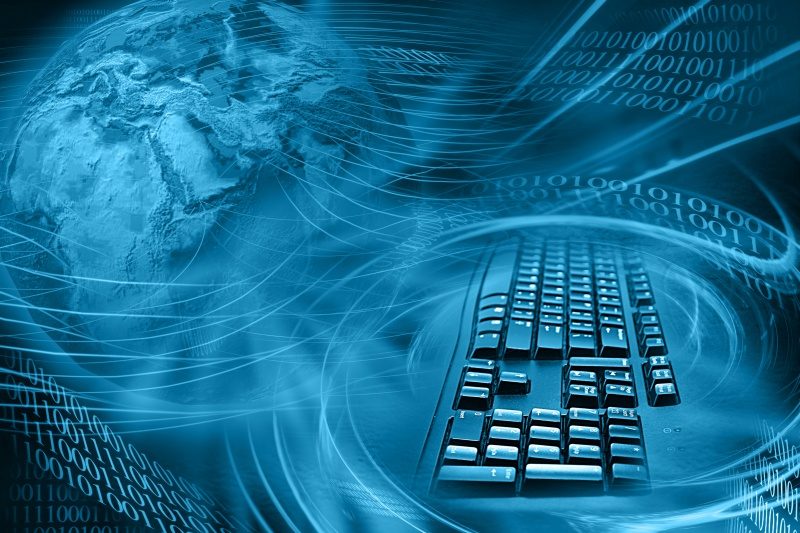
La parola ad alcuni dei costruttori di CNC presenti in Italia per scoprirne l'evoluzione tecnologica.
Il controllo numerico (CNC), come tutti sappiamo, è stato l’artefice di una delle più importanti trasformazioni tecnologiche, produttive, operative, organizzative, nel settore delle lavorazioni meccaniche. Durante la sua “vita” non è stato certamente fermo ma ha subito continue evoluzioni e trasformazioni che l’anno portato ad essere lo strumento indispensabile ed insostituibile su una qualsiasi macchina utensile.
Questo ruolo fondamentale ne ha fatto sviluppare il mercato un po’ in tutto il mondo dove c’è una lavorazione meccanica. Nelle officine ci sono certamente ancora installate macchine utensili senza il controllo numerico, ma una cosa è certa oggi qualsiasi azienda voglia inserire una macchina utensile nel proprio stabilimento sarà certamente a controllo numerico.
Ma a che punto siamo oggi in ambito di tecnologia quando parliamo di controllo numerico.
In merito Tecnologie Meccaniche ha voluto incontrare alcuni tra i principali produttori di controlli numerici presenti sul territorio italiano e insieme a loro cercare di fare una fotografia di un prodotto che è diventato una vera e propria macchina dentro la macchina.
Fanuc, serve un CNC all’avanguardia
A rompere il ghiaccio sull’argomento Pietro Squarzon di Fanuc. «I costruttori di macchine utensili richiedono un prodotto CNC a prezzi competitivi e tecnologicamente all’avanguardia, attraverso il quale affrontare con successo i mercati di tutto il mondo. Fanuc, un punto di riferimento mondiale nel settore CNC con più di 800 ingegneri impegnati nella ricerca e sviluppo e 6.500 persone dislocate in tutto il mondo, è in grado di rispondere al meglio alle esigenze dei costruttori di macchine utensili non solo in termini di affidabilità, flessibilità e facilità d’uso del prodotto ma anche in termini di supporto allo sviluppo delle applicazioni e successivamente in termini di assistenza worldwide; tant’è che uno degli slogan Fanuc, ‘Service first’, sintetizza la mission aziendale orientata a garantire un servizio di assistenza ai clienti finali di estrema qualità. Inoltre, oggi più che mai gli utilizzatori sono alle prese con mercati globali dove le sfide di competitività si giocano ai massimi livelli, trovandosi ad affrontare la concorrenza di Paesi con costi produttivi diversi. L’affidabilità di prodotto, il total cost of ownership (TCO) insieme ad altri indici come KPI, OEE, TEEP sono elementi chiave dei prodotti e delle macchine equipaggiate con CNC Fanuc. I CNC Fanuc di ultima generazione equipaggiati con la semplice e innovativa interfaccia iHMI garantiscono la massima facilità d’uso, mentre l’integrazione con i nostri robot è in grado di assicurare la massima produttività degli impianti permettendo di essere più competitivi che mai riducendo i costi di produzione del prodotto finito. Riguardo a Industria 4.0 Fanuc nelle sue sedi produttive mette in atto da tempo i criteri di produzione Industria 4.0 utilizzando più di 2.000 robot per la produzione di CNC, azionamenti, motori e robot stessi, monitorando e analizzando i dati produttivi al fine di assicurare i massimi livelli di produttività. Internet of Things costituisce il criterio in base al quale è necessario ripensare la fabbrica in modo da garantirsi la competitività necessaria in uno scenario produttivo sempre più complesso. Fanuc dispone da tempo di soluzioni Industria 4.0 che assicurano un importante vantaggio