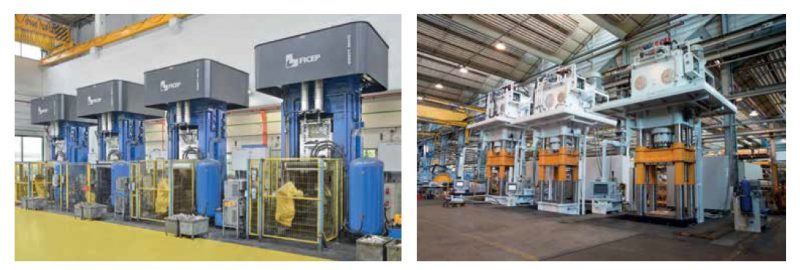
L'azienda risponde alle esigenze del settore della forgiatura con un portafoglio prodotti che si compone di tutte le tecnologie necessarie per lo sviluppo di una linea completa, dal taglio delle barre alle presse per lo stampaggio a caldo. La punta di diamante di questo portafoglio è la serie di presse DD (Direct Drive).
di Davide Davò
Ottenere pezzi finiti in un solo colpo e senza scarto. È questa la massima aspirazione delle aziende che realizzano componenti attraverso il processo di forgiatura. Un obiettivo certamente di alto livello, questo, influenzato anche da condizioni di lavoro difficilmente controllabili come per esempio la temperatura del pezzo, oppure fattori ambientali come l’umidità presente nell’aria, che possono alterare il funzionamento stesso della pressa. Senza contare l’evoluzione dei materiali da stampare a caldo, diventati sempre più ad alte prestazioni e che richiedono di conseguenza impianti all’altezza del compito.
Nel corso degli anni si sono susseguite innovazioni tecnologiche che hanno permesso alle presse a vite di adeguarsi di volta in volta alle esigenze del mercato, esigenze legate soprattutto alla qualità del pezzo e all’efficienza del processo. In quest’ottica, una delle più recenti evoluzioni è rappresentata dalla linea di presse Direct Drive sviluppate da Ficep, la cui ultima versione è caratterizzata dalla presenza di un sistema per il recupero dell’energia che contribuisce a un’importante riduzione dei consumi di macchine storicamente molto energivore.
Dalla frizione al Direct Drive
«Ficep produce presse a vite da diversi decenni, e abbiamo quindi una lunga esperienza in questo ambito», esordisce Carlo Maffei, Area Sales Manager per gli impianti di forgiatura di Ficep. «Analizzando le criticità che emergevano durante le varie sfide da noi affrontate, ci siamo resi conto che le tradizionali presse a vite con frizione non garantivano risultati costanti nel tempo proprio perché la frizione in cuoio era soggetta a usura e all’effetto di fattori ambientali. Inoltre, su tali impianti era presente un numero di componenti decisamente elevato che rendeva l’attività di manutenzione tutt’altro che semplice. Abbiamo quindi avviato uno studio che ci ha portato ad affrontare il settore della forgiatura con una nuova linea di presse senza frizione. Si tratta della linea DD (Direct Drive), che presenta anzitutto un’architettura più semplice, con meno componenti in quanto tutta la parte legata alla trasmissione del moto è stata eliminata. Come suggerisce il nome infatti è il motore brushless ad azionare direttamente la vite: controllandolo tramite software possiamo regolarne la velocità e gestirlo sia come motore che come freno, anche se sarebbe più corretto usare il termine “generatore di corrente”».
Combinando l’azione dei magneti permanenti del motore brushless e il controllo della tensione tramite software, è infatti possibile controllare la velocità di rotazione della vite, che determina anche la velocità di discesa della mazza e di conseguenza l’energia cinetica di cui dispone la mazza stessa nel momento in cui colpisce il pezzo forgiandolo. Tale controllo è un aspetto chiave nel processo di forgiatura, poiché è proprio la quantità di energia che la mazza trasferisce al materiale grezzo a determinare quanto verrà deformato e di conseguenza anche il livello di precisione del pezzo finito.
Precisione ed efficienza
«Il sistema Direct Drive opera come un controllo numerico, poiché è sufficiente impostare il valore della velocità che deve avere la mazza al momento dell’impatto e il sistema in automatico interviene durante la discesa per accelerare o rallentare la caduta dello stampo», prosegue Maffei. «Per dare un’idea del livello di affidabilità di processo che riusciamo a garantire è sufficiente un dato: grazie all’elettronica fornitaci da Siemens assicuriamo una precisione dello 0,5% sul valore dell’energia della mazza a fine caduta. Un risultato raggiunto grazie anche all’eliminazione di tutta la parte di trasmissione del moto, che influiva in modo importante sulla variabilità del processo e contemporaneamente ci ha permesso di semplificare l’attività di manutenzione della pressa. Ovviamente sono state introdotte una serie di migliorie in varie parti della macchina, tra le quali i nuovi profili di vite e chiocciola per ridurne l’attrito, e l’utilizzo di nuovi motori più compatti con efficienza migliorata».
