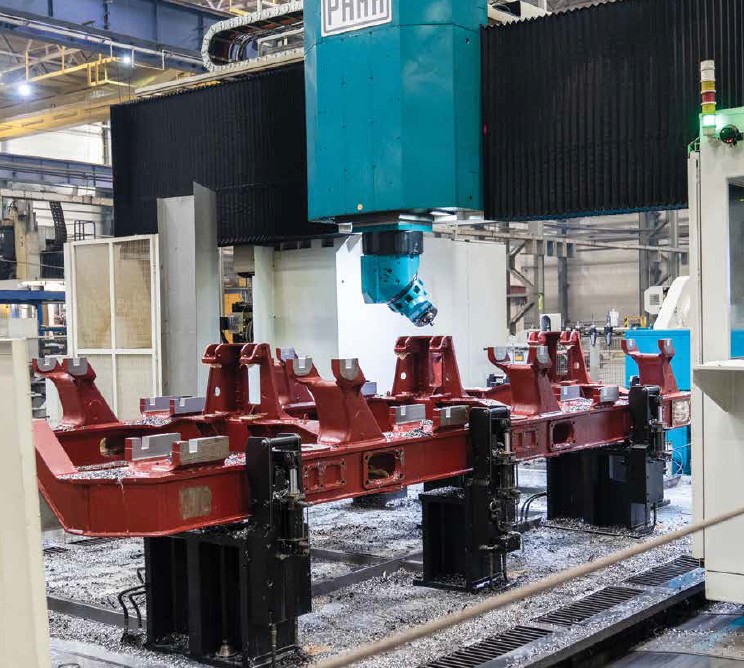
L’azienda russa BMZ ha scelto le soluzioni Pama per incrementare in modo significativo la produttività nei propri impianti. Il risultato è una riduzione dei tempi di lavorazione di circa il 40% rispetto al passato.
di Flavio Tosato
BMZ (Bryansk Engineering Plant) sviluppa e produce nei suoi stabilimenti di Bryansk, in Russia, locomotive diesel di linea, locomotori di manovra, vagoni merci e vagoni speciali. BMZ appartiene al Gruppo russo Transmashholding, la più grande società russa nel mercato del trasporto ferroviario e una delle più grandi al mondo nello stesso settore. La fabbrica nacque inizialmente come segheria per la produzione di traversine lungo la ferrovia Riga-Orel e fu costituita con “Licenza Imperiale” nel lontano 1873 in “società per la produzione di acciai e costruzioni meccaniche”. La prima locomotiva a vapore fu prodotta nel 1892. Come altre fabbriche russe, la BMZ seguì le vicende storiche del Paese: tra la rivoluzione russa e l’inizio della Seconda guerra mondiale si sviluppò nella produzione di treni e veicoli militari, costituendo anche un istituto tecnico che ha formato generazioni di ingegneri meccanici. Fu evacuata e distrutta durante l’invasione del Paese nella guerra (per i russi la Grande Guerra Patriottica) e completamente ricostruita a partire dal 1945, riprendendo in pieno la produzione di locomotive e materiale ferroviario. Con la fine del periodo sovietico, dal 1992 la fabbrica subì un periodo di forte crisi, per risollevarsi definitivamente a partire dal 2002 con l’entrata nel gruppo Transmashholding, che diede un forte impulso agli investimenti e alla innovazione tecnologica. Attualmente la capacità produttiva annua è di circa 300 locomotori diesel per il trasporto commerciale a lungo raggio e 240 locomotori di manovra. La forza lavoro aziendale è di circa 8800 dipendenti.
Un rapporto di cooperazione tecnologica
Pama ha fornito e condotto a termine l’installazione della prima macchina Vertiram 2000 nel 2018, la seconda macchina della stessa serie è in corso di avviamento nella prima metà del 2020. La macchina è dedicata alla lavorazione completa dei carrelli di locomotive diesel di linea, prodotto che costituisce il core business di questa fabbrica. La decisione di implementare nei reparti produttivi una macchina di questo genere nasce dalla necessità di incrementare la produttività dell’impianto, riducendo drasticamente i tempi di produzione dei componenti principali del locomotore. Possiamo affermare che Pama è stata scelta come fornitore dell’impianto in base alla comprovata esperienza nel settore specifico e alla capacità di realizzare un impianto personalizzato sulla base delle esigenze tecnologiche dell’utilizzatore, a partire da un prodotto fortemente consolidato e di elevate prestazioni. Non è un caso che l’azienda italiana disponga di un team di tecnologi applicativi di vasta esperienza, che la rende in grado di fornire ai suoi clienti non soltanto macchine di indiscussa qualità e prestazioni, ma anche un servizio tecnologico prezioso per implementare le tecnologie che ne consentono il pieno sfruttamento. Questa è stata in definitiva la ragione che ha convinto l’utilizzatore ad acquistare la seconda macchina dopo la prima: una riduzione dei tempi di lavorazione di circa il 40% rispetto ai cicli tecnologici utilizzati in precedenza.
