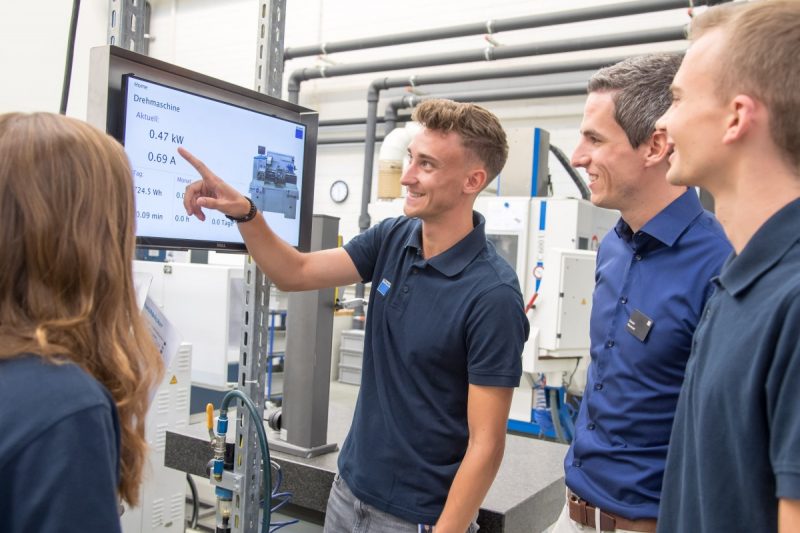
La digitalizzazione nella costruzione delle macchine utensili e nella lavorazione dei metalli.
Nel bel mezzo della crisi causata dal nuovo Coronavirus responsabile della malattia CoViD-19, fra restrizioni alla mobilità e al contatto, ecco improvvisamente comparire di nuovo una parola d’ordine: la digitalizzazione, ritenuta a lungo una panacea per l’industria e il commercio. I virologi alla ricerca di risposte sulla durata e la gravità dell’epidemia sperano che i dati collettivi forniti dagli utenti di telefonia mobile in forma anonima diano indicazioni sul comportamento della popolazione, migliorando quindi le previsioni. Alla luce della necessità di isolamento e distanza fisica, gli strumenti digitali per la comunicazione e la visualizzazione a distanza, noti da tempo, stanno rapidamente aumentando di importanza e di utilizzo in tutti i settori economici. Politici, medici e consiglieri di amministrazione dell’industria si riuniscono in videoconferenza, le scuole trasformano le loro lezioni in clip di immagini in movimento e gli strumenti di manutenzione remota ottengono lo status di componente “critica del sistema”.
L’industria conosce da tempo il potenziale insito nella digitalizzazione. Le speranze e gli obiettivi sono molteplici. Che si tratti di uno sviluppo più rapido di macchine più flessibili, di una maggiore affidabilità, di una manutenzione (a distanza) più regolare, di una migliore documentazione, di un grado di automazione più elevato, di effetti di apprendimento basati sulla comparabilità fra abilità collettiva o individuale – l’elenco delle possibilità è infinito. Alla luce delle attuali sfide non pochi vorrebbero essere molto più avanti rispetto al progresso della digitalizzazione e il potenziamento delle reti necessarie, come ad esempio quello del nuovo standard di comunicazione mobile 5G: «Il 5G per le imprese apre le porte a produzione, manutenzione e logistica totalmente wireless. Elevate velocità di trasmissione dei dati, trasmissione ultra affidabile e tempi di latenza brevissimi consentiranno di aumentare notevolmente l’efficienza e la flessibilizzazione nella creazione di valore aggiunto all’industria», dichiara Eckard Eberle, CEO della Business Unit Process Automation alla Siemens. Eberle risponde del Siemens 5G Test Center. Sebbene non si veda (ancora) alcuna macchina utensile wireless, la strada verso questo tipo di collegamento in rete nelle fabbriche del futuro è chiaramente tracciata. Da alcuni mesi, a Norimberga la Siemens sta testando la banda di frequenza da 3,7-3,8 GHz con componenti logistici in un ambiente industriale reale, utilizzando controllori Simatic e sistemi IO.
