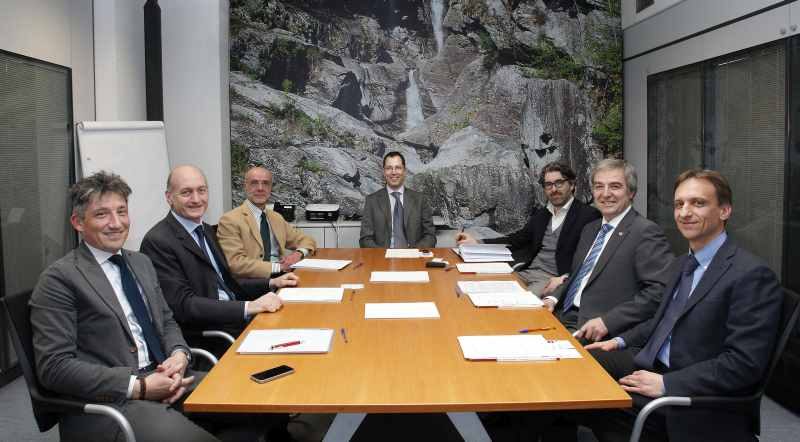
I principali player del settore laser si confrontano sull’andamento del mercato e sulle tendenze tecnologiche
L’avvento delle sorgenti in fibra ha rivoluzionato la tecnologia laser degli ultimi anni: che si tratti di taglio, di saldatura, di marcatura o di apporto di materiale (Selective Laser Sintering, SLS), i benefici derivanti dall’impiego delle nuove sorgenti sono indiscutibili.
Il primo, più evidente, è l’elevata velocità di lavoro, seguito a breve distanza dai bassi costi operativi. La semplicità costruttiva degli impianti, poi, ha come effetto collaterale una maggiore affidabilità complessiva delle macchine stesse.
I bassi costi – uniti ai recenti incentivi statali – hanno così contribuito allo sviluppo del mercato e alla crescita dei costruttori di macchine laser.
Possiamo quindi decretare la fine del CO2? Neanche per sogno!
Sicuramente ridimensionato nei numeri, rimane comunque una scelta valida in alcune applicazioni e merita di essere valutato caso per caso.
Abbiamo chiesto ad alcuni tra i principali player di questo complesso settore quali siano i fattori chiave che stanno guidando lo sviluppo delle soluzioni laser e quali saranno i possibili sviluppi tecnologici proprio ora che le sorgenti in fibra si stanno consolidando.
Qual è l’andamento del mercato italiano secondo voi costruttori di macchine laser e quali sono i settori applicativi oggi più interessanti per questa tipologia di macchine?
Pierandrea Bello, Salvagnini Italia
Per la tipologia di macchine che costruiamo siamo legati al taglio laser bidimensionale. In quest’ambito, l’andamento complessivo è per noi stabile: negli ultimi tre anni abbiamo sempre ottenuto buoni risultati, con una leggera crescita negli ordini e nel fatturato. Interessante come il mercato italiano continui a spingere, in particolare grazie alle richieste dei terzisti, mentre nel resto del mondo vendiamo una quota leggermente inferiore ai contoterzisti e di più alle aziende che realizzano un prodotto proprio. Certo hanno influito positivamente i nuovi Superammortamenti, ma anche gli anni precedenti sono stati altrettanto positivi quindi credo si tratti di un trend ben delineato.
Per quanto riguarda le due categorie citate, terzisti e produttori diretti, si tratta in entrambi i casi di condizioni interessanti, perché soddisfare le richieste di un terzista è una grossa sfida tecnologica mentre i secondi puntano su cicli fortemente ottimizzati e valutano di buon occhio le soluzioni “chiavi in mano”.
Giovanni Zacco, BLM Group
L’Italia per noi è stata un mercato in ripresa dal 2015: gli incentivi del governo – ammortamenti al 140%, nuova Sabatini e incentivi al sud – hanno fatto la propria parte e perciò riteniamo che anche nel corso del 2016 verrà mantenuto questo trend. Vedremo se, quando termineranno gli incentivi, il “volano” avrà ripreso a girare a sufficienza per proseguire con la crescita, noi siamo ottimisti.
