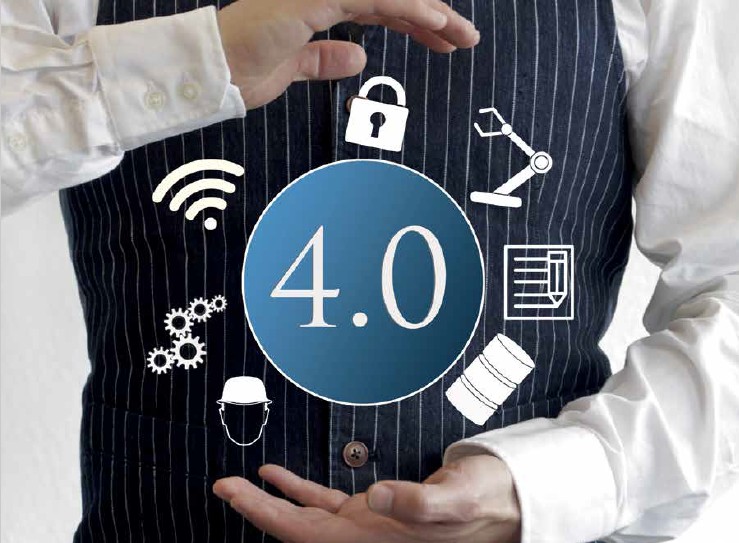
Kuka Roboter Italia ha organizzato un webinar dove, attraverso numerose esperienze applicative, sono state messe in luce le best practices in ambito robotico utili per un rilancio dell’industria manifatturiera.
Più forti della pandemia. Le aziende della meccanica si riorganizzano e, dopo la fase più acuta di lockdown per contenere i contagi, si sono rimesse in moto non soltanto con la produzione (in molti casi mai interrotta del tutto, ma che deve tornare al più presto a regime), ma anche con la comunicazione e le attività collaterali di informazione e formazione. Ecco quindi che il consueto workshop di Kuka è divenuto grazie alla versatilità dell’azienda un vero e proprio webinar, mantenendo invariati i protagonisti e la qualità delle informazioni trasmesse ai partecipanti.
Un mercato in difficoltà
Nell’introduzione dei lavori Alberto Pellero (Direttore Strategy & Marketing di Kuka Roboter Italia) ha mostrato in una rapida panoramica che cosa stava accadendo nel mondo della robotica fino a poco prima della crisi mondiale dovuta al Coronavirus: dopo una crescita media del +18% negli anni 2016-2018, nel 2019 si è registrato un –10% sostanzialmente per l’incrinarsi dei rapporti fra Cina e Stati Uniti con nuovi dazi e tensioni politiche ma anche per la nuova crisi dell’automotive, anche se si parla pur sempre di un volume di vendita di 330 mila robot l’anno. I numeri più significativi si registrano con la Cina (dove non figura più un +30/40% ma un –12%), in Germania e nel Nord America (dove si registra un calo del –23%). Pellero ha poi ricordato che le rivoluzioni robotiche dal 1963 sono già 4: la prima con la nascita del PLC e l’automazione robotica, la seconda con l’av vento dell’Industria 4.0 con i cobot in sicurezza, la terza con la robotica mobile e la quarta con quella cognitiva grazie all’IA (Intelligenza Artificiale) che si sta evolvendo giorno dopo giorno. Inoltre, già nel 2017 una ricerca del McKinsey Global Institute stimava nel 14% la percentuale dei lavoratori (375 milioni di persone) che entro il 2030 si interesseranno nei confronti delle nuove skill per il mondo dell’automazione e dell’IA: in un altro rapporto pubblicato lo scorso maggio 2020 (quindi in piena pandemia) si dice esplicitamente che la chiave per tutti sarà il reskilling; eppure, in Italia soltanto il 9% si è mosso in tal senso, una condizione più che mai da correggere e sulla quale intervenire prima che sia troppo tardi.
Esperienze vincenti
Entrando nel merito degli interventi tecnici del webinar, iniziano il confronto delle esperienze Valter Grifoni (Operation Manager di Bonfiglioli) e Manuel Todesco (CEO di Novotic) con il tema “Coprogettazione per l’evoluzione verso la smart manufacturing”. Grifoni ricorda che anche in tempi di crisi è sempre stato tipico di Bonfiglioli guardare avanti, anche considerando che questa è nata per offrire ai clienti un “pacchetto completo” per risultare operativi sin da subito. C’è ancora di più la necessità di modificare il modo di lavorare e, poco dopo avere inaugurato uno stabilimento operativo dallo scorso gennaio con una nuova linea di assemblaggio che si completa in 4 settimane, ci si è posti obiettivi ambiziosi. Da parte sua, Todesco presenta la linea di assemblaggio in partnership con Bonfiglioli per un obiettivo comune, segnalando che dopo 10 anni nella manutenzione (anche robotica) per l’azienda era giunto il momento del passaggio a system integrator per diversi settori, non limitandosi a copiare e incollare soluzioni standard bensì creandone di mirate e customizzate in partnership con i clienti.
