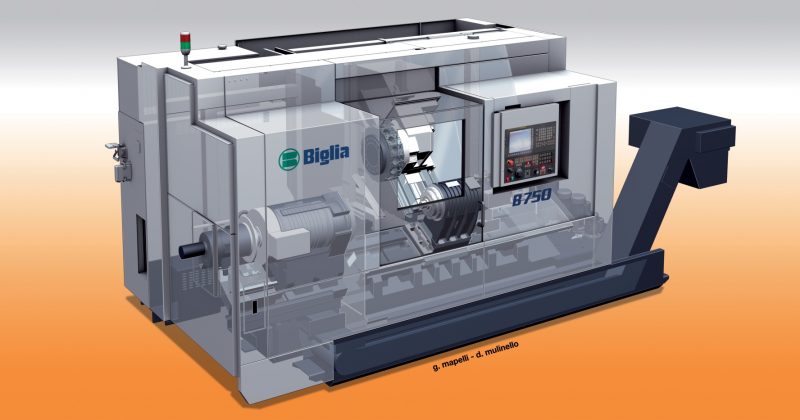
I centri di tornitura B750 e B1250 sostituiscono due modelli di successo di produzione Biglia, migliorandone la rigidezza, precisione e la produttività.
Anche i prodotti meglio riusciti, con il passare del tempo, devono beneficiare di un aggiornamento tecnologico.
È il caso dei centri di tornitura Biglia B750 e B1250, due nuovi modelli che sostituiranno rispettivamente le serie B650/B658 e B1200.
Presentata nel 2003 e con ormai 10 anni sulle spalle, la gamma precedente è risultata un best seller in casa Biglia: ne sono stati venduti oltre 1000 esemplari in 10 anni, circa il 25% della produzione complessiva dell’azienda di Incisa Scapaccino (AT).
Differenze di sostanza
Le principali differenze rispetto alla gamma precedente sono due: per prima cosa i tecnici Biglia hanno lavorato per aumentare la rigidità e la precisione. Ridisegnando le strutture sfruttando l’analisi agli elementi finiti (FEM) è stato ottimizzato il basamento incrementandone il peso; inoltre, sono state aumentate la dimensione e la spaziatura delle guide degli assi X e Z, tutte rigorosamente prismatiche. La conseguenza è una macchina ad elevata stabilità e ottimale assorbimento delle vibrazioni..
Il secondo aspetto innovativo è la presenza di una torretta portautensili di nuova concezione. La torretta, di progettazione e produzione Biglia, adotta un motore integrato per l’azionamento degli utensili motorizzati al posto della classica trasmissione meccanica con catena cinematica. L’impiego di un motore integrato nel disco portautensili elimina la necessità di cinghie, rinvii, coppie coniche ecc., accoppiando direttamente il motore al portautensili motorizzato.
La riduzione dei giochi e delle vibrazioni migliora la qualità finale delle lavorazioni sia in termini di precisione, sia di qualità della finitura superficiale. Inoltre, consente di sfruttare al meglio la potenza disponibile: la catena cinematica di un sistema tradizionale assorbe circa il 15-20% di potenza girando a vuoto, . Con la nuova torretta progettata da Biglia questo valore è ridotto a zero, rendendo disponibile tutta la potenza all’utensile o, in alternativa, utilizzando meno potenza al motore per effettuare le medesime operazioni. Si riduce inoltre la generazione di calore dovuti ai rinvii. Trattandosi di un motore integrato, è previsto il suo raffreddamento attraverso un sistema di raffreddamento a liquido simile a quelli presenti negli elettromandrini.
Come accennato, si tratta di una linea centrale nella produzione Biglia: la robustezza e l’affidabilità hanno rappresentato due fattori chiave nella progettazione di questa macchina. Oltre alla struttura interamente in ghisa, i nuovi modelli dispongono di guide prismatiche temprate, rettificate e raschiettate, che garantiscono un incremento di rigidità del 30% rispetto alla serie precedente.