Per quanto riguarda i settori applicativi, siamo da sempre molto attivi nell’automotive: in Germania abbiamo partecipato ad un progetto ricerca applicata per lo sviluppo del prototipo di automobile “EDAG Light Cocoon” esposta al salone di Ginevra, per il quale EDAG ha ricevuto il “German Design Award 2016”. Prototipo fatto con un telaio di tubi tagliati al laser e particolari realizzati in additive manufacturing, tecnologia che ben si abbina al laser.
Interessanti anche i riscontri dal settore dell’edilizia: alcune recenti modifiche nelle normative per le costruzioni favoriscono l’impiego della lavorazione laser per la sua caratteristica precisione e le aziende del settore stanno prendendo coscienza delle grandi opportunità che questa tecnologia offre loro.
Stefano Cattaneo, IPG Photonics
Il nostro punto di vista, da costruttore di sorgenti, è sicuramente positivo: il mercato è cresciuto e continuerà così. Certo, rispetto a pochi anni fa le quote tra CO2 e fibra si sono ribaltate, con un significativo tasso di crescita di quest’ultima.
Per noi laser, in Italia, significa taglio nell’85-90% delle applicazioni. Il mercato della saldatura lo giudichiamo ancora abbastanza inesplorato, soprattutto considerando che, all’estero, ha quote ben superiori. Riteniamo quindi che ci sia ancora un ottimo margine di crescita e una grande possibilità di installare nuove macchine. Questo è sicuramente uno stimolo in più per noi, che ci ha portati anche alla realizzazione di nuovi laboratori per lo studio di processi sempre più ambiziosi, con sorgenti più potenti (a fine 2015 abbiamo installato nel nostro laboratorio di Cerro Maggiore una sorgente in fibra da 20 kW in continua, la più potente oggi presente in Italia) o con lunghezze d’onda diverse o, ancora, con impulsi corti e ultracorti. Le applicazioni su cui lavoriamo quotidianamente spaziano dalla saldatura dei metalli, di precisione come su alti spessori, al laser cladding, alla saldatura delle plastiche, alle microlavorazioni, fino all’additive.
Marco Casanova, Yamazaki Mazak Italia
Come Mazak Italia ci occupiamo sia della commercializzazione di macchine ad asportazione truciolo, sia di macchine per il taglio laser. Per entrambe, i volumi di vendita sono cresciuti negli ultimi due anni, dando così un’importante indicazione sullo sviluppo generale del mondo manifatturiero. Per quanto riguarda il laser, abbiamo notato una crescita significativa da parte dei terzisti e dalle aziende produttrici di macchine industriali.
Essendo Mazak un fornitore a 360°, è per noi strategico, ove fosse possibile, far abbracciare ad aziende manifatturiere di sola asportazione truciolo, anche la tecnologia laser. Stiamo infatti lavorando per creare questa sinergia. Il taglio laser fibra diventa più accessibile e utilizzabile, infatti alcuni nostri clienti nel settore truciolo hanno investito in questa nuova tecnologia.
Ci aspettiamo un ulteriore miglioramento quest’anno, grazie anche alle agevolazioni e agli incentivi fiscali. Inoltre il mercato sta tornando a crescere e le sue richieste sono sempre più esigenti.
Alberto Vismara, Trumpf Italia
Per quanto riguarda le macchine laser, in Italia abbiamo registrato una crescita a due cifre già l’anno scorso grazie alla legge Padoan-Guidi che ha incentivato gli investimenti. Confermo poi che il rifinanziamento della Sabatini, il Superammortamento al 140% e gli incentivi al sud stanno decisamente aiutando il mercato italiano.
I più interessati ad ampliare o modernizzare il proprio parco macchine sono i terzisti, che stanno puntando decisamente verso le soluzioni in fibra; non tutti però hanno trovato utili i benefici di questa tecnologia, quindi le macchine a CO2 rimangono una opzione valida per determinati utilizzatori, convincendoci a mantenere questa tipologia di macchine a catalogo, anche se oggettivamente le percentuali si sono ridotte moltissimo.
