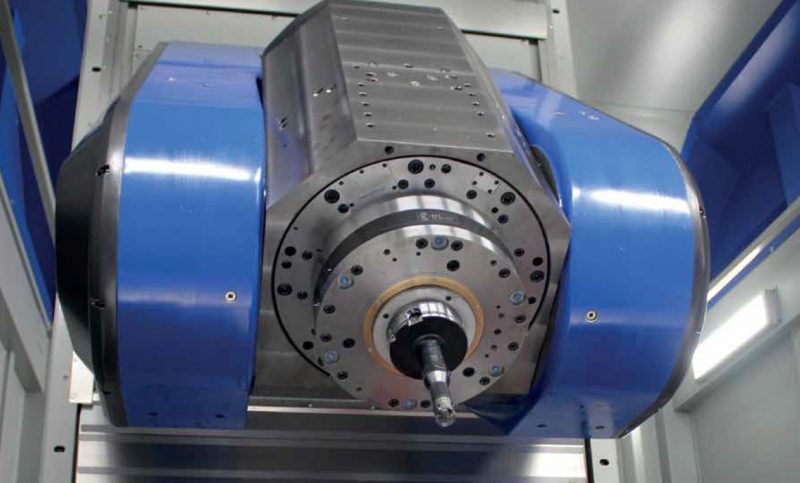
L’innovativa linea dei centri di lavoro Spark di Mandelli Sistemi si completa con la taglia 1200, nata per rispondere al concetto di flessibilità assicurando, al contempo, elevate prestazioni sia in tornitura che in fresatura anche grazie a una tavola annegata nel basamento, garanzia di alta precisione.
di Davide Davò e Flavio Della Muzia
Due tecnologie complementari integrate in una sola macchina. È la complessa sfida accettata da Mandelli Sistemi di mettere a punto una soluzione ibrida di tornitura e fresatura all’interno di un unico centro di lavoro, capace di assicurare performance del tutto sovrapponibili ai tradizionali impianti concepiti per le due singole operazioni ad asportazione di truciolo. Una sfida affrontata e vinta con la linea d’impianti Spark cui si aggiunge oggi la taglia più piccola, Spark 1200, frutto dell’esperienza e delle conoscenze maturate nel settore della costruzione di centri di lavoro da una realtà presente sul mercato sin dal lontano 1932.
Tradizione innovativa
Dalla realizzazione delle prime macchine utensili Positiv, Medal e Thema alla costruzione del primo esemplare con caratteristiche fondamentali per un centro di lavoro, Ego, fino ai moderni e innovativi CNC e sistemi d’automazione industriale la società, con sede a Piacenza, è divenuta partner affidabile e autorevole per una moltitudine di clienti sparsi in tutto il mondo, verso i quali rivolge le proprie risorse al fine di promuovere lo sviluppo della tecnologia del domani. Con una rete di vendita ramificata in tutta Europa, e due filiali nei mercati strategici nordamericano e cinese, Mandelli Sistemi si rivolge a settori come l’aeronautico, l’energia / oil & gas e la meccanica di precisione sviluppando, progettando e realizzando al proprio interno impianti molto versatili adatti a diverse applicazioni, capaci di evolvere nel tempo con l’implementazione di sempre nuove funzionalità, frutto di una costante evoluzione tecnologica dei sistemi proposti. Soluzioni come la nuova Spark 1200, il cui concetto filosofico trae spunto dall’impostazione che l’azienda ha dato a questa linea per quanto concerne la possibilità di lavorazioni in tornitura e fresatura. «Questa gamma comprendeva già i modelli 1600 e 2100 (con il nome a indicare il diametro del pezzo che la macchina può gestire), pensati in maniera rivoluzionaria: infatti, la nostra è stata la prima azienda, nel 1991, a realizzare un tornio/fresa sulla base di un centro di lavoro orizzontale con l’allora Mandelli 8UT», ci spiega Marco Colombi, direttore commerciale di Mandelli Sistemi. «Dopo 25 anni d’esperienza abbiamo fatto tesoro degli insegnamenti, arrivando a dedicare un’architettura specifica proprio a quelle macchine che possono fare sia tornitura, che fresatura. La specificità di questo sistema consiste nel fatto di avere la tavola fissa, con il solo movimento rotatorio, mentre tutti gli assi lineari si trovano sul lato utensile: questo consente, in tornitura, di avere le performance proprie di un tornio grazie alla tavola annegata nel basamento, che garantisce la massima stabilità e robustezza dell’impianto, dunque grande precisione».
Efficienza in ogni produzione
La decisione da parte della società di realizzare la più piccola Spark 1200 nasce dalla necessità sempre più diffusa, in particolar modo nell’ambito delle pro duzioni medio-piccole, di poter contare su un alto grado di flessibilità in aggiunta all’efficienza produttiva. Oggi il mercato chiede non tanto la massima efficienza solo in fresatura o in tornitura, quanto la possibilità di lavorare in maniera flessibile, non facendo magazzino e potendo riconfigurare rapidamente la propria produzione. In quest’ottica la tendenza a concentrare sempre più tecnologia all’interno del medesimo mezzo produttivo aiuta molto durante i processi di lavorazione: infatti, se oggi si dovesse realizzare un pezzo che richiede un 30% di fresatura e il restante di tornitura, mentre domani le percentuali si dovessero ribaltare, con l’utilizzo di tecnologie tradizionali si potrebbero rischiare pesanti perdite in termini d’efficienza. «Con la linea Spark, invece, proprio in virtù della grande flessibilità intrinseca alla soluzione che c’è alle spalle l’efficienza viene garantita anche con variazioni della tipologia di produzione. Limitare il numero di volte in cui i pezzi vengono movimentati, quindi, riduce la possibilità di errore e aumenta la precisione, con tutti i vantaggi della produzione combinata», prosegue Colombi. «In questi ultimi tempi abbiamo percepito che il mercato, anche su particolari di dimensioni più contenute (attorno al metro di diametro), cerca una reattività immediata e una flessibilità più elevata possibile. Così, con 70 kW al mandrino in tornitura e altrettanti a quello in fresatura, il volume del truciolo che si riesce a realizzare è ai livelli di quello tipico dei torni o delle fresatrici tradizionali».
