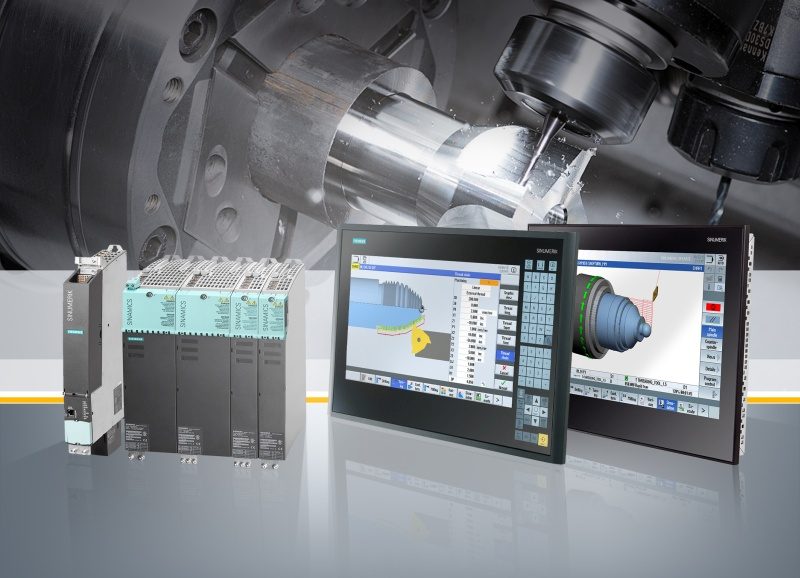
Siemens Italia con il motto “Digitalization in Machine Tool Manufacturing” ha messo a punto un interessante programma con cui mostrare le più recenti soluzioni per la gestione completa dei processi produttivi in accordo con i dettami dell’Industria 4.0
Illustrare ai costruttori di macchine utensili e agli utilizzatori finali l’ampia offerta di soluzioni integrate e guidarli lungo un percorso che si snoda su varie tappe, partendo dalla progettazione e attrezzaggio macchine e passando per le lavorazioni tecnologiche sino ai servizi post vendita, seguendo tutte quelle fasi produttive che portano alla realizzazione di prodotti personalizzabili di alta qualità. Questo il posizionamento di Siemens Italia per l’edizione 2018 di MecSpe, i saloni della Meccanica Specializzata in programma dal 22 al 24 marzo alle Fiere di Parma. Un percorso iniziato con la presentazione delle innovazioni tecnologiche in occasione dell’ultima edizione della EMO di Hannover, cui hanno fatto seguito quattro workshop in altrettante sedi organizzati in collaborazione con Tecnologie Meccaniche, dedicati ai costruttori di macchine.
Siemens e l’Industria 4.0
Presente in Italia sin dal lontano 1899, Siemens è oggi una delle maggiori realtà industriali del nostro Paese con centri di competenza su software industriale e mobilità elettrica, un polo tecnologico applicativo (TAC) e due stabilimenti produttivi, e con un fatturato di circa 2 miliardi di euro nell’esercizio fiscale 2017. In occasione dell’edizione 2018 dei saloni a Parma, Siemens Italia prosegue lungo il cammino di promozione del proprio portfolio prodotti e soluzioni per la macchina utensile, con un unico filo conduttore: il flusso di processo che una PMI dovrebbe avere all’interno della propria officina per implementare il processo di digitalizzazione in ottica Industria 4.0 nel mondo delle lavorazioni meccaniche, così da aumentare la propria competitività nel mercato globale. «A partire dalla postazione dei software di progettazione con la soluzione PLM NX CAD/CAM completa, con simulazioni di macchine orientate sia alla robotica che all’additive manufacturing alla postazione che permette di analizzare la moltitudine di funzionalità della suite Sinumerik Integrate e della soluzione Sinutrain per la preparazione macchina e l’attrezzaggio, per poi passare alle innovazioni tecnologiche nel la produzione in macchina dove i visitatori toccano con mano l’effettiva lavorazione di due pezzi nel centro di lavoro a cinque assi Raffaello, di Rema Control, e nel centro di tornitura orizzontale modello Puma, di Doosan, commercializzato da Overmach»: così Luigi Ruggieri, Business Development Manager Machine Tool Systems di Siemens Italia, descrive lo stand Siemens. Il primo centro di lavoro, equipaggiato con un CNC Sinumerik 840D sl Sinumerik Operate V4.8 SP2, pannello touch da 19”, Top Surface e Friction Compensation, fornisce una dimostrazione tangibile dell’incremento della produttività e della qualità delle superfici. Il secondo centro di tornitura invece è dotato di un pannello touch screen da 15”, CNC Sinumerik 828D SL, Sinumerik Operate V4.7 e ShopTurn per la produzione di pezzi di precisione in diversi settori industriali. Obiettivo di entrambe le macchine è quello di dimostrare le enormi potenzialità della realtà aumentata applicata alle macchine utensili, disponibile e personalizzabile in base alle singole necessità e senza grossi impegni finanziari.
Ampio spazio anche alle postazioni di usability e di sicurezza di macchina, caratteristiche obbligatorie del Piano governativo Industria 4.0, così come la postazione automazione a 360 gradi dove approfondire le collaborazioni con costruttori di robotica. «A partire da quella con Kuka Roboter GmbH, iniziata parecchi anni fa – continua Ruggieri – dalla quale è nata l’interfaccia intelligente Sinumerik Integrate Run MyRobot per l’automazione integrata di macchine utensili e robot, facendo sì che entrambi possano essere programmati, gestiti e monitorati tramite un unico controllo numerico, con l’interfaccia utente intuitiva del CNC Sinumerik Operate semplificando ulteriormente la gestione da parte dell’ operatore della robotica nelle celle di lavorazione».
