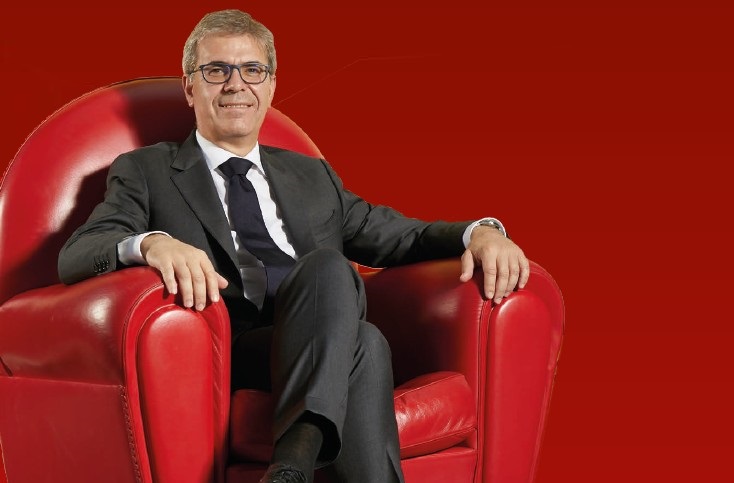
Nato nel 1966, Marco Taisch è Professore Ordinario presso il Politecnico di Milano, nel Dipartimento di Ingegneria Gestionale, dove insegna Advanced & Sustainable Manufacturing e Operations Management. È presidente del Competence Center MADE ospitato negli spazi del Politecnico di Milano. Dal 2002 si è particolarmente dedicato per la Commissione Europea allo studio dei trend tecnologici svolgendo alcune roadmap tecnologiche e degli studi di technology foresight sui sistemi produttivi. In questo ambito, opera come membro del Board di EFFRA (European Factories of the Future Research Association) e del board del cluster italiano Fabbrica Intelligente. Ha fatto parte della cabina di regia del Piano Nazionale Industria 4.0 coordinato dal Ministero dell’Industria e dello Sviluppo Economico. È chairman scientifico del World Manufacturing Forum, l’evento mondiale per la definizione della agenda sul manifatturiero. È socio fondatore di Miraitek, spinoff del Politecnico di Milano per i temi dell’Industria 4.0.
di Edoardo Oldrati, Raffaella Quadri ed Ezio Zibetti
Il futuro della macchina utensile sarà all’insegna della servitizzazione. In un futuro prossimo non si venderanno più macchine, ma solo servizi?
«Credo che sia un futuro possibile ma non prossimo. Sicuramente dobbiamo immaginare macchine sempre più intelligenti e connesse, che andranno ad abilitare in molti casi o servizi di noleggio o il fatto che l’utilizzatore della macchina paghi il fornitore o il produttore della macchina utensile stessa sulla base dei prodotti che questa produce. Sono realtà che già esistono, per esempio nel mondo dell’assemblaggio oppure del packaging; non ancora in maniera così significativa, invece, in quello delle macchine utensili. È quindi un futuro che si avvererà e per il quale non possiamo non essere pronti. Tuttavia è davvero difficile prevedere quanto sarà il tempo in cui avremo entrambi i modelli di business affiancati, ovvero quello della vendita tradizionale della macchina e quello del noleggio e della servitizzazione della stessa».
In ambito produttivo, su quale tecnologia le aziende manifatturiere dovranno investire per avere un ritorno di valore maggiore?
«L’Additive Manufacturing sarà sicuramente una tecnologia produttiva molto più importante di quanto oggi si possa pensare e succederà non tanto perché diventerà più performante da un punto di vista tecnologico, quanto perché subirà una grande spinta da parte del mercato per avere prodotti sempre più customizzati, mentre il concetto della grande serie tenderà a ridursi in volumi. La personalizzazione, che oggi è elemento su cui il cliente tendenzialmente imposta le proprie scelte di acquisto dei prodotti, comporta giocoforza che si elevi l’Additive Manufacturing a tecnologia principale, in grado di rispondere alla richiesta di personalizzazione. In realtà sono in gioco due fenomeni: un technology-push che fa sì che l’Additive diventi più flessibile, più veloce e a costi più bassi; e un market-pool che invece spinge e rende più premiante tale tecnologia rispetto alle più tradizionali, offrendo nel contempo la possibilità di realizzare un prodotto molto più complesso e difficile, non realizzabile con le tecnologie tradizionali. E molto sarà in mano ai designer; oggi il paradosso è che questa tecnologia non è così diffusa perché chi progetta prodotti continua a farlo pensando a un tipo di produzione tradizionale, mentre sono ancora pochi i progettisti capaci di progettare in Additive».
