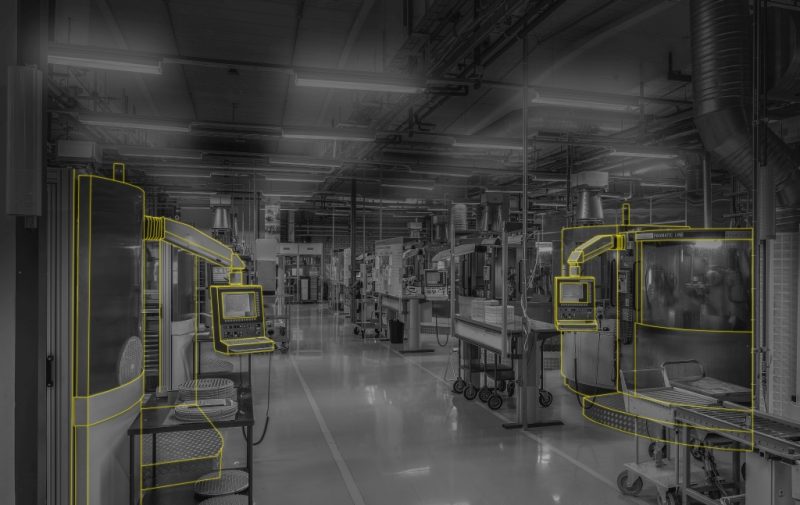
Oggi i dati di processo sono facili da ottenere: il vero valore risiede nel loro impiego. Un approccio olistico è quindi fondamentale per ottenere risposte giuste alle domande del mondo manifatturiero
di Adir Zonta
La raccolta e l’uso dei dati per apportare miglioramenti sono da molti anni considerati in diversi settori industriali strumenti di valore aggiunto, con una tecnologia consolidata in termini di monitoraggio di processo e lavorazione nell’industria manifatturiera. Eppure è attraverso la connettività e la capacità di visualizzare e condividere i dati con altri utilizzatori che la tecnologia può passare a un livello più alto.
Per un periodo di tempo è stato possibile monitorare singole macchine impiegate nella lavorazione dei metalli, ma il passo successivo di questo percorso prevede il monitoraggio e la condivisione dettagliata di ciò che accade nel processo di lavorazione con altre parti interessate. Oggi siamo in grado di “ascoltare” le macchine utensili, raccogliere dati, interpretarli, visualizzare ciò che accade, stabilire se l’utensile da taglio si sta usurando, se il processo è troppo veloce, troppo lento o non risponde alle aspettative, per poi rinviare tali dati alla macchina. In tal modo, è possibile non solo rilevare ma anche correggere tempestivamente gli errori, migliorando sempre più il processo di lavorazione fino a ottenere un’efficienza ottimale.
In precedenza, l’approccio rigido “a silos” prevedeva un singolo sistema di monitoraggio del processo dedicato a una macchina indipendente, senza connettività né possibilità di aggiornamento quando necessario. Sandvik Coromant ritiene però fondamentale la connessione delle macchine e conferisce un ruolo vitale al monitoraggio della lavorazione per l’interazione con la macchina utensile. Mediante la connessione delle macchine, è possibile installare aggiornamenti degli algoritmi e dei software tramite cloud o rete aziendale, ottenendo così un aggiornamento costante. Con questo livello di connettività, questa capacità di condivisione dei dati e questo approccio scalabile al monitoraggio della lavorazione, i produttori hanno trovato la soluzione a molti dei loro problemi. I vantaggi comprendono la riduzione dei tempi di fermo non pianificati provocati da improvvise collisioni, la riduzione dei costi di attrezzamento e riparazione mediante il monitoraggio del sovraccarico o della rottura dell’utensile, oltre alla riduzione dei tempi di fermo macchina provocati dall’assenza degli utensili. Al contempo, gli utilizzatori sono ora in grado di aumentare notevolmente la produttività e ottenere una qualità uniforme dei componenti, potendo disporre di limiti di setup degli utensili più precisi. Tali potenzialità rappresentano un beneficio per i futuri utilizzatori degli utensili da taglio e delle macchine utensili e aggiungono valore al tradizionale monitoraggio dei processi.
Tecnologia diversificata e differenti sistemi di produzione
Per aumentare produttività, sicurezza e qualità mediante il monitoraggio del processo e della lavorazione, l’utilizzatore deve operare con un’ampia gamma di tecnologie per tenere sotto controllo i vari aspetti del processo di lavorazione e per connettersi a molteplici sistemi. Ciò può coinvolgere diversi dispositivi di rete e software, il cloud e molto altro ancora. Un tale livello di connettività della lavorazione richiede la standardizzazione totale delle connessioni, che sembra ancora un lontano miraggio, o un elevato livello di integrazione. Che sia o meno possibile conseguire prima o poi processi di produzione del tutto privi di errori, Sandvik Coromant ha oltrepassato i confini che delimitano questo settore e ha sviluppato sistemi e soluzioni che consentono ai produttori di ottenere un margine competitivo attraverso il monitoraggio della lavorazione e l’uso efficace dei dati.
