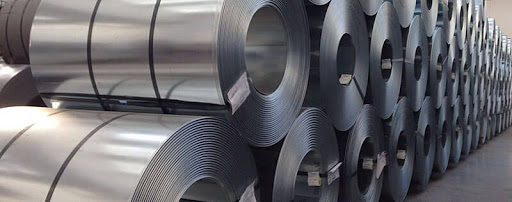
Sulla rivista "TecnoLamiera" abbiamo dato spazio ai costruttori d'impianti per la lavorazione della lamiera direttamente da coil, dando loro modo di raccontare concretamente come affrontano i cambiamenti del mercato italiano e internazionale.
di Davide Davò
Tra gli oggetti che ci circondano, la presenza di particolari in lamiera è ben visibile attorno a noi, dall’arredo di casa ai componenti delle nostre auto fino agli strumenti usati in ufficio o nelle officine meccaniche. Pezzi che possono essere lavorati partendo da un foglio di lamiera precedentemente tagliato a misura oppure operando direttamente sul nastro di coil. Quest’ultima è una tecnologia molto diffusa e in continua evoluzione per garantire a chi la utilizza performance sempre migliori in termini di produttività, qualità del pezzo lavorato e affidabilità dal sistema produttivo. Per capire quali sono le principali richieste di chi lavora la lamiera direttamente dal coil e in che modo i vari costruttori di macchine rispondono a tali esigenze, la nostra rivista TecnoLamiera ha organizzato un’inchiesta per dare ai lettori una fotografia dello stato dell’arte di questa tecnologia di impianti.
Ascoltare il mercato
A rompere il ghiaccio è Lara Cecchi di Servopresse, che sottolinea l’importanza di adattarsi ai cambiamenti del mercato e di sviluppare soluzioni flessibili. «Servopresse è specializzata nello sviluppo di impianti di svolgimento e raddrizzatura coil per l’asservimento delle presse, ma negli anni il nostro portafoglio di soluzioni si è ampliato e oggi le nostre linee possono essere abbinate a presse, punzonatrici, teste slitter, profilatrici o macchine laser fibra. Pertanto trovano applicazione in un’ampia varietà di settori, che per quanto ci riguarda hanno tutti in comune la richiesta dell’elevata produttività. Nell’automotive, a questa esigenza si sta affiancando anche la necessità di disporre di macchine flessibili poiché la trasformazione dell’auto verso le tecnologie elettriche, pure o ibride che siano, porta all’utilizzo di nuovi materiali e allo sviluppo di nuovi componenti. Ciò influenza anche le caratteristiche che devono avere le presse, e di conseguenza anche i nostri sistemi si devono adeguare a una produzione caratterizzata da un’alta variabilità del prodotto. Altrettanto apprezzata è la nostra capacità di sviluppare soluzioni su misura per specifiche esigenze. Per esempio in tempi recenti ci è stato commissionato lo sviluppo di una linea composta da una raddrizzatrice e un aspo svolgitore, con quest’ultimo che ha la peculiarità di potere accogliere contemporaneamente 6 diversi coil movimentandoli uno alla volta per alimentare un’unica raddrizzatrice».
Veronica Just di Millutensil illustra i vantaggi derivanti dal potere disporre di un ampio portafoglio prodotti per assecondare le più svariate richieste. «L’ampio programma di soluzioni tecnologiche che propone Millutensil ci permette di offrire coil lines a settori diversi. Ogni settore ha esigenze distinte e specifiche, e la tecnologia offerta deve essere in grado di soddisfare le richieste del prodotto finito che i nostri clienti vogliono realizzare. Possiamo partire dal settore dell’elettronica e della lamination dove sono richieste linee per presse veloci e particolari di precisione per poi spostarci al settore del bianco, dove la qualità del pezzo e l’aspetto estetico sono essenziali e dove l’acciaio inox domina sugli altri materiali, grandi numeri e processi sempre più integrati. Il percorso continua sui grandi dell’automotive dove le linee sono sempre più complesse, i processi integrati e i materiali impiegati si spostano sull’utilizzo di materiali alto resistenziali lavorati su servopresse o pezzi di alta precisione con alto spessore per i particolari fine blanking. I clienti ci chiedono di proporre la soluzione ottimale per realizzare il loro prodotto. Vogliono flessibilità, processi integrati ma utilizzabili in maniera smart per l’operatore e soluzioni che permettano loro di ottimizzare il loro processo e i costi del loro prodotto finale».