Queste qualità hanno benefici a cascata sulle funzionalità della macchina. Anche la vita utensile risulta incrementata, poiché l’impiego di un sistema di bloccaggio idraulico con dentatura Hirth con diametro maggiorato rende meccanicamente più rigido l’intero assieme, riducendo ulteriormente le vibrazioni trasmesse all’utensile ed evitandone così la scheggiatura o l’usura prematura.
Una gamma articolata
I modelli B750 e B1250 differiscono tra loro fondamentalmente per la corsa dell’asse Z e per dettagli conseguenti (come la presenza di due portelli di accesso anziché uno).
Il massimo diametro lavorabile per entrambe le macchine è pari a 552 mm, mentre la lunghezza tra le punte è rispettivamente di 765 mm e 1195 mm.
Entrambi i modelli sono in grado di gestire fino a un diametro massimo rotante sul banco di 680 mm (500 mm sul carro).
Poiché gli elettromandrini delle serie precedente erano stati appena rinnovati, sono stati utilizzati anche sui nuovi B750 e B1250. Sono disponibili in svariate taglie e potenze: il più piccolo è quello ASA 6” da 65 mm di passaggio barra, capace di erogare 30 kW in S1 con una coppia di 286 Nm e un regime massimo di 4.500 giri/min. Il modello ASA 8” con passaggio barra da 80 mm offre 22 kW, una coppia di 398 Nm e 3.500 giri/min; sempre ASA 8”, ma con passaggio barra da 100 mm, la versione più potente garantisce 38 kW e 1014 Nm, capaci di spingere il mandrino fino a 3.000 giri/min.
Indipendentemente dal modello, tutti gli elettromandrini sono raffreddati e stabilizzati. Poiché le potenze in gioco sono notevoli, comprese quelle di spinta degli assi lineari, i progettisti Biglia hanno previsto una combinazione di cuscinetti a rulli cilindrici (il primo e l’ultimo) e una coppia di cuscinetti a sfera a contatto obliquo: questa sequenza si rivela ottimale per massimizzare la rigidità e contrastare le spinte assiali e radiali.
Veloce e produttiva
La superiore rigidità, unita all’alta potenza disponibile al mandrino, consente di incrementare la capacità di asportazione senza sacrificare la precisione e, in definitiva, di ottenere un’elevata produttività.
Nello sviluppo delle nuove macchine, la “precedenza” è stata data a questi fattori anziché alle velocità pure e semplici degli assi, che comunque raggiungono i 18 m/min in X, 24 m/min in Z e, quando disponibile, 7,5 m/min in Y: quando le corse sono brevi, infatti, è più importante poter contare sull’accelerazione poiché spesso la velocità massima, su brevi tratti, non viene raggiunta.
L’adozione di PLC e relativi software estremamente reattivi consente poi di migliorare le prestazioni limitando al minimo i tempi morti: se da un lato le potenze e la rigidità consentono di lavorare al meglio quando si sta asportando truciolo, nel cosiddetto “taglio in aria” la macchina non perde tempo nell’esecuzione dei vari passaggi, nell’elaborazione del programma ecc. Passare dalla modalità di tornitura a quella di fresatura in meno di un secondo, ad esempio, si rivela più utile di un asse veloce.
La rotazione della torretta di una posizione, poi, richiede solo 0,2 secondi: se ogni cambio utensile richiedesse più tempo, si finirebbe per azzerare i vantaggi derivanti dalle qualità dinamiche degli assi.
Maggiore asportazione significa inevitabilmente maggiore generazione di calore.
L’isolamento delle fonti di calore è il primo passo per ridurre al minimo le dilatazioni termiche di una macchina utensile: la vasca del lubrorefrigerante e l’impianto di termostatazione del motore torretta e dell’elettromandrino sono scollegati dal basamento, in modo da non trasmettere il calore fino all’area di lavoro.