La stretta collaborazione con Siemens e la volontà di apportare costanti migliorie alle proprie soluzioni ha portato Ficep a sviluppare in tempi recenti una nuova versione delle presse DD che si contraddistingue per la presenza del KERS (Kinetic Energy Recovery System) per il recupero di parte dell’energia utilizzata durante la forgiatura. Sfruttando un secondo motore brushless più compatto ma ad altissima velocità di rotazione, l’energia che normalmente verrebbe persa per frenare la macchina viene immagazzinata per essere riutilizzata nel ciclo successivo, con un risparmio energetico complessivo che in determinate condizioni raggiunge il 60%. «Il fatto di poter regolare finemente la velocità della mazza e di poterne variare la corsa rende queste macchine estremamente versatili e appetibili per molti settori applicativi», spiega Maffei. «Abbiamo un portafoglio completo da questo punto di vista, che copre tutte le taglie. Le presse DD infatti trovano applicazione nell’ambito automobilistico, delle macchine agricole e movimento terra, dove una fetta importante è dedicata alla produzione dei semiassi dei mezzi pesanti. Nell’aerospace e nella produzione di energia, l’elevata resistenza delle leghe di titanio, alluminio e acciai speciali per alte temperature richiede importanti forze di stampaggio, e quindi le nostre macchine a elevata rigidità strutturale si dimostrano particolarmente idonee alla forgiatura di componenti per questi settori. In ambito petrolchimico si adottano presse importanti per la lavorazione di flange in acciai speciali duplex e superduplex, nei quali sono presenti leganti che ad alte temperature perdono le proprie caratteristiche e di conseguenza impongono la lavorazione del grezzo a temperature più basse di quelle tipiche del processo di forgiatura, con forze ed energie più elevate. Infine, possiamo vantare anche un grandissimo successo nel settore delle protesi medicali, e in questo caso parliamo delle taglie medio-piccole».
Idrauliche e meccaniche
Parallelamente alle presse DD, Ficep ha sviluppato altre linee di prodotto per completare l’offerta di tecnologie nell’ambito della forgiatura. Nascono così le presse idrauliche della serie HF declinate in due versioni: la serie con struttura elettrosaldata e la serie 4C a 4 colonne. Le presse con struttura monoblocco elettrosaldata vantano un’elevata rigidità con una naturale predisposizione a lavorare fuori asse e con stampi multipli; oltre a essere impiegate nella fase di tranciatura possono anche operare come presse per la forgiatura vera e propria, qualora le forze in gioco non siano particolarmente elevate. La soluzione a 4 colonne è particolarmente adatta per l’esecuzione di preformature raggiungendo un duplice obiettivo: oltre a eseguire una prima deformazione del materiale, permettendo alla successiva pressa di forgiatura di completare il pezzo impiegando meno energia, compie anche un’azione meccanica con la quale viene rotta ed eliminata la scoria che si forma per ossidazione sulla superficie del grezzo durante il riscaldo e la movimentazione dal forno alla macchina. In questo modo la pressa di forgiatura può lavorare il materiale “pulito” e ottenere un componente dalle caratteristiche geometriche più precise, allungando al tempo stesso anche la durata degli stampi.
«In tempi più recenti abbiamo iniziato a sviluppare anche una terza famiglia di presse per il settore della forgiatura, ovvero quelle meccaniche della linea MF», precisa Maffei. «Si tratta in realtà di una versione più evoluta rispetto alle classiche presse meccaniche di forgiatura, che abbiamo voluto sviluppare con soluzioni tecniche innovative per andare incontro alla forte richiesta dal mercato e che ben si adatta a un ampio ventaglio di applicazioni. Le presse meccaniche hanno notoriamente un tempo ciclo più rapido rispetto alle presse a vite e idrauliche, anche se la regolazione della slitta per ottenere una corretta chiusura dello stampo risulta essere più laboriosa, con un tempo di settaggio leggermente superiore rispetto alle presse a vite e idrauliche. Di conseguenza, si dimostrano assolutamente vincenti nel caso di produzioni che richiedano elevati volumi di componenti di piccole e medie dimensioni e nei quali la precisione del pezzo finito non è il requisito fondamentale».
Linee complete
L’esperienza di lunga data nell’ambito della forgiatura ha spinto Ficep ad approcciare questo settore ponendosi come partner fornitore di tutte le tecnologie necessarie a completare il processo di lavorazione, con la sola eccezione degli impianti di riscaldo del pezzo, che comunque possono essere integrati su richiesta dei clienti. La realtà di Gazzada Schianno (VA) infatti realizza anche le macchine per il taglio delle barre, che possono essere seghe a disco, cesoie a freddo, semicaldo o caldo, e fornisce l’automazione per movimentare gli spezzoni dalla zona di taglio all’impianto di riscaldo, e successivamente alle presse di preformatura o di forgiatura. «Man mano che le macchine diventavano più precise, l’attenzione della clientela si è spostata su altre fasi del processo nelle quali l’attività dell’operatore poteva incidere negativamente sul risultato finale», conclude Maffei. «Per questo motivo l’automazione si è diffusa con grande rapidità, poiché i sistemi automatizzati impiegano sempre lo stesso tempo per portare il pezzo dal forno alla pressa, e quindi il pezzo verrà lavorato sempre alla stessa temperatura. Anche la lubrificazione degli stampi oggi viene eseguita tramite robot, che stendono un layer uniforme su tutta la superficie dello stampo garantendo così uno scorrimento ottimale del materiale in tutte le zone dello stampo stesso. Si tratta di operazioni relativamente semplici ma che assicurano il mantenimento della qualità per l’intero lotto e la riduzione al minimo degli scarti, che è poi l’obiettivo primario dei nostri clienti. Il tutto si riassume nella possibilità di ottemperare ai requisiti relativi al nuovo concetto di Industria 4.0, consentendo alle macchine prodotte da Ficep di affrontare con slancio le nuove sfide del futuro».
Condividi l'articolo
Scegli su quale Social Network vuoi condividere