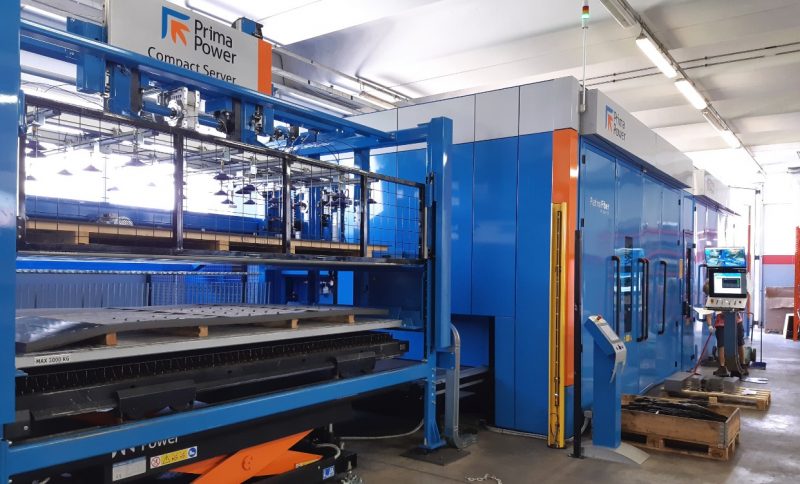
Con il progetto di una linea versatile, Prima Power è riuscita a conquistare la fiducia di Vibo, realtà vicentina sempre attenta alle innovazioni tecnologiche e che ha internalizzato il processo di taglio, punzonatura e piegatura della lamiera.
di Davide Davò
Ognuna delle migliaia di imprese che costituiscono il ricco tessuto industriale italiano si è sviluppata negli anni seguendo un proprio percorso di crescita. Una strada che ha reso ogni azienda una realtà pressoché unica nel suo genere anche se, a ben guardare, ci sono due aspetti comuni alla maggior parte delle imprese italiane. Il primo è il luogo di nascita, il tradizionale “garage sotto casa” adibito a piccolo laboratorio nel quale l’attività ha mosso i suoi primi passi. Il secondo è lo spirito che guida la crescita dell’azienda, ovvero la volontà di fare. Soprattutto nelle realtà che conservano una conduzione familiare, la volontà di fare del fondatore viene tramandata alle generazioni successive, che proseguono sulla strada tracciata facendo dell’innovazione tecnologica la propria bussola. È questo il caso di Vibo, fondata nel 1980 da Franco Bonin e dalla moglie Luisa Nardi, attualmente in azienda in qualità rispettive di presidente e amministratore delegato, ai quali si è affiancato il figlio Francesco che si occupa dell’organizzazione e della gestione dei flussi produttivi. A lui oggi spetta il compito di adottare le giuste strategie e tecnologie di produzione per mantenere Vibo ai vertici nell’ambito dei componenti interni per mobili di cucine e armadi.
Crescere come una famiglia
«Abbiamo percorso molta strada da quel piccolo laboratorio per la lavorazione del filo metallico», esordisce Franco. «All’epoca eravamo la tipica azienda contoterzista, ma negli anni il nostro approccio è cambiato, e siamo diventati noi stessi dei produttori mantenendo al nostro interno le lavorazioni, perché è rimasto in noi il piacere di seguire un oggetto mentre prende vita. Attualmente la nostra realtà ha un respiro internazionale, siamo presenti in oltre 70 Paesi del mondo con due linee distinte di prodotto. La linea cucina è composta da estraibili, meccanismi angolari, colonne, cassetti, pattumiere, scolapiatti, sottolavelli e sottopensili. Qui abbiamo soluzioni di alta gamma destinate ai più prestigiosi produttori di cucine, che integrano i nostri elementi nelle loro cucine, e da prodotti più competitivi rivolti alla grande distribuzione. La linea armadio invece si compone di telai, contenitori, appendiabiti e altri accessori. In questo caso la nostra clientela è costituita da ferramenta e dalla grande distribuzione». «Negli anni, di pari passo con l’offerta è cresciuta anche la struttura aziendale – prosegue Luisa – con lo spostamento del quartier generale dal primo capannone produttivo situato ad Arzignano (VI) al nuovo plant di Trissino (VI), all’interno del quale operano circa 220 persone e che si estende su una superficie di circa 100.000 mq dove sono presenti diversi stabili, mentre altri ne verranno costruiti a breve. Ma la crescita più grande è anche quella meno visibile dall’esterno, con il costante aggiornamento e arricchimento dei sistemi produttivi. Per filosofia aziendale infatti abbiamo progressivamente internalizzato tutte le fasi del processo, ma non solo. Abbiamo anche investito nelle tecnologie più evolute, cercando di dare il giusto spazio all’automazione, come dimostrato dagli oltre 50 robot installati e operativi nei nostri stabilimenti».
