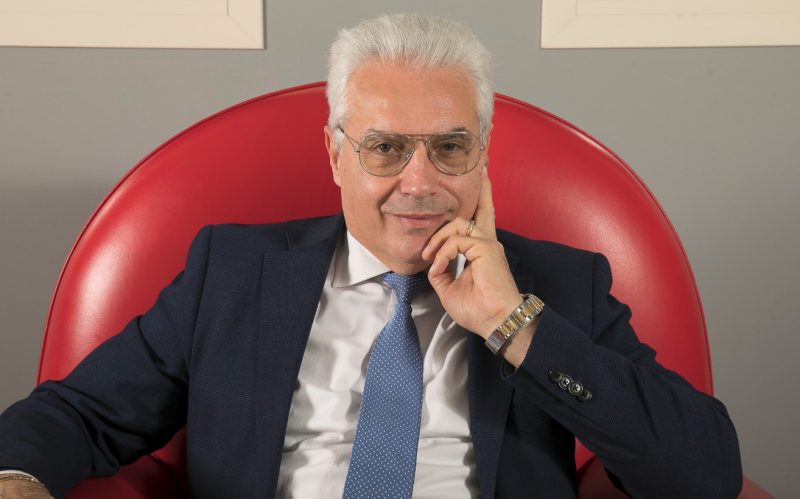
Luca Iuliano è professore ordinario di Tecnologia e Sistemi di Produzione al Politecnico di Torino, coordinatore del Master Universitario di II livello in Manufacturing 4.0, coordinatore del Master Universitario di II livello in Additive Manufacturing e Project Manager del Centro Interdipartimentale di Additive Manufacturing del Politecnico di Torino. Inoltre è autore e coautore di 2 testi sulla fabbricazione additiva e microfusione e di oltre 250 lavori a stampa nei settori delle lavorazioni ad alta velocità di leghe termoresistenti e compositi a matrice metallica, delle lavorazioni non convenzionali su leghe termoresistenti e compositi a matrice metallica, dell’Additive Manufacturing e della reverse engineering. È presidente del centro di competenza CIM4.0 (Competence Industry Manufacturing 4.0) e membro del Consiglio Direttivo dell’AITA (Associazione Italiana di Tecnologie Additive).
di Edoardo Oldrati e Raffaella Quadri
.
Come presidente del centro di competenza CIM4.0 quali obiettivi si è posto?
«Gli obiettivi del CIM4.0, di cui ho assunto la presidenza a fine 2018, sono sostanzialmente quattro. Il primo è relativo al recepimento delle linee pilota per il trasferimento tecnologico. Il nostro Competence Center ha deciso di concentrarsi su due pillar di Industria 4.0: l’AM (Additive Manufacturing) o produzione additiva e la digitalizzazione della fabbrica. L’intento è definire la struttura di queste due linee operative, sfruttando le competenze dei nostri 23 consorziati e mettendole a disposizione soprattutto delle PMI.
Il secondo e il terzo obiettivo sono inerenti alla formazione, con l’attuazione di un learning hub e l’avvio della CIM4.0 Academy che prevede 5 mesi di attività e 350 ore complessive di lavoro. Di recente abbiamo consegnato i primi 24 diplomi di “Industry 4.0 Innovation and Technology Leader”, un’attività unica nel panorama nazionale e il 4 giugno è iniziata la seconda edizione.
Il quarto obiettivo è gestire i finanziamenti che il Ministero dello Sviluppo Economico ha affidato al Competence Center, per una cifra di circa 3 milioni di euro. Sono stati fatti due bandi: uno per le piccolissime imprese, avviato a fine 2019, e uno destinato anche alle grandi imprese, per il quale abbiamo ricevuto circa 120 domande e ne abbiamo potuto finanziare soltanto 17. Una piena soddisfazione».
Sempre più spesso si identifica come essenziale per lo sviluppo della manifattura italiana un’intensa attività di reskilling: quali sono le competenze “nuove” di cui ha bisogno la nostra industria oggi?
«Il manifatturiero italiano ha bisogno di digitale, che va declinato in tecnologia hardware e software. Riguarda quindi tutte le varie tematiche di Industria 4.0, dai big data alla cybersecurity, all’AM fino alla robotica collaborativa. Tematiche che evolvono in modo molto rapido e spesso le aziende, soprattutto le più piccole, hanno difficoltà a mantenere i propri dipendenti al passo con la tecnologia. L’obiettivo del nostro learning hub, dunque, è fare l’upskilling e il reskilling delle persone che operano in azienda. La CIM4.0 Academy ha dato una risposta in questi termini in quanto, seguendo la politica del Competence Center, non forma i giovani che escono dall’università bensì ridà le competenze sia a chi opera in azienda sia a coloro che purtroppo per la congiuntura economica hanno perso il lavoro o sono in attesa di ricollocazione e necessitano di essere aggiornati. Per esempio, nell’ambito della CIM4.0 Academy appena conclusa, grazie anche all’accordo con Federmanager, sono state rese disponibili cinque borse di studio a cinque manager che avevano perso il lavoro nell’ultimo periodo e due di questi hanno già trovato collocazione, mentre gli altri tre la troveranno rapidamente; indice che queste attività funzionano. Le attività dei Competence Center sono fondamentali proprio perché, senza sovrapporsi alle iniziative universitarie, danno quelle competenze in più che si possono ottenere sfruttando il sapere universitario e soprattutto quello delle aziende».