Diversi settori, diverse richieste
Anche nell’ambito della profilatura le performance con i nuovi materiali e la versatilità sono fattori chiave, come afferma Andrea Barazza di Stam. «Nel settore automotive la richiesta di utilizzare acciai a elevatissimo limite elastico, come gli acciai martensitici, è sempre più importante. Le linee di punzonatura e profilatura devono essere quindi in grado di processare questi materiali. Una sfida complessa, anche perché le caratteristiche del materiale possono variare lungo il coil. Nelle linee di profilatura per chassis di camion, i limiti elastici su spessori elevati (fino a 10 mm) sono saliti da 550 a 800 MPA, e comportano lo sviluppo di impianti sempre più performanti. La richiesta di maggior flessibilità è invece evidente nelle profilatrici a sezione variabile, che producono profili una volta producibili solo con grandi stampi, attrezzati a ogni cambio prodotto. Oggi questo non è più necessario, visto che con le nostre linee possiamo modificare le sagome dei profili, programmando la movimentazione delle teste di profilatura. Anche nel settore delle costruzioni o della logistica è richiesta molta flessibilità, sia nella parte di punzonatura (con punzonatrici flessibili a CN), sia nella parte di profilatura, dove macchine a spalle mobili, in più sezioni, consentono di variare la larghezza/lo spessore dei profili, senza attrezzamenti manuali».
Francesco Falghera di Iron pone l’accento sulla capacità di unire versatilità e personalizzazione delle linee. «Partendo dal fatto appunto che la nostra esperienza si focalizza su linee e macchinari da coil, i settori produttivi con i quali lavoriamo sono molteplici. Già parlando di linee di asservimento presse, gli ambiti applicativi sono numerosi e spaziano dall’automotive al settore del bianco, passando per l’illuminazione e così via. Dal momento che Iron negli ultimi 20 anni ha acquisito esperienza nella produzione di linee di punzonatura e pannellatura i settori si sono ampliati maggiormente abbracciando l’elettrico, la produzione di pannelli di vario genere come pannelli per ascensori, armadi metallici, porte blindate, distributori automatici solo per citare alcuni esempi. Le richieste sempre più frequenti da parte dei nostri clienti riguardano anzitutto una maggiore flessibilità della macchina, per potere sfruttare coil con un range di dimensioni più ampio, e sono richieste macchine sempre più customizzate, dove le linee prodotte integrano vari equipaggiamenti come per esempio unità di saldatura, piegatura, punzonatura, marchiatura in modo da completare il processo di lavorazione su un unico impianto. In altre parole, il cliente chiede sempre più linee presidiate da un unico operatore dove a tempi ciclo sempre più ridotti si riesca a produrre più pezzi finiti possibili, ovviamente partendo sempre da coil».
Materiali e innovazione
L’automotive è senza dubbio un settore cruciale anche nell’ambito della lavorazione lamiera da coil. Roberto Crespi di Saronni spiega in che modo l’azienda risponde alle nuove esigenze di tale settore. «Tra i più recenti cambiamenti nelle richieste dei nostri clienti, l’e-mobility è quella che maggiormente modifica i processi produttivi e di conseguenza i macchinari di nostra produzione. I veicoli devono essere sempre più leggeri e di conseguenza l’impiego di acciai alto resistenziali ma soprattutto di leghe di alluminio è diventato un must. Inoltre, una sempre maggiore attenzione all’aspetto superficiale di tali materiali durante e dopo il processo di stampaggio impone un trattamento particolare in tutte le fasi produttive. Saronni è stata in grado di rispondere a tale cambiamento grazie alla sua decennale esperienza nel settore e grazie a uno studio a livello prototipale in partnership con uno dei più importanti OEM del settore automotive condotto circa 6 anni fa. Quindi, sistemi di svolgitura coils, raddrizzatrici e spianatrici, alimentatori e tutte le parti a contatto con il materiale devono oggi essere concepiti per potere processare alluminio e acciaio alto resistenziale, spesso combinati nella stessa linea, ad alte velocità, con estrema precisione e con set up automatico».