Abbiamo poi parecchi clienti costruttori di macchine che stanno portando al proprio interno la lavorazione della lamiera: se un tempo la carpenteria metallica in Italia veniva quasi sempre esternalizzata, oggi stiamo osservando un trend opposto.
In assoluto in Italia con il laser si taglia molto ma si salda poco, prevalentemente nel settore automotive: è una situazione atipica rispetto al resto del mondo, ma volendo leggere il dato in positivo significa che c’è un margine di crescita significativo che dobbiamo cercare di stimolare. Buona infine la crescita delle macchine a tecnologia additiva con deposito di polveri, anche se i numeri sono ancora relativamente contenuti.
Stefano Draghi, Rofin Baasel Italiana
In qualità di costruttori di sorgenti laser, la nostra percezione è di un 2016 che si prospetta molto positivo. Produciamo entrambe le tipologie di sorgenti e confermiamo i grandi incrementi della fibra nei confronti del CO2 che pur conserva una significativa fetta di mercato.
Per quanto riguarda i clienti finali e gli integratori, i volumi sono aumentati e non solo nel taglio: abbiamo visto interessanti quote anche nelle applicazioni di saldatura e questo ci fa ben sperare per il futuro. ROFIN, come tutti sanno, è presente anche nei settori della marcatura, dove i volumi si mantengono stabili, e delle microlavorazioni in cui i numeri sono decisamente in aumento per quanto riguarda i laser a impulsi corti e ultracorti (pico e femtosecondi).
Le differenti sorgenti laser potranno convivere o lo sviluppo di quelle a fibra ottica è destinato a cambiare gli equilibri tecnologici di questo settore?
Stefano Draghi, Rofin Baasel Italiana
Da alcuni anni il trend è a favore del laser fibra rispetto a quello CO2. Ciononostante, riteniamo, confortati anche dal mercato, che per alcune applicazioni – sia di taglio che di saldatura – sia ancora la soluzione migliore. Quando si pensa al CO2 viene naturale associarlo alle sorgenti multi kW, in realtà c’è una quota significativa anche nel campo delle basse potenze, ci riferiamo ai laser CO2 sigillati. Il mercato di questi ultimi, impiegati normalmente per il taglio di materiali non metallici dove la fibra non è utilizzabile, è sempre cresciuto negli ultimi anni proprio perché inaccessibile alle altre tecnologie.
Immaginare cosa ci riserverà il futuro non è scontato. Solo fino a 7-8 anni fa, il CO2 sembrava la soluzione a tutte le necessità applicative, mentre ora sappiamo che non è così. Oggi la domanda è: quale sarà l’evoluzione dei diodi per applicazione diretta? Fino a pochi anni fa se ne parlava solo per applicazioni di brasatura, mentre oggi alcune sorgenti e alcuni costruttori cominciano a valutarli anche per il taglio.
In marcatura abbiamo inoltre notato che i clienti non chiedono più “un laser fibra”, ma “la soluzione” che svolga al meglio il compito cui è destinata. Ciò significa che è passata un po’ la moda che portava a puntare solo sulla fibra e ci si è focalizzati sulle effettive necessità applicative.
Alberto Vismara, Trumpf Italia
Il mercato italiano del taglio richiede assolutamente le macchine in fibra: la tendenza è quella e, con quote attorno al 75-80%, i nostri numeri lo confermano. Il CO2 presenta comunque applicazioni dove la qualità del processo o le richieste del cliente lo rendono la scelta ideale. Inoltre il mercato italiano si sta muovendo moltissimo sul fibra, ma ci sono mercati europei che lavorano senza problemi con il CO2: occorre quindi comprendere quali siano le esigenze effettive e come soddisfarle al meglio.
Per quanto riguarda il prossimo futuro, il diodo diretto sembra la naturale evoluzione, anche se occorre pensare a quale tecnologia emergerà nel frattempo.
