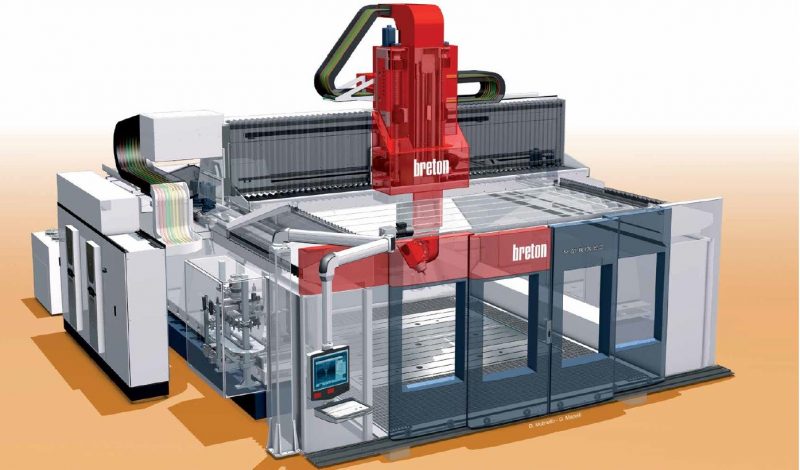
Con il lancio di Matrix E3, viene completato il rinnovamento della gamma Matrix di Breton. Nasce così una piattaforma tecnologica che permette di passare dal concetto di officina composta da più macchine a una macchina con le molteplici funzioni di un’officina.
di Andrea Pagani
La gamma Matrix è la linea storica di Breton, utilizzata in ambiti applicativi dove è richiesta alta precisione su dimensioni del pezzo che vanno da medie a molto grandi. Questa tipologia di macchine permette di combinare la robustezza e la spinta necessaria nelle fasi di sgrossatura con la dinamica e la precisione richieste nelle fasi di finitura. È grazie a queste caratteristiche che Matrix è la serie ideale per settori quali automotive (prototipazione ad alta precisione, stampi e strutture in composito), aerospace (lavorazione di strutture e attrezzature), la stampistica di grandi dimensioni e la meccanica generale di precisione. È una gamma che prevede per ogni macchina un pacchetto dedicato a una specifica combinazione di settore-materiale da lavorare. In questo modo Breton offre una soluzione su misura a seconda che si tratti di una lavorazioni wet o dry su materiali compositi, su alluminio, su acciaio o su superleghe.
Da centro di lavoro a piattaforma
Più che un centro di lavoro è infatti una vera e propria piattaforma: una base stabile e robusta ma allo stesso tempo estremamente dinamica, configurabile con un’ampia gamma di componenti e accessori con l’obiettivo di eseguire interi processi lavorativi in molteplici settori. Si va ad analizzare nei dettagli le specifiche esigenze del cliente, soddisfacendo le richieste più comuni fino a proporre i più avanzati sistemi come il controllo automatico dello spessore, taglio a ultrasuoni, laser per la scansione dei pezzi e software sviluppati per Industria 4.0. Matrix E3 non è solo adattabile in fase di configurazione, ma lo è anche successivamente, permettendo eventuali aggiornamenti ed espansioni in un secondo momento. In un periodo storico nel quale avere certezze è un plus, i clienti possono trovare nell’intera gamma Matrix la scelta ideale per le esigenze odierne come anche per quelle future.
Nativa digitale
Anche Matrix E3, come altri prodotti Breton, nasce sfruttando tutti i vantaggi del gemello digitale, reso possibile dall’utilizzo delle nuove funzionalità del controllo numerico Sinumerik One di Siemens. L’approccio che ha permesso di creare Sinumerik One, dapprima tutto in digitale per poi dar forma all’elettronica e all’hardware, è lo stesso utilizzato anche per lo sviluppo della Matrix E3: all’interno di un ambiente virtuale sono state inserite tutte le caratteristiche della macchina, incluse quelle dei vari componenti forniti da terzi (viti a ricircolo di sfere, cuscinetti, motori e così via) al fine di ottenere una simulazione quanto più possibile realistica e verificarne il comportamento nei vari scenari di utilizzo. Il risultato è una struttura costruita sulla base delle simulazioni che ha permesso una ottimizzazione mirata volta a incrementare le performance dei componenti più critici. Con questo tipo di attività si vanno a individuare in anticipo eventuali punti deboli e si trovano le soluzioni ancora prima di chiudere il progetto “su carta”. Il gemello digitale può essere utilizzato anche a valle dai clienti di Breton, simulando il processo lavorativo della macchina e operando tutte le modifiche per far sì che sia il più efficiente possibile.