Per Riccardo Borgonovo di Novastilmec l’evoluzione tecnologica non può prescindere dalla collaborazione con le università. «I nostri impianti permettono la realizzazione di prodotti che trovano applicazione nei più svariati ambiti industriali: siamo infatti presenti sia nel settore del centro di servizio, sia direttamente in catena automotive e più largamente in quei settori che necessitano di servizi speciali. Il fattore comune sono l’affidabilità e la riduzione di manutenzione, oltre che ovviamente la sicurezza. Automotive e B2C chiedono altissime qualità di prodotto, una richiesta che si è fatta molto più decisa rispetto agli anni passati. Negli ambiti aerospace e militare invece la tendenza è verso la lavorazione di materiali ad alta resistenza. Per soddisfare tali richieste sviluppiamo impianti performanti e dall’alto contenuto tecnologico grazie alla costante attività di ricerca, alla formazione del personale e alla collaborazione con università e centri di eccellenza del territorio sia per la ricerca di personale qualificato sia nello sviluppo di nuove soluzioni progettuali».
Ridurre scarti e sprechi
A chiudere il primo giro di interventi è Andrea Dallan di Dallan, che affronta il tema dell’efficienza produttiva. «In molti anni di lavoro nel settore della lamiera come direttore vendite ho ricevuto diverse richieste da parte dei nostri clienti e affrontato molte sfide. Le problematiche relative agli impianti di lavorazione della lamiera, dei prodotti e della gestione della produzione sono le più disparate, ma ho notato che c’è un fattore comune in tutti i casi che ho affrontato: il problema dell’efficienza. Molti imprenditori si sono rivolti alla Dallan consapevoli di volere migliorare la propria efficienza produttiva chiedendoci soluzioni innovative e all’avanguardia. Allo stesso tempo ho riscontrato che in molti altri casi non si ha la reale percezione di quanto l’efficienza sia davvero un problema e quindi molte aziende si ritrovano una gestione della produzione che se correttamente impostata può trarre enormi benefici in termini di produzione e flessibilità. In Dallan siamo da sempre attenti al tema dell’efficienza e da molti anni applichiamo i principi della Lean Production in tutti gli aspetti della nostra attività: dalle procedure interne alle tecnologie che sviluppiamo per le nostre macchine. Il risultato di questo approccio è stato lo sviluppo delle linee di produzione “Coil to”, tra i primi sistemi di produzione sul mercato completamente automatizzati che assicurano le massime prestazioni in termini di efficienza e produttività grazie alla riduzione degli scarti di materia prima fino al 16%, basso consumo energetico e senza l’ausilio di personale esperto».
Prodotti e settori
Terminata una panoramica dei trend legati ai vari settori applicativi, abbiamo chiesto ai costruttori coinvolti di illustrarci le tecnologie da loro sviluppate per rispondere alle richieste del mercato e la loro offerta in termini di servizi. Andrea Dallan di Dallan descrive le proprie soluzioni in funzione dei settori di interesse. «Da oltre quarant’anni in Dallan ci siamo specializzati nello sviluppo di sistemi di produzione per la lavorazione – a partire da coil – di lamiere sottili, profili estetici e materiali delicati. Riprendendo il discorso fatto prima, oggi il nostro catalogo prodotti offre diverse soluzioni esclusive ad alta efficienza per diversi campi di applicazione: i sistemi Coil to Window sono dedicati al settore della protezione solare, quindi alla produzione di teli di tapparelle e veneziane per esterni, a partire dal coil fino al prodotto finito e imballato, pronto per la spedizione e il montaggio. I sistemi Coil to Pack sono pensati per il settore delle costruzioni, come la produzione di profili metallici per cartongesso e accessori. Infine i sistemi Coil to Box si applicano alla produzione di profili t-bar per controsoffitti, anche in questo caso lavorati e imballati in un unico ciclo di lavorazione. Oltre a queste soluzioni sviluppiamo sistemi per profili speciali, punzonatrici e taglio laser efficienti a partire da coil. Dallan offre da sempre un servizio a 360° ai propri clienti, a partire dalla consulenza personalizzata sullo sviluppo del prodotto e del sistema di produzione fino alla costruzione della linea, la definizione del set-up ottimale, la formazione del personale e un servizio all’avanguardia di post vendita tramite sistemi di teleservice e interventi dei nostri tecnici specializzati in tutto il mondo».
