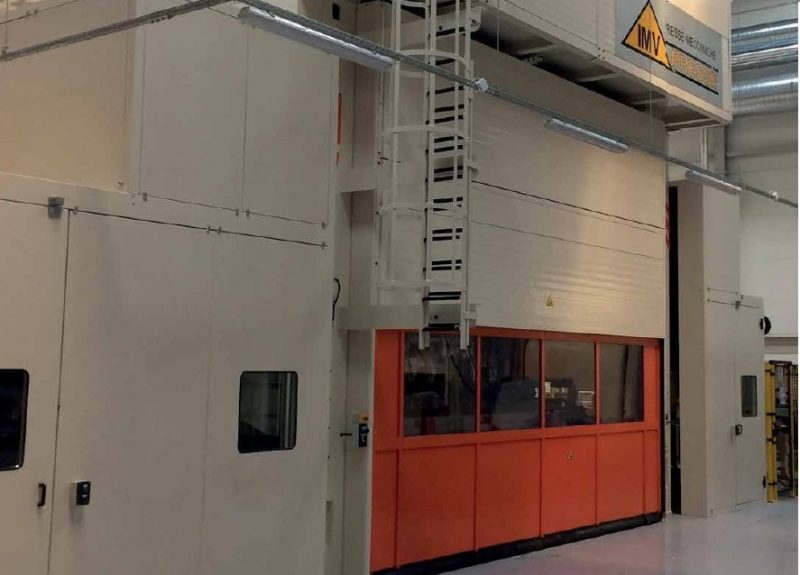
Competenze e innovazione tecnologica sono la chiave del successo di I.M.V. Presse, che da oltre ottant’anni progetta e realizza internamente presse apprezzate in tutto il mondo. In tempi recenti, alle linee con rallentamento meccanico e servo si è aggiunta la famiglia Servokers.
di Davide Davò
Tecnologia e supporto al cliente sono i due cardini attorno ai quali ruota il rapporto cliente-fornitore. Il solo contenuto tecnologico infatti, per quanto possa essere innovativo e di alto livello, non è sufficiente per consentire a un utilizzatore finale di sfruttare il pieno potenziale di una macchina utensile. Le profonde competenze legate all’intero sistema produttivo e non solamente alla propria soluzione, la capacità di comprendere l’obiettivo del cliente e di affiancarlo nell’individuare le tecnologie più idonee per raggiungerlo, la capacità di trasferire all’utilizzatore finale le competenze necessarie per sfruttare il pieno potenziale di una macchina sono tre aspetti indispensabili per instaurare una partnership vincente, assicurando al cliente un reale vantaggio competitivo. Di questo scenario è ben consapevole I.M.V. Presse, realtà di Villasanta (MB) fondata nel 1934 e specializzata nella costruzione di presse che trovano applicazione in ambiti produttivi nei quali le sfide tecnologiche di alto livello sono all’ordine del giorno.
Offerta completa
«Nel nostro settore la macchina standard nel senso stretto del termine non esiste», esordisce Lorenzo Galli, CEO di I.M.V. Presse. «In particolare, quando si parla di taglie medio-grandi le presse possono differenziarsi tra loro per una grande varietà di elementi, che vanno da quelli più evidenti come le dimensioni o la tipologia di azionamento per scendere fino a dettagli legati per esempio a specifiche funzionalità del controllo o a sistemi accessori installati sull’impianto, che lo rendono un esemplare pressoché unico. I.M.V. Presse, grazie alla struttura di azienda a carattere familiare abbinata a una gestione dell’attività di stampo sempre più manageriale, ha il giusto mix di flessibilità e organizzazione che le permette di realizzare soluzioni cucite su misura partendo da una base di prodotto consolidata, che viene completata con le più evolute tecnologie e opportunamente configurata sfruttando le profonde esperienze che abbiamo maturato nel corso di diversi decenni». Una missione, quella di soddisfare le più svariate esigenze applicative, che la realtà lombarda porta a termine potendo contare su un portafoglio di soluzioni decisamente ampio, con presse che vanno dalle 100 alle 3500 t di forza e piani che possono raggiungere i 7 m. Allo stesso modo anche velocità, energie in gioco e tipologie di trasmissione vengono selezionate in base alle necessità del cliente, con tipologie di rallentamento che possono essere meccaniche oppure tramite servomotore. «Tale varietà è frutto della nostra strategia di mantenere al nostro interno il know how e di sfruttare l’esperienza acquisita durante un progetto per adattarla in altri ambiti, qualora le soluzioni tradizionali non ci permettano di raggiungere determinati obiettivi», precisa Galli. «Con questo approccio siamo riusciti a consolidare la nostra presenza anche oltre i confini nazionali, al punto da rendere l’export una vera e propria vocazione. Circa l’80% dei nostri progetti infatti è destinato a clienti esteri».
