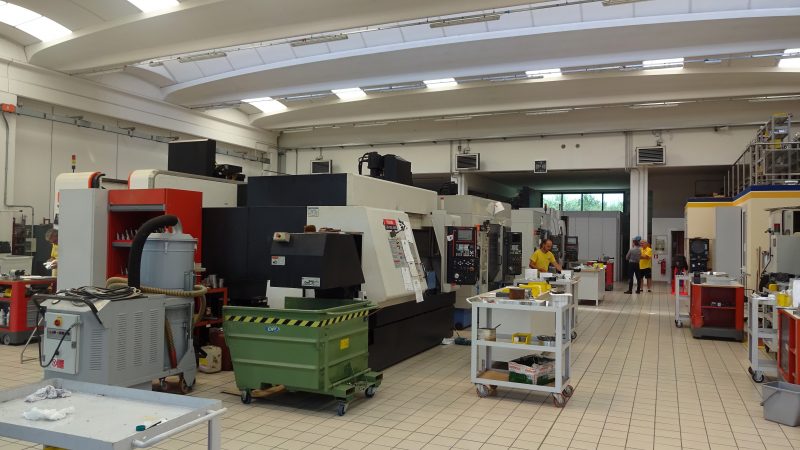
L’area compresa tra Rimini e Pesaro ha in comune una passione: quella per le moto da corsa e la meccanica. Qui Paolo Dondi fin da giovane subisce il fascino dell’ambiente sportivo, del rombo dei motori, dell’aspetto tecnico delle gare. Negli anni ‘80 corre con una propria motocicletta; nel garage di casa comincia a modificare alcune parti per alleggerire i pesi, migliorare le prestazioni, ottimizzare la guida. Ha successo; amici e piloti gli chiedono di intervenire anche sui loro mezzi. In breve decide di creare un’azienda proprio per costruire parti speciali per moto da corsa. La sua inventiva viene presto notata dalle scuderie più importanti e la passione si trasferisce dal circuito all’officina, entrando nel settore delle competizioni del motomondiale.
Oggi la DP Parti Speciali opera nel settore della meccanica di precisione nella sua sede di Pesaro e costruisce prototipi speciali anche per altri settori ad alto contenuto tecnologico (aeronavale ed energia). Il settore delle gare motoristiche rimane comunque quello d’elezione: l’azienda pesarese non è un semplice fornitore, ma svolge il ruolo di vero e proprio partner di importanti team di Formula 1 e MotoGP.
Chirurghi della meccanica
Chi lavora in questo settore sa che l’attività può spaziare da dinamica a frenetica, ma raramente scende a livelli di tranquilla routine; quasi sempre tutti i committenti sono in ritardo. D’altronde, la capacità di realizzare prototipi di componenti anche molto articolati e a brevissima scadenza è uno dei punti di forza dell’azienda di Paolo Dondi; i clienti sanno di potere contare su una straordinaria affidabilità e quindi apprezzano la cura a essi riservata.
Gli ingegneri progettisti studiano continuamente nuove soluzioni per migliorare le prestazioni di motori e telai. Componenti mai banali devono essere modificati o inventati ex novo; vengono ordinati e bisogna costruirli immediatamente, magari da un giorno all’altro, spesso ignorando soste o festività. Un po’ più di respiro c’è quando nasce un nuovo modello; qui l’azienda pesarese è chiamata a costruire i primi prototipi per valutazioni e prove, come precisa Paolo Dondi stesso: «I progettisti, non accontentandosi del rendering sullo schermo, vogliono vedere i pezzi, esaminare gli accoppiamenti, studiare gli ingombri. Noi dobbiamo inventare le migliori strategie di lavorazione, una volta per costruire un portapacchi, un’altra per un cruscotto o per una struttura portante, sempre ricavando oggetti dal pieno. Talvolta dobbiamo intervenire direttamente sul progetto perché magari non è geometricamente realizzabile, e quindi insieme ai progettisti concordiamo le necessarie modifiche. Spesso costruiamo utensili appositi, per lavorazioni “in tiro” o all’interno di cavità difficilmente raggiungibili, veri e propri interventi di chirurgia meccanica! Dopo avere ricevuto il modello tridimensionale, una fase delicata è la preventivazione: dobbiamo prestare molta attenzione perché è facile sovra o sottovalutare. Anche per questo motivo dobbiamo potere fare affidamento su strumenti potenti in officina che ci consentano di preventivare prima e di realizzare poi, senza incertezze e senza sorprese, la geometria che ci viene affidata».
Un CAM affidabile e intuitivo
L’officina è ordinata e pulita, assomiglia più a un laboratorio che a un tradizionale ambiente di lavorazioni meccaniche. Sono presenti numerose macchine di ultima generazione, anche a 5 assi e multitasking. Tutta la programmazione delle macchine viene eseguita con Edgecam, un sistema CAM che l’azienda utilizza già da molti anni, giudicato potente e affidabile ma anche di programmazione semplice e intuitiva: «Man mano che le esigenze sono andate aumentando, abbiamo installato nuovi moduli e dall’iniziale licenza standard oggi l’ufficio di programmazione lavora intensamente su due stazioni complete di modulo di fresatura 5 assi avanzato. Questo tipo di configurazione ci ha dotato di funzionalità molto utili per noi, essendo sempre alle prese con pezzi geometricamente complessi e di difficile lavorazione. Il CAM riesce a semplificarci le operazioni e garantirci che, qualunque sia la forma da costruire, il percorso di lavorazione sarà efficiente e senza sorprese; abbiamo sempre ottenuto quello che dovevamo costruire».