Prestazioni…
Declinando le caratteristiche della nuova Spark 1200 sul campo, è interessante evidenziare un’applicazione sviluppata da Mandelli Sistemi per un cliente del comparto aeronautico impegnato nella costruzione di propulsori, uno degli ambiti per i quali questa taglia d’impianto è stata concepita. All’interno dello stabilimento produttivo sono stati installati due centri di lavoro Spark 1200 finalizzati alla realizzazione di anelli di tenuta, del diametro di 900 mm e spessori variabili da 1 a 2 mm, destinati a equipaggiare i motori LEAP (Leading Edge Aviation Propulsion) dei velivoli per il trasporto passeggeri di medie dimensioni.
«In questa commessa erano due le principali esigenze del cliente, ossia un’estrema precisione, dell’ordine dei 15 micron nel posizionamento dei fori sulla flangia, oltre che la possibilità di lavorare materiali particolarmente tenaci, dato che questi anelli devono fare tenuta ai gas caldi in movimento durante la combustione e l’espansione in turbina», illustra Colombi. «Qui val la pena citare una tecnologia che s’è dimostrata molto efficiente in particolar modo nella tornitura di questi materiali, ovvero la lavorazione con refrigerante in alta pressione, fino a 350 bar, al fine di spezzare il truciolo e raffreddare in maniera molto efficace la zona del taglio».
Per questo tipo di applicazione Mandelli Sistemi ha addirittura brevettato una soluzione con guarnizioni di tenuta innovative, che permettono di fare passare il refrigerante attraverso le spalle della testa operatrice senza applicare tubi esterni, normalmente fonte d’ingombro e pericolosi punti d’aggancio del truciolo. Da sottolineare che nel campo aeronau tico, se un tempo c’era molta attenzione alla soluzione tecnica e leggermente in secondo piano al costo della soluzione stessa, oggi invece le due esigenze sono paritetiche, dunque serve sempre più automazione nelle lavorazioni non presidiate. Il controllo del truciolo diventa quindi fondamentale, con la necessità di produrre uno sfrido di spessore sottile che possa essere spezzato dall’alta pressione della lubrificazione per non interferire con le operazioni di tornitura e fresatura.
…e flessibilità
Un’altra interessante applicazione che ha visto protagonista la Spark 1200 è stata realizzata per un cliente impegnato nel comparto della costruzione di impianti per l’industria alimentare. La ditta Sancassiano, in provincia di Cuneo, che realizza macchine impastatrici, aveva l’esigenza di lavorare acciai inox difficili da processare destinati alla costruzione di pezzi di spessore sottile e piuttosto cedevoli. «La tecnologia che ha convinto il cliente è stata quella del fine tuning automatico dei parametri di funzionamento, contenuta nel nostro pacchetto iPum@smartcut destinato all’Industria 4.0. Tale soluzione permette alla macchina di riconoscere una situazione di vibrazioni non sotto controllo che potrebbero mettere in serio pericolo l’integrità dell’utensile, danneggiare il pezzo e magari anche l’impianto, cambiando opportunamente le frequenze di funzionamento in modo da trovare un assetto stabile di lavorazione», prosegue Colombi. «Questi pezzi destinati alle impastatrici, dalla forma un po’ particolare, non si prestavano a essere irrigiditi e quindi, entrando in stabilimento, si percepivano subito i rumori delle vibrazioni delle macchine: veniva quindi affidata alla sensibilità dell’operatore la regolazione dell’override per trovare il settaggio corretto. Con l’utilizzo del nostro sistema iPum@smartcut, dotato di accelerometri e di un pacchetto software in grado di interpretare e cambiare il regime di funzionamento del centro di lavoro, il cliente potrà così affrontare con tranquillità le lavorazioni anche in modalità non presidiata».
Tra i componenti lavorati sulla Spark 1200 figurano anche i meccanismi del cinematismo principale di mixaggio delle macchine impastatrici. Si parla in particolare di tamburi con albero di 100 mm di diametro ottenuti in un pezzo unico con tamburi di 800 mm di diametro. La possibilità di tornire in un’unica macchina questi pezzi è legata alla capacità della tavola di tornitura di raggiungere importanti velocità di rotazione abbinata a un’elevata rigidezza che assicura la lavorazione di pezzi molto pesanti in totale sicurezza. «In questa applicazione, Spark 1200 ha risposto alle esigenze produttive di oggi – conclude Colombi – e si allinea alla visione del domani da parte del management di Sancassiano, sempre attento alle innovazioni tecnologiche come dimostrato dall’interesse manifestato per la cella con tecnologia AM (Additive Manufacturing) da noi sviluppata».
Condividi l'articolo
Scegli su quale Social Network vuoi condividere