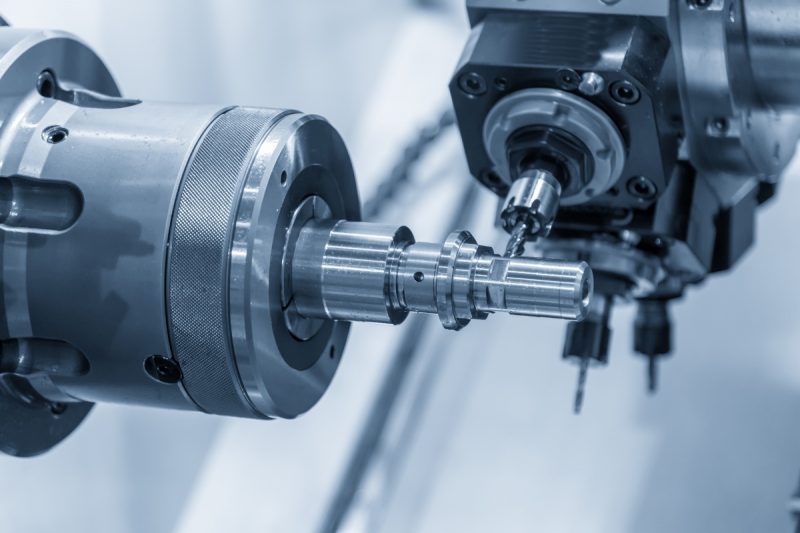
I centri di tornitura sono veri e propri torni polifunzionali, capaci di eseguire in maniera flessibile e produttiva operazioni differenti su pezzi complessi.
I centri di tornitura sono l’ulteriore passo in avanti della tecnologia rispetto ai torni a controllo numerico e conciliano una grande flessibilità con un’elevata produttività e tolleranze ristrette. Andiamo a vedere più in dettaglio cosa sono i centri di tornitura e fresatura e come funzionano queste interessanti macchine utensili.
Caratteristiche principali dei centri di tornitura
I centri di tornitura possono essere considerati la versione più evoluta dei normali torni a controllo numerico. La principale distinzione rispetto ai normali torni a CNC è il maggior numero di assi controllati, che permette alla macchina utensile di svolgere un numero maggiore di lavorazioni, anche non necessariamente limitate alla sola tornitura, rendendo così la macchina molto versatile e capace di produrre pezzi complessi.
Inoltre, queste macchine possono avere più di un mandrino contrapposto. Questo facilita l’esecuzione di pezzi che, altrimenti, richiederebbero la ripresa per le lavorazioni da entrambi i lati. L’idea di fondo dei centri di tornitura, e più in generale anche dei centri di lavoro, riferendoci alla categoria delle fresatrici, è che, con un solo piazzamento in macchina, vengono eseguite una pluralità di operazioni senza, quindi, dover ricorrere ad altre lavorazioni su macchine utensili differenti, rendendo così i centri di tornitura delle vere e proprie macchine multifunzionali.
Sulla torretta, oltre all’utensile motorizzato di fresatura, che permette di eseguire fresature e fori radiali, spesso è presente anche l’asse Y (oltre ai tradizionali assi X e Z rispettivamente in direzione assiale e radiale). L’asse Y permette agli utensili sulla torretta di spostarsi perpendicolarmente al piano passante per il pezzo, operazione molto utile per eseguire fresature complesse. Grazie a ciò, si ha indirettamente anche maggior libertà nel magazzino utensili. Infatti, è possibile collocare due utensili affiancati nella stessa posizione del magazzino con un leggero offset rispetto al piano del pezzo (grazie all’asse Y). Durante la fase di tornitura, si utilizzerà prima uno e poi l’altro utensile disassando la torretta rispetto all’asse Y, in modo che lavori solo un utensile dei due alla volta. Questa strategia non solo permette di raddoppiare il numero di utensili nel magazzino, ma anche di aumentare la produttività.
Grazie alla ridondanza di utensili, infatti, si avranno meno fermi macchina: in caso di rottura inserto dell’utensile, non è più necessario fermare la macchina per cambiare placchetta, ma basterà semplicemente lavorare con il secondo utensile. Un’altra importante caratteristica dei centri di tornitura è che, in genere, possono avere anche più di una slitta con la relativa torretta portautensile.
Tutti questi accorgimenti spingono la macchina utensile in un’ottica di completa automazione, che, infatti, è spesso attrezzata con robot di carico e scarico del pezzo o con caricatore spingi-barra. Per questa ragione, queste macchine sono una ottima scelta per creare delle celle produttive, in concomitanza con altre macchine (ad esempio CMM o sistemi di lavaggio dei pezzi).
Come è fatto un centro di tornitura
Nel paragrafo precedente abbiamo spiegato cosa sono e come funzionano i centri di tornitura. Sebbene vi siano dei punti in comune con il tornio a controllo numerico, i centri di tornitura e fresatura possiedono alcune peculiarità:
Struttura – La struttura dei centri di tornitura è, in genere, basata sul concetto di modularità. I vari accessori e dispositivi periferici possono essere installati e aggiustati in base al tipo di prodotto da lavorare.
Controllo numerico – Il CN, che esegue il controllo della posizione e della velocità degli assi, può adottare metodi di controllo molto sofisticati, come, ad esempio, il controllo adattativo. Durante la lavorazione, la macchina misura le condizioni di taglio (come la forza di taglio, l’accelerazione in prossimità del mandrino, la temperatura della macchina, l’usura dell’utensile e la finitura superficiale) e converte questi dati aggiustando i parametri di processo, come ad esempio l’avanzamento e la velocità di taglio, in modo da lavorare nelle migliori condizioni di taglio e di massima produttività.
Torrette portautensili e mandrini – Come detto, queste macchine adottano una struttura a uno o due mandrini contrapposti e due torrette portautensili che possono lavorare in contemporanea, ciascuna sul rispettivo mandrino. È possibile anche trovare i due mandrini disassati tra loro in modo che il pezzo venga sostenuto da un’apposita controtesta e dalla relativa contropunta. Alla fine della lavorazione sul mandrino principale, il pezzo viene prelevato dal mandrino secondario per la lavorazione del lato rimanente. Per queste macchine utensili è largamente usato il motorizzato di fresatura, che garantisce una grande flessibilità di lavorazioni eseguibili. Su ogni torretta è possibile caricare diversi utensili, in modo che ci sia un’ampia scelta di lavorazioni di cui disporre. Le due torrette possono anche lavorare contemporaneamente sullo stesso pezzo: l’utensile sgrossatore sulla prima torretta inizia la lavorazione e, pochi millimetri dietro, contemporaneamente, un utensile sulla seconda torretta esegue la finitura ancora prima che sia finita la sgrossatura. Alternativamente, è possibile lavorare simultaneamente differenti diametri del pezzo.
Per la stesura di questo articolo sono state consultate le seguenti fonti:
Eugene Avallone “Marks Standard Handbook for mechanical Handbook”, Mc Graw Hill, 2006
Richard Kibbe et al, “Machine tool Practices”, tenth edition, Pearson, 2014
Steve Krar et al, “Technology of Machine Tools”, seventh edition, Mc Graw Hill, 2011
Sito web B2B voice, “Machining centers purchase guide: components and types”.
a cura di Ing. Alberto Mora
Condividi l'articolo
Scegli su quale Social Network vuoi condividere