ai clienti come MT-Linki (che attiva il collegamento in rete di macchine e dispositivi, anche di terze parti, per scopi di manutenzione preventiva). La nuova piattaforma Fanuc Field System (Fanuc Intelligent Edge Link & Drive System), in grado di analizzare i Big Data acquisiti da più CNC, robot, macchine eccetera permette di implementare moduli applicativi dedicati a manutenzione preventiva, analisi dati produttivi e altro. In Field sono anche implementabili moduli di AI (Artifical Intelligence) che forniscono ai clienti la possibilità di personalizzare la piattaforma al più elevato livello tecnologico oggi disponibile nel mercato. MT-Linki e Field sono le soluzioni che Fanuc propone ai clienti finali per raggiungere la maggiore competitività possibile nei loro impianti di produzione».
Mitsubishi electric, il CNC è sempre più intelligente
Interviene Paolo Soroldoni della Mitsubishi Electric che sottolinea quanto «la crisi ha portato a ripensare anche all’approccio alla produzione, con un passaggio da un approccio quasi artigianale a uno che potremmo a tutti gli effetti dire industriale. In questo passaggio è notevolmente cresciuta l’attenzione destinata ad alcuni aspetti come la flessibilità, il controllo dei costi di produzione e la possibilità di incrementare l’efficienza riducendo i tempi di fermo impianto. Mitsubishi Electric permette di fare fronte a queste esigenze focalizzando l’attenzione su sistemi di produzione connessi e sistemi di controllo intelligenti. Una connettività aumentata contribuisce ad apportare miglioramenti nell’ottimizzazione della produzione, monitoraggio, servizi da remoto e manutenzione predittiva. Il concetto di e-F@ctory sviluppato da Mitsubishi Electric offre una struttura pratica per la fornitura di tali soluzioni, rendendo possibile il processo di trasformazione digitale a livello di produzione. I CNC della serie M8 garantiscono un controllo rapido e preciso delle macchine utensili e grazie alle loro potenti funzionalità monitorano e riducono i tempi e i costi di produzione. Inoltre, grazie alla connettività Ethernet integrata di serie permettono di interfacciarsi facilmente col mondo esterno. Per gli utenti inoltre è possibile implementare sistemi di controllo in grado di ottimizzare le prestazioni delle singole macchine e il rendimento dell’intero stabilimento. Ma non sono solo le caratteristiche tecniche dei nostri controlli a fare la differenza. La riduzione dei tempi di fermo macchina è un obiettivo fondamentale sia per i costruttori di macchina sia per gli utilizzatori. Il nostro service gioca un ruolo fondamentale per permettere di centrare questo target. Con questa consapevolezza, noi di Mitsubishi Electric abbiamo deciso di fornire un servizio di assistenza tecnica non basato su di un ticketing ma su un contatto diretto e immediato non appena nasce l’esigenza tra utente e uno staff qualificato e competente, in grado di fornire supporto via telefono o e-mail. Per esempio, quando un cliente chiama il nostro numero dedicato service, entra immediatamente in contatto con un tecnico esperto in grado di supportarlo. Il risultato è un enorme abbattimento dei tempi di attesa e un più elevato grado di soddisfazione del cliente. Inoltre, tutti i ricambi sono disponibili presso i nostri magazzini, per garantire una consegna rapida su tutto il territorio. In questo modo il cliente, sia esso costruttore, importatore o utilizzatore di macchine, può contare davvero su di un partner pronto a supportarlo in modo rapido ed efficace».