Il CIM4.0 si rivolge in particolare alle PMI del manifatturiero: in cosa devono cambiare queste realtà per cogliere a pieno le opportunità della transizione digitale?
«Le PMI devono essere pronte ad attuare la trasformazione digitale: devono avere le competenze al proprio interno per svolgere tali attività e devono investire in nuove tecnologie, come l’AM o la robotica collaborativa, in modo da soddisfare le richieste del mercato. Per queste finalità se da un lato il Competence Center ha attivato il progetto di formazione dall’altro le PMI hanno la possibilità, prima di effettuare gli investimenti, di testare le proprie soluzioni sulle linee del Competence Center – in ambito sia di digitalizzazione della fabbrica sia di AM – utilizzandole come una sorta di palestra ed evitando così il rischio di effettuare investimenti non corretti».
Impatto ambientale e costo delle materie prime sono aspetti che hanno un peso importante nella scelta delle tecnologie produttive da adottare. In quest’ottica quali punti di forza può vantare l’AM?
«Se consideriamo l’AM più conosciuta, cioè quella del metallo, il punto di partenza per la quasi totalità dei casi è la polvere; ci sono altre tecniche, che partono dal filo ma sono ancora di nicchia. Polvere che si produce con sistemi di gas di atomizzazione. Dopodiché la tecnologia additiva è in grado di produrre componenti in un volume attorno al ezzo metro cubo con pochi kW di energia di potenza installata. Questo rappresenta un grande vantaggio, perché per fare un pezzo di metallo con un simile ingombro in fonderia è necessario avere un impianto che consuma MW di potenza e che non può essere installato all’interno delle città. Viceversa con l’AM, potendo operare con macchine a basso assorbimento, è possibile rivedere la strategia industriale, riportare all’interno delle città alcune operazioni manifatturiere e abbattere l’impatto ambientale. Soprattutto la tecnologia additiva – lo dice la parola stessa – aggiunge materiale solo dove necessario; le altre tecniche, quelle sottrattive ad asportazione di truciolo, partono invece da un parallelepipedo di metallo di cui si butta via anche il 90% del materiale per ottenere il pezzo. Con l’AM invece avviene esattamente il contrario e lo spreco è ridotto al minimo, pari solo a qualche punto percentuale. Aspetti “green” delle tecnologie per il metallo che valgono però anche per i polimeri, per i quali non si utilizzano più gli stampi, ottenendo anche in questo caso una serie di vantaggi dal punto di vista ambientale».
Come avviene per ogni nuova tecnologia, la rapidità con la quale un’azienda acquisisce esperienze e competenze si trasforma in un vantaggio competitivo. Da questo punto di vista, rispetto agli altri Paesi, l’Italia come si posiziona a livello di conoscenza e utilizzo dell’AM in ambito produttivo?
«La situazione è a macchia di leopardo, ci sono molte competenze in determinate aree, mentre in altri ambiti queste tecnologie non sono ancora sfruttate appieno. I settori consolidati sono l’aerospaziale e il medicale, la cui caratteristica principale è data dai volumi limitati e dove quindi si possono sfruttare al meglio queste tecnologie; e ancora il racing: pensiamo per esempio alla Formula 1 che sfrutta l’AM per svisviluppare le vetture. Viceversa, si fa fatica a penetrare in certi mercati di massa. La situazione è varia anche a livello di attività di ricerca. A Torino abbiamo un centro di eccellenza a livello internazionale costituito dal Centro interdipartimentale di Additive Manufacturing del Politecnico di Torino (IAM@PoliTo) che si affianca al CIM4.0. Siamo in grado di produrre sia le polveri sia i componenti e caratterizzarli con la tomografia. Ma siamo gli unici in Italia con il ciclo completo dell’AM, in grado di coprire tutte le attività di ricerca. Se un’azienda necessita di sviluppare un componente in una nuova lega, al centro IAM del Politecnico di Torino possiamo progettare la lega, producendone con il gas atomizzatore una quantità tra i 50 e i 100 kg, dopodiché verifichiamo che questa lega sia trasformabile nell’ambito della tecnologia additiva e, in caso affermativo, realizziamo il prototipo e lo caratterizziamo con la tomografia. Quindi curiamo: produzione della lega, definizione dei parametri di processo e arrivo al prototipo. La seguente fase di produzione e industrializzazione, e trasferimento del prototipo sul mercato, è un’attività del CIM4.0 dove sono presenti impianti di AM a elevata produttività».