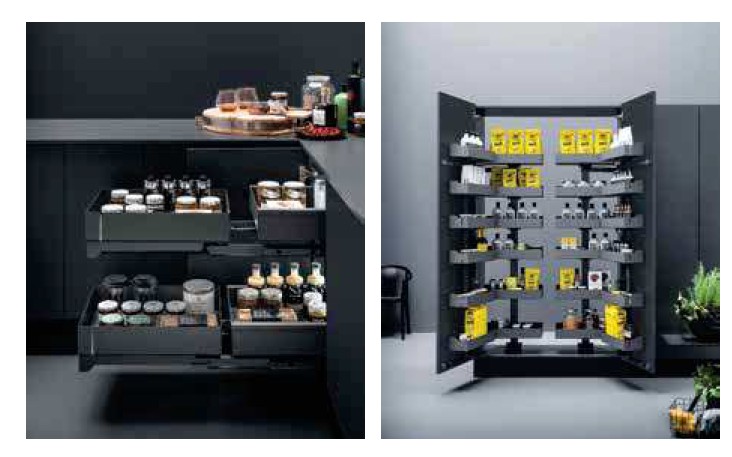
Flessibilità e automazione
«Sono diverse le motivazioni – spiega Francesco – che ci hanno spinto a portare al nostro interno le lavorazioni, a partire dalla già citata passione del fare. Con la produzione completamente al nostro interno infatti possiamo garantire un migliore controllo di tutte le fasi del processo e delle singole lavorazioni, arrivando così a realizzare un prodotto di elevata qualità. La nostra struttura aziendale a carattere familiare ci rende reattivi nelle decisioni da prendere, mentre il controllo di tutta la filiera ci svincola dalle tempistiche dei fornitori esterni e ci consente di rispettare le scadenze. Considerando che complessivamente gestiamo circa 95.000 codici di semilavorati, che diventano 4500 codici prodotto, è evidente l’importanza di avere sempre tutto sotto controllo». Molti di questi semilavorati sono elementi metallici, quindi fili, tubi o lamiere, che vengono tagliati, piegati e saldati prima di passare alle operazioni di cromatura e verniciatura, mentre la fase finale del processo prevede attività di assemblaggio e spedizione del prodotto finito. La lavorazione della lamiera in particolare rappresenta un’attività avviata di recente, quando tra fine 2017 e inizio 2018 Vibo ha deciso di internalizzare anche questa fase del processo. «Noi avevamo grandissima esperienza nella lavorazione del filo – afferma Francesco – e poca esperienza relativamente al tubo ma nessuna per quanto riguarda la lamiera. Nonostante questo, volevamo partire già con un impianto di produzione completo e tecnologicamente evoluto, il più possibile automatizzato e pensato anche nell’ottica di futuri ampliamenti della linea. Per questo motivo abbiamo avviato un lungo dialogo con i principali fornitori di tecnologie per la lavorazione della lamiera, e al termine di sette mesi di incontri, abbiamo scelto il progetto che ci è stato proposto da Prima Power».