In alcuni casi, poi, il lungo ciclo di vita delle macchine non aiuta: chi ha investito 6 o 7 anni fa ha ammortizzato completamente la macchina e preferisce farla lavorare con un costo orario più basso anziché cambiarla. Abbiamo attivato servizi di noleggio macchina con clienti con una pianificazione della produzione molto accurata, dove dopo 4 o 5 anni può risultare conveniente cambiare modello, ma si tratta di casi sporadici e non sempre gli imprenditori italiani vedono di buon occhio questa possibilità.
Marco Casanova, Yamazaki Mazak Italia
I numeri parlano da soli: sia per quanto riguarda gli ordini, sia per le offerte, le richieste di macchine per il taglio laser in fibra sono prevalenti rispetto ai modelli CO2.
Negli ultimi anni abbiamo raggiunto prestazioni di taglio stabili e la produttività nel taglio di lamiere sottili è aumentata grazie all’elevata qualità del fascio laser in fibra. Abbiamo introdotto nuove funzioni intelligenti e l’esclusiva Multi-Control Torch di nostra produzione, che permette di realizzare tagli ottimali a grande velocità e precisione. Oggi, siamo certi di poter offrire macchine in fibra con potenzialità sempre più vicine a quelle del CO2, ma con costi di manutenzione e di esercizio sempre più ridotti.
Come prova di questa visione sinergica delle tecnologie di taglio laser e asportazione truciolo, abbiamo sviluppato e presentato l’anno scorso l’innovativo Integrex i-400 AM, che unisce in un’unica piattaforma la fabbricazione additiva alla lavorazione multitasking con una testa laser fibra. Mazak, per proprio natura, è sempre alla ricerca di nuove soluzioni.
Stefano Cattaneo, IPG Photonics
Un fatto è certo: il laser fibra ha già cambiato gli equilibri. Un tempo la fibra veniva utilizzata unicamente per fare ciò che non era realizzabile con le sorgenti in CO2, mentre oggi le parti si sono definitivamente invertite.
Quest’anno abbiamo festeggiato i 10 anni dalla consegna in Italia del primo laser fibra per applicazioni di taglio (febbraio 2006). Siamo partiti con un piccolo integratore, CY-Laser, che, andando contro il parere comune e la cattiva informazione dell’epoca, ha avuto il coraggio di sviluppare un’idea nuova: una macchina semplice, economica da usare e decisamente vantaggiosa rispetto a una tecnologia matura com’era quella del CO2. Vorrei sottolineare anche che, a quei tempi, mancavano addirittura le teste di taglio adatte alla tecnologia a fibra e il mercato proponeva soltanto teste da CO2 modificate. Oggi questo integratore ha installato oltre 250 macchine seguendo, negli anni, la crescita della stessa IPG Photonics, passata da un solo laser con potenza maggiore di 1 kW installato nel 2006 a 418 consegnati l’anno scorso solo in Italia.
Per quanto riguarda l’avvento di nuove sorgenti, non penso ai diodi diretti come una possibile alternativa alla fibra, poiché rappresentano un passo in avanti relativamente contenuto (potenze, qualità del fascio, lunghezza d’onda ed efficienza praticamente identiche); di sicuro non siamo di fronte a un grande cambiamento come nel passaggio da CO2 a fibra. Al contrario, invece, sono fiducioso nei confronti di soluzioni con nuove lunghezze d’onda, nel visibile o nell’infrarosso, così come per sistemi basati su principi di funzionamento diversi.
Giovanni Zacco, BLM Group
In qualità di utilizzatori esperti di sorgenti, valutiamo ogni novità immessa sul mercato. Siamo stati tra i primi a credere nella fibra alcuni anni fa e da allora il percorso è stato molto rapido, in particolare per la semplicità di utilizzo e l’affidabilità di processo.
Un elemento importante è la semplicità costruttiva delle macchine stesse. Un vecchio detto recita che “ciò che non c’è non può rompersi”: la meccanica molto raffinata che caratterizza il CO2 è stato un elemento fondamentale nel passaggio alla fibra, più semplice e meno “delicata”.
La tendenza è quindi sicuramente favorevole al laser fibra, ma non credo che il CO2 sparirà, è più credibile che ciascuna tecnologia si ricavi il proprio ambito applicativo più o meno ampio un po’ come è successo fra punzonatura e taglio laser. Inoltre non si deve dimenticare che lo sviluppo continua: i diodi diretti al momento rappresentano una tecnologia molto interessante da investigare, analizzare e valutare e potrebbero costituire elemento di novità importante.