Controllo totale
Dimostrazione tangibile della volontà di I.M.V. Presse di mantenere le competenze al proprio interno è la decisione di seguire internamente la totalità del processo produttivo, a eccezione delle sole operazioni di lavorazione degli ingranaggi e di saldatura della struttura, quest’ultima esternalizzata per motivazioni logistiche. La lavorazione degli ingranaggi invece è affidata a realtà specializzate con le quali il costruttore definisce geometrie, trattamenti termici e livelli di finitura superficiale dei componenti, che vengono comunque controllati al loro ingresso nella sede di Villasanta. Controlli che avvengono anche durante le varie fasi della produzione, in modo da intercettare eventuali non conformità e intervenire il prima possibile evitando che queste incidano sulle operazioni successive, sulle performance della pressa e sulle tempistiche di consegna. Terminato il ciclo delle lavorazioni meccaniche viene eseguito un ulteriore controllo finale prima dell’assemblaggio e del collaudo. Tutte le presse I.M.V. infatti prima di essere spedite vengono testate sia per certificare che l’impianto funzioni senza alcuna criticità, sia per garantire al cliente una pressa perfettamente operativa e produttiva fin dal primo pezzo stampato. «In tempi recenti il nostro ruolo si sta trasformando in modo sempre più frequente da fornitori di una macchina a capocommessa per progetti che prevedono soluzioni di automazione più o meno complesse», aggiunge ancora Galli. «La configurazione tipica prevede la nostra pressa alimentata da una linea coil, ma abbiamo sviluppato anche soluzioni che prevedevano l’inserimento di un robot antropomorfo. Per tali esigenze possiamo contare su una rete di partner affidabili e di primissima fascia, con i quali dialoghiamo per individuare la migliore soluzione in base alla situazione produttiva che stiamo analizzando, e che verrà integrata a livello meccanico ed elettronico direttamente dai nostri tecnici».
La giusta tecnologia
Linee di produzione complete, dunque, in cui il cuore tecnologico sono le presse realizzate da I.M.V. Presse. «Come detto, siamo fornitori sia di macchine con rallentamento meccanico sia di quelle con tecnologia servo, e questo rappresenta per noi un duplice vantaggio», spiega Galli. «Anzitutto possiamo studiare l’applicazione illustrando ai clienti pregi e difetti di entrambe le tecnologie, permettendogli di decidere senza nessuna forzatura da parte nostra verso l’una o verso l’altra tipologia di impianto. Le presse servo infatti presentano numerosi vantaggi se paragonate alle presse eccentriche tradizionali, ma a mio parere è più corretto fare un confronto con macchine a rallentamento meccanico come quelle a ginocchiere modificate, per esempio. In questa comparazione, il vantaggio della soluzione servo in termini di possibilità di programmazione della velocità del colpo rimane netto, ma a fronte di costi di acquisto e gestione nettamente superiori. Per offrire ai clienti una terza strada da percorrere, abbiamo lanciato di recente la linea Servokers, particolarmente adatta al settore automotive e dell’elettrodomestico per la sua capacità di abbinare produttività, flessibilità nella programmazione e costi d’esercizio contenuti».
Obiettivo: efficienza
Il punto chiave attorno al quale è nato il progetto Servokers è l’efficienza energetica della pressa. La tecnologia con servomotori infatti diventa sempre più energivora al crescere dell’energia di cui la pressa deve disporre per deformare il materiale, poiché aumenta anche la taglia di motori, azionamenti e buffer installati. Per ovviare a questa situazione, I.M.V. Presse ha sviluppato un sistema brevettato che permette alla macchina di raggiungere le stesse prestazioni di una tradizionale servopressa, con la medesima facilità di programmazione dei movimenti, ma adottando motori, buffer e azionamenti di taglia inferiore. Più nel dettaglio, la soluzione ideata dal costruttore di Villasanta sfrutta due buffer, uno meccanico e uno elettronico, che operano su sistemi differenti pur essendo integrati tra loro. Durante la fase passiva del ciclo, ovvero quando la pressa non sta deformando la lamiera, il buffer meccanico ha il compito di immagazzinare l’energia cinetica. Il buffer elettronico invece accumula energia durante le fasi di accostamento dello stampo e di stampaggio, restituendola al sistema nelle fasi di apertura stampo e nella gestione della velocità del ciclo. Un sistema combinato che consente di dimezzare la potenza installata rispetto a una tradizionale pressa servo di pari prestazioni. «Tutta questa tecnologia risulta essere facilmente fruibile per l’operatore grazie a un’interfaccia estremamente intuitiva che riporta le stesse funzionalità di qualsiasi altra macchina, con la sola aggiunta delle pagine per la gestione della velocità», conclude Galli. «L’operatore indica la velocità di lavoro, ovvero la velocità con la quale viene deformata la lamiera una volta chiuso lo stampo, e le velocità di apertura e chiusura della slitta. A questo punto il software genera un ciclo, all’interno del quale l’operatore può intervenire liberamente per ottimizzare le tempistiche della fase di deformazione, e sarà poi il software ad adattare di conseguenza accelerazioni e movimenti della macchina nelle altre fasi».
Condividi l'articolo
Scegli su quale Social Network vuoi condividere