Modulare e flessibile
Dopo aver rinnovato gli altri modelli della famiglia (Matrix 800 nel 2019, ora denominata Matrix E1, e Matrix 1000 nel 2018, adesso chiamata Matrix E3) è ora il turno della più grande Matrix E3. All’interno della gamma si posiziona al vertice per volume di lavoro gestibile essendo configurabile in varie opzioni dimensionali: l’asse Z può avere una corsa di 1300 o 1500 mm, in Y la corsa del carro è di 3000 o 4000 mm, mentre l’asse X parte da 3 m e sale a 4, 6 e 8 m per poi proseguire a step di 2 fino a 30 m totali, particolarmente utili nel settore aerospace o per organizzare lavorazioni in pendolare. Nelle configurazioni con corsa asse X lunghe, può montare una doppia trave per lavorazioni in pendolare, così come tavole rotanti per il posizionamento pezzo ma anche per operazioni di tornitura, sistemi per il cambio teste e predisposizione per la doppia accessibilità (fronte e retro macchina).
Tanta la potenza a disposizione sulle diverse teste compatibili, tutte Direct Drive e di produzione interna Breton. È possibile scegliere tra le due teste ortogonali, Typhoon e Typhoon HD che permettono di montare mandrini fino a 200 Nm in S1 e utensili HSK-A100. Entrambe le versioni sono dedicate principalmente al mondo degli stampi per la migliore capacità di penetrazione in forme complesse.
Per quanto riguarda le teste a forcella si può scegliere tra la Phoenix e la Tornado. Eccezionale è la versatilità della macchina grazie ai sistemi automatici di cambio testa che permettono l’utilizzo di diversi elettromandrini. Da segnalare che sulle versioni equipaggiate con le teste Typhoon o Typhoon HD è inoltre possibile richiedere il sistema di cambio della sola cartuccia elettromandrino. Vasta la gamma di elettromandrini a disposizione dell’utilizzatore, con coppie da 62 a 200 Nm in S1 e regimi di rotazione da 14.000 a 28.000 giri/min.
Robustezza a prova di asportazione
Anche nei reparti produttivi interni di Breton è all’opera da qualche mese una nuova Matrix E3 che esegue importanti lavorazioni su strutture in acciaio e carpenterie che in precedenza venivano realizzate su macchine a portale mobile, estremamente rigide ma sensibilmente più lente e molto limitate in termini di bloccaggio degli assi rotativi e orientamento del campo di lavoro. I dati evidenziano una riduzione dei tempi di esecuzione a parità di precisione, infatti grazie all’elevata dinamica e ai 5 assi interpolati, che permettono di lavorare il pezzo in maniera più produttiva, si arriva ad asportare fino a 600 cm3/min su acciaio da stampi. Il vero vantaggio però è avere in un unico serraggio tutte le fasi: sgrossatura, semi-finitura, finitura, misurazione, controllo e verifica della superficie. Come sono state raggiunte queste prestazioni?
Il rischio è infatti quello di innescare una progressione nociva tra motori sovradimensionati, sistemi di raffreddamento adeguati, strutture sovrabbondanti e così via. Con un’attenta progettazione e l’ottimizzazione strutturale supportata dai dati simulati con il ge mello digitale, si è riusciti a combinare tutte le caratteristiche che permettono a una macchina utensile di operare con elettromandrino ad alta asportazione su materiali tenaci ma anche a mantenere quell’agilità che contraddistingue i prodotti idonei alla superfinitura come anche al raggiungimento di tolleranze elevate. Sugli assi lineari i tecnici Breton hanno scelto di impiegare motori tradizionali e non motori lineari i quali, pur essendo potenzialmente più veloci, in pratica offrono minor spinta quando si tratta di fare molto truciolo. Inoltre, dispongono di poca coppia e necessitano di impianti di raffreddamento adeguati per il loro impiego, con evidenti costi in fase di acquisto e consumi durante l’intera vita utile della macchina.
