica di Deutsche Bahn ESG. «Abbiamo fornitori di materiale rotabile che finanziano i treni e li noleggiano agli operatori. Gli operatori gestiscono i servizi ferroviari giornalieri e si occupano della manutenzione di base. Poi ci sono società di manutenzione addette al ricondizionamento e alla revisione dei veicoli di grandi dimensioni. E infine società di supporto ingegneristico, come DB ESG, che erogano servizi tecnici per l’industria».
Le sfide del mercato
Non ha dubbi Stevens quando spiega che la sfida principale è rappresentata dai bassissimi volumi di produzione. «Un ordine importante di un unico modello di treno per un valore complessivo di 800 milioni di sterline serve a produrre un centinaio di unità e questo è un numero troppo esiguo per una fabbricazione di massa standard. Se a ciò si aggiunge che i treni arrivano ad avere una vita utile di oltre 40 anni, si configura una situazione in cui esistono poche unità funzionanti di una quantità enorme di modelli di treni diversi. Questo rappresenta un’autentica sfida per la fornitura di parti di ricambio, perché non è possibile sfruttare le tecniche di produzione di massa per la fabbricazione di questi pezzi».
Concorda Kuczmik, che sottolinea: «In alcuni casi, abbiamo visto treni che arrivano ad avere una vita utile di 60 anni. Nel peggiore dei casi, poi, gli alti costi una tantum e tempi di consegna talvolta molto lunghi possono essere causa di obsolescenza. D’altra parte, comprendere le norme e garantire la conformità per casi d’uso specifici rappresentano a loro volta una sfida significativa e un prerequisito assoluto, motivo per cui ci si può fidare solo di fornitori qualificati».
«Dobbiamo consegnare i treni molto più velocemente rispetto a 3 o 5 anni fa», conferma Bialoscek. «Questo aumenta la pressione generale su tutti gli aspetti delle nostre operazioni compresi l’ingegneria, l’approvvigionamento, la produzione e il collaudo/l’omologazione. Dobbiamo adattarci rapidamente a un mercato in continua evoluzione e questo spesso può rappresentare una spinta costante per la nostra azienda a rimanere all’avanguardia. È qui che entra in gioco la fabbricazione additiva».
L’AM per il ferroviario
«La fabbricazione additiva – prosegue Bialoscek – è l’approccio giusto e rappresenta un significativo passo in avanti per le aziende di trasporto. Utilizzando questa tecnologia, siamo in grado di produrre rapidamente non solo prototipi, ma anche pezzi finali delle dimensioni necessarie durante tutto il processo di convalida dei progetti di nuovi treni, comprese anche parti in serie. Un altro elemento importante è il servizio on demand, in cui la fabbricazione additiva offre enormi vantaggi per la sostituzione di parti obsolete o la produzione di piccoli lotti, così come per la reingegnerizzazione di componenti».
«Siemens Mobility – spiega Kuczmik – ha adottato questa tecnologia da tempo, creando appositamente un team di 18 persone che supportano i clienti interni ed esterni fornendo consulenza ingegneristica e assistenza per la realizzazione di parti di ricambio tramite fabbricazione additiva. A seconda dei tempi di consegna richiesti, i clienti possono ordinare pezzi di ricambio on demand attraverso il nostro Easy Spares Marketplace. E, se necessario, siamo in grado di rielaborare anche progetti di 30 anni fa, talvolta in collaborazione con i clienti stessi».
