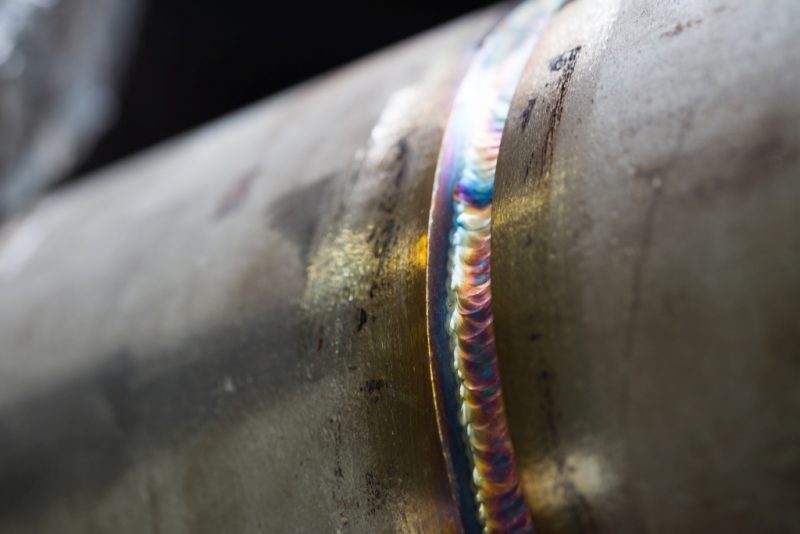
Ogni processo di saldatura ha le sue peculiarità. Di seguito riportiamo una carrellate delle differenti tipologie di processo
Per definizione, la saldatura è un processo di connessione tra due o più parti mediante l’azione del calore, della pressione o di entrambi, ottenendone, talvolta, la continuità di materiale.
Le saldature possono essere classificate in due famiglie:
- Saldature autogene: il collegamento avviene per fusione localizzata dei lembi da unire, con l’eventuale aggiunta di materiale d’apporto; si realizza in questo modo la continuità strutturale tra i pezzi.
- Saldature eterogene: tipiche nelle brasature e saldobrasature. In questo caso il collegamento avviene per fusione del solo materiale d’apporto che si frappone tra i lembi da unire, i quali non fondono neanche parzialmente; non si realizza la continuità strutturale fra i pezzi.
Per eseguire le saldature, a seconda della tecnologia impiegata, si utilizzano diverse apparecchiature come, ad esempio, la saldatrice ad arco, il cannello ossiacetilenico, o la torcia a TIG.
Un’altra caratteristica che contraddistingue le saldature è la preparazione dei giunti da saldare. In base alla tecnologia usata e allo spessore delle piastre da saldare, è possibile selezionare la preparazione dei giunti con l’eventuale cianfrinatura dei lembi per facilitare la penetrazione della saldatura.
Il disegno tecnico prevede una dettagliata simbologia per descrivere nei minimi particolari le saldature.
Saldatura TIG
L’acronimo di questa saldatura sta per “Tungsten Inerent Gas” perché questo processo sfrutta un gas, tipicamente l’argon, per proteggere il bagno dalla corrosione dell’ossigeno ambientale. Durante la saldatura, elevate correnti di centinaia di Ampere vengono scaricate sul pezzo scaldandolo ad elevate temperature facendo così fondere il materiale di base da saldare. L’elettrodo è di tungsteno e non si fonde durante il processo.
Se necessario, il materiale d’apporto è fornito dall’operatore tramite una bacchetta, come nella saldatura ossiacetilenica.
La saldatura TIG è un procedimento adatto alle saldature di acciai pregiati, ad esempio gli acciai inossidabili, rame, ottone e leghe leggere (alluminio e magnesio). In genere la saldatura TIG è usata per saldare lamiere sottili e di medio spessore.
Saldature MIG e MAG
Le saldature MIG e MAG sono processi semi-automatici di saldatura in cui il metallo d’apporto viene fatto avanzare dalla saldatrice in modo automatico consumandosi man mano (elettrodo consumabile). Nella saldatura MIG viene usato un gas inerte per proteggere il bagno dalle ossidazioni (come nella TIG, si usa l’argon), nella saldatura MAG si usa la CO2 che rende il processo più economico, ma, di contro, meno raffinato.