Pierandrea Bello, Salvagnini Italia
Per noi la domanda assume un significato particolare, poiché già nel 2010 abbiamo fatto la scelta di abbandonare la tecnologia CO2 per affidarci unicamente alla fibra.
Ricordo le difficoltà iniziali legate all’impiego di questa tecnologia, ma i presupposti erano ottimi e il tempo ci ha dato ragione.
Al di là delle caratteristiche che oggi tutti conosciamo, come velocità ed efficienza, all’inizio è stata la semplicità d’uso a incentivare l’impiego di questa tecnologia. Ho lavorato come Project Manager per diversi anni e ricordo cosa comportasse l’installazione di un impianto a CO2 rispetto a uno in fibra: ciò non significa che quest’ultima sia migliore in assoluto, poiché occorre comprenderla e utilizzarla nel modo corretto.
Interessante infine il fermento legato ai diodi che, pur non essendo molto differenti dalla fibra convenzionale, promettono discreti margini di sviluppo per il futuro.
Se escludiamo il costo di acquisto, quali sono i parametri che influenzano i clienti nella scelta di una moderna macchina laser (tempistiche di consegna, configurabilità della macchina, fornitura chiavi in mano, flessibilità operativa ecc.)?
Pierandrea Bello, Salvagnini Italia
Un elemento sempre più richiesto è l’attenzione al processo: per noi non è una novità, ma oggi è particolarmente evidente anche nel laser.
Oggi anche in Italia si vendono molti più impianti con automazione rispetto a quelli stand alone: i clienti hanno compreso che l’automazione non va vista nell’ottica della riduzione dei costi derivanti da un eventuale operatore in meno, ma ragionano più in termini di efficienza.
Fondamentale poi l’integrazione degli impianti a monte e a valle: ci vengono chieste macchine in grado di dialogare tra loro, che consentano di arrivare al pezzo finito in modo più efficiente – che può significare più velocemente, con costi inferiori, con una determinata qualità ecc. – e con maggiore flessibilità. È inutile essere più veloci del 3% in fase di taglio se poi si perde il 30% tra setup e tempi morti! L’integrazione software rappresenta quindi un notevole beneficio non solo per le grandi aziende ma soprattutto per le piccole realtà, che probabilmente ne traggono ancora maggior vantaggio.
Giovanni Zacco, BLM Group
I clienti sono sempre più competenti e attenti non tanto al costo dell’impianto in sé, ma piuttosto al costo del pezzo finito che devono produrre; scelgono cioè il modello di macchina in funzione di ciò che devono fare, valutando molto attentamente il costo del processo nel suo complesso.
Consapevole di questo, BLM Group si è mossa in due direzioni distinte: semplicità nell’utilizzo della macchina e integrazione.
Come esempio di semplicità ed efficienza del processo abbiamo recentemente presentato una applicazione software che permette all’utilizzatore di importare un disegno 3D e trasferire alla macchina il relativo programma di lavoro corretto, senza alcun intervento da parte dell’operatore.
Per quanto riguarda l’integrazione, la intendiamo in maniera trasversale tra le diverse tecnologie. La lavorazione del tubo include taglio laser, piegatura, sagomatura: il nostro sistema Cad-Cam considera il pezzo nel suo complesso ed è in grado di individuare e scorporare le diverse lavorazioni a partire da un unico modello 3D producendo, per i diversi sistemi, programmi corretti che tengono conto anche delle deformazioni indotte dalle lavorazioni che devono seguire. Noi lo chiamiamo All-In-One.
Stefano Cattaneo, IPG Photonics
Pur occupandoci principalmente di sorgenti laser e non di applicazioni finali, riteniamo comunque fondamentale la prova con il cliente.
Il motivo per cui abbiamo investito così tanto nel nostro laboratorio qui in Italia è proprio questo: rispondere al cliente nel più breve tempo possibile. Il cliente ci fornisce il pezzo grezzo e ci spiega il suo problema; noi effettuiamo delle prove e gli diamo risposte certe.