Stevens spiega: «La fabbricazione additiva rappresenta anche per noi una fetta enorme della nostra attività ed è perfetta per produzioni in volumi ridotti, perché consente una progettazione e una stampa semplificate, eliminando ritardi iniziali o costi di attrezzaggio. Per esempio, se fossero necessarie 5 bocchette di ventilazione per una piccola flotta di treni, basterebbe la fabbricazione additiva per produrle. È vero che il costo unitario sarebbe più alto, ma potremmo acquistarne solo cinque e riceverle in un paio di settimane, piuttosto che 10 mila in 3 mesi. Gli enormi vantaggi superano di gran lunga i possibili svantaggi. Infatti, di recente, abbiamo collaborato con Angel Trains, uno dei tre grandi fornitori di materiale rotabile del Regno Unito, e con l’operatore ferroviario Chiltern Railways per montare e testare con successo le prime parti stampate in 3D sui treni passeggeri britannici. Abbiamo infatti diversi esempi di parti montate sui treni delle Chiltern Railways, come le maniglie interne che originariamente erano in alluminio fuso e il cui design è diventato obsoleto. È raro che queste parti debbano essere sostituite, ma l’operatore ormai ha esaurito le scorte e se si verifica una rottura le norme impongono la riparazione entro una settimana. In questa situazione, la fabbricazione additiva ci ha fornito la soluzione ideale perché ci ha permesso di produrne rapidamente 5 utilizzando il materiale Ultem 9085 di Stratasys, una resina compatibile con i requisiti di fiamma, fumo e tossicità».
Un altro esempio di componente realizzato con tecnologia additiva arriva da Siemens Mobility, racconta Kuczmik: «Il nostro è un caso di applicazione in fase di post vendita, perché produciamo i componenti della scocca anteriore di veicoli leggeri su rotaia, noti anche come tram. I tram condi vidono i binari con altri veicoli ferroviari e questo è la causa principale di molti incidenti. Le nostre parti stampate sostituiscono le sezioni danneggiate come il paraurti anteriore e la consegna non richiede più mesi, ma avviene nel giro di pochi giorni. I clienti possono ordinare un unico pezzo invece di dieci e non hanno bisogno di sostituire l’intero paraurti, ma solo una sezione pari a un terzo. Questo significa che il lavoro può essere svolto da una sola persona in modo più rapido ed economico».
Anche in Bombardier Transportation hanno interessanti esperienze in questo ambito: «Ritornando alle bocchette di ventilazione – conclude Bialoscek – grazie alla tecnologia di fabbricazione additiva di Stratasys noi siamo riusciti a ridurre i tempi di produzione di una parte personalizzata del sistema di condotti dell’aria da 4 mesi a circa 4 settimane. Il risultato è stato un risparmio di quasi il 77% del tempo, un traguardo incredibile per il nostro reparto. Un esempio perfetto di come adesso siamo in grado di produrre determinati pezzi su richiesta in base alle nostre esigenze, senza dovere sostenere lunghi tempi di produzione oppure scendere a compromessi con la qualità del materiale».
I vantaggi dell’AM
«I vantaggi di una produzione a tiratura limitata offerti dalla fabbricazione additiva – spiega Yann Rageul, Responsabile Manufacturing Solutions di Stratasys – soddisfano in modo ideale i requisiti dell’industria ferroviaria: non sorprende quindi che questa tecnologia sia diventata parte integrante delle attività dei principali operatori del settore. Negli ultimi tre decenni, la fabbricazione additiva è maturata e la gamma delle possibili applicazioni è cresciuta in modo considerevole. La stampa 3D è ormai uno strumento di livello industriale che i fornitori dei servizi ferroviari possono sfruttare per assicurare l’approvvigionamento di parti per l’assistenza, per creare attrezzi a supporto di operatività e manutenzione, per migliorare la sicurezza e l’esperienza del cliente. Poiché sono sempre più numerose le imprese del settore che ottimizzano l’uso della fabbricazione additiva tramite l’inventario digitale, la produzione di pezzi di ricambio on demand, dove necessari e nella quantità esatta desiderata, è già una realtà. In questo modo non solo si riduce la necessità di magazzini e scorte di pezzi di ricambio, ma si può anche accelerare notevolmente la velocità degli interventi di manutenzione e riparazione dei treni. Per chi vuole adottare questo modello di business e salire a bordo, la prossima fermata non è mai troppo lontana».
Condividi l'articolo
Scegli su quale Social Network vuoi condividere