Aperti al domani
La soluzione sviluppata da Prima Power si è dimostrata vincente sotto molteplici punti di vista, a partire dalla versatilità delle macchine. «La nostra attività si basa su tanti lotti medio-piccoli – continua Francesco – di componenti a loro volta di piccole dimensioni. Avevamo quindi bisogno di macchine taglio laser e di piegatrici della taglia più adatta e soprattutto versatili, per ridurre al minimo il fermo macchina nel passaggio tra un lotto e quello successivo. In quest’ottica anche i sistemi di automazione dovevano essere flessibili e capaci di adattarsi alle nostre esigenze in termini di spazio a terra disponibile. Inoltre, considerando il fatto che ci stavamo muovendo in un terreno per noi inesplorato, avevamo bisogno di un partner che ci indicasse la giusta tecnologia in termini di taglio laser scegliendo tra sorgenti fibra e CO2. Ci siamo fidati delle indicazioni dateci da Prima Power, che ci ha caldamente suggerito la tecnologia laser fibra, e con il senno di poi possiamo dire che è stata una scelta vincente, una torretta molto flessibile e un interessantissimo robot a portale (LSR) che su tre livelli sovrapposti gestisce il carico del grezzo, lo scarico con pallettizzazione ordinata del prodotto finito e l’evacuazione della griglia residua con una minimizzazione dell’ingombro a terra. Infine ci tengo a sottolineare l’apertura mentale di Prima Power e la loro predisposizione a tenere in considerazione anche eventuali sviluppi futuri del progetto della linea, come la possibile integrazione di altre macchine o sistemi di automazione più complessi. Un aspetto importante per un’azienda come la nostra in costante evoluzione». La prima versione della linea di produzione installata presso Vibo era composta da una macchina combinata laser/punzonatura Combi Genius CG 1530 con sorgente CF 3000 di Prima Power e con LSR e da due pressepiegatrici elettriche, una eP1030 e una eP0520, a cui due anni più tardi si sono aggiunte una macchina per il taglio laser Platino Fiber PLf 1530 (nella foto in alto) con sorgente CF 4000 dotata di automazione di carico/scarico CS e robot per lo scarico e impilamento dei pezzi tagliati LST e una terza pressapiegatrice elettrica eP0520, saturando di fatto gli spazi al momento disponibili.
Standard, ma su misura
In particolare Combi Genius è equipaggiata con sorgente da 3 kW e può lavorare fogli da 3.000×1.500 mm. Assicura elevate produttività e flessibilità con tempi minimi di setup, e consente quindi un rapido passaggio da un lotto a quello successivo. Inoltre è completata con il sistema robotizzato LSR che permette di automatizzare le operazioni di carico della lamiera e scarico del pezzo finito. Il robot permette la pallettizzazione del pezzo singolo, semplificando l’attività di gestione dei lotti e migliorando la tracciabilità dei pezzi. Passando alla piegatura, le pressepiegatrici serie eP garantiscono altissima precisione e ripetibilità grazie alla tecnologia servoelettrica, grandi velocità di risposta e sono progettate per mantenere la massima velocità di discesa dei punzoni fino a pochi mm dal pezzo da piegare. Le due presse eP 1030 hanno una forza di piegatura di 100 t e una lunghezza utile di 3 m, mentre la più piccola eP 0520 ha 50 t di spinta e lunghezza di 2 m. Nell’ottica di futuri sviluppi, Vibo sta già pensando a come abbinare un robot anche a queste macchine, automatizzando almeno in parte anche la fase di piegatura dei pezzi. A completamento dell’attuale parco macchine della realtà vicentina figura la macchina laser fibra Platino Fiber 1530 con LST dotata di sorgente, testa e software di gestione dei parametri di lavoro studiati per garantire un taglio di elevata qualità su qualsiasi materiale e spessore lavorato presso Vibo. In aggiunta, la macchina è completata con il sistema di automazione LST, compatto e ideale per una produzione diversificata grazie alla capacità di organizzare al meglio i pezzi finiti da scaricare, che vengono impilati in automatico per una gestione ottimale del flusso di materiale. Infine abbiamo una automazione CS per il carico del foglio grezzo e lo scarico della griglia residuale. «Un aspetto che abbiamo grandemente apprezzato di Prima Power – conclude Francesco – è che questa linea è stata costruita su misura per le nostre esigenze, ma non è una soluzione “speciale”. Grazie a una mentalità aperta e a macchine e automazioni flessibili, Prima Power è in grado di utilizzare soluzioni standardizzate per rispondere a specifiche richieste non solo in termini di tecnologia, ma anche di layout».
Condividi l'articolo
Scegli su quale Social Network vuoi condividere