Parlando di macchine e non solo di sorgenti, possiamo portare come esempio il sistema per la saldatura in continuo del tubo, sviluppato in questi anni da IPG Photonics Italia e con i primi esemplari in produzione dal 2013. I motivi principali che portano alla scelta delle macchine fibra rispetto alle consolidate soluzioni con CO2 sono sempre gli stessi: il costo orario di esercizio (ridotto nel caso del tubo del 70%!), l’affidabilità delle sorgenti e la grande semplicità di utilizzo. Come per il taglio, la fibra semplifica tutto, dall’installazione alla manutenzione, incluso l’utilizzo quotidiano. I clienti non credono ai propri occhi quando constatano che è sufficiente clonare i parametri da una macchina fibra a un’altra per ottenere i medesimi risultati; l’allineamento degli specchi nella catena ottica, la calibrazione della singola sorgente e altre “amenità” caratteristiche del CO2 sono ormai un triste ricordo. Non è più necessario avere un “esperto” di laser in azienda che conosca alla perfezione la macchina per ottenere il risultato voluto, perché chiunque abbia un minimo di dimestichezza con questa tecnologia, oggi lo può fare.
Marco Casanova, Yamazaki Mazak Italia
Sono diversi i fattori che influenzano la scelta di una macchina laser.
Per nostra esperienza, in fase di trattativa sicuramente il punto di partenza è lo studio di fattibilità del componente. In questa prima fase emergono le caratteristiche del macchinario in termini di prestazione e non da meno le nostre competenze tecniche.
Nell’evoluzione della trattativa subentrano altre tematiche, quali l’automazione, la semplicità d’uso, l’affidabilità, il controllo numerico e la gestione del processo produttivo a 360°.
Più volte bisogna tener conto anche del luogo d’installazione del macchinario che spesso influenza lo sviluppo dell’automazione. Come Mazak ci facciamo carico dell’intera fornitura, tenendo in giusta considerazione ogni necessità del cliente e sempre in tempi rigidamente stabiliti l’impianto deve entrare in produzione a regime.
Per nostra natura l’affidabilità è uno dei nostri principi di fornitura. Siamo consapevoli dei costi d’esercizio di un impianto complesso. L’impianto deve sempre produrre con continuità, in modo affidabile e con una qualità costante nel tempo.
Alberto Vismara, Trumpf Italia
Sicuramente quello dell’automazione è un tema caldo: dalla ripresa economica, infatti, la maggior parte delle richieste di preventivi includono l’automazione.
Trumpf è sempre stata attenta a questo fattore, tanto che anni fa ha costruito uno stabilimento dedicato proprio alla costruzione di magazzini e sistemi automatizzati. Lo stesso vale per i software: con TruConnect ci proponiamo come consulenti per valutare il processo produttivo a monte e a valle della nostra macchina, dalla programmazione della produzione allo scambio di dati all’interno dell’impianto.
Occorre però anche fare i conti con i piccoli clienti che non hanno le risorse o la necessità di una offerta così completa: per questo abbiamo fondato lo scorso anno una società finanziaria che si occupa appunto della fornitura di finanziamenti a condizioni favorevoli, in modo da aiutare i clienti a slegarsi dalle macchine stand alone e a fare un primo passo verso le soluzioni integrate.
Il costo di una macchina è però influenzato da una serie di fattori esterni altrettanto strategici, come un service rapido nel rispondere e una rete di assistenza estesa: sul mercato ci sono costruttori che non si sono strutturati in questo modo, che possono fare leva su prezzi molto aggressivi. Il problema sopraggiunge in caso di necessità, quando ci si trova a fare i conti con giorni o settimane di fermo macchina rispetto a poche ore spesso garantite da chi dispone di una rete capillare.
Stefano Draghi, Rofin Baasel Italiana
In quanto costruttori di sorgenti laser, pensiamo che tra i fattori chiave in grado di determinare la scelta di una macchina ci siano la facilità d’uso (soggettiva ma comunque quantificabile), l’affidabilità e l’efficienza energetica (un parametro oggettivo).
