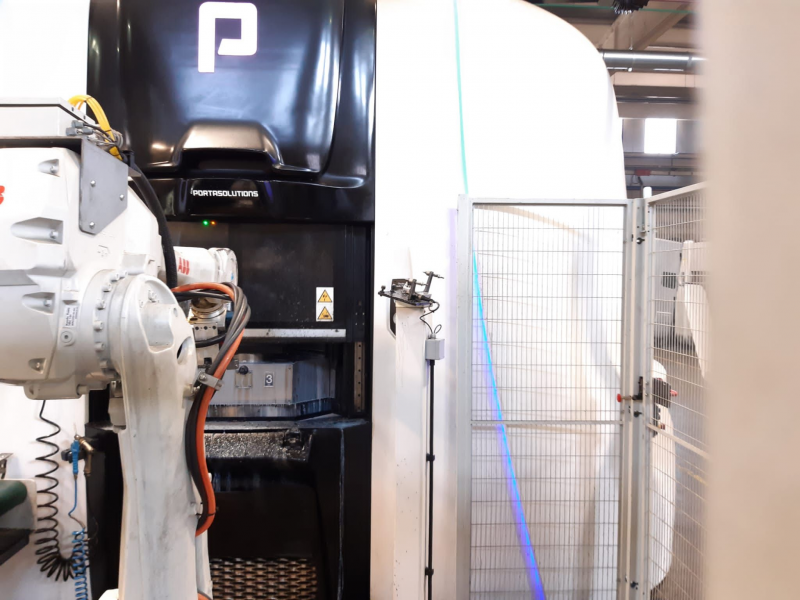
Un unico ciclo di lavorazione con un transfer a 3 mandrini indipendenti. È questa la soluzione scelta dall’azienda bresciana Tecnofor con l’acquisizione dell’impianto Portacenter, sviluppato da Porta Solutions. I vantaggi produttivi spiegati da Giancarlo Coglio, CEO di Tecnofor.
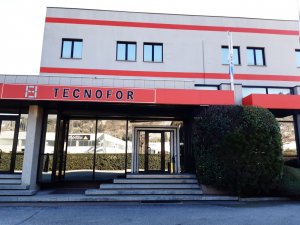
Tecnofor è una realtà italiana specializzata nel settore della lavorazione dei metalli che si rivolge direttamente agli OEM e ai più importanti TIER1 che sviluppano componenti propri. Grazie al consolidato know-how nelle lavorazioni e nella realizzazione dei grezzi e al personale altamente qualificato, l’azienda di Paitone (BS) è in grado di rispondere alle esigenze della clientela proponendo le migliori soluzioni in base alle singole esigenze anche attraverso un lavoro di co-engineering.
L’ascolto del cliente è alla base del lavoro svolto dal team di Tecnofor che studia, propone e realizza soluzioni alternative in grado di ridurre i costi e garantire allo stesso tempo la massima efficienza e qualità. Proprio per questo, l’azienda investe molto in innovazione e sviluppo attraverso nuovi macchinari, formazione costante del personale e certificazioni (per esempio la IATF per il settore Automotive e molte altre). Sempre più proiettata verso il settore automotive, Tecnofor vanta una struttura capace di dialogare con i più grandi client nazionali e internazionale del settore.
Tecnofor e Porta Solution: una collaborazione vincente
Proprio in questo scenario si inserisce la collaborazione tra Tecnofor e Porta Solutions che ha portato allo sviluppo di una soluzione produttiva che rappresenta il miglior compromesso tra la flessibilità del centro di lavoro e la produttività della macchina transfer. Questo ideale rapporto tra flessibilità e produttività, nel solco tracciato dai sistemi di automazione industriale, si chiama Portacenter, il centro di lavoro modulare a 3 mandrini indipendenti, progettato e realizzato da Porta Solutions. Il costruttore di Villa Carcina (BS), con oltre 65 anni di attività, dal 2005 ha deciso di abbandonare la produzione di macchine transfer per dedicarsi a questa innovativa soluzione, studiata per permettere all’utilizzatore una maggiore efficienza produttiva, grazie al cambio di produzione rapido e al sistema a 3 mandrini totalmente autonomi: è come avere 3 centri di lavoro in un unico impianto. Numerosi i vantaggi produttivi ottenuti dalla Tecnofor che, circa due anni fa, ha installato il modello Portacenter 250, con cubo di lavoro di 250 mm, nel proprio stabilimento di Paitone.