Heidenhain, più qualità e flessibilità dai CNC
Oltre ad accuratezza e qualità della lavorazione è in aumento la richiesta di flessibilità, alla quale Heidenhain risponde con soluzioni a hoc come sottolinea Andrea Bianchi. «La produzione italiana di macchine utensili è in maggiore misura orientata su prodotti tecnologicamente evo luti e spesso con un elevato grado di personalizzazione. Per questo motivo la richiesta prevalente sia da parte degli OEM che degli utilizzatori finali è indirizzata verso tecnologie in grado di migliorare l’accuratezza e la qualità della lavorazione, a cui negli ultimi anni si è aggiunta una maggiore necessità di flessibilità, cioè la possibilità di potere lavorare pezzi di qualità in piccoli lotti. Per dare risposta a queste esigenze, Heidenhain ha sviluppato all’interno del TNC 640 due pacchetti software specifici denominati “Dynamic Efficiency” e “Dynamic Precision”, in grado di esaltare le prestazioni della macchina utensile abbattendo i tempi di produzione e migliorando nel contempo la qualità e l’accuratezza superficiale delle lavorazioni. Sul fronte Industria 4.0 TNC 640, il controllo numerico high-end Heidenhain, offre le aperture necessarie ai software aziendali di alto livello per la gestione digitale delle commesse. Per il monitoraggio delle macchine e delle lavorazioni, Heidenhain ha sviluppato un software specifico “user friendly” denominato StateMonitor, integrato nel pacchetto di funzioni “Connected Machining”, che è in grado di mostrare in tempo reale su pc, tablet o smartphone l’andamento della produzione e segnalare attraverso SMS oppure e-mail lo stato della produzione e/o eventuali messaggi diagnostici».
Siemens, la digitalizzazione al centro
Secondo Paolo Trezzi di Siemens l’innovazione passa oggi attraverso la digitalizzazione. «L’innovazione tecnologica per la macchina utensile è senza dubbio legata alla digitalizzazione e all’Industria 4.0. I costruttori di macchine sono sempre più attenti all’adozione di soluzioni software innovative per incrementare la loro competitività. Esistono già vari casi di successo, anche tra costruttori italiani, di applicazioni di Digital Twin per la progettazione e messa in servizio virtuale della macchina; nei prossimi mesi vedremo una crescita importante nell’adozione di queste tecnologie perché i vantaggi dell’investimento sono ripagati in breve tempo da maggiore produttività, riduzione del time to market ed eliminazione dei rischi di progetto. Notevole attenzione è rivolta verso le soluzioni cloud based per l’analisi dei dati con particolare interesse per le acquisizioni di dati ad alta frequenza e preelaborazione dei dati in macchine, il cosiddetto edge computing; i costruttori sono consapevoli che per ottenere informazioni di valore dalle loro macchine serve una soluzione integrata tra le componenti di automazione e le tecniche di data analytics in cloud. La parola chiave dell’innovazione è quindi integrazione tra sistemi fisici (macchine, automazione, robot) e sistemi digitali (analisi dati, simulazione) sia per i costruttori di macchine sia per i clienti finali. I clienti finali stanno sperimentando e riscontrando il maggiore valore dell’integrazione rispetto alla semplice connessione. Incoraggiate dai piani governativi, le imprese che lavorano con macchine utensili stanno facendo investimenti in nuove soluzioni software per l’ottimizzazione della produzione. La connessione di sistemi diversi, che non sono stati progettati per lavorare in modo integrato, comporta costi elevati e rischi di progetto e non permette di evolvere verso soluzioni realmente vantaggiose in termini di produttività e competitività. Per questo i clienti saranno sempre orientati verso soluzioni integrate all’origine e si affideranno a fornitori capaci di proporre soluzioni complete di controllo, robotica, software, sicurezza informatica e consulenza. Siemens risponde a queste esigenze con un ampio portfolio di prodotti e soluzioni integrate specifiche per la macchina utensile, unite a soluzioni consolidate per l’Information Technology e la Cybersecurity e all’esperienza dei suoi consulenti e tecnici specializzati. Già nel 2015, in occasione della EMO e con il motto “On the way to Industrie 4.0 – Digitalization in Machine Tool Manufacturing”, Siemens ha guidato la trasformazione digitale della macchina utensile e anticipato le richieste del mercato in tema di innovazione. Oggi il percorso continua con maggiore enfasi nel mondo cloud e Industrial IoT (con il sistema operativo aperto per l’IoT basato su cloud Mindsphere) oltre che con soluzioni dedicate ai nuovi trend tecnologici dell’Additive Manufacturing e robotica collaborativa».