MatrixE3 sfrutta la potenza e la precisione dei motori Dual Drive, due motori che si muovono insieme per avere la massima spinta quando la lavorazione richiede uno sforzo importante, mentre lavorano “in precarico” quando la macchina effettua lavorazioni ad alta precisione. Inoltre, per gestire il calore generato, i motori sono posizionati sui bordi esterni delle strutture: in questo modo il calore in aria libera si allontana dalla macchina, non creando nessun tipo di sbalzo termico sulle strutture e rendendo superflui i sistemi di raffreddamento dei motori con benefici palesi in bolletta per il cliente.
Il RAM più “pulito” di sempre
Un nuovo approccio ha permesso di sviluppare l’asse Z mantenendo il campo di lavoro privo di componenti che vadano a interferire con il pezzo in lavorazione, rendendo quindi il volume di ingombro del RAM uguale a quello della testa. Si tratta di un dettaglio molto utile sia nel mondo degli stampi, dove sono richieste operazioni particolari in spazi ridotti o in punti difficili da raggiungere, che su pezzi profondi di altri settori dove si richiede di penetrare con una parte del RAM. L’altro vantaggio importante è dato dalla pulizia delle componenti. Con un RAM costruito in questo modo non ci sono parti in cui trucioli e polveri possono depositarsi causando problemi o riduzione della precisione. Rispetto ad altre macchine, quindi, non è necessaria la pulizia di queste parti. La movimentazione dell’asse verticale è ottenuta da un sistema a doppia vite a ricircolo di sfere e doppia guida, posizionate simmetricamente all’asse del RAM in modo da annullare ogni minima distorsione, mentre su carro e gantry è presente un sistema con doppio pignone e cremagliera con precarico elettronico.
Dinamica e controllo della temperatura per la finitura
Per garantire superfici perfette in finitura anche la Matrix E3 sfrutta la tecnologia High Dynamics di Breton. Questa soluzione porta all’eliminazione dei fattori di attrito per ottenere ancora più jerk, accelerazioni e velocità, migliorando sia la precisione che la qualità della superficie in fase di finitura del pezzo. Un altro aspetto che ha un forte impatto sulla precisione della macchina e sui relativi costi di gestione è la climatizzazione del volume di lavoro. Breton ha risolto questa problematica impiegando un sistema di isolamento termico passivo. Il ThermalShield, soluzione brevettata Breton, isola termicamente il campo di lavoro grazie a un “cappotto” che mantiene costante la variazione di temperatura della macchina e riduce le distorsioni geometriche. Che si tratti dei motori o del campo di lavoro, è infatti fondamentale mantenere la temperatura costante (erroneamente talvolta si pensa sia necessario climatizzare tutta la macchina), altrimenti si corre il rischio di avere l’ambiente fresco e il pezzo caldo, con evidenti scompensi. ThermalShield allunga molto il transitorio delle temperature fungendo da vero e proprio “volano termico”. La macchina è così in grado di stabilizzarsi autonomamente grazie all’uso di piccole ventole che si occupano della omogeneizzazione dell’aria all’interno delle strutture. Se da un lato le temperature della macchina sono stabilizzate con diversi sistemi, molti dei quali passivi, è comunque importante monitorarle per evitare qualsiasi sbalzo. Sono infatti presenti, oltre ai sensori già previsti nei motori e negli azionamenti, anche altri dispositivi che consentono di rilevare i dati e di intervenire in maniera trasparente per l’operatore. Gli accelerometri verificano in tempo reale le condizioni operative in base alle vibrazioni rilevate, facendo anche da “scatola nera” per verificare eventuali collisioni in fase di lavorazione.