Proseguendo con la nuova collaborazione con Comau, dalla quale è nata Sinumerik Integrate Run MyRobot/DirectControl, una soluzione che garantisce una completa integrazione della cinematica del robot nel CNC e viene offerta in maniera nativa dal Sinumerik 840D SL. «Obiettivo della soluzione è l’integrazione di un robot antropomorfo attraverso il collegamento al solo cavo Profinet: tutto il dialogo tra CNC e robot è già residente nel controllo numerico, la parte asservimenti e motori rimane quella del robot stesso, mentre tutta la parte di comando risiede nel CNC Sinumerik», conclude Ruggieri. Postazione successiva alla lavorazione in macchina e all’automazione di cella non poteva che essere il controllo della produzione e della manutenzione, con sistemi intelligenti e innovativi per la gestione dell’efficienza dell’officina, il monitoraggio della produzione, una soluzione nativa CNC per la manutenzione predittiva oltre che Mindsphere, il sistema operativo aperto per l’IoT basato su cloud di Siemens.
Il percorso si conclude con temi molto importanti per il lavoro quotidiano degli utilizzatori di macchine, i servizi a loro dedicati, anche quelli digitali, offerti dal customer service di Siemens, le soluzioni di retrofit con incremento della produttività della macchina, contratti personalizzati di manutenzione, adeguamento macchine al Piano Industria 4.0, assistenza e riparazione elettromandrini Weiss, temi molti importanti per gli utilizzatori di macchine. Numerose infine le presentazioni che si sono susseguite durante le giornate di fiera presso lo stand Siemens, con approfondimenti e dimostrazioni “live” di tematiche attuali. «È importante, a questo punto, sottolineare il fatto che tutte le soluzioni presentate in fiera sono a disposizione delle PMI e implementabili anche gradualmente; è infatti possibile scegliere quello che più si addice a un particolare processo produttivo e implementando “step by step” altre soluzioni, creando così nel tempo un percorso totalmente personalizzato», interviene Paolo Trezzi, Head of Business Development del Business Segment Machine Tool Systems di Siemens Italia. «Ospiti infatti del nostro stand due macchine utensili: la prima di un costruttore italiano e la seconda importata. L’obiettivo è mostrare come, indipendentemente dal fatto che nel nostro Paese sono presenti centri di lavoro prodotti in Italia (che, lo ricordiamo, è il secondo mercato mondiale dopo la Germania) e altri d’importazione, i nostri sistemi si integrano perfettamente all’interno di ogni processo produttivo, mostrando tutto il loro potenziale».
Industria 4.0 e l’affidabilità operativa
Il centro di lavoro a 5 assi Raffaello R5A.6, progettato e realizzato da Rema Control, vanta l’uso delle più recenti tecnologie di progettazione, assieme a componentistica di assoluta qualità per un’affidabilità operativa senza compromessi. Presente sul mercato da una decina d’anni, con continui sviluppi e aggiornamenti tali da renderlo sempre all’avanguardia, il centro di lavoro si distingue per l’assoluta precisione di lavorazione che può offrire unita all’ergonomia della postazione di lavoro, attentamente studiata per garantire grande comodità in tutte le fasi di utilizzo. Caratteristica distintiva di Rema Control è la grande flessibilità nella personalizzazione dei propri modelli in base alle esigenze del singolo cliente che viene applicata anche all’R5A.6, che può così contare su una vasta scelta di elettromandrini (ISO 40 o HSK 63, velocità di rotazione fino a 24mila giri/minuto, potenze fino a 38 kW e coppie fino a 268 Nm), un magazzino utensili espandibile e un ampio assortimento di opzioni a disposizione, dalle più semplici fino a linee automatiche complete e prodotti “chiavi in mano”.
Industria 4.0 e un esempio di potenza
Doosan Machine Tools ha lanciato i centri di tornitura Puma 2100Y-II e 2600YII con asse Y, ideali per la produzione di pezzi di precisione in diversi settori tra cui l’industria automobilistica, elettronica, degli elettrodomestici, dell’energia e delle lavorazioni meccaniche in generale. Dotati di autocentranti del diametro di 210/255/315 mm possono lavorare con grande precisione pezzi dalle forme complesse quali valvole, alberi, ingranaggi, flange, alloggiamenti e raccordi, con un diametro fino a 376 millimetri e una lunghezza massima fino a 1280 mm in un solo piazzamento. Dotata di basamento ad alta rigidità con ampie guide piane di scorrimento su tutti gli assi e di un mandrino da 22 kW, la nuova serie di torni offre un’eccellente potenza e un’ottima capacità di lavorazione con forti asportazioni di truciolo. Inoltre, il design migliorato dell’alloggiamento del mandrino e delle viti a ricircolo di sfere, unitamente alla struttura fortemente smorzata, consente di contenere al minimo eventuali imprecisioni che possono verificarsi durante l’assemblaggio della macchina, garantendo pertanto una qualità di lavorazione superiore anche durante la produzione a ciclo continuativo e non presidiata. In termini di programmazione del controller, l’esclusiva funzione di ottimizzazione del ciclo di lavorazione di Doosan riduce i tempi morti fino al 25% e il tempo ciclo totale fino a un massimo del 6% rispetto alla precedente generazione.
Condividi l'articolo
Scegli su quale Social Network vuoi condividere