Lavorazioni meccaniche ad alto valore aggiunto
Tecnofor è, oggi, una importante realtà industriale del territorio bresciano impegnata in lavorazioni meccaniche per la produzione di componenti destinati a clienti che operano nei settori automotive e termoidraulica. Con circa 30 milioni di fatturato, 50 dipendenti e uno stabilimento di 25.000 m2, di cui 12.000 coperti, l’azienda di Paitone ha saputo saldamente posizionarsi sul mercato grazie a una lungimirante strategia di crescita perseguita dai vertici del Gruppo Forelli al quale appartiene.
Fondata nel 1997 da alcuni artigiani con l’obiettivo di produrre componentistica per rubinetteria industriale in ottone, con particolare riferimento alle sfere per valvole, Tecnofor ha vissuto un momento di svolta produttiva e commerciale negli anni successivi, in concomitanza con la sua acquisizione da parte del Gruppo Forelli, già suo fornitore di semilavorati in ottone.
Con il successivo trasferimento in un nuovo stabilimento e con l’installazione di nuovi macchinari, Tecnofor rilancia la sua produzione di sfere divenendo così il braccio Service che si occupa di lavorazioni meccaniche per il Gruppo. Le altre aziende che compongono il Gruppo sono: Farelli Pietro, che produce lingotti di ottone e bronzo utilizzati per la rifusione e produzione di componentistica; Metallurgica S. Marco, che produce barre in ottone per torneria e stampaggio; Cidneo Metallurgica, specializzata nella produzione di estrusi e trafilati in ottone per il settore edilizio.
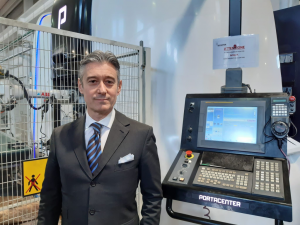
«Grazie alla cooperazione con le aziende del Gruppo e alla condivisione del portafoglio clienti – afferma il CEO di Tecnofor, Giacomo Coglio, che rappresenta la quarta generazione di imprenditori alla guida di un Gruppo nato nel 1925 con la fondazione della Forelli Pietro – la Tecnofor ha vissuto un significativo sviluppo industriale che, nel 2008, l’ha portata ad allargare il suo mercato di sbocco verso il settore automobilistico per il quale vengono lavorati componenti di precisione in alluminio, ghisa e acciaio. L’esperienza e la professionalità del nostro personale altamente specializzato, unite a un moderno parco macchine composto prevalentemente da transfer, da centri di lavoro bimandrino e da torni monomandrino e plurimandrino, consentono di offrire ai nostri clienti soluzioni tecnologiche diversificate e all’avanguardia, adattate alle produzioni più varie, in termini di materiali, di complessità morfologica e di numero di pezzi per commessa. A dimostrazione della flessibilità della struttura produttiva, l’azienda fornisce ai mercati automobilistico e termoidraulico, a seconda delle richieste, componenti meccanici in diversi stadi, grezzi, finiti di lavorazione meccanica, assemblati e verniciati, oltre a un servizio di prototipazione e campionatura, per le consegne in tempi rapidi».
In questo contesto produttivo avanzato, si inquadra la recente esperienza con Porta Solutions per l’acquisizione dell’impianto Portacenter 250, resosi necessario per la produzione di supporti motore per veicoli pesanti, secondo livelli di produttività superiori a quelli registrati con la precedente soluzione adottata da un altro fornitore.
Centro di lavoro a 3 mandrini indipendenti
Il Portacenter, disponibile oggi nelle versioni 250 e 500, è il primo centro di lavoro a 3 mandrini indipendenti, costruito in serie, ed è stato concepito prendendo spunto dalla filosofia della Lean Manufacturing applicata al mondo degli utilizzatori di macchine utensili. L’obiettivo perseguito dal costruttore bresciano fin dal 2005 è quello di trovare il giusto equilibrio tra flessibilità e produttività per affrontare le nuove sfide di mercato dove l’efficienza produttiva gioca un ruolo determinante. Grazie alle caratteristiche di rigidità offerte dal telaio a cella chiusa, il Portacenter può essere una valida alternativa all’impiego dei classici centri di lavoro ISO40 monomandrino in linea, diventando la soluzione più competitiva per certe tipologie di pezzi da lavorare. Nella sua configurazione base, il Portacenter si compone di: 4 stazioni e 3 robusti moduli XYZ orizzontali in ghisa fusa con attacco utensile ISO40 o HSK63; magazzino utensili con 12 o 20 posti per modulo per un totale di 36/60 utensili; 4 tavole satellitari in continuo (360.000 posizioni), 2 o 4 mandate olio per ogni tavola satellitare; sistema di programmazione ISO standard; controllo numerico Siemens o Fanuc.