Sono i costi operativi a fare la differenza
Nel ciclo di vita di un centro di lavoro il costo sostenuto dal cliente è composto da due parti: il costo iniziale di acquisto e il costo operativo. Se il primo è ben evidente nel momento dell’acquisto il secondo è molto difficile da valutare, ma non per questo è meno importante. Nei molti anni che una macchina rimane operativa ogni euro risparmiato sul costo orario diventa estremamente importante. Per questo motivo Breton ha spostato l’attenzione su questo secondo tipo di costo, eliminando tutti i sistemi superflui della macchina o cercando soluzioni apparentemente più costose ma che portano risparmi nell’utilizzo. Da questa filosofia derivano scelta come la stabilizzazione termica statica (data dal ThermalShield, dalle strutture termosimmetriche e dal posizionamento periferico dei motori e dall’eliminazione del relativo sistema di raffreddamento), dal rinnovato sistema idraulico che sfrutta tutti i vantaggi della nuova centralina Rexroth CytroPac, da un nuovo sistema di lubrificazione che semplifica moltissimo tutto l’impianto a parità di prestazioni e da molti altri piccoli interventi che vanno a limare sia il consumo orario della macchina, sia i costi di manutenzione e ricambistica.
Più opzioni, più scelta
Sempre per offrire una piattaforma configurabile, vengono messe a disposizione numerose opzioni di personalizzazione: teste e relative motorizzazioni, sistemi di misurazione laser, tastatori pezzo di diverso tipo, cambio pallet frontale, posteriore o integrato in un FMS esistente, tavole rotanti, magazzini utensili da 30 fino a 300 posti, software per Industria 4.0 e soluzioni per la lavorazione in pendolare, ma anche tecnologie meno convenzionali come la testa per il taglio a ultrasuoni dei materiali aeronautici (honeycomb), i sistemi di controllo ultrasonico dello spessore, l’aspirazione polveri per la lavorazione a secco del carbonio e così via. È infine possibile configurare Matrix E3 in modalità dual bridge, una soluzione molto utilizzata in ambito aeronautico per lavorare con due macchine in due punti distanti di particolari molto lunghi oppure per gestire due pezzi diversi. Matrix E3 è disponibile sia con il controllo numerico Heidenhain serie 640 che con il nuovo Siemens Sinumerik One. Inoltre, sfruttando un tablet in modalità realtà aumentata, è possibile osservare la macchina con evidenziati gli interventi da effettuare. Tutto questo è parte del pacchetto software Breton chiamato SmartDoc.
5 motivi per scegliere Matrix E3
Ecco un piccolo prontuario tecnico-commerciale:
1 – Perché è una piattaforma tecnologica e non solo un centro di lavoro
2 – Per l’elevata capacità di asportazione del materiale
3 – Per la precisione e la qualità delle superfici in finitura
4 – Per i ridotti costi operativi
5 – Perché è modulare e scalabile sia in fase di acquisto, sia in seguito
Un progetto agile
Come per gli ultimi modelli lanciati, anche Matrix E3 ha beneficiato dell’approccio cosiddetto agile. Si tratta di una vera e propria “fabbrica nella fabbrica”, che permette di ridurre i tempi di realizzazione. Vengono create delle startup interne che operano in maniera – appunto – agile e autonoma per sviluppare quei prodotti e quelle tecnologie che poi verranno utilizzate sui nuovi modelli. Slegati dalle attività quotidiane dell’azienda, i tecnici possono così concentrarsi completamente sul proprio progetto e portarlo a termine in tempi ridotti; ogni 15 giorni circa vengono monitorati gli sviluppi, aggiornate le caratteristiche, effettuate riunioni con il resto della “fabbrica” per contribuire a migliorare le tecnologie oggetto dello sviluppo. Ma perché utilizzare un simile approccio? Innanzitutto per la riduzione del time to market: è possibile infatti raggiungere gli obiettivi imposti e immettere sul mercato i nuovi modelli in minor tempo. Obiettivi che includono sia performance maggiori, sia un uso più parsimonioso delle risorse. La nuova MatrixE3 riesce infatti, pur costando meno dei precedenti modelli, a lavorare consumando meno energia e con maggiori prestazioni.
Condividi l'articolo
Scegli su quale Social Network vuoi condividere