D.Electron, il CNC e l’Industria 4.0
Quando si parla di tecnologia, secondo Andrea Becattini della D.Electron «le richieste della clientela sono principalmente tre: riduzione dei costi, aumento delle prestazioni e affidabilità del prodotto. Questo mix chiaramente è diverso a seconda del settore al quale ci rivolgiamo. Inoltre, con Industria 4.0 le richieste degli utilizzatori e quindi l’evoluzione tecnologica sono finalizzate al dialogo tra le macchine, tra le macchine e il sistema gestionale, tra le macchine e i sistemi di monitoraggio delle condizioni di lavoro. In questo ambito stiamo realizzando un progetto con l’Università di Firenze finalizzato al monitoraggio in tempo reale e all’acquisizione dei dati necessari per effettuare una diagnosi predittiva della macchina e ottenere notevoli vantaggi a livello di manutenzione, riduzione dei tempi morti e quindi produttività della macchina. Mettiamo inoltre a disposizione un semplice protocollo di comunicazione denominato EPS (Easy Protocol Server): in pratica è un server, disponibile su tutti i CNC Z32 recenti, che consente lo scambio di dati e/o di comandi con software esterni attraverso un dialogo basato su stringhe ASCII-coded. Tramite questo protocollo, infatti, è per esempio possibile ricavare lo stato del CNC, quello dell’esecuzione di un part program e numerosi altri dati, potendo inoltre comandare da remoto l’esecuzione di uno specifico programma. Sempre nell’ottica di una produzione 4.0 abbiamo dotato i nostri controlli di un software DCM (Data Collector Manager) che può essere installato su un qualsiasi pc collegato in rete con tutte le macchine equipaggiate dallo Z32 permettendo di raccogliere, da queste, svariate informazioni utilizzabili dai gestionali di officina o collezionabili sul web, generando output su file o web cloud. Il controller è infine in grado di inviare, su richiesta del part program o del PLC, delle e-mail a un centinaio d’in dirizzi diversi per comunicare quanto ritenuto necessario dal cliente finale o dal costruttore della macchina. Tengo a evidenziare, inoltre, l’innovativa funzione DSF, Dynamic Stabilizer Filter, installata all’interno di tutti i nostri controlli dotati degli azionamenti digitali, in grado di dimezzare gli errori di inseguimento degli assi, dunque raddoppiare la loro precisione: con questa nuova funzionalità, altamente dinamica e autoadattante all’operatività degli impianti, si possono raggiungere qualità di lavorazione fino a ieri impossibili, quindi un nuovo salto tecnologico nella tecnologia del controllo numerico Made in Italy. Non ultimo abbiamo pensato molto al comfort operativo che si traduce in maggiore efficienza per gli operatori macchina, ed è proprio ai giovani operatori di macchina che D.Electron ha voluto rivolgersi introducendo sul mercato la nuova console OST22 per lo storico CN Z32, dotata di controlli touch screen del tutto simili a quelli presenti sugli smartphone, cercando di rendere più familiare e amichevole il nostro CNC».