Una tecnologia vincente
Durante le fasi di definizione dell’impianto, i tecnologi Pama hanno tenuto diversi incontri con i loro omologhi della JSC-BMZ, durante i quali sono stati discussi e definiti gli obiettivi di riproduttività dell’impianto e i metodi tecnologici atti a raggiungerli. Durante questa fase i tecnologi si sono “calati” nell’officina del cliente e, disegni alla mano, hanno sviscerato con i colleghi di BMZ tutte le particolarità e le criticità della lavorazione di questi componenti, facendo tesoro delle indicazioni fornite dagli operatori e dai tecnologi del cliente. Inizialmente sembrava impossibile raggiungere l’ambizioso obiettivo di una così drastica riduzione del tempo di lavorazione del singolo carrello, ma grazie a uno studio tecnologico accurato, partendo dal disegno del pezzo e da una aperta analisi di tutte le possibilità che si prospettavano, è stata adottata una strategia vincente basata sul concetto di ridurre al minimo i piazzamenti di lavorazione del pezzo. In pratica, il pezzo grezzo viene posizionato una sola volta nelle attrezzature di bloccaggio e viene tolto dalla macchina completamente lavorato in tutti i dettagli. Per far questo, considerando che il carrello deve essere necessariamente lavorato sula faccia superiore e inferiore, si è ricorsi all’utilizzo di una testa speciale a mandrino inverso in grado di eseguire fresature, forature e maschiature dal basso verso l’alto, con la stessa capacità di lavoro e precisione del mandrino principale. La testa viene caricata con procedura completamente automatica sul ram della macchina, come ogni altra testa accessoria di cui è dotato l’impianto. Le forma e le dimensioni della testa sono state accuratamente studiate per potere entrare nelle cavità del pezzo e così potere lavorare, senza entrare in collisione, tutti i dettagli della faccia inferiore. A loro volta le attrezzature di staffaggio sono state conformate e dimensionate in modo da consentire un rigido e preciso bloccaggio del pezzo e al tempo stesso consentire il passaggio al loro interno della testa operatrice. Le attrezzature di staffaggio sono di tipo meccanico/ idraulico, dove il caricamento del pezzo viene fatto a mano mediante il paranco di officina. Il settaggio dei riscontri meccanici viene tarato a mano in base alle dimensioni medie dei grezzi, mentre il bloccaggio sui riscontri di posizionamento e il bloccaggio di forza del pezzo sono attuati idraulicamente. Tutte le lavorazioni della faccia superiore del pezzo vengono eseguite con altre due teste: una robusta testa a mandrino diritto verticale, di elevata potenza e numero di giri, e una testa universale a doppio asse di rotazione con posizionamento ogni 0,001°. Un ulteriore fattore che ha consentito la drastica riduzione di tempi di lavorazione è stato l’utilizzo di utensileria di elevata produttività. Sono stati anche impiegati, ove possibile, utensili multipli (che consentono diverse operazioni in un’unica passata assiale), che hanno contribuito a ridurre i tempi morti di riposizionamento e cambio utensile. Ovviamente l’impiego di tale utensileria è stato reso possibile dalla disponibilità di teste di elevata rigidità, aventi allo stesso tempo elevata velocità di rotazione ed elevata coppia disponibile.
La macchina
Il modello prescelto per queste realizzazioni è un Vertiram 2000 del tipo a portale mobile con traversa fissa. In effetti il Vertiram 2000 è il modello più diffuso della serie dei portali Pama, in quanto riunisce un mix di prestazioni e un rapporto qualità/prezzo che lo rende, nella sua categoria, una della macchine migliori presenti sul mercato. I punti di forza di questa macchina sono molteplici, come la disponibilità di motore mandrino direct drive (senza cambio gamma) a elevate prestazioni disponibile in diverse versioni di coppia/potenza/velocità, da 73 kW, 6000 giri/min e coppia 1200 Nm fino a 94 kW e coppia di 2600 Nm. Importante anche la struttura del portale in acciaio elettrosaldato stabilizzato, opportunamente dimensionato e calcolato tramite software di FEM (analisi agli elementi finiti). Questa soluzione garantisce elevata rigidezza statica e dinamica, ottimizzando nel contempo la massa della struttura al fine di massimizzare le accelerazioni. Il RAM della macchina, di generose dimensioni, è realizzato in ghisa sferoidale ed è guidato all’interno della testa mediante pattini idrostatici in bronzo. Questa soluzione, unitamente ai piani di lavoro realizzati in ghisa, garantisce un elevato smorzamento delle vibrazioni proprio vicino a dove queste vengono generate. Le linee cinematiche sono poi di tipo dual drive su tutti gli assi. La traslazione del portale sui banchi è comandata, in asservimento gantry, da due coppie di servomotori con recupero elettronico del gioco da CN; la corsa verticale del RAM è comandata da una coppia di viti a sfere di precisione con motorizzazione indipendente e asservimento gantry; la corsa orizzontale della testa è comandata da due gruppi servomotoreriduttore con recupero del gioco via CN. Le motorizzazioni usate consentono una spinta su tutti gli assi superiore a 40.000 N, con accelerazioni fino a 1 m/s2. Un cenno particolare meritano le teste accessorie che possono essere impiegate sui modelli Vertiram: esse sono state concepite come vere e proprie teste, progettate per avere una vita utile e intervalli di manutenzione equivalenti a quelli di tutto il resto della macchina. Per questo sono estesamente sensorizzate, al fine di rilevare tempestivamente possibili stati di surriscaldamento, vibrazioni o collisioni, carenza di lubrificazione e così via, in modo da prevenire ed evitare danneggiamenti e fermate dell’impianto. Fattore essenziale per garantire elevate prestazioni di velocità, precisione e massima resistenza all’usura dei gruppi cinematici è la lubrificazione: dove possibile è ottenuta con sistemi a ricircolo d’olio climatizzato, con portate dell’ordine di alcuni litri al minuto che consentono anche una efficace asportazione del calore; nei casi in cui le dimensioni della testa non permettano un sicuro sistema di recupero si utilizzano invece sistemi di lubrificazione aria-olio. Infine, per garantire un’ottima stabilità geometrica, le teste sono termostabilizzate con ricircolo di fluido a temperatura controllata.
Condividi l'articolo
Scegli su quale Social Network vuoi condividere