Edgecam offre un completo controllo dell’utensile e una vasta scelta di cicli di lavorazione che consentono un’elevata finitura superficiale; essendo un’applicazione interamente a 64 bit sfrutta tutte le potenzialità hardware a disposizione, garantendo rapidità di calcolo anche su modelli solidi e assiemi complessi. I modelli 3D inoltre vengono caricati direttamente nei formati nativi grazie a un’interfaccia diretta con i sistemi CAD più diffusi. L’azienda pesarese è uno degli utenti più esigenti nel campo dei 5 assi, tanto da trovare risposte nella versione avanzata. In questo modulo, per esempio, sono a disposizione tecnologie specifiche per lavorare i condotti: grazie alla gestione automatica del gambo utensile, il percorso utensile viene generato automaticamente dove possibile, limitandolo solamente nella zona dove il gambo si avvicina troppo alle superfici in lavorazione. Il controllo collisioni verifica il percorso fino al punto di contatto. È poi presente un’opzione di rotolamento su spigolo capace di creare un’estensione del percorso durante l’entrata nel condotto per un approccio più graduale alla lavorazione.
Lavoro non presidiato
Nonostante non ci siano grandi lotti, il lavoro in officina richiede due turni perché le finiture sono molto accurate.
«Naturalmente le macchine lavorano da sole, vanno avanti anche tutta la notte. Utilizziamo molto anche i quattro e cinque assi simultanei per finire un pezzo con un solo staffaggio. Ulteriori passaggi su altre macchine porterebbero a tempi di attraversamento oggi non più sostenibili. Inoltre un solo piazzamento consente di mantenere la precisione complessiva a valori eccellenti, impossibili da garantire altrimenti. Anche un’azienda che costruisce prototipi deve recuperare tutti i tempi morti, così manteniamo flessibilità e produttività. Il sistema Edgecam, con la sua simulazione realistica e accurata dei cicli di lavorazione, ci conferisce sicurezza sulle lavorazioni non presidiate da lanciare. L’esecuzione del programma viene simulata insieme a tutto lo spazio operativo coinvolto, con controllo di collisione per staffaggi, parti macchina, grezzo e pezzo in lavorazione».
DP Parti Speciali lavora essenzialmente per le scuderie in gara, tuttavia ha ancora un catalogo di prodotti propri costruiti uno per uno, generalmente ricavati dal pieno, dedicati a un pubblico di appassionati. L’azienda pesarese, per esempio, è stata la prima a proporre al settore delle moto mini GP (quelle per bambini) speciali cerchi in lega leggera da montare al posto di quelli originali in fusione. Questi ultimi, essendo derivati dalla serie, risultano molto pesanti; l’adozione dei cerchi in alluminio fa risparmiare 7-8 kg, migliorando la stabilità del mezzo. Ci sono poi le pinze freno per la Moto 3; si tratta di componenti di estremo pregio che, insieme ai dischi anch’essi costruiti da DP Parti Speciali, garantiscono una frenata molto più efficiente.
Non solo strumenti
Edgecam è supportato in Italia da ProCAM Group di Padova, che cura l’addestramento degli operatori e offre un vero e proprio servizio di consulenza sull’utilizzo del sistema: sia telefonico, quando è sufficiente a sbloccare situazioni di minore difficoltà, sia con l’affiancamento di personale in loco per i casi più complessi. Il supporto è tanto più apprezzabile quanto maggiore è la capacità degli utenti di sfruttare a fondo il sistema; è il caso di DP Parti Speciali, sempre alle prese con prodotti da realizzare alla massima velocità, di qualità eccellente e alta precisione, chiamati a sopportare stress meccanici micidiali.
ProCAM Group nei molti anni di attività ha tessuto una rete di rivenditori e figure tecniche specializzate che coprono l’intero territorio italiano, grazie alla quale può soddisfare richieste di intervento anche a brevissima scadenza. D’altro canto l’azienda pesarese in dieci anni ha sicuramente avuto modo di conoscere altri sistemi CAM, ma continua a utilizzare Edgecam con soddisfazione; è peraltro un sistema che viene costantemente allineato con l’evoluzione tecnologica del mercato. Il team di sviluppo presenta due release all’anno colme di interessanti novità, più alcuni “software update” intermedi. L’importanza di questi aggiornamenti è evidente: Edgecam ha sempre prestato un attento ascolto a tutti i suggerimenti e le osservazioni dei clienti e dei partner, ricevuti direttamente e tramite la collaborazione dei distributori locali come ProCAM.
Condividi l'articolo
Scegli su quale Social Network vuoi condividere