Riccardo Borgonovo di Novastilmec differenzia le linee anche in funzione dei materiali lavorati. «Progettiamo, costruiamo e manteniamo impianti completi per il trattamento di bobine metalliche (coil). Il 95% del prodotto è Novastilmec. In particolare il nostro portafoglio comprende linee per la spianatura e il taglio di nastri di acciaio laminati a freddo e a caldo, zincati, preverniciati, inox laminati a freddo e a caldo, alluminio, materiale alto resistenziale, spinatura e taglio di Duplex, Domex e materiali ultra alto resistenziali. Per quanto riguarda poi il supporto al cliente, offriamo un servizio di progettazione e consulenza grazie all’ufficio tecnico composto da personale preparato ed esperto, che affianca il cliente nella ricerca delle soluzioni migliori per la riuscita di un progetto. Offriamo inoltre pacchetti e servizi di manutenzione e revamping programmati. Il tutto completa un eccellente servizio di consulenza gratuito pre/post vendita».
Portafoglio completo
L’evoluzione delle macchine riguarda anche temi quali l’autoapprendimento, come spiegato da Roberto Crespi di Saronni. «Siamo specializzati nello studio e realizzazione di linee di alimentazione presse e linee di taglio a lunghezza ad alte prestazioni e disponiamo di soluzioni per nastri con spessori da 0,1 a 18 mm e larghezze da 20 a 2.150 mm. Possiamo proporre sistemi completamente automatici sia nel cambio tipo che nell’autoapprendimento dei valori di raddrizzatura e spianatura, e disponiamo di un laboratorio in grado di eseguire test di raddrizzatura/spianatura per determinare con precisione il modello più adatto alle esigenze del cliente. Il sistema di raddrizzatura/spianatura computerizzato (A.S.A.) permette l’ottenimento dei risultati richiesti senza l’intervento dell’operatore ed è in grado di garantire il tasso di plasticizzazione del materiale ottimale per le operazioni di stampaggio successive. Disponiamo di un servizio pre e post vendita centralizzato, con branche in alcuni Paesi chiave nel mondo con addetti altamente specializzati in grado di svolgere tale servizio in lingua cliente, offriamo contratti di manutenzione preventiva ritagliati su misura per ogni cliente e dotiamo tutte le macchine di nostra costruzione di connessione remota. Possiamo inoltre, ove richiesto, fornire un servizio di General Contractor, integrando nelle forniture macchinari complementari realizzati da altri».
Oltre alla varietà dell’offerta, Francesco Falghera di Iron sottolinea l’importanza dell’affidabilità. «I macchinari da noi prodotti coprono una vasta gamma di materiali processabili, con coil di larghezza dai 200 mm fino a larghezza di 2000 mm per assecondare il più possibile le richieste del mercato. Parlando invece dei valori di portata, partiamo dalle 2 t di peso per arrivare a un massimo di 30 t. La competenza maturata negli anni e la flessibilità con la quale progettiamo i nostri impianti ci permettono di garantire al cliente la possibilità di processare spessori da un minimo di 0,5 mm fino a un massimo di 12 mm. Considerando la tipologia di macchine che realizziamo, l’affidabilità è senza ombra di dubbio un punto di partenza per garantire la continuità di funzionamento. Nel caso però venga richiesto un intervento, per un buon numero di macchine le parti di ricambio sono sempre a disposizione presso Iron e quindi facilmente reperibili dal cliente finale. Inoltre, forniamo un’assistenza post vendita in grado di soddisfare le richieste del cliente il più velocemente possibile sia su tutto il territorio nazionale che quello internazionale».