Anche senza il 5G, tra gli specialisti dell’automazione si intravedono già applicazioni entusiasmanti per il supporto digitale: per identificare le cause di errore in problemi di qualità attinenti componenti a forma libera, la Siemens, ad esempio, punta su un software capace di ispezionare tutti i punti nevralgici della catena di processo e controllare le stazioni fra il sistema CAD e gli utensili utilizzati. Infatti, le cause di errore possono essere molteplici e varie quali l’output dello stesso CAD, l’output del CAM o del post processor, la parametrizzazione del CNC e dei controllori di azionamento, la meccanica della macchina, gli utensili, il refrigerante e teoricamente anche il materiale del pezzo in lavorazione. Il programma Analyze MyWorkpiece/Toolpath controlla i dati in uscita delle singole parti del sistema, come il file in formato STL per il CAD, il file MPF per il CAM o il post processor, la registrazione dei setpoint di posizione e, infine, il modo in cui il controllore di azionamento, la meccanica della macchina e l’utensile hanno convertito i dati. Così è possibile fornire già prima della produzione una garanzia della qualità dei dati CAD/CAM di pezzi di grande formato. Questi sistemi di ottimizzazione, attuati in prossimità delle macchine utensili, rivestiranno un ruolo importante anche alla fiera AMB 2020. A Stoccarda le cosiddette soluzioni Edge saranno probabilmente quelle vincenti. Offrono una potenza di calcolo aggiuntiva per il supporto digitale nella produzione e in molti casi utilizzano algoritmi basati sull’intelligenza artificiale che sostengono l’operatore della macchina durante il suo lavoro. A settembre 2020 bisognerà trovare vie d’uscita dalla crisi praticabili, preparando una crescita delle cifre d’affari e un risparmio sui costi; in particolare, aumentando la produttività e migliorando l’efficienza di impianti e macchinari per quando i registri degli ordini saranno nuovamente pieni.
Tra opportunità e sfida
Con le nuove soluzioni come l’Edge Computing la digitalizzazione negli ambienti produttivi eterogenei della lavorazione dei metalli offre varie possibilità. Tuttavia restano ancora numerose sfide da raccogliere. Per rendere utilizzabile la digitalizzazione su vasta scala sono necessari degli standard, afferma con convinzione Markus Horn, direttore generale della Paul Horn GmbH (nella foto qui accanto): «L’associazione VDMA sta portando avanti l’argomento nell’ambito della GTDE. Ne sono molto lieto e noi, come impresa, stiamo facendo la nostra parte mettendo a disposizione i relativi dati». GTDE è l’acronimo di Graphical Tool Data Exchange Standard Open Base e.V., associazione che opera come centro di competenza, come rappresentante di parti interessate e fornitore di servizi nello scambio dei dati sugli utensili. I soci e i partner di questa associazione sono famosi produttori e fruitori di utensili, aziende produttrici di software e membri dell’associazione di categoria utensili di precisione in seno alla VDMA. L’obiettivo è quello di creare uno scambio lungimirante di dati attinenti gli utensili sulla base di standard internazionali e affiancare le aziende attive in questo campo. L’associazione fornisce il suo sostegno alla realizzazione dello scambio dei dati degli utensili, appoggiando pertanto la messa a disposizione unificata dei dati degli utensili attraverso un proprio server che permette ai produttori partecipanti di controllare i dati degli utensili, come ad esempio le specifiche, la grafica 2D e 3D secondo gli standard DIN e ISO, e renderli disponibili gratuitamente.
Tuttavia Horn chiarisce anche che «I soldi si fanno con l’utensile. Integrato, ma non completamente sostituito dal digitale. Per noi produttori di utensili significa questo: se l’utensile non fornisce la qualità e la precisione necessaria, la digitalizzazione non serve a niente». Attualmente ci sono molte aziende sul mercato che offrono servizi digitali: produttori di software, macchine e utensili. Senza standard, però, è spesso difficile per i clienti implementare gli utensili che, inoltre, perdono di flessibilità nell’uso. «I prodotti o i servizi digitali supplementari dovrebbero essere impiegati solo là dove creano effettivamente un vantaggio. Continueremo a concentrarci sull’utensile, forniremo i dati e offriremo soluzioni digitali per quei casi concreti per i quali sarà possibile produrre un effetto», conclude Horn. Poiché anche quest’anno la AMB coprirà l’intera catena di processo nel campo della lavorazione dei metalli, i visitatori potranno fruire di un’ampia panoramica della tecnologia classica combinata con altri vantaggi della digitalizzazione.
Sensori sensibili
La riduzione al minimo degli scarti è un obiettivo importante per il quale le soluzioni digitali possono risultare utili. Così, la Paul Horn GmbH e il gruppo Kistler hanno unito le proprie competenze per individuare possibili problemi durante la truciolatura, quali materiali difettosi, materiali da taglio usurati e rotture di utensili. Gli esperti in tecniche di misura dinamica rilevano la pressione, la potenza, il momento torcente, l’accelerazione e, in stretta collaborazione con gli ingegneri della Horn, hanno sviluppato una soluzione per il monitoraggio in tempo reale degli utensili nelle microlavorazioni di tornitura. Il PTS (Piezo Tool System) è composto da un trasduttore di forza inserito nell’utensile di tornitura, capace di fornire informazioni sulle condizioni dell’utensile durante la lavorazione. Il sensore PTS è estremamente piccolo e misura persino la forza di truciolatura più bassa con un’alta risoluzione. Il sistema è adatto a essere utilizzato nelle operazioni di tornitura, in special modo nella microlavorazione. Qui i metodi di misura alternativi, come il monitoraggio della potenza di azionamento del motore del mandrino principale, sono poco utili a causa delle piccole anomalie. Anche la misurazione del suono intrinseco non produce risultati sempre soddisfacenti sui pezzi piccoli. Infine, è esclusa anche l’ispezione visiva a causa dell’uso di lubrificanti refrigeranti e delle elevate velocità di rotazione durante il processo di lavorazione. La nuova soluzione non richiede alcun intervento nel sistema di controllo CNC e l’uso è indipendente dalla macchina. Di conseguenza, il PTS riduce i costi di produzione, aumentando la capacità produttiva.