La progettazione termosimmetrica consente di controllare gli allungamenti e di evitare le torsioni: fonti di calore isolate, che intervengono su una sola parte della macchina, sono complesse da gestire e contrastare. Proprio per questo l’isolamento termico e il raffreddamento delle fonti di calore è stato curato in modo particolare.
Macchina tuttofare
La torretta portautensili è disponibile in versione semplice o motorizzata, con 12 o 16 posti. Statisticamente, in Biglia hanno rilevato che la versione più richiesta è quella da 16 posizioni motorizzate, perché rendono la macchina un vero centro di tornitura in grado di effettuare ogni genere di lavorazione. Con il crescere della complessità dei pezzi da lavorare, infatti, diventa fondamentale poter contare su macchine estremamente flessibili: per questo la soluzione motorizzata con 16 posti utensile risulta ad oggi quella preferita dagli utilizzatori, in particolare dai terzisti che necessitano di impianti produttivi ma molto flessibili, in grado di gestire di volta in volta lotti anche molto diversi tra loro per numerosità di pezzi, complessità geometrica e tenacità del materiale da lavorare.
Grazie all’impiego di un motore efficiente e all’assenza della catena cinematica, è possibile disporre di una potenza massima di 17 kW all’utensile con coppia di 56 Nm e 10.000 giri/min (velocità limitata a 6000 per via dei portautensili motorizzati) questa combinazione permette di effettuare asportazioni anche molto consistenti, sfruttando a dovere le prestazioni degli utensili più moderni e senza scendere a compromessi con i parametri di lavoro.
La presenza di un motore in prossimità della torretta e della relativa adduzione di lubrorefrigerante ha richiesto una particolare cura nell’assicurarne le condizioni operative ideali: il corpo della torretta è infatti provvisto di guarnizioni e, come ulteriore precauzione, è pressurizzato affinché i fluidi non vi penetrino.
Modelli completamente personalizzabili
Al di là di corse e potenze, i modelli B750 e B1250 possono essere equipaggiati con una vasta gamma di opzioni capaci di ampliarne le possibilità operative o di rispondere ancora meglio a specifiche necessità.
In funzione delle richieste dell’utilizzatore, queste macchine possono montare una contropunta o un contromandrino: nel secondo caso, il motore da 30 kW, 286 Nm e 4.500 giri/min permette di svolgere agevolmente tutte le operazioni di ripresa necessarie.
Oltre agli encoder coassiali sulle viti presenti di serie, possono essere richieste righe ottiche pressurizzate per incrementare ulteriormente la precisione della macchina.
Anche l’evacuatore può essere scelto sulla base di differenti fattori, come il volume di trucioli generato, il materiale lavorato ecc.
Per la lavorazione da barra è disponibile un kit costituito da un dispositivo di scarico automatico dei pezzi finiti e l’interfaccia per spingibarra; inoltre, sul B1250 è possibile avere una lunetta trascinata dal carro dell’asse Z o motorizzata come asse indipendente.
Il controllo numerico è l’apprezzato Fanuc 32iB, disponibile con schermo da 10,4” o, a richiesta, da 15”. Di Fanuc sono anche motori e azionamenti, completando così il pacchetto di comando e potenza installato sulle macchine Biglia.
La macchina ha due pompe: la prima, da 3,5 bar, si occupa dei lavaggi nel campo di lavoro; la seconda, da 7 bar, provvede all’adduzione dei fluidi alla torretta. In opzione si può arrivare per step fino a 70 bar, indispensabili quando vengono eseguite operazioni critiche come le forature profonde.
Sistemi di aspirazione dei fumi, dispositivo di azzeramento utensili e interfacce per caricatori automatici completano il capitolo relativo alle opzioni di personalizzazione.
Sul fronte della manutenzione e dell’accessibilità, la macchina è di semplice gestione: la riduzione al minimo dei sistemi di rinvio ha semplificato anche la manutenzione, mentre il posizionamento dei dispositivi di verifica e gestione di pressioni, livelli e rabbocchi è ridotto al minimo.
Condividi l'articolo
Scegli su quale Social Network vuoi condividere