A gennaio 2019 è partito il Competence Center MADE: qual è il primo obiettivo che vi siete posti per questi primi mesi di attività?
«Il primo anno è dedicato alla fase di startup, stiamo costruendo fisicamente MADE e gli spazi che lo accoglieranno che riteniamo possano essere pronti per gennaio 2020: abbiamo a disposizione 2.250 metri quadrati che ospiteranno i 14 use case che costituiscono MADE. Parallelamente stiamo lavorando, come prima attività concreta, alla pubblicazione e all’e rogazione del bando dei progetti cofinanziati dal Ministero dello Sviluppo Economico. Inoltre, stiamo mettendo a punto anche altri servizi, come l’orientamento professionale e la formazione che saranno oggetto dell’attività del Competence Center. Infine, contiamo di essere a pieno regime entro il secondo anno e di continuare a erogare tutti i servizi: orientamento, formazione, consulenza tecnologica, scouting tecnologico, supporto alle aziende nella definizione e costruzione della loro roadmap tecnologica Industria 4.0. Quest’ultimo aspetto è fondamentale in quanto oggi molte aziende sono disorientate, non sanno cosa devono fare, e pur conoscendo le tecnologie 4.0 non hanno chiaro dove usarle, come farlo, quali scegliere e su cosa investire; ecco quindi che MADE, che al proprio interno ha partner con competenze di tecnologie hardware e software, di consulenza, di ricerca e innovazione, diventa il partner migliore – essendo, tra l’altro, totalmente indipendente – nel fornire all’azienda i consigli di cui ha bisogno. Un partner che è quasi una sorta di angelo custode».
Ha definito MADE come “Un’iniziativa delle imprese per le imprese”. Che cosa possono fare le imprese per rendere questo progetto un successo?
«Il ruolo delle imprese è di mettere a disposizione tutto il proprio know how. Nel realizzare MADE abbiamo scelto i migliori sul mercato delle tecnologie hardware e software, coloro i quali riteniamo essere in grado di trasferire tutto ciò che serve per aiutare le piccole e medie imprese italiane a vincere la sfida del 4.0. In questo senso la ritengo un’iniziativa delle imprese per le imprese».
Parliamo di nuove competenze per affrontare il mare tempestoso dell’Industria 4.0: qual è la nuova figura professionale da imbarcare per prima a bordo e la priorità per un’azienda del manifatturiero che vuole investire in nuove figure?
«La capacità di leggere i dati e trasformarli in informazioni rimane la competenza principe su cui bisogna agire. Ovvero diventano fondamentali la capacità di leggere i processi e quella organizzativo-gestionale dell’impianto. Oggi la competitività si gioca sul riuscire a rendere l’intero sistema produttivo, all’interno del quale la macchina è inserita, il più efficiente ed efficace possibile. Ciò significa che chi progetta macchine dovrà non solo avere al proprio interno tutte le competenze tradizionali delle tecnologie meccaniche, ma – di fronte a un mercato sempre più esigente – avere anche macchine intelligenti, che sappiano sia effettuare la lavorazione sia avere un sistema di monitoraggio in tempo reale. E i costruttori dovranno sapere fornire macchine che abbiano entrambe queste dimensioni. Esattamente come oggi un’automobile ha a bordo molta più elettronica rispetto alla meccanica che un tempo la caratterizzava, allo stesso modo dobbiamo immaginare – fatte ovviamente le dovute comparazioni – il medesimo tipo di processo evolutivo. A questo punto la figura principale diventa quella con la capacità di leggere e interpretare il dato».
Guardando la questione da un’altra prospettiva, quale contributo deve dare l’università per formare figure professionali ad hoc e dare questo contributo alle imprese?
«Le figure professionali specifiche oggi escono già dalle nostre università. Il problema è che il numero di laureati al momento non è sufficiente a coprire il fabbisogno delle imprese, che quindi devono investire nella formazione delle persone che hanno già al proprio interno. A oggi ogni lavoratore ha il dovere di formarsi, non si può pensare di restare fermi. La formazione non è più un diritto, è un dovere ed è questo che noi dobbiamo trasmettere».