Avendo una capacità di penetrazione ben più elevata della TIG, le saldature MIG e MAG sono usate per saldare spessori notevoli.
In entrambi i casi, dall’elettrodo consumabile viene applicata una tensione elettrica mentre al pezzo viene connesso un morsetto per richiudere il circuito elettrico. L’arco elettrico scocca tra l’estremità del filo e il metallo di base creando un notevole calore che fonde il materiale di base e il metallo d’apporto che man mano fluisce.
Saldatura a ultrasuoni
Per saldare i materiali plastici (in particolare la famiglia dei termoplastici) viene largamente impiegata la tecnologia a ultrasuoni per la sua ripetibilità, velocità d’esecuzione e le sue eccellenti prestazioni meccaniche.
In questo processo, i due pezzi da saldare vengono appoggiati ad una piastra che vibra ad altissima frequenza (oltre i 20 kHz) e piccola ampiezza (alcuni micron). Tale vibrazione è sufficiente a generare attrito a livello delle lunghe macromolecole sulla superficie del manufatto polimerico da saldare. Questo elevato attrito interno al materiale sviluppa molto calore e, quindi, la temperatura localmente sale molto. Una volta che la zona d’interesse arriva a fusione, i due pezzi da saldare vengono rimossi dalla zona di riscaldamento e premuti l’uno contro l’altro fino al raffreddamento completo in modo da solidificarsi nella posizione corretta.
Saldatura ossigas e ossiacetilenica
Nella famiglia delle saldature a ossigas, il calore necessario alla fusione del metallo di base e al materiale d’apporto viene fornito dalla combustione di un gas (combustibile) con l’ossigeno (comburente). I due gas vengono poi convogliati nel cannello per essere miscelati nel rapporto opportuno e fuoriescono da un ugello bruciando ad altissima temperatura.
Un esempio molto diffuso di saldatura a ossigas è la fiamma ossiacetilenica, che, impiegando acetilene, permette di raggiungere temperature di 3200°C.
Il materiale d’apporto è fornito in bacchette o bobine di diverso diametro in dipendenza dalla saldatura da eseguire. Vengono anche impiegate sostanze disossidanti per evitare l’ossidazione del giunto fuso durante la saldatura.
Saldatura al plasma
Nella saldatura al plasma, un gas inerte viene riscaldato a elevata temperatura da un arco elettrico facendo così ionizzarne gli atomi e sprigionando moltissima energia termica (temperature fino a 20’000°C). I gas adottati per creare l’atmosfera ionizzata sono argon, elio, azoto e idrogeno.
La saldatura al plasma è adatta a tutti i materiali, ma è particolarmente sfruttata per gli acciai inox, nickel, rame, ottone, titanio e leghe leggere. Rispetto alla saldatura TIG, quella al plasma è molto più veloce e, a parità di spessore, richiede un numero minore di passate. Inoltre, visto che l’arco al plasma è molto concentrato, la zona termicamente alterata (ZTA) risulta di dimensioni limitate, pertanto i ritiri e le deformazioni residue del materiale sono minori. Di conseguenza, c’è un minor rischio di cricche.
Esiste anche la variante per piccolissimi spessori (sotto il millimetro), chiamata microplasma, ed è usata nei settori elettrici, elettronici e nella meccanica di precisione.
Saldatura per attrito
La saldatura per attrito è un processo di giunzione di pezzi metallici che sfrutta il calore generato dall’attrito tra due pezzi in movimento relativo che vengono compressi tra loro. Dopo la fase di riscaldamento, in cui il materiale rammollendo diventa plastico, avviene la fase di forgiatura in cui i due pezzi vengono compressi tra loro fino al raffreddamento.
La saldatura per attrito può avvenire sia per unire elementi circolari come tubi o alberi (in questo caso un pezzo rimane fisso e l’altro viene portato in rotazione), oppure può essere eseguita su piastre e lamiere e, in questo caso, si parla del processo di “Friction Stir Welding”. In questa variante un utensile cilindrico ruota su sé stesso e viene fatto avanzare lentamente compenetrando tra i due lembi da unire. I due pezzi, scaldandosi per attrito dell’utensile rotante, entrano in campo plastico e dopo il passaggio dell’utensile si raffreddano agglomerandosi tra loro.