Fagor, puntiamo su semplicità e prestazioni
Semplicità e alte prestazioni sono le strade sulle quali si sta muovendo Fagor, come ci spiega Alberto Fasana. «Da sempre i prodotti di Fagor Automation si contraddistinguono per essere quelli che meglio uniscono semplicità e prestazioni, una filosofia che ci contraddistingue rispetto ai competitors e che si concretizza in numerosi esempi. Vediamo che questa strategia risponde alle esigenze dei nostri clienti: tutti vogliono la tecnologia più moderna, la massima velocità, la massima precisione ma tutti vogliono anche semplicità e immediatezza d’uso, per rendere facile il dominio di questa tecnologia. Prendiamo alcuni esempi. Nei sistemi di misura, i nuovi encoder serie 2 offrono un rinnovamento di gamma volto a facilitare montaggio e manutenzione, con testina di lettura a doppio connettore e doppia presa di pressurizzazione, ma ovviamente parliamo sempre di prodotti che sono al top del mercato per precisione e prestazioni (Fagor è l’unica azienda al mondo in grado di fornire righe assolute fino anche a 50 metri). Nel CNC, la gamma Fagor offre prodotti per tornitura, laser e fresatura. Si tratta di un enorme vantaggio per una officina, gli operatori possono spostarsi su macchine diverse ma ritrovando lo stesso CNC. Altri esempi arrivano dalle funzionalità software, pensiamo alla programmazione ProGTL3. Un linguaggio molto semplice, che con sole 5 funzioni (G810, G811, G813, G820, G812) consente di creare profili di qualsiasi complessità, che possono essere combinati in macro per realizzare superfici 3D (G8736, G8725 eccetera) e tantissime altre fun zionalità per lo stampista. Il tutto con un editor 2D e 3D contestuale, che disegna il profilo durante l’editazione. Infine, vorrei parlare di connettività: tutti i nostri modelli sono aperti allo scambio dati e comandi a distanza. Quindi, le agevolazioni fiscali Industry 4.0 ci hanno trovati già pronti. È stato facile offrire un portafoglio di possibili soluzioni, dove ciascuno ha scelto quella più indicata per la sua fabbrica. Ma in questo campo riteniamo che il mondo industriale sia solo all’inizio: è per questo che R&S Fagor lavora continuamente su progetti che ora sembrano il futuro, ma che presto saranno il presente di ogni officina».
Bosch-Rexroth, il mercato vuole flessibilità
Soluzioni ad alto valore aggiunto e flessibilità sono gli ingredienti secondo Michele Pirelli di Bosch-Rexroth. «L’offerta che proponiamo al mercato si sta spostando sempre più verso soluzioni a elevato valore aggiunto per i costruttori OEM e di riflesso per gli utilizzatori finali. La nostra piattaforma CNC, Indramotion MTX, essendo multitecnologica e multicanale è in grado di gestire qualsiasi tipo di macchina utensile, quindi estremamente flessibile per l’utilizzatore, poiché integra già il software per tecnologie di taglio come il laser, il plasma e il waterjet, punzonatrici e piegatrici oltre che transfer multistazione, rettifica e centri di lavoro e automazioni interconnesse. Stiamo riscontrando un significativo interesse a livello ergonomico verso i nostri CNC grazie a soluzioni HMI intuitive multitouch, interconnesse con tecnologie abilitanti per l’Industry 4.0 come il monitoraggio predittivo e la connessione verso infrastrutture cloud e software di analisi dati; in questo ambito possiamo contare sull’esperienza e infrastruttura della consociata Bosch Connected Industry che sviluppa le infrastrutture e fornisce software e servizi di Analytics e diagnostica predittiva, oltre che sensoristica a bordo macchina. Per la macchina utensile abbiamo da tempo una consolidata e qualificata presenza sensoristica finalizzata a una manutenzione predittiva tramite connessione di tipo IoT e a pompe a regolazione digitale per risparmio energetico e bassa rumorosità. Siamo in grado quindi di orientare scelte progettuali e di prestazioni con la massima integrazione funzionale oggi disponibile sul mercato».