Dopo anni di sostanziale silenzio sul tema, nell’ultimo periodo la cybersecurity è diventata una tematica importante anche in ambito industriale. A che punto siamo però, secondo lei? Le aziende hanno capito come affrontare la questione?
«Non del tutto, ritengo. Su questo evidentemente bisogna lavorare ancora molto. Oggi però la questione non è di tipo tecnologico bensì culturale: le tecnologie di protezione esistono, basta comprarle e fidarsi di persone esperte che fanno questo mestiere. Spesso c’è ancora inconsapevolezza e accade persino di non accorgersi neanche che i propri dati sono stati hackerati e trafugati. Certamente sono ancora poche le figure molto esperte di questi tematiche, però le società che vendono sistemi di cybersecurity esistono. È finito il tempo in cui si poteva pensare di avere tutto all’interno della propria impresa».
Qual è il principale ostacolo alla crescita in ottica 4.0 delle aziende della meccanica italiane?
«È di nuovo un tema di competenze o di non completa consapevolezza dell’importanza di avere tali tecnologie e di utilizzarle. Nel settore italiano delle macchine utensili – che continua a essere molto tradizionale – ho la sensazione che spesso, purtroppo, vi sia una certa difficoltà nel comprendere la portata innovativa che certe tecnologie – quelle innovative e digitali tipiche dell’Industria 4.0 – possono avere sulla revisione del business aziendale».
Quali sono stati i temi al centro dell’edizione 2019 del World Manufacturing Forum?
«I temi centrali di questa edizione sono stati le competenze e lo skill gap (divario di abilità), ovvero il fatto che oggi le imprese si giocano la propria competitività sostanzialmente andando a formare le persone. La scarsità di risorse umane qualificate è e rimane ancora il limite allo sviluppo della competitività delle aziende. Abbiamo preso le mosse da una delle principali raccomandazioni del World Manufacturing Forum dell’anno scorso, ovvero la questione delle competenze, e su questo tema abbiamo focalizzato l’evento di quest’anno».
C’è un altro aspetto che è importante mettere in evidenza?
«A mio parere il tema della ricerca. Investiamo ancora troppo poco in ricerca e sviluppo. Il nanismo delle nostre imprese da un lato, e i meccanismi di competizione dall’altro, fanno sì che la capacità di investimento in ricerca capace di creare impatti significativi sia estremamente limitata. E ritengo che questo porterà molte delle nostre imprese, soprattutto quelle più piccole, a non essere più competitive. Per questo motivo le aziende si devono aggregare e crescere».
Uno dei possibili elementi potrebbe essere proprio l’aggregazione, al fine di riuscire a fare massa critica e poter investire?
«Esattamente. Oggi la competizione è più forte che in passato, siamo in una fase di grande trasformazione e ancora più di prima è indispensabile investire. Certamente quando l’innovazione tecnologica accelera è sempre positivo, ma per un’azienda non è necessariamente un’opportunità, piuttosto è un elemento di rischio. Oltre che un impegno, un investimento e un cambio di paradigma».
Soluzioni di realtà aumentata possono essere uno strumento efficace per trasmettere competenze specifiche ai nuovi operatori? Pensiamo a settori come le vetrerie, dove trovare operatori formati è sempre più complesso e la formazione diretta è un’attività che richiede molto tempo (troppo per realtà spesso di piccole dimensioni)…
«Sì, ma non credo che siano la soluzione. Ritengo piuttosto che attualmente il problema sia una questione di immagine: viviamo ancora una società eccessivamente tecnofoba per cui la robotica e l’automazione vengono viste come tecnologie che rubano posti di lavoro. Ci troviamo di fronte a un problema culturale serio e a una diffusa percezione negativa che finisce per influenzare anche le scelte dei giovani e delle loro famiglie. Bisogna mettere i ragazzi nelle condizioni di fare scelte per il loro futuro che siano consapevoli, basate su dati reali e questi dicono che la tecnologia, oggi, paga. Il rischio altrimenti è di perdere uno dei patrimoni più importanti che abbiamo: la capacità di trasformazione. Come Paese non abbiamo materia prima e il nostro successo è dato proprio dalla trasformazione, se non dovessimo più avere queste aziende finiremmo per perdere ricchezza».
Condividi l'articolo
Scegli su quale Social Network vuoi condividere