In termini d’impostazione e monitoraggio dei limiti degli utensili da taglio o di ciclo, l’esperienza accumulata nella tecnologia di taglio è in grado di aggiungere ulteriore valore al processo di monitoraggio della lavorazione, eliminando per gli utilizzatori la necessità d’impostare autonomamente tali limiti. Fattori cruciali di differenziazione in un’industria altamente competitiva quale quella manifatturiera risiedono nella rapidità e nella precisione dei tempi di risposta, associate al minore numero di falsi allarmi durante la produzione.
L’arresto non necessario del processo di lavorazione comporta ingenti costi ed è stato in passato un evento sin troppo frequente nel settore della lavorazione dei metalli, quando non esistevano algoritmi in grado di interpretare i segnali generati da una macchina. Per la raccolta e l’interpretazione dei segnali in pochi millisecondi è necessario un elevato livello di competenza e, in genere, tale onere spettava all’utilizzatore. Di fatto, però, se è vero che tale competenza è in grado di portare il monitoraggio del processo a un livello superiore, la comprensione dei limiti richiede decenni di conoscenza.
Monitoraggio in tempo reale e sostenibilità
Un valore aggiunto del monitoraggio della lavorazione risiede nella capacità di utiliz zare gli utensili al massimo delle loro potenzialità, il che si traduce a sua volta in una qualità superiore dei componenti e in tempi di lavorazione inferiori. Un altro vantaggio fondamentale del monitoraggio della lavorazione sta nella riduzione dei consumi energetici, che rende tale tecnologia sostenibile dal punto di vista ambientale, abbattendo al contempo i costi poiché permette un maggiore controllo da parte dell’utilizzatore. Senza un tale livello di controllo è più facile che l’utilizzatore si trovi ad affrontare problemi che interessano il processo di lavorazione, con conseguenti sprechi in termini di energia e risorse, i quali possono comprendere il disassamento errato degli utensili, la posizione di cambio utensile scorretta o ancora il bloccaggio o l’orientamento scorretto del pezzo, la selezione del programma sbagliato, rotture degli utensili non rilevati o impostazioni scorrette.
È indubbio che la produttività migliorerebbe se anche solo uno di questi problemi fosse eliminato, dunque basta immaginare il cambiamento radicale che si otterrebbe in termini di efficienza se si riuscisse a risolverli tutti. Similmente, se il controllo costante del processo elimina i problemi legati alla bassa sicurezza, a una qualità dei componenti non ottimale e al sottoutilizzo degli utensili, un sistema di monitoraggio della lavorazione garantisce non solo la presenza dell’utensile, ma anche l’assenza di guasti e l’esecuzione del processo entro i parametri corretti. Se necessario, il sistema intraprende azioni correttive, invia messaggi d’avviso per evitare usura e danni e arresta il processo di lavorazione in caso di rottura o assenza di un utensile. In questo modo è anche possibile ridurre la necessità di rottamazione, fondamentale in settori come l’aerospace, che si avvale di materiali dal costo elevato.
Armati di importanti dati di monitoraggio del processo a livello della macchina, gli utilizzatori possono prevedere ed evitare collisioni migliorando al contempo il controllo della manutenzione per estendere la durata dei componenti delle macchine utensili. Allo stesso modo, il monitoraggio a livello del componente aiuta a ottenere una qualità uniforme del pezzo prodotto e il monitoraggio a livello dell’utensile può offrirne un migliore impiego, una miglior previsione del costo per componente, livelli di inventario corretti e un uso della macchina notevolmente superiore.
La produttività è l’obiettivo del monitoraggio delle macchine utensili
Nell’industria della lavorazione dei metalli, l’epoca della bassa sicurezza dei processi, della qualità non ottimale dei componenti e del sottoutilizzo degli utensili volge ormai al termine. La mancanza di controllo determina costi maggiori, mentre un controllo costante del processo attraverso il monitoraggio della lavorazione si traduce in una maggiore efficienza, con una conseguente riduzione in termini di costi. Inoltre, il monitoraggio a livello degli utensili offre un utilizzo ottimale degli stessi, con livelli di inventario corretti, previsione più precisa dei costi per componente e uso migliore della macchina.
Lo scopo dell’approccio Sandvik Coromant al monitoraggio del processo di lavorazione è quello di aumentare i livelli di utilizzo della macchina fino all’85% grazie all’eliminazione dei fermi macchina non pianificati. Al tempo stesso, attraverso un processo di apprendimento automatico, l’efficienza di rimozione del metallo potrebbe raggiungere il 95% rispetto all’80% offerto dalla produzione convenzionale. Come molti altri processi di produzione, la lavorazione presenta delle cause di instabilità proprie che sono, tuttavia, neutralizzate da un monitoraggio del processo di lavorazione in grado di “ascoltare” ciò che accade nell’ambiente, verificare il corretto svolgimento delle operazioni e correggere eventuali deviazioni. Riducendo al minimo l’instabilità, il monitoraggio del processo di lavorazione può quindi fungere da catalizzatore per un cambiamento significativo nell’industria manifatturiera.
Adir Zonta è Product Manager Process Monitoring & Machining Analytics per Sandvik Coromant
Condividi l'articolo
Scegli su quale Social Network vuoi condividere