La parola è quindi passata a Gabriele Natale, CEO di Moi Composites, una spin-off del Politecnico di Milano nata nel 2018 dopo che il Laboratorio ha trovato un riscontro sul mercato implementando un processo di stampa 3D unico nel suo genere. “Dalla ricerca al mercato: viaggio di una start-up hitech” l’argomento della presentazione della start-up, che si occupa di materiali compositi in particolare per settori automotive, biomedicale e aerospace, dove il rapporto peso/prestazioni arriva a risultati anche 20 volte migliori rispetto a quanto ottenibile con gli acciai. Oggi il 45% del mercato mondiale, che vale 125 miliardi di dollari, esegue la laminazione impregnandola manualmente: unendo stampa 3D, robotica e materiali ad alte prestazioni il risultato migliora notevolmente poiché non sono necessari stampi (e il relativo break-even legato al numero di pezzi da produrre), si possono realizzare forme altrimenti irrealizzabili in maniera tradizionale ed è possibile personalizzare ogni singolo particolare senza impatto significativo sui costi di produzione. In questo caso i robot Kuka hanno peraltro migliorato la risoluzione di stampa e la flessibilità, aprendo alla stampa 3D altri mercati tradizionali.
È stato quindi il turno di Mirko D. Comparetti (R&D Project Manager del consorzio Synesis) di parlare di “Tecnologia, digitalizzazione, collaborazione: ascoltare i robot per migliorare”: un ascolto che in realtà non serve solo a migliorare la macchina e il processo, ma anche la lavorazione. Come è ormai ben noto, con il processo non s’intende più soltanto un insieme di dispositivi ma anche tutti i dati generati che vanno opportunamente letti e utilizzati: quindi è questo “cyber physical system” con integrazione OT-IT nelle macchine industriali a essere la vera digitalizzazione moderna.
A questo punto è seguito Giovanni Bocchi (Head of Data Science & A.I. Researcher di Kiwi Data Science), che ha concluso la mattinata con l’intervento “Dai dati alla conoscenza: come l’intelligenza artificiale genera valore nell’industria”. L’azienda milanese offre consulenza per migliorare le prestazioni dei clienti ma anche prodotti disponibili a “pacchetti” ragionati per un aumento della qualità: l’obiettivo dichiarato è passare dal chiedersi “quanto costa” a “quanto vale” un determinato prodotto, cercando di “fare parlare” più macchine tra loro.
Flessibilità e produttività
Ha aperto la sessione pomeridiana Angelo Galimberti, fondatore di CIA Automation & Robotics, che ha parlato di “Esperienze industriali, e non solo, di robotica mobile e collaborativa”. Specializzatasi nella produzione di sistemi automatizzati per importanti clienti nel settore meccanico, farmaceutico e chimico, nel 1986 l’azienda ha progettato e costruito il primo robot antropomorfo con motori brushless. I sistemi di automazione robotizzata hanno giocato e tuttora più che mai giocano un ruolo importante nella produzione industriale, per esempio con cobot mobili e asservimenti con manipolazione, ma anche trattando plastica e compositi, nonché in operazioni d’incollaggio e finitura, modellazione e fresatura, assemblaggio, pallettizzazione: una grande varietà in cui la robotica dimostra ogni giorno l’estrema flessibilità.
Arash Ajoudani (Senior Researcher a capo dell’HRI2 Laboratory dell’Istituto Italiano di Tecnologia) ha esposto la presentazione “Enabling Flexible and Agile Work Practices using Kuka Collaborative Robotic Technologies”: sviluppare il pieno potenziale dei cobot, dalle aree ad accesso limitato per l’uomo a quelle dove gli operatori possono interagire in sicurezza. La spinta a usare cobot nasce infatti da tre fattori: l’età della forza lavoro che aumenta, la sicurezza di ridurre o abolire i disordini muscolari da lavori usuranti, la flessibilità produttiva ottenibile con investimenti iniziali minimi. Oltre agli orizzonti del progetto SoPHIA 2020-2024 finanziato dal Programma H2020 e i Joint Laboratory IIT-KMR del 2019-2023, tra i prossimi traguardi si punta a quando il cobot saprà reagire e riuscire a immaginare come aiutare meglio l’operatore (mentre già ora con il machine learning si riesce a insegnargli a riprodurre ritmi e modalità di lavoro).
Claudio Locatelli, System Machining & Assembling Operations di Brembo, ha invece ragionato sui “Robot al servizio della smart manufacturing”, ricordando come oggi si cerchi sin dall’inizio personalizzazione, velocità, qualità e flessibilità, per passare da una “mass production” a una “mass customization” che pur già operativa sarà sempre più implementata: per esempio, massimizzando l’automazione impiantistica delle linee e la loro digitalizzazione con lo sfruttare al meglio le tecnologie abilitanti dell’Industria 4.0. L’uso dei robot aumenta la sicurezza e la sostenibilità, elimina operazioni ripetitive e gravose o pericolose, diminuisce i tempi e i costi, aumenta la diagnostica e la flessibilità.
Michele Lucioni (Direzione Tecnica & Sales di Reti) ha infine riassunto una piccola “Guida all’uso per l’Industria 4.0” nella quale, grazie all’esperienza di consulenza e sviluppo di soluzioni ad hoc, oltre a infrastrutture ed education ha mostrato le tante opportunità dell’Industria 4.0 che consentono semplicità, integrazione ed efficientamento nell’acquisizione e utilizzo avanzato dei dati, per una vera Smart Factory moderna.
Condividi l'articolo
Scegli su quale Social Network vuoi condividere