NUM, un CNC sempre più integrato
NUM, come sottolinea Marco Battistotti, è sempre attenta sia alle esigenze dei costruttori che a quelle degli utilizzatori. «Molti utilizzatori, spinti dagli incentivi fiscali ma anche e soprattutto alla ricerca di una maggiore efficienza produttivo/logistica, vogliono integrare le loro macchine nel sistema gestionale aziendale; questo permette di semplificare il flusso dei dati (per esempi pertanto avere un’interfaccia uomo macchina semplice e intuitiva è fondamentale. NUM fornisce un’interfaccia standard adeguata a varie tipologie di macchine, da fresatrici semplici a macchine multiprocesso. NUM offre inoltre sia la possibilità di personalizzare l’interfaccia uomo-macchina nell’ambiente di programmazione del PLC, sia la possibilità di costruire un’interfaccia completamente dedicata tramite linguaggi moderni di alto livello (tipo .NET). Per rispondere alle più stringenti normative di sicurezza NUM fornisce, oltre a un PLC di sicurezza integrato, tutte le funzioni di controllo sicuro del moto. Una delle esigenze fondamentali degli utilizzatori consiste nella possibilità di monitorare lo stato del le macchine (da remoto) ed effettuare interventi di telediagnostica/telemanutenzione. L’architettura dei sistemi NUM permette di collegare le macchine alle Lan aziendali e quindi di potere utilizzare software commerciali per accedere alle funzioni di diagnostica e manutenzione. Per analizzare e monitorare le macchine in modo continuo è anche possibile pubblicare i dati macchina (stato, allarmi eccetera) su cloud; questi dati sono poi accessibili tramite qualsiasi web browser. Anche la necessità di simulare i processi di lavorazione prima di eseguirli è una delle richieste emergenti in alcuni settori: Flexium 3D di NUM è in grado di simulare in modo tridimensionale vari processi di lavorazione mostrando il risultato finale nei minimi dettagli, il tempo di esecuzione del pezzo eccetera».
ECS, sempre maggiore personalizzazione
Personalizzazione, flessibilità e performance le tre voci su cui sta puntando ECS, come ci spiega Giorgio Rossi. «Per quanto riguarda il costruttore chiede sempre più spesso la possibilità di personalizzare a suo piacimento l’interfaccia del CNC: questo con CNC ECS è possibile in modo semplicissimo grazie a un software chiamato RB900 sviluppato interamente da ECS e messo a disposizione dei clienti gratuitamente. Inoltre, monitor sempre più grandi: infatti in Lamiera abbiamo presentato il nuovo CNC 901S con nuovo hardware, monitor 19 pollici e nuova interfaccia, questa completamente sviluppata con il sistema RB900. Per quanto riguarda gli utilizzatori, oltre a fornire loro oggetti sempre più performanti e sempre più affidabili cerchiamo di fornire loro una interfaccia sempre più semplice nell’utilizzo per rendere l’operatore della macchina sempre più autonomo nel programmare pezzi a bordo macchina. Per quanto riguarda Industria 4.0 abbiamo implementato un protocollo standard che può colloquiare con il mondo esterno mettendo a disposizione tutto quanto serve per soddisfare le esigenze del costruttore/utilizzatore».
Fidia, attenti alle necessità dell’officina
Realizzare soluzioni che rispondano alle reali necessità dell’officina è uno dei compiti di Fidia, come ci spiega Claudio Castagno. «Fin dalla fondazione, Fidia ha sviluppato e prodotto controlli numerici per macchine fresatrici di alta gamma e per applicazioni che richiedono prestazioni elevate e funzioni specifiche. Collaborando con clienti, costruttori e centri di ricerca abbiamo sempre prestato grande attenzione alle richieste degli utilizzatori finali, realizzando soluzioni sulla base delle reali necessità dell’officina. Tra queste Velocity5, che migliora qualità delle superfici fresate e tempi di lavorazione, e ViMill, un sistema anticollisione sempre attivo durante tutte le fasi di utilizzo della macchina, sia da programma che movimentando gli assi da pulsantiera o da volantino. Al tema dei collegamenti con sistemi informatici Fidia ha sempre prestato grande attenzione: già il nostro primo controllo nel 1975 era collegato con il centro di calcolo dell’Università di Torino. Oggi i nostri CNC consentono una facile integrazione con i sistemi aziendali e di fabbrica e offrono funzioni di telemanutenzione e di monitoraggio continuo delle condizioni di lavoro e dei parametri di processo remoto. In particolare il nostro modulo HiMonitor consente di tenere sotto controllo le attività eseguite sulle macchine, dai tempi di fresatura ai fermi macchina e ai guasti, sia sul controllo stesso che su dispositivo remoto quale smartphone, tablet o pc. Offriamo quindi ai nostri clienti gli strumenti per gest
ire l’officina in modo efficiente e per usufruire di tutti gli incentivi previsti dalle normative Industria 4.0»
Condividi l'articolo
Scegli su quale Social Network vuoi condividere