I parametri con cui l’utilizzatore finale effettua la propria scelta sono diversi a seconda dell’applicazione. Se una macchina è destinata al taglio la sorgente è la chiave e rappresenta il vero ago della bilancia. In saldatura, invece, è il processo a comandare: l’utilizzatore ha un problema da affrontare e risolvere, con tempi, costi e qualità stabiliti, spesso in conformità con le norme del settore applicativo di sbocco.
Il service (pre e post-vendita) sta diventando sempre più importante nella fornitura di un impianto: come siete strutturati per rispondere, anche in questi termini, alle necessità dei clienti?
Stefano Draghi, Rofin Baasel Italiana
Poiché offriamo entrambe le tecnologie (CO2 e fibra), siamo in grado di fornire consigli oggettivi al cliente che si avvicina al mondo delle macchine laser. Ci proponiamo quindi come “consulenti”. Da questo punto di vista, il supporto che offriamo basa le proprie fondamenta sulla disponibilità di laboratori in grado di studiare e ottimizzare il processo del cliente per guidarlo verso la scelta più idonea.
In merito al servizio post vendita, occorre tenere presente che oggi i laser sono molto più affidabili di quanto non fossero in passato e, conseguentemente, anche il servizio post-vendita si è adeguato. Non è più sufficiente disporre di un “service” adeguato composto da tecnici preparati e dal tempo di reazione veloce. Oggi è necessario disporre anche di un efficiente servizio di diagnostica da remoto che permetta di comprendere l’eventuale problema così da rendere l’intervento fisico, se necessario, più efficiente.
A tal proposito Rofin ha implementato il nuovo controllo numerico in tutti i suoi modelli di laser per offrire le medesime capacità operative – inclusa appunto la diagnostica remota.
Alberto Vismara, Trumpf Italia
Una macchina con sorgente allo stato solido è sia più efficiente, sia meno sensibile a eventuali guasti; la stessa catena ottica è un elemento di criticità in meno con il quale fare i conti, visto che la testa è sigillata (è sufficiente cambiare periodicamente il vetro di protezione) e i diodi di pompaggio sono pressoché eterni. In definitiva, si tratta di tecnologie molto affidabili.
Esiste comunque un detto che recita che “la seconda macchina si vende grazie a un buon servizio sulla prima”. Per questo tutte le nostre macchine sono collegate in telediagnosi e dispongono della tecnologia Wireless Integration Point, che permette a ogni sistema di taglio di diventare un punto di accesso senza fili per controllarla sia da remoto, sia in locale attraverso un tablet per contattare la nostra assistenza tecnica verificandone le condizioni e scambiandosi video, foto del processo ecc.
Tutte soluzioni che aiutano a velocizzare i tempi di risposta, anche perché a volte non c’è un vero e proprio problema, ma si tratta di una consulenza sui parametri da utilizzare e rispondere velocemente è un dettaglio molto apprezzato.
Marco Casanova, Yamazaki Mazak Italia
In Mazak dividiamo il servizio in tre fasi distinte: pre-vendita, installazione e post-vendita.
Per la prima disponiamo di un ufficio applicazioni attraverso il quale studiamo la richiesta del cliente (come produrre, in quanto tempo, con quali costi ecc.) e, sulla base delle specifiche necessità, procediamo con l’offerta e la trattativa.
Nel nostro Centro Tecnologico di Cerro Maggiore abbiamo sempre a disposizione sia macchine a taglio laser, sia macchine ad asportazione truciolo per test cut dedicati al cliente. Se necessario, lo accompagniamo nel Centro Tecnologico Europeo dove è disponibile la macchina richiesta, al fine di permettergli di valutare in prima persona le caratteristiche del macchinario che gli occorre.
In fase di installazione, l’accettazione da parte del cliente arriva solo dopo una fase di controllo e messa in servizio, al fine di assicurare una soluzione perfettamente funzionante e rispondente alle sue aspettative.
Sul fronte del service post-vendita, Mazak in Italia può contare su 80 tecnici pronti a rispondere velocemente (oltre l’80% dei problemi viene risolto telefonicamente) o a intervenire rapidamente con il ricambio appropriato, grazie a un magazzino centralizzato in Belgio che fornisce nel 98% dei casi il componente entro 24 ore.