Saldatura robotica
La saldatura robotica è il connubio della robotica e delle tecnologie di saldatura. Normalmente un impianto di saldatura robotica prevede un robot antropomorfo con una testa di saldatura che può essere ad arco (MIG o MAG), a resistenza (tipicamente a punti), a TIG o a laser.
Questo tipo di saldatura è adatto alla saldatura di grandi lotti per ammortizzare i costi dell’impianto e delle maschere di saldatura. L’operatore non esegue più manualmente la saldatura ma ne programma il ciclo, che poi viene ripetuto con elevata ripetibilità su tutto l’intero lotto, con il vantaggio di poter lavorare ininterrottamente.
Brasatura e saldobrasatura
La brasatura è una tecnica di saldatura eterogenea: il metallo d’apporto ha una temperatura di fusione molto inferiore rispetto al metallo di base che infatti non viene portato a fusione ma solo riscaldato.
Nella brasatura il metallo d’apporto viene assorbito per capillarità nelle micro-fenditure dei lembi dei pezzi da saldare e l’unione si realizza con la solidificazione del metallo bagnante. Le superfici da brasare hanno piccoli gap (qualche centesimo di millimetro d’aria) e devono essere perfettamente pulite e disossidate.
La saldobrasatura è un procedimento di brasatura forte (temperature di fusione del metallo d’apporto>450°C) che prevede la preparazione dei lembi da saldare (specialmente se di spessore > 4 mm) e la possibilità di depositare il materiale d’apporto con passate successive. Tipicamente si usa il cannello per eseguire l’operazione.
Saldatura a resistenza
La saldatura elettrica a resistenza è un processo di connessione tra due parti metalliche conduttive in cui il calore viene fornito dal passaggio di corrente tra due elettrodi. Per questa tipologia di saldatura non è previsto materiale d’apporto. In aggiunta, durante il passaggio di corrente, i due elettrodi premono con forza le due lamiere da saldare. Il passaggio di corrente fa scaldare puntualmente il metallo per effetto Joule e, grazie alla forza premente, il nocciolo fuso si agglomera.
Questo processo è tipicamente usato per saldare lamiere e piastre sottili (in genere di spessore inferiore a 10 mm). I materiali saldabili sono: acciaio, inclusa la famiglia degli acciai inossidabili, alluminio e bronzo.
Questo tipo di processo è applicabile con diverse tecniche, tra cui:
- saldatura a punti (o puntatura);
- saldatura a rulli (o rullatura);
- saldatura a rilievi.
Saldatura laser
La saldatura laser sfrutta la potenza luminosa di un fascio di luce concentrato in un punto estremamente piccolo. L’energia scaricata su pezzo lo fa scaldare fino a portarlo localmente alla fusione in pochissimo tempo. La zona termicamente alterata in questi casi è molto piccola in quanto il processo non fa a tempo a scaldare le zone limitrofe al giunto, di conseguenza la resistenza meccanica della connessione è eccellente. Un altro vantaggio è la velocità: questo processo permette velocità di esecuzione molto elevate se comparate con altre tecnologie (esempio TIG).
D’altro canto questo tipo di saldatura richiede una preparazione estremamente precisa dei lembi che si ripercuote in attrezzature di staffaggio estremamente complesse e costose.
I materiali adatti alla saldatura laser sono acciaio e acciaio inox, o altri materiali metallici.
Saldatura ad arco
Questa metodologia di connessione è molto diffusa nelle aziende metalmeccaniche per la saldatura di carpenteria metallica. Si tratta di un processo di saldatura elettrico che fa uso di una bacchetta che funge sia da materiale d’apporto che da elettrodo. La bacchetta ha al centro un filo metallico chiamato anima di acciaio extra-dolce e questa è ricoperta da un rivestimento che assicura la stabilità dell’arco e la protezione del bagno di fusione dalle ossidazioni. Durante la saldatura, si genera un flusso di elettroni tra la bacchetta e il pezzo che è connesso alla saldatrice tramite un morsetto.
Questa saldatura sprigiona molto calore: questo facilita la penetrazione della saldatura su piastre anche di grosso spessore tramite diverse passate. In questi casi i lembi vanno cianfrinati a dovere.
Condividi l'articolo
Scegli su quale Social Network vuoi condividere