Lotto1 o produzione? Alternativa o affiancamento alle altre tecnologie produttive? L’AM ha un enorme potenziale di sviluppo, ma inizia ad avere alle spalle un buon bagaglio di esperienze. La fabbricazione additiva oggi ha già trovato la sua collocazione nel settore industriale?
«L’attuale AM è un’evoluzione della vecchia prototipazione rapida arrivata in Italia alla fine degli anni Ottanta del Novecento. In 30 anni si è passati da una tecnologia destinata prettamente a produrre prototipi a una che si vuole utilizzare anche in produzione. Il problema è che la maggior parte delle macchine attualmente presenti sul mercato, pensate per fare prototipi, non ha i classici sistemi di automazione previsti dalla produzione di massa e ha quindi difficoltà a rispettare cadenze produttive molto elevate. Di conseguenza, la produttività di queste macchine risulta più bassa rispetto a quella delle tecnologie tradizionali. Occorre però capire che l’AM non è la panacea di tutti i mali, è una tecnologia che si deve affiancare e integrare alle tecnologie tradizionali. A oggi il maggiore vantaggio è per le produzioni che hanno un limitato numero di componenti del lotto o anche per produzioni personalizzate, possibili quindi in settori in cui i numeri sono comunque elevati e le tecnologie additive non sono ancora pienamente competitive. Per esempio, in provincia di Torino abbiamo seguito il caso di due aziende, che effettuano unicamente lavorazione meccanica, che hanno integrato le tecnologie additive nella loro offerta di servizi, proponendo ai propri clienti anche le riprogettazioni dei componenti e riducendo così i costi».
Cosa potrebbero fare le aziende italiane per facilitare l’attività di trasferimento tecnologico dal mondo universitario a quello industriale? Di cosa hanno bisogno gli atenei per essere più efficaci in questa attività così importante?
«Il cambiamento deve essere da entrambe le parti. Da un lato l’università deve essere aperta alle richieste del mondo industriale in modo da rispondervi con progetti di ricerca che siano adeguati alle sue necessità. La ricerca di base è fondamentale, ma bisogna anche essere aperti ad attività più legate al trasferimento tecnologico, andando a risolvere dei problemi che le aziende possono avere. L’università può agire in due modi: innanzitutto dando uno strumento di formazione per potere rendere l’azienda indipendente nell’ambito dell’AM e poi può definire tirocini, insieme alle imprese, in cui giovani che sono già stati formati sulla fabbricazione additiva e sull’ottimizzazione topologica possono entrare in azienda e dare il proprio contributo. Le aziende viceversa devono crederci e portare all’università problemi concreti. Una soluzione sono i voucher che già utilizziamo in Piemonte: ognuno copre una cifra di spesa tra i 60 e i 70mila euro che può essere spesa presso il centro IAM@PoliTo per fare attività di riprogettazione o di valutazione con la tomografia. L’azienda grazie al voucher può usufruire delle nostre competenze. È un metodo che, secondo me, bisogna adottare; che sia un voucher, un progetto nazionale o europeo l’importante è lavorare assieme per definire e portare avanti obiettivi comuni. Questo richiede ovviamente che ci sia un’apertura mentale sia da parte dell’azienda sia da parte dall’università che, soprattutto nel settore tecnologie e sistemi di lavorazione, deve essere un po’ più vicina all’impresa rispetto a quanto fatto finora».
Qual è la sua idea di fabbrica 4.0? Ci aiuta a tratteggiare le caratteristiche dell’industria di domani?
«Una fabbrica 4.0 che già evolve verso il 5.0, con le tecnologie abilitanti integrate con una trasformazione digitale che deve interessare tutti i settori dell’azienda, dall’amministrazione fino alla spedizione passando per la produzione, la gestione e la logistica. Ovviamente cambieranno le tecnologie, ma la fabbrica è fatta anche da persone. Quindi, oltre che in tecnologia digitale bisogna investire anche sul personale: non ci sarà più l’operaio che carica e scarica il pezzo ma ci sarà il gestore del reparto, della linea, della macchina che dovrà avere competenze elevate. Avremo fabbriche green, più pulite e a basse emissioni con tecnologie abilitanti e con una gestione anche in remoto delle attività. Pensiamo per esempio a certe attività di manutenzione, almeno quelle basilari, che possono essere definite in remoto. Addirittura, la fabbrica del futuro potrebbe anche avere una parte di impianti e attrezzature non di proprietà ma in utilizzo sulla base delle ore di impiego. Uno scenario futuristico e dirompente rispetto a quello che avviene attualmente perché scarica l’impresa da una serie di costi vivi e di ammortamento che molte volte influiscono sui bilanci. Aumenterà ovviamente anche il modello dei servizi. Evoluzioni che richiederanno un cambio radicale delle modalità».
Condividi l'articolo
Scegli su quale Social Network vuoi condividere