Il ruolo del service
Andrea Barazza di Stam affronta in modo approfondito il tema del service a 360°. «La nostra azienda progetta e costruisce linee di profilatura e linee di taglio (spianatura e taglio trasversale e linee di taglio in strisce). Ogni impianto è realizzato seguendo le esigenze specifiche del cliente. Nella fase di prevendita, la nostra attività è di consulenza tecnico-commerciale per definire insieme al cliente la tipologia e le caratteristiche dell’impianto più adatto, e compatibile con il budget di investimento. Si tratta di un processo alle volte molto lungo, dove si analizzano diverse soluzioni prima di arrivare alla definizione finale dell’impianto. In caso di acquisizione ordine, lo sviluppo del progetto è fatto tenendo sempre informato il cliente, e al termine della costruzione, per gli impianti di profilatura, si eseguono test di validazione del prodotto e delle prestazioni. Dopo l’installazione seguiamo il cliente in teleservice e con il nostro servizio di assistenza, con tecnici specializzati della casa madre. Vista la lunghissima durata dei nostri impianti, spesso operiamo degli ammodernamenti o inserimento di nuovi prodotti e processi in linee Stam esistenti, per mantenere sempre efficienti e aggiornati anche impianti forniti nel passato».
Per Veronica Just di Millutensil è essenziale potere integrare le linee con soluzioni e sistemi ad hoc. «“All around the press” è la proposta di Millutensil presentata nel catalogo green line completo di 90 pagine dove si può trovare un’ampia gamma di aspi raddrizzatrici, avanzatori, avanzatori turbo feeder per servo presse e zig-zag, microfeeder, cesoie. Il tutto può essere poi integrato da sistemi di lubrificazione con o senza aria sempre sviluppati dal nostro team di tecnici, e da soluzioni per evacuare gli sfridi e i pezzi di nostra progettazione e costruzione. Massima integrazione di tutte le tecnologie intorno alla pressa con dati richiamabili con un click e integrati di tutto il processo della coil line e dei componenti ausiliari. L’ottimizzazione dei tempi e il process management integrato in soluzione “smart” permettono l’ottimizzazione, il ritorno dell’investimento e grandi risparmi di tempo per i time di reset per i cambi di produzione. Millutensil compie 65 anni, ha un team di 80 persone. Le nostre tecnologie sono sviluppate dai nostri tecnici e dai nostri softwaristi all’interno dell’azienda. La dedizione e la passione ci distinguono e ci hanno permesso di sviluppare nuove proposte molto interessanti come i sistemi servo reel per materiali alto resistenziali, fine blanking, le nostre linee zig-zag che permettono un risparmio di materiale dall’8 al 10% e sono vendute in tutto il mondo nei più grandi Gruppi».
Offerta modulare
Lara Cecchi di Servopresse ribadisce l’importanza di abbinare competenze, tecnologia e servizio al cliente. «Siamo sul mercato da oltre 50 anni, e lo affrontiamo in qualità di costruttori. Questo ci ha permesso di acquisire esperienze sia nelle lavorazioni meccaniche sia nello sviluppo dei progetti. Abbiamo quindi pensato alle nostre linee di prodotti come a dei macromoduli da comporre in base alle richieste del cliente finale. Grazie a tale modularità del progetto possiamo realizzare linee per trattare coil con larghezze che variano da 400 a 2000 mm, e pesi compresi tra un minimo di 4 t e un massimo di 20 t. Tutto parte dalla nostra visita presso lo stabilimento del cliente, che ci permette di capire anzitutto del livello tecnologico di cui ha bisogno per completare la propria attività, e poi di evidenziare particolari esigenze come per esempio quella della compattezza dell’impianto per il poco spazio che ha a disposizione nel proprio capannone. Da questo incontro ha poi inizio la definizione del progetto, per il quale all’occorrenza facciamo da capocommessa soprattutto nel caso di linee particolari quali linee di taglio dischi o di quadrottatura, completando il nostro impianto con cesoie, punzonatrici o macchine di taglio laser fibra come nel caso della Servolaser recentemente presentata. La capacità di comprendere le esatte necessità applicative e rispondere con un impianto pensato ad hoc è un elemento apprezzato dal mercato, con la maggior parte dei clienti che torna da noi dopo l’acquisto del primo impianto, riconoscendo i vantaggi ottenuti grazie alla prima soluzione installata».
Condividi l'articolo
Scegli su quale Social Network vuoi condividere