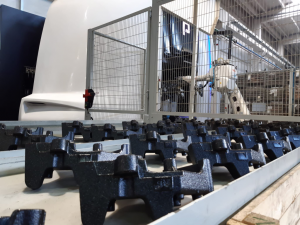
«Portacenter – sottolinea Coglio – è una macchina che si pone in una posizione intermedia tra il transfer, ad alta produttività ma scarsa flessibilità, e il centro di lavoro che paga la sua alta flessibilità con una produttività non sempre adeguata alle attuali esigenze di mercato. Essendo noi produttori terzisti, è essenziale poter disporre di macchine più flessibili che siano di facile riconfigurazione nei cambi di produzione, senza andare a penalizzare i tempi ciclo. Nell’impianto di Porta Solutions abbiamo identificato il giusto compromesso tra queste due esigenze: grazie alla collaborazione, nata tra noi e lo staff di engineering del costruttore, siamo riusciti ad adattare il centro di lavoro trimandrino affinché ci consentisse di produrre i supporti motore per veicoli pesanti con un ciclo di lavoro vantaggioso, cioè più affidabile e più competitivo rispetto alla nostra precedente esperienza su altre macchine. Oggi, il nostro Portacenter 250, asservito da un robot con funzioni di carico/scarico e di controllo intermedio/finale del pezzo, lavora su tre turni di lavoro, per 6 giorni alla settimana, più un eventuale turno domenicale. Il terzo turno non è presidiato. Il pezzo pesa circa 7 kg prima delle lavorazioni e necessita di quattro piazzamenti, di cui tre di lavoro e uno di carico/scarico. Ogni piazzamento ha due fasi di lavoro: il mandrino maggiormente sollecitato è il primo dove facciamo le più grosse asportazioni e dove la macchina dimostra la sua massima robustezza; nelle altre due stazioni eseguiamo fresature più leggere e forature. Il pezzo è bloccato molto vicino al mandrino garantendo così alta rigidità della lavorazione. Sistemi di controllo dell’usura e della rottura utensile hanno contribuito al raggiungimento di una produzione di pezzi buoni al 100%; fattore questo di assoluta importanza perché parliamo di un componente che è strutturale e che andrà su una catena di montaggio, dove non è previsto un controllo a inizio linea: eventuali interruzioni per pezzi difettosi causerebbero forti danni economici. Riteniamo che il Portacenter 250 sia stata una scelta vincente, anche in considerazione dell’efficienza del servizio di pre- e post-vendita di Porta Solutions».
Service a tutto campo
«Abbiamo molto apprezzato l’affiancamento dei tecnici di Porta Solution – conclude Coglio – che è stato continuativo fin dai primi contatti. Il loro team di engineering ha compreso tutte le nostre esigenze e ha sviluppato la configurazione più congeniale per il nostro prodotto che, peraltro, presenta delle dimensioni limite rispetto al volume utile della macchina. I tempi di consegna sono stati molto stretti, parliamo di 4-5 mesi; anche l’installazione e la formazione del nostro personale si sono rivelati semplici e rapide. La macchina utilizza una componentistica abbastanza reperibile e questo sarà favorevole nel caso dovessimo richiedere interventi di assistenza che, finora, si sono rivelati tempestivi. La produzione di questo supporto motore durerà ancora un anno circa e siamo stati già contattati dal cliente per la successiva produzione del nuovo e più grande supporto motore. Pertanto, abbiamo già coinvolto i tecnici di Porta Solutions che stanno studiando un nuovo Portacenter con prestazioni e con corse di lavoro maggiori».
di Davide Davò, Maria Bonaria Mereu ed Ernesto Imperio
Condividi l'articolo
Scegli su quale Social Network vuoi condividere