Stefano Cattaneo, IPG Photonics
Parlando di pre-vendita, occorre fare una distinzione iniziale tra le applicazioni di taglio e tutte le altre.
Per le prime, ormai nessuno si rivolge più a IPG per chiedere conferme sulla bontà della tecnologia a fibra per il taglio laser poiché è una informazione oggi data per scontata.
Al contrario, la saldatura, così come il cladding, le microlavorazioni o qualsiasi altra applicazione laser diversa dal taglio, richiede invece una precisa attività di supporto già prima della vendita; questo non tanto per la tecnologia in sé, ma perché le incognite che questi processi comportano sono ancora importanti. Qui ritorniamo di nuovo sull’importanza del laboratorio “vicino” al cliente, importante sia per dare a quest’ultimo qualche certezza prima dell’acquisto, sia per garantirgli una futura assistenza qualora il processo, una volta installato in produzione, presenti delle difficoltà impreviste. Sembra un dettaglio, ma il cliente può apprezzare da subito le competenze del fornitore ed essere certo che ne trarrà beneficio durante l’intera vita operativa della macchina.
Per quanto riguarda il post vendita, a prescindere dalla tipologia di applicazione, la filosofia di IPG è sempre stata quella di mettere l’utilizzatore in condizione di non fermarsi mai, anche in caso di guasto, permettendogli di portare a termine una lavorazione e di finire una commessa aperta, pianificando l’eventuale intervento in un secondo momento, a macchina “scarica”.
Cerchiamo inoltre di assicurare costi certi al cliente: normalmente le macchine vengono vendute con un periodo di garanzia standard di due o tre anni, senza alcun limite sulle ore di emissione delle sorgenti; prima della scadenza di questo periodo, la garanzia può poi essere estesa, a pari condizioni e per costi decisamente contenuti, fino a 8 anni totali. In questo modo il cliente può ragionare su cifre precise, molto più convenienti rispetto al CO2.
Giovanni Zacco, BLM Group
In fase di pre-vendita siamo organizzati con showroom attrezzati con macchine che i clienti possono valutare sulla base della propria applicazione o per fare dei corsi. A tal proposito, facciamo formazione sia da noi in sede, prima dell’installazione che presso il cliente in fase di avviamento dell’impianto; successivamente offriamo assistenza tecnica con tutti gli strumenti che la tecnologia attuale mette a disposizione, come il teleservice, le varie modalità di connessione attraverso rete, le telecamere ecc.
Ogni cliente ha poi la propria area dedicata all’interno del nostro portale dalla quale scaricare gli aggiornamenti software per le macchine, aggiornamenti delle applicazioni installate o nuovi pacchetti. Qui trova inoltre i nostri corsi on-line, completi di test a fine corso. Un sistema innovativo e molto utile per prendere dimestichezza con aspetti specifici dell’utilizzo degli impianti e per formare eventuali nuovi operatori.
Pierandrea Bello, Salvagnini Italia
Per noi è fondamentale sviluppare impianti che riducano le attività ripetitive o non utili agli operatori e consentano loro di concentrarsi su quelle ad alto valore aggiunto.
Le macchine intelligenti sono quindi importanti, ma è lo è altrettanto assicurare il giusto margine affinché gli operatori più capaci possano fare la differenza.
Il giusto punto di equilibrio è offrire gli strumenti per evitare le attività delegabili a un computer e, nel contempo, fornire quelli utili per effettuare operazioni più complesse o creative.
Con l’acquisto di un modello particolarmente performante, ad esempio, un nostro cliente ha notato che il tempo di programmazione era quasi superiore a quello della lavorazione vera e propria: sfruttando le informazioni già presenti nel sistema, automatizzando alcune procedure e snellendone altre, ha recuperato non solo tempo produttivo grazie a una macchina dalle elevate performance, ma ha anche ridotto i tempi accessori grazie a strumenti pensati specificamente per velocizzare la programmazione.
Condividi l'articolo
Scegli su quale Social Network vuoi condividere