Percorsi brevi per raggiungere i clienti
La consapevolezza dei costi e l’efficienza coinvolgono anche i produttori di macchine. «La necessità di prodotti digitali va di pari passo con la messa a fuoco da parte dei nostri clienti dell’efficienza nei processi produttivi. A questo proposito, le soluzioni basate sul digitale contribuiscono anche a migliorare la struttura organizzativa dei nostri clienti. L’accorciamento dei tempi di risoluzione dei difetti costituisce un tema tanto quanto la maggiore disponibilità della macchina», considera Olaf Furtmeier, direttore generale della Burkhardt und Weber. Il vantaggio di una media impresa è quello di poter fruire dei percorsi brevi, di affrontare progetti di sviluppo con squadre agili per apportare il maggior numero possibile di prospettive al processo di sviluppo. «Tuttavia è essenziale chiedere aiuto a partner qualificati. Solo in questo modo possiamo garantire che nei prodotti venga incorporato un know-how completo, capace di offrire un prodotto finale con un reale valore aggiunto accessibile anche ai nostri clienti», inquadra Furtmeier.
La comunicazione fluida fra i singoli elementi di produzione è anche alla base della digitalizzazione e di Industria 4.0 della Zoller quando si tratta di impostare, misurare e gestire gli utensili. Oggi, in particolare per il percorso di trasmissione dei dati dal dispositivo di impostazione alla macchina esistono molti modi affidabili e veloci. I dati effettivi degli utensili vengono preparati in modo adeguato per ciascun sistema di controllo della macchina e trasferiti direttamente dal dispositivo di regolazione e misurazione al sistema di controllo CNC. Il software converte i valori specifici della macchina in un formato adatto al controllo e li emette. Il software contiene una libreria di oltre 230 formati di emissione standard per le macchine più disparate. La fiera AMB 2020 è la piattaforma giusta anche per questi argomenti oltre che per intavolare discussioni su possibili modifiche atte a soddisfare esigenze specifiche di clienti che alla Zoller sono sempre possibili, a quanto pare.
Transfer di conoscenze e formazione
Il motivo per cui, rispetto ad altri settori, la digitalizzazione è riuscita ad affermarsi relativamente tardi nella costruzione delle macchine utensili e nella lavorazione dei metalli non sta solo nei costi o nell’impegno necessario alla sua realizzazione, ma largamente anche nei nuovi paradigmi e negli approcci di tutti i dipendenti. Con l’inizio di quest’anno di formazione, l’espositore della AMB Trumpf ha già dimostrato quanto sia importante la questione del transfer di conoscenze e della formazione per affrontare da zero la digitalizzazione: per rendere giustizia al cambiamento digitale, la Trumpf punta sul networking e qualifica per la prima volta le sue nuove leve con un “Istruttore di Industria 4.0”. Il programma coordina tutti i contenuti digitali dei vari orientamenti formativi, assistendo gli apprendisti e gli studenti che aderiscono al sistema di studio duale. «Da noi la digitalizzazione diventerà un elemento formativo fondamentale. Chi studia informatica o compie un apprendistato in quel campo deve conoscere le mansioni di un ingegnere meccanico. Dal canto suo, l’ingegnere meccanico deve conoscere il software di cui ha bisogno per la sua macchina. Questi requisiti si integrano anche con gli studi di economia aziendale che, per esempio, per il calcolo delle macchine devono includere parti in lamiera e software», dice Katja Tiltscher, responsabile della formazione presso la Trumpf. In questo contesto si inserisce bene la Trend Lounge, il nuovo elemento del programma collaterale della AMB 2020 che offrirà ai visitatori un forum gratuito per il transfer delle conoscenze e lo scambio con esperti. Durante i 5 giorni di questo forum, al centro dell’attenzione del programma si troveranno vari argomenti di interesse come la produzione additiva, la costruzione con materiali leggeri e, naturalmente, la digitalizzazione.
Condividi l'articolo
